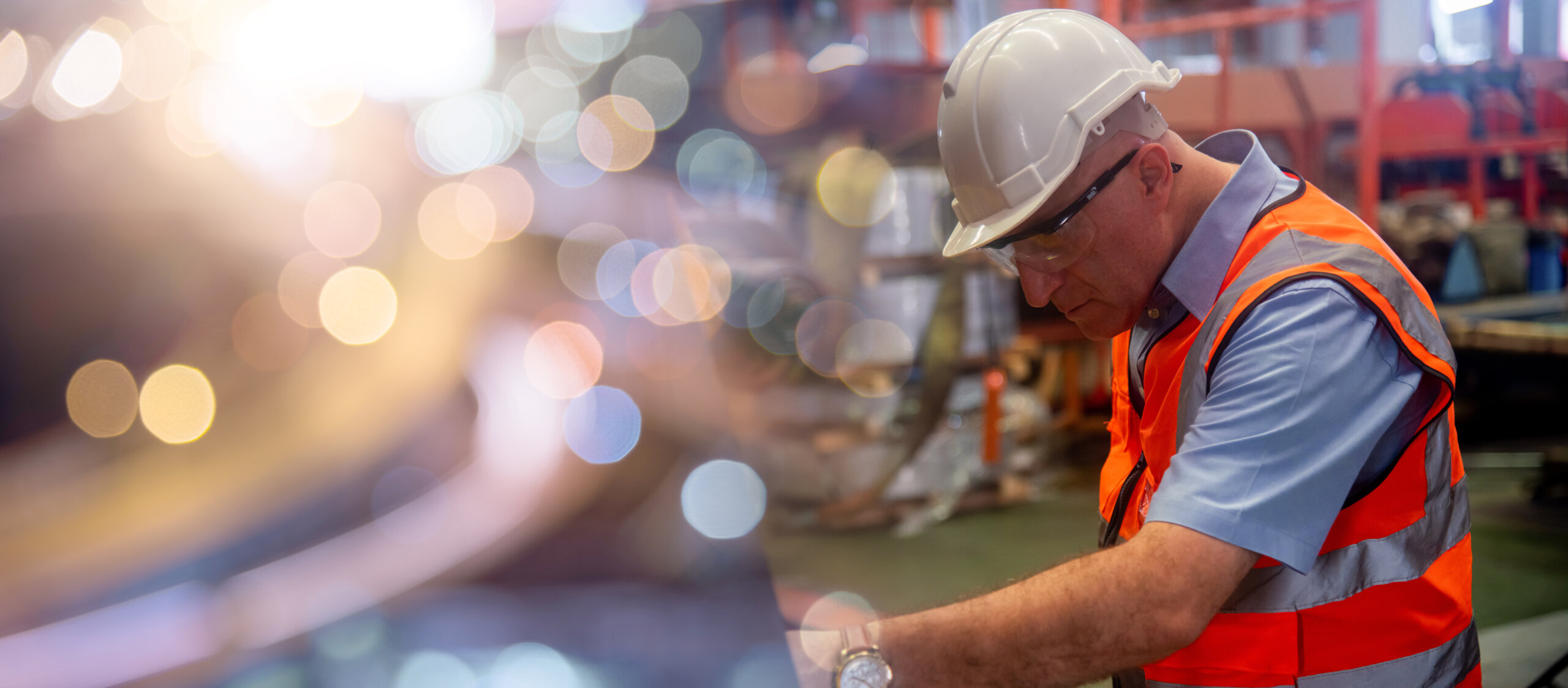
Every business faces unforeseen hurdles—both internally and externally—along the road to success. These past few years, in particular, have been filled with unprecedented ups and downs, forcing executives to rethink how to effectively accomplish even the simplest tasks.
However, as is often the case in the business world, management can either view unexpected challenges as crippling sources of frustration or welcome opportunities for innovation. Even when the “winds of fortune” are seemingly in their favor, businesses often have at least one department that can be improved.
Some operational bottlenecks may benefit from complete overhauls, while others can be fixed with small process improvements.
