Work orders are more than just a fancy piece of paper: They're the unsung and underappreciated heroes of maintenance that help you track, organize, and prioritize those critical tasks that keep your operations running smoothly.
Ready to unlock their full potential? In this guide, we'll explore the different types of work orders (from emergency repairs to routine checkups), what to include in them to ensure they're effective, and how cutting-edge software can streamline your workflow and boost productivity. So, let's dive in and discover how work orders can transform your maintenance game!
What is a work order?
A work order (WO) is a document outlining instructions for a scheduled maintenance job, including information about who should complete the task, the process involved, and when the task needs to be completed.
Operational managers use work orders to assign maintenance work to maintenance teams in both paper and digital formats. According to Plant Engineering’s Maintenance Report, approximately 58% of facilities rely on work order software like computerized maintenance management systems (CMMS) to manage their work orders, 45% use spreadsheets, and 39% of those in facilities management still rely on paper records.
Given that paper work orders often lead to missing information and are difficult to manage, it’s no surprise that the number of facilities adopting CMMS continues to increase. CMMS apps allow maintenance teams to create work orders in advance, schedule maintenance tasks at intervals, maintain digital audit trails for historical work orders, and, in some cases, comment and chat within work orders.
If you’ve been using paper work orders for some time, making a change can be daunting. Luckily, many free work order software options exist and are easy to use. MaintainX, recently named the best work order software in the “ease of use” category by Capterra, offers a free option with powerful features.
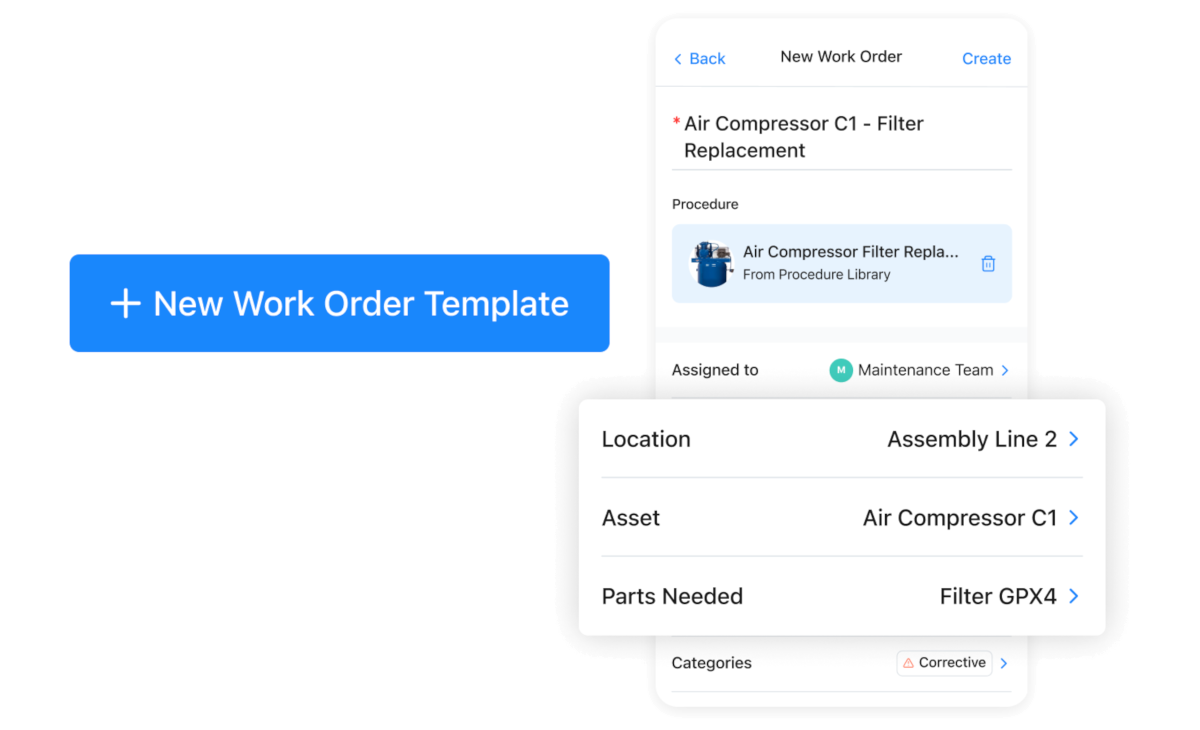
Types of Work Orders
Although the definition of work order remains relatively constant, different types of work orders exist. While the format of the work order may appear the same, the work order procedure requested and work order prioritizing may be very different.
