The PDCA cycle is a simple four-step approach to continuous improvement. PDCA stands for Plan, Do, Check, Act, and it is an improvement cycle widely used in manufacturing businesses to introduce incremental changes to processes, services, and products.
The PDCA cycle is all about testing out ideas or alternatives on a small scale before committing to large, complex, or expensive changes.
By approaching new initiatives within a plan-do-check-act framework, your organization can try out new processes or maintenance procedures, assess the results, and implement the approach that best suits your requirements.
“Just as a circle has no end, the PDCA cycle should be repeated again and again for continuous improvement. The PDCA cycle is considered a project planning tool.”
ASQ
Understanding the PDCA Cycle
The PDCA cycle is a powerful tool for driving continuous improvement in businesses. It is a cyclical process that involves four stages: Plan, Do, Check, and Act. The cycle is designed to be repeated continuously, with each iteration building on the previous one to drive ongoing improvement.
The PDCA cycle is based on the scientific method, which involves formulating a hypothesis, testing it, and refining it based on the results. In the context of business, the PDCA cycle involves identifying a problem or opportunity for improvement, developing a plan to address it, implementing the plan, and evaluating the results.
The PDCA cycle is also known as the Shewhart cycle or the Deming cycle, after its founders Walter Shewhart and W. Edwards Deming. It is a key component of lean manufacturing and the Toyota Production System, and is widely used in industries such as healthcare, finance, and technology.
Where Does Plan-Do-Check-Act Come From?
The PDCA model is an essential part of the lean manufacturing philosophy, along with well-known concepts like Lean Six Sigma and Kaizen.
Originally described by American engineer W. Edwards Deming, the PDCA cycle evolved out of Deming’s work and the work of his contemporary fellow engineer Walter Shewhart. After WWII, Deming undertook extensive work with Japanese industry leaders, like Toyota. These industry leaders were beginning to gain international renown for their incredibly efficient lean manufacturing processes.
In fact, Deming preferred the term PDSA, noting that Study rather than Check represented a more practical lens to see if a proposed change was worth implementing, especially during the plan phase.
The PDCA cycle is also referred to as the Plan-Do-Study-Act or PDSA Cycle, the Deming Cycle, the Deming Wheel, or the Shewhart Cycle.
How to Use the PDCA Methodology in Detail
Let's look at how you can apply these four steps in a manufacturing environment.
1. Plan
Plan what needs to be done
The planning stage can be broken down into smaller steps. This crucial stage can take up a significant amount of time and effort by your team. But, it’s important if you want the cycle to work.
Proper planning prevents poor performance, and the PDCA cycle focuses on implementing smaller, incremental changes aimed at improving processes while minimizing disruption. Here you determine the baseline, plan what resources are needed, and consider how you will measure success.
In the planning stage, gather your team for a problem-solving session to discuss the following:
- What the core problem is you want to solve
- What quality improvement or cost reduction you want to achieve
- What resources do you need vs. what resources you already have on hand
- What potential solutions are worth pursuing
- How you will measure success
2. Do
Execute the plan
It’s time for action–take small steps to apply the new methods or processes you arrived at in your planning phase. This stage may take some time. It can involve changes to production or maintenance processes or training staff on new work practices. This stage may take some time and requires careful monitoring to ensure that the improvement effort yields the desired results.
3. Check
Review and analyze the data
You’ll find out if your early planning worked in the check phase. Did you reach the expected goal as expected? What challenges did you encounter along the way? Finally, compare your results with the current business-as-usual process to identify areas for continual improvement.
4. Act
Implement the new process or method
After drawing conclusions from the data and deciding that the new approach will be successful, it’s time to act. Remember the plan-do-check-act cycle is an iterative process, and the act phase involves implementing successful changes broadly or revisiting earlier phases if results were unsatisfactory.
Regardless of the outcome, the information you have extracted from the testing process can be recorded and applied to your continuous improvement processes, bringing you back to the beginning of the PDCA cycle.
Benefits and Limitations of the PDCA Cycle
The PDCA cycle offers several benefits that make it an effective tool for continuous improvement. Firstly, it ensures that all appropriate steps are followed in the improvement process, providing a systematic method for tackling issues. This structured approach serves as an effective guide for problem-solving, helping teams to stay organized and focused.