Regardless of the industry, most Fortune 500 CEOs agree on one thing: a commitment to operational excellence is essential to achieving lasting reliability, efficiency, and profitability.
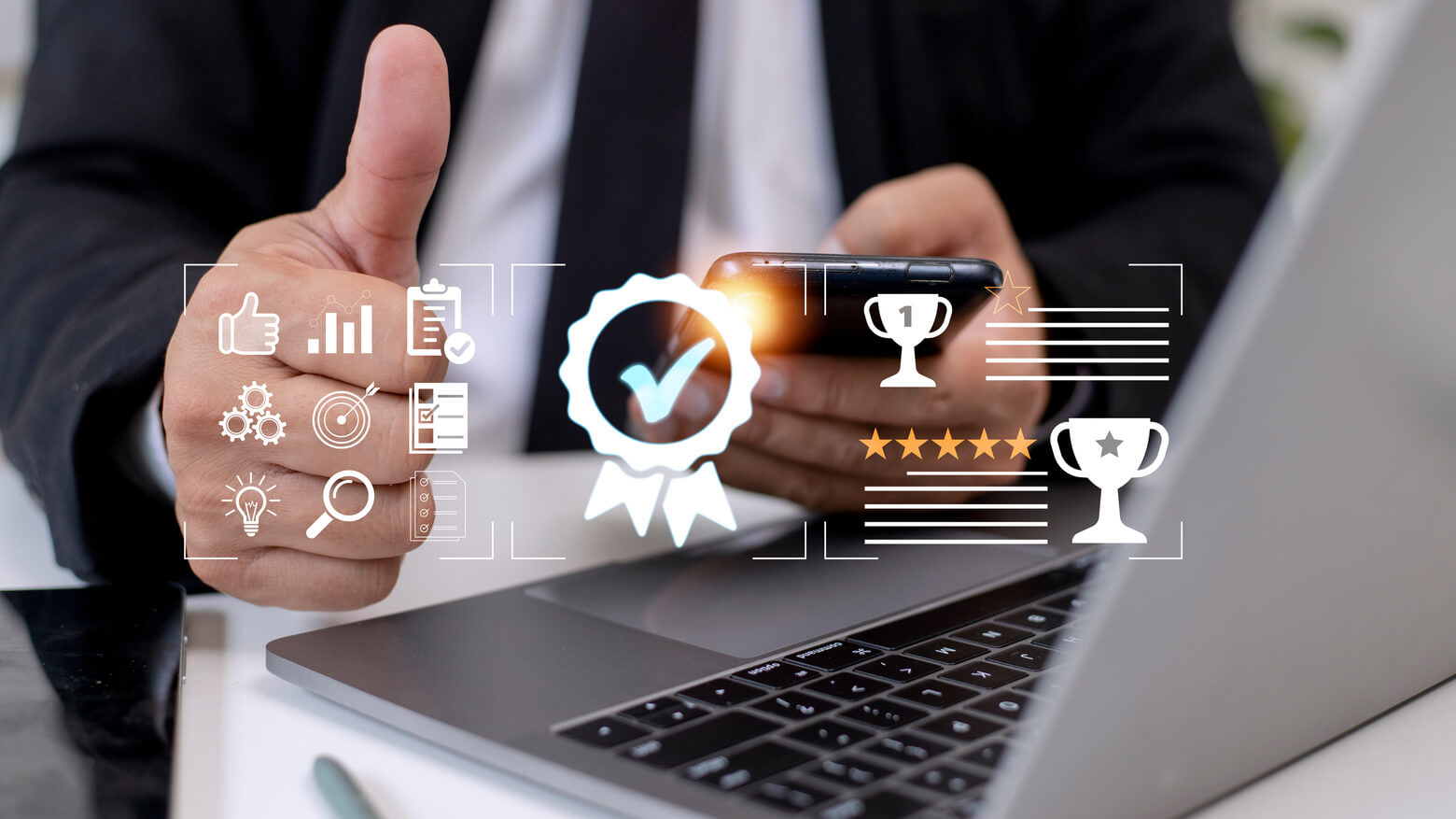
How to Achieve Operational Excellence
This post will delve into how top organizations define and achieve operational excellence.