Work order types include the following:
- Inspection Work Orders: Teams use these to test and verify the functionality of an asset, its components, and systems.
- Preventive Maintenance Work Orders: These include routine maintenance activities intended to preserve an asset’s functionality and full lifecycle. Manufacturer recommendations, organizational maintenance policies, regulatory requirements, and/or asset performance help to inform when these work orders are needed. Robust asset management requires a robust preventive maintenance (PM) system.
- Other Maintenance Work Orders: From servicing broken equipment to scheduling a work order before a breakdown occurs, maintenance work orders exist in different forms. Learn more about the various types of maintenance work orders.
Work Order Software
- Emergency Work Orders: Emergency maintenance is a form of reactive maintenance. Emergency issues, such as equipment breakdowns and failure or unusual predictive meter readers, trigger immediate corrective maintenance work orders to restore uptime.
- Safety Work Orders: These WOs strive to protect employees from harm. They include activities such as chemical cleanups, Lockout Tagout procedures, and repairs to prevent accidental slips.
- Special Project Work Orders: These can provide instructions for installing new assets, increasing productivity, and modernizing maintenance operations.
Notably, WOs are both planned and unplanned. Emergency work orders are an example of unplanned work orders. As mentioned above, they can be initiated internally within an organization or externally by customers. The key is that your system needs to flow smoothly from technicians to teams to management, and vice versa.
Teams that deploy a CMMS work order software with built-in chat and real-time data on mobile devices can respond quickly from the field. No need to go back to the office to get a hard copy work order.
What's the purpose of a work order?
The primary purpose of a WO is to provide precise details of scheduled maintenance tasks. The documents also serve as official authorizations to service equipment. Maintenance technicians may initiate maintenance work requests after identifying parts’ problems during routine inspections and audits. Facility users, customers, and other stakeholders can create a work request after noticing a problem at a facility.
There are four primary purposes for generating work orders:
- Authorization: Work orders serve as an official greenlight to start work on a specific task or project. They ensure that the necessary resources and personnel are allocated, and that the work is aligned with organizational goals and priorities.
- Instruction: Work orders provide clear, step-by-step instructions on how to complete a task, including any safety precautions, tools required, and quality standards. This ensures consistency in the work rendered and minimizes the risk of errors or misunderstandings.
- Collaboration: Work orders facilitate communication and collaboration between teams and departments. They help coordinate schedules, allocate resources, and track progress, ensuring that everyone is on the same page and working towards a common goal.
- Information: Work orders serve as a valuable source of information for tracking maintenance history, analyzing trends, identifying problem areas, and making data-driven decisions to improve efficiency and reduce costs.