Additionally, the PDCA cycle informs future improvement efforts through feedback. By analyzing the results of each cycle, organizations can learn from their experiences and apply these insights to subsequent iterations. This feedback loop is crucial for maintaining order during problem-solving and ensuring that improvements are sustainable.
However, the PDCA cycle also has some limitations. It requires significant commitment over time, as the process is iterative and ongoing. This can be a challenge for organizations looking for quick fixes or those with urgent projects that need immediate attention. Furthermore, the PDCA cycle requires support from senior management to be effective. Without this backing, it can be difficult to implement changes and sustain the improvement efforts.
Despite these limitations, the PDCA cycle remains a powerful tool for driving continuous improvement in businesses. By understanding its benefits and limitations, organizations can use the PDCA cycle to drive ongoing improvement and achieve their goals.
Relationship between PDCA and Kaizen
The PDCA cycle is closely related to Kaizen, a Japanese philosophy that emphasizes continuous improvement. Kaizen involves making small, incremental changes to processes and products to drive ongoing improvement.
The PDCA cycle is a key component of Kaizen, as it provides a structured approach to identifying and addressing opportunities for improvement. By using the PDCA cycle, organizations can identify areas for improvement, develop plans to address them, and implement changes to drive ongoing improvement.
In turn, Kaizen provides a cultural framework for the PDCA cycle, emphasizing the importance of continuous improvement and encouraging employees to identify and address opportunities for improvement. By combining the PDCA cycle with Kaizen, organizations can create a culture of continuous improvement that drives ongoing growth and success.
How the PDCA Process Affects Your Company's Continuous Improvement
Whether you changed a manufacturing process, revised a maintenance program, introduced a new piece of equipment, or designed a new product, the outcome of your PDCA process is likely to affect other teams and departments. Unlike a fixed, linear end-to-end process, the PDCA cycle is an iterative learning loop that emphasizes continuous improvement and adaptability.
When the PDCA cycle introduces a change to a process, be sure to update your standard operating procedures, maintenance checklists, worksheets, training manuals, and any other materials impacted by the change.
Likewise, alert production workers and maintenance crews to the new processes. Make sure they know how to move forward safely and efficiently.
Failure to update key business processes across the organization can lead to incorrect procedures, increased reworks or quality assurance (QA) failures, and potential safety issues for maintenance staff if they continue working from outdated manuals or instructions.
It may take some time for these issues to bubble to the surface, making the root cause more difficult to pinpoint.
With any process improvement, quality control is vital. Therefore, in your planning stage, create a comprehensive list of the processes, people, and plants to update once you implement the new approach.
Using Technology to Apply the PDCA Cycle for Continuous Improvement
Making sure continuous improvement is applied consistently in your organization comes down to good project management skills. Using the right resources to plan, track, and review changes will help you seamlessly introduce new ways of working to everyone on your team, thus facilitating the improvement cycle.
Examples of helpful resources can include physical reminders such as kanban boards or visual cues such as color-coding, floor tape, machinery guards, or signage to help employees remember new processes.
A good “paper” trail is important too, which is where online process management and maintenance software is most beneficial.
CMMS platform provides a simple, secure, and easily accessible repository for all your updated manuals, standard operating procedures, and work order maintenance schedules. By sharing this new documentation with your production and maintenance teams, you can be sure that everyone has access to the most up-to-date information at all times.
CMMS tools like MaintainX also allow analysis and reporting, so you can review the results of your PDCA endeavors and ensure your entire team remains focused on continuous improvement
Check out MaintainX. Try it free.
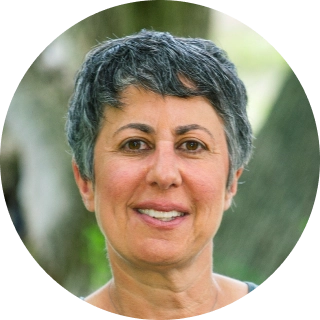
Caroline Eisner
Caroline Eisner is a writer and editor with experience across the profit and nonprofit sectors, government, education, and financial organizations. She has held leadership positions in K16 institutions and has led large-scale digital projects, interactive websites, and a business writing consultancy.
See MaintainX in action