We’ll also look at how to tackle commonly associated challenges, provide examples of operational excellence in action, and discuss how to measure the effectiveness of your efforts. Before diving into the nitty-gritty, let’s dissect the term operational excellence.
What Is Operational Excellence?
One of the best definitions of operational excellence comes from Kevin Dugan, founder of the Institute for Operational Excellence and Industry Week contributor:
“Operational excellence is when each and every employee can see the flow of value to the customer, and fix that flow when it breaks down. It’s that simple. What this means is that each employee knows that the product moves from process A to process B in a specific quantity, at a specific time, to a specific location; otherwise, something is wrong.”
Operational excellence is about equipping every employee with the skills, tools, and information needed to complete operational procedures as efficiently as possible.
One might say operational excellence comes down to each team member demonstrating exceptional decision-making skills. It’s part cultural paradigm, part data-driven strategy.
Well-executed initiatives result in decreased operational risks, decreased operating costs, increased revenue, and enhanced customer experiences.
The goal? To accomplish these improvements to a larger degree and with more reliability than the competition.
Benefits of Operational Excellence
- Enhanced employee confidence in their roles via accessible procedures.
- Improved teamwork, communication, and morale.
- Greater customer satisfaction, loyalty, and trust (in the brand).
- Increased customer referrals (online and by word of mouth).
- Decreased downtime, which increases productivity and profitability.
Additionally, following guiding principles makes it easier for businesses to navigate transformation through times of uncertainty. We can see this in how we deal with the current supply chain disruption crisis.
In other words, businesses need to address previously hidden vulnerabilities and face the typical roadblocks to running world-class operations. In our next section, we’ll provide an overview of the most common hurdles growth-oriented companies face.
Common Stumbling Blocks to Success
Obviously, no one starts a company with the intention of failing, losing money, or receiving one-star Glassdoor reviews from their employees.
Nonetheless, businesses fall short of their original intentions to create value in many ways every day. Put simply, running a tight ship is easier said than done.
Reasons for Program Failure
As reported by McKinsey, 70% of operational excellence initiatives fail. Common reasons for failure include flawed leadership, unsuccessful cultural shifts, and poor execution.
- Poor Leadership: Ineffective leadership is the reason most cited for program failure. According to the 2020 Global State of Operations Report, 23% of survey respondents blamed the failure of their operational excellence programs on their company’s leadership. Respondents said leadership lacked the understanding and buy-in needed to sustain long-term progress.
- Unsuccessful Culture Shifts: Failing to inspire employee participation is another common hindrance to program success. Many executives underestimate the effort required to enlist the support of employees across departments. Not explaining “the why” behind procedural changes can lead to spotty follow-through.
- Poor Execution: Organizations confront several challenges on the road to operational excellence, including lack of accountability measures, limited “bottom-up” feedback, and inefficient standard operating procedures (SOPs). The report mentioned above suggests that 36% of organizations experience at least one of these common execution roadblocks. Oftentimes, these leaders attempt to enforce too many changes at once, making it difficult for teams to keep up.