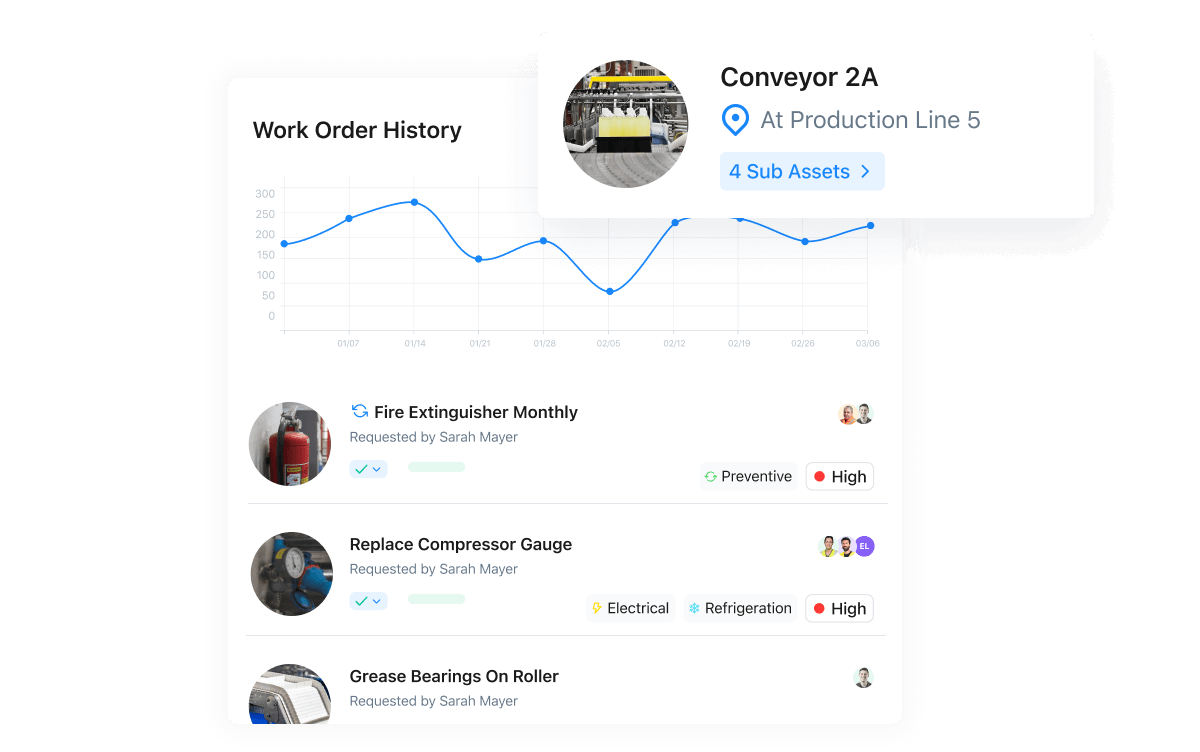
Upon receiving requests, maintenance managers evaluate them and decide what to do next. Not all work requests turn into work orders. If, for example, a maintenance manager notices multiple work requests for the same issue, the manager will close the duplicate requests and move forward with only one.
With the request in hand, the maintenance manager will create a work order (WO) and assign it to an available technician. Remember that the best work orders provide detailed information necessary to complete the requested tasks, informational fields for estimating labor costs, replacement parts, and other relevant expenses, and historical data on asset maintenance.
CMMS software like MaintainX help ensure the quality of maintenance requests and work orders by automatically prompting users to fill in the relevant information. Digital checklists and templates prevent users from leaving out any crucial details and allow for easy tracking and follow-up if necessary.
Industries that use work orders
Industries across the board use work orders. Common ones include:
- Residential and commercial building services
- Field service companies
- Manufacturing
- Food and Beverage
- General contractors
- Utilities
- Aggregate industry
- Transportation industry
- Aviation industry
- Government
- Science and research
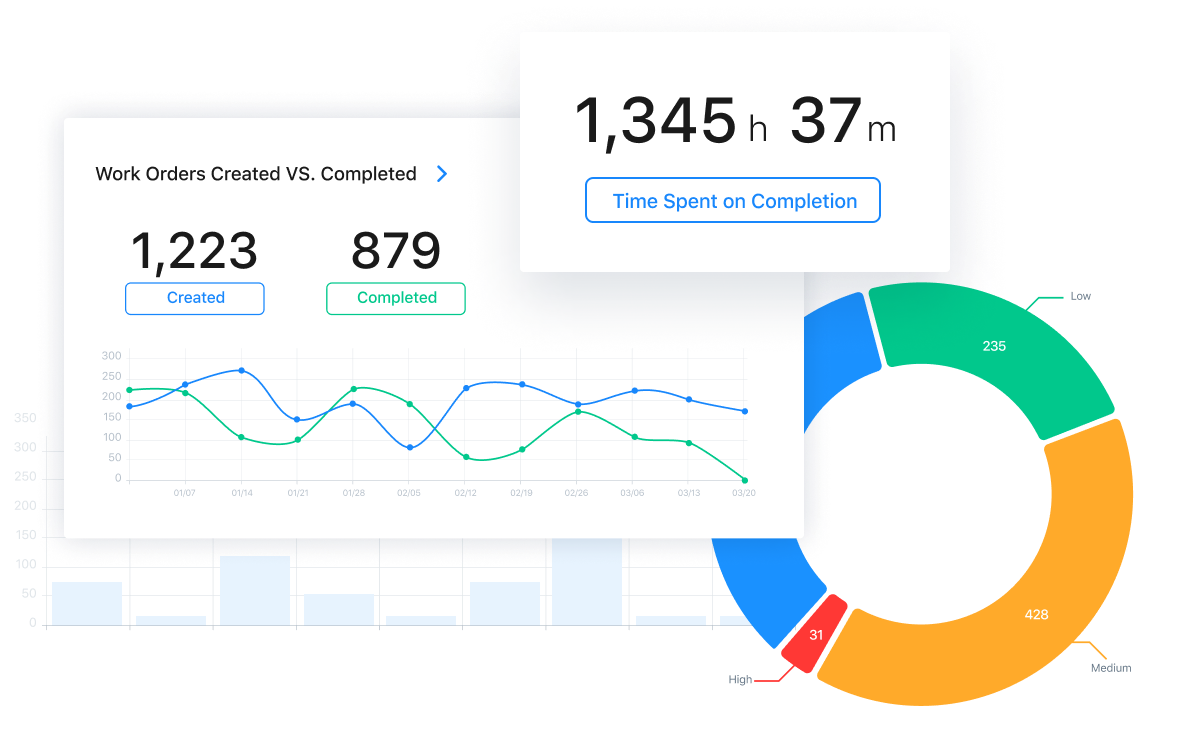
What to include in a work order
Successful completion of maintenance tasks largely depends on how detailed the work order is. Incomplete information can result in costly errors.
The last thing you want is for technicians to spend valuable time and resources on fixing a problem, only to realize later that they were addressing the wrong issue, all because they didn’t have the complete picture from the start.
A standard maintenance WO should contain the following pieces of information:
- Location of asset needing work
- Priority Level of requested work
- Description of asset
- Description of problem
- Scope of work to be completed
- Standard operating procedure (SOP)
- List of needed tools and replacement parts
- List of safety procedures for the job
- Name of person or department that requested it
- WO creation and submission date
- Projected work completion date or due date
- Expected hours of work needed
Work orders can also include checklists for completing the assigned tasks and urgency priority levels. Managers should attach standard operating procedures (SOPs), asset maintenance histories, manuals, and images to help maintenance technicians complete the WO efficiently.
Managers can include notes with observations, such as the frequency of the problem and techniques for troubleshooting the problem. These notes help maintenance staff complete WOs, and managers review them for verification after assignments.
Work order management software optimizes these approaches. For example, digital work orders with standard operating procedures allow staff to access necessary instructions right from the site of the work.
MaintainX, for example, is a CMMS with a digital procedures library. Staff can access multiple procedures and cross-reference information to ensure they have the best problem-solving approach.
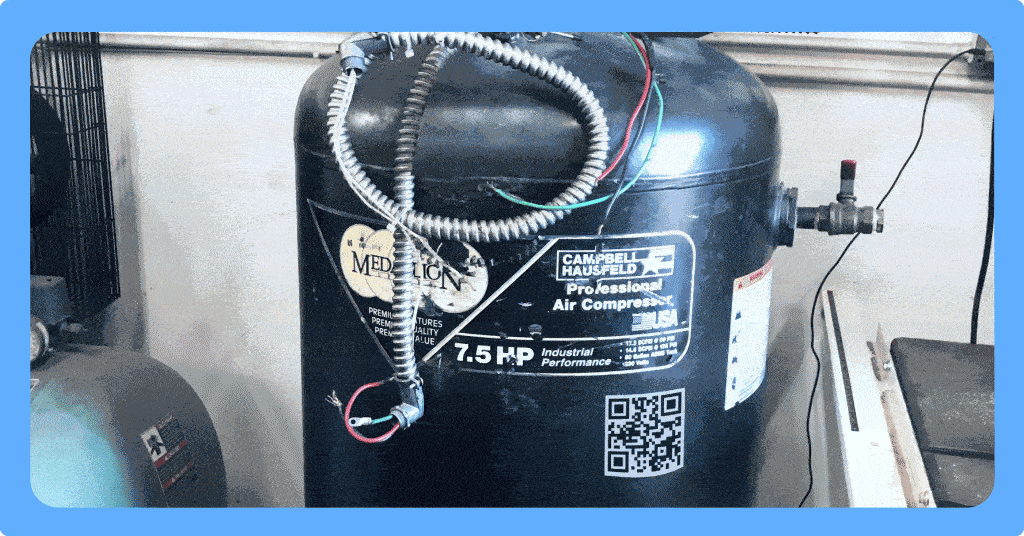
Similarly, a CMMS with QR code and barcode scanning functionality provides staff with detailed asset history on the floor or out on a job site. Workers can scan these codes to pull up maintenance histories of machines that then inform their present maintenance approach.
Maintenance work order process: Four steps
Work order management is crucial to smooth workflow. WOs usually go through a four-step maintenance management process:
Step 1: Submitting work requests
Machine operators, equipment inspectors, employees, and tenants, to name a few, can all submit work requests that managers turn into work orders.
In residential organizations, tenants often submit work requests. Depending on the type of technology a maintenance department uses, stakeholders can create work requests digitally in a work order system like a CMMS or manually log requests via phone or text message.
Logging a work request via a work order management system, especially a mobile CMMS, allows staff to directly capture as much information as needed directly from the shop floor or job site. A team member who notices an issue only needs to pull out their smartphone to record the necessary data for the work request. MaintainX
Step 2: Creating work orders
Maintenance supervisors usually review requests and, if approved, create a new work order. As stated, not all work requests get approved. Managers can deny work requests if a technician has already completed the reported problem or the task doesn’t fall under their department. If resources for the request’s completion aren’t available, the manager can schedule the task as a “deferred maintenance activity.”
CMMS applications are particularly useful for managing multiple work orders simultaneously. A good CMMS will provide visibility into all work order requests, allowing managers to decide which to prioritize and how to allocate resources.
Step 3: Assigning WOs to technicians
Maintenance technicians receive digital or analog instructions about when, where, and how to do the job. Organizations that use CMMS work order apps can automatically assign them to technicians based on availability and accessible digitized maintenance schedules. Depending on the priority level, technicians complete the job immediately or schedule it for later.
With mobile CMMS apps, maintenance workers receive push notifications directly on their smartphones, ensuring they don’t miss any tasks. MaintainX, the only CMMS software with in-app chat, allows team members to communicate directly via instant messaging. This feature allows assigned technicians to reach out for clarification and support. With a mobile CMMS app, technicians can access procedures, work order templates, work order forms, and procedures to support their maintenance work.