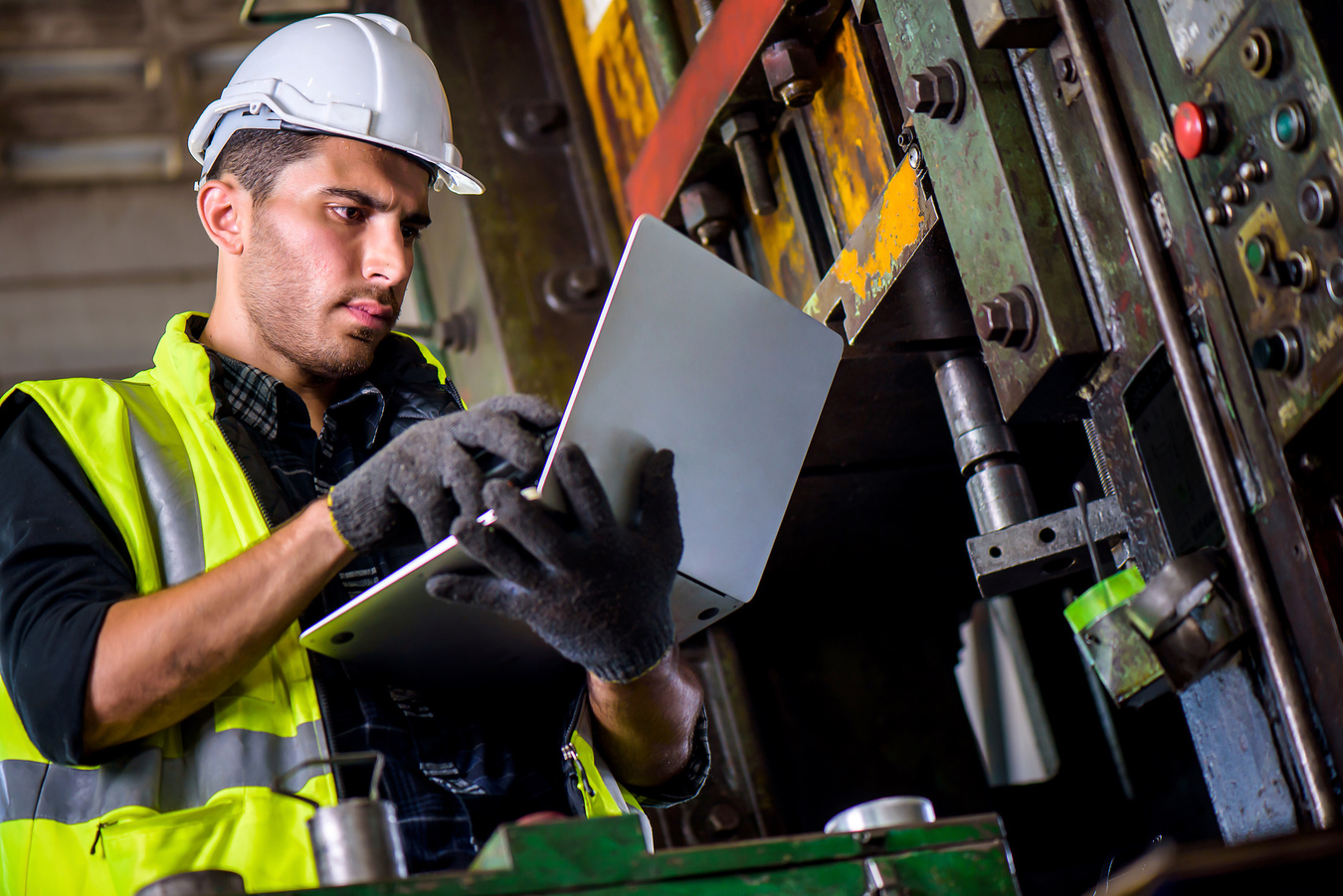
7 Steps for Reaching Operational Excellence
Since each organization faces unique challenges, there is no “one-size-fits-all” approach to mastering operational excellence. However, the core principles are the same. Below are our best tips on how to master operational excellence right now.
1. Diversify Supply Chains
If there’s one glaring lesson we’ve learned from 2020, it’s the importance of flexible supply chains. Consistently meeting customer demands proved challenging for businesses in industries across the board.
The pandemic, along with tariffs and trade disagreements, put a massive wrench in on-time delivery. As a result, management must diversify its supplier relationships to reduce risk. Should one supplier create a significant roadblock, another resource can step in to provide needed materials.
Revisit your inventory histories to identify where your organization needs the most coverage in the year ahead and communicate this information to suppliers.
Additionally, you may want to tap into digital supply networks (DSNs) powered by artificial intelligence, robotics, and 5G. Newer supply-chain technologies support end-to-end visibility, communication, and cost-optimization.
Use a platform like MaintainX to support the automation of low-quantity inventory alerts to ensure critical equipment part orders are always placed in advance.