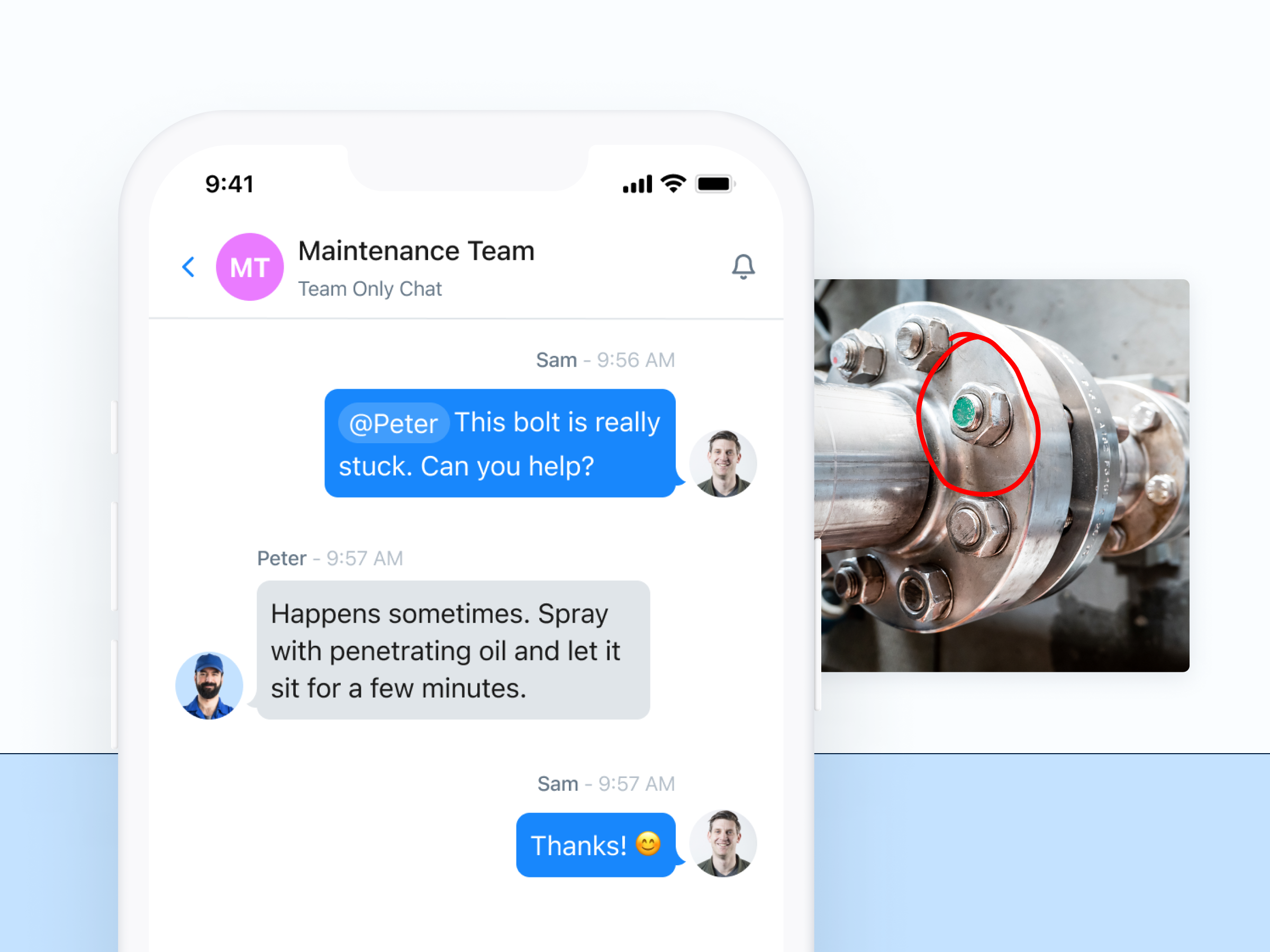
Step 4: Closing WOs
Maintenance technicians should close the WO as soon as they’ve performed the assigned tasks. Details they’ll be asked to provide can include:
- Amount of time spent on task
- Replacement parts used
- Comments and images, including troubleshooting tips
- Completion notes, such as observations beyond assigned tasks
CMMS software automatically updates the maintenance log on the given asset after a work order is closed. Maintenance supervisors can then review the completed tasks and decide on the next course of action.
A CMMS app with robust reporting features helps companies make actionable insights based on maintenance activities, identify patterns, and drive improvement. For example, MaintainX Reporting dashboards analyze key performance indicators and metrics like Time to Complete, MTTR, Asset history, and Reactive vs. Repeatable work order history.
The lifecycle of maintenance work orders
A work order's journey doesn't end once the task is complete. It goes through a lifecycle that ensures work gets done and provides valuable insights for optimizing maintenance operations. Let's break down the key phases of this lifecycle:
- Production: A work request is submitted, either by a technician, an operator, or through automated triggers. Once the work request is reviewed, prioritized, and approved by a supervisor or manager, the work order is created, detailing the task, required resources, and when it needs to be completed.
- Performance: The assigned technician or team begins work on the task, following the standard operating procedures outlined in the work order. Progress is tracked, updated, and documented in a work order system like MaintainX.
- Closure: Once the work is completed, the technician marks the work order closed and records the time taken, materials used, and any relevant observations and findings. A supervisor or manager reviews the work to ensure quality and adherence to standards.
- Analysis: Completed work orders are analyzed to identify trends, recurring issues, and areas of improvement.
- Reference: Before new work orders are created and the cycle repeats, completed work orders are referred to for important information and service notes.
Coming back to completed work orders and analyzing what work needs to be repeated can be a great way to understand asset health. If an asset requires constant upkeep, more time and research may need to be spent to identify the root cause of the issues and to avoid them from repeating in the future. The ability to refer back to old work orders and attach pictures to them allows your organization to maintain key knowledge that could otherwise be lost to retiring technicians.
Enjoy automated work orders & templates with MaintainX
Work orders help maintenance teams efficiently and effectively streamline their activities. Well-planned task assignments increase the efficiency of PM strategies and reduce unplanned downtime and backlogs, reactive maintenance, emergency parts ordering, and overtime labor costs.
Automated work order programs enable maintenance personnel to define roles, track work orders, document information, and streamline workflows. Furthermore, they’re a great source of asset maintenance history and provide valuable insights to make data-driven maintenance decisions. CMMS solutions, like MaintainX, offer a robust work order tracking system to give maintenance managers visibility into work orders, from creation to completion.
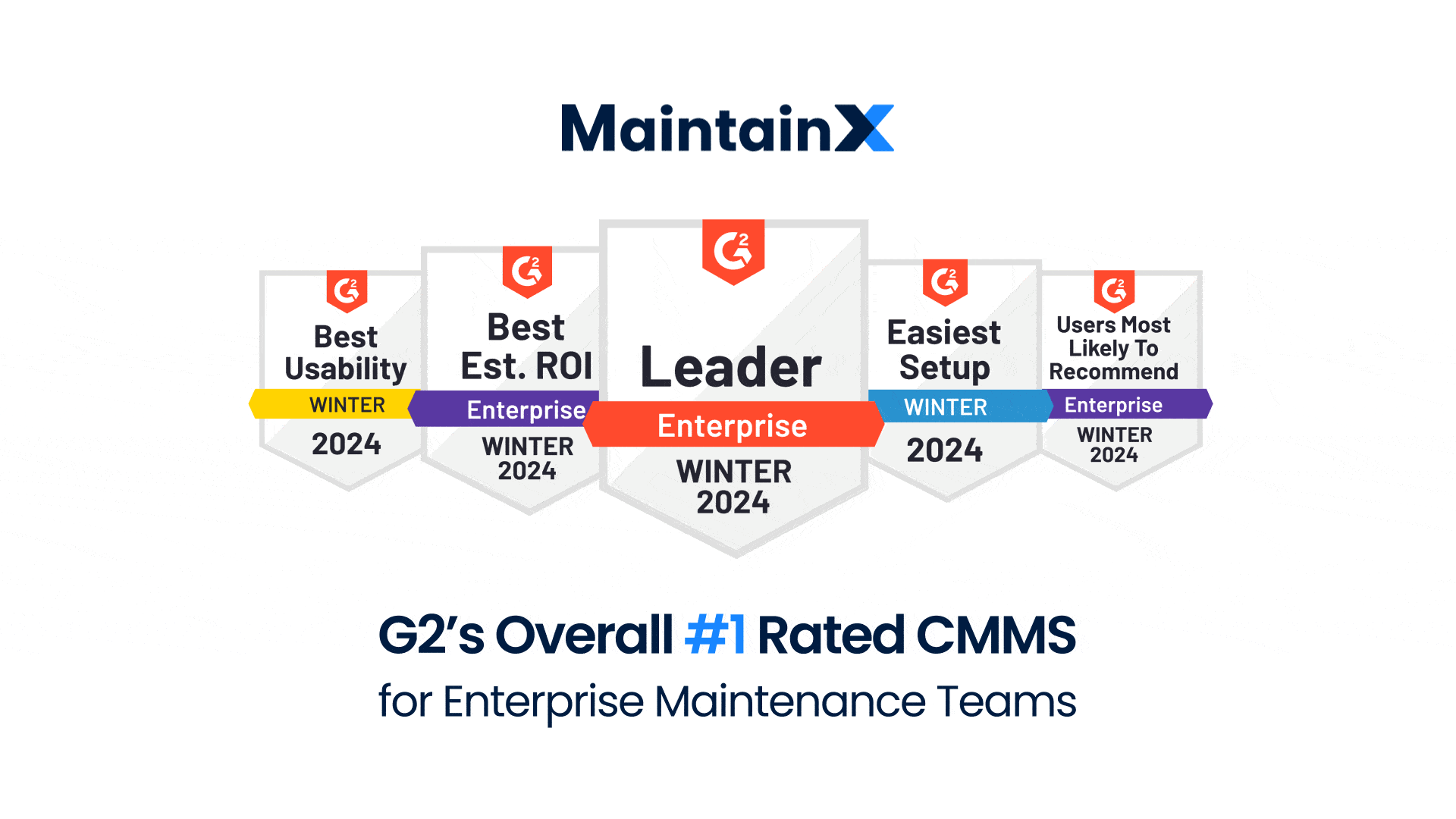
The right CMMS also makes creating and automating work orders easy with work order templates. With these templates, you don’t have to be a technical expert to create functional templates that help your team. You can easily attach procedures, forms, and checklists to clearly communicate the steps involved in completing simple and multi-step work orders. Once they are created, it’s simple to update the templates to meet your evolving needs. Most importantly, these pre-made work order templates save you time and money.
Organizations that use modern maintenance work order software for purchase orders, asset inventory management, and preventive maintenance have better productivity KPIs than those companies still relying on paper records and Excel spreadsheets. Check out our free work order examples and templates to learn more about implementing digital work orders.
Ready to check MaintainX out? Let us give you a tour.
Work Order FAQs
What Is a maintenance work order?
A maintenance work order is a document that outlines maintenance work instructions. The information found on a maintenance work order includes the details of the work to be done, who should perform the work, when the task needs to be completed, where the asset is located, and more. Maintenance work orders are used to better upkeep the integrity and overall asset health of physical assets. They are used by manufacturers, governments, educational institutions, healthcare providers, and more.
How are work orders tracked and managed?
Tracking work orders can be a tough process without the right tools. Manual work orders take more time to process and don’t provide actionable insights. A CMMS makes tracking and managing work orders easy, especially a mobile-first solution that allows technicians to have all the information they need in the palm of their hands. It allows for work orders to be completed quicker and provides actionable insights to help cut costs and prolong asset lifecycles.
Can work orders be modified or canceled?
Yes, work orders can be modified or canceled at any time. If more information is gathered, new processes are implemented, or anything else changes that would require you to change the scope of your work order, edits can be made. This information will sync across desktop and mobile, allowing technicians in the field to get up-to-date information at a moment's notice. Some powerful tools, like MaintainX, allow you to put work orders on hold or use an existing one as a work order template.
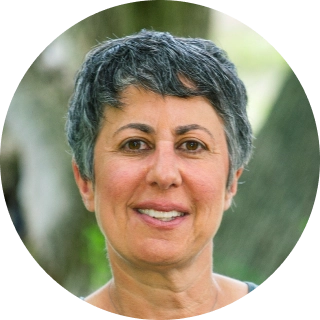
Caroline Eisner
Caroline Eisner is a writer and editor with experience across the profit and nonprofit sectors, government, education, and financial organizations. She has held leadership positions in K16 institutions and has led large-scale digital projects, interactive websites, and a business writing consultancy.
See MaintainX in action