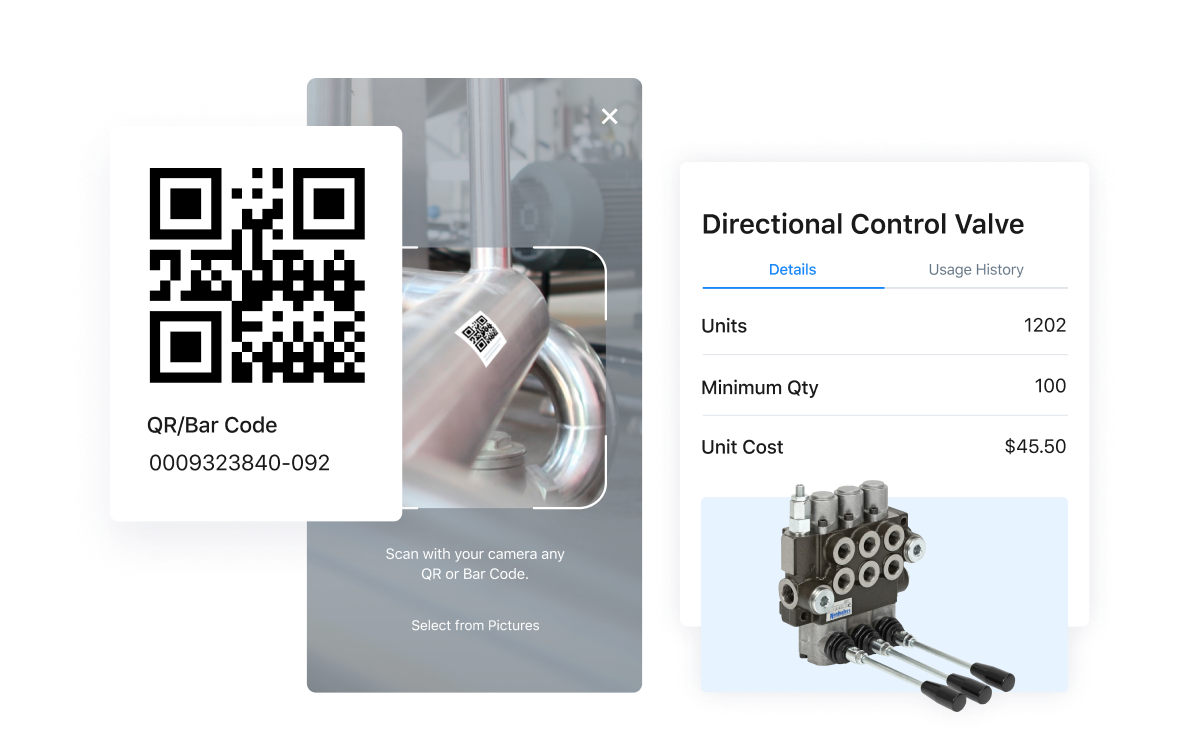
2. Implement Lean Process Improvement Methodologies
Toyota introduced the Lean manufacturing production methodology in 1930.
Since then, companies from industries across the board have embraced the operational framework worldwide for a simple reason: it simplifies the process of producing high-quality deliverables with optimized amounts of resources.
Lean manufacturing focuses on the systematic elimination of waste that doesn’t add value to a production system. It recognizes that every business process experiences issues that can be resolved to add value. Organizations wanting to achieve operational excellence should eliminate the eight types of waste as identified by Lean manufacturing.
Commit to ongoing process management to experience less downtime, greater efficiency, and more profitability. Who doesn’t want that?
3. Strengthen Disaster Recovery Plans
Now is the time to revisit your organization’s disaster recovery plan. Collaborate with department leaders to better understand the challenges they may face when implementing new rules, policies, and communication systems.
Considering how frequently both industry and government regulations have been changing, you may want to put a management SOP in place. Conducting a periodic regulatory review will ensure your team’s disaster recovery plans and daily safety policies are up to date.
Of course, one of the most challenging aspects of policy development is compliance. Ensure your planning documents are easily accessible to both managers and employees at all times.
4. Commit to Continuous Improvement
Many people assume that operational excellence is synonymous with continuous improvement. However, prioritizing improvement is only a stepping stone to operational excellence.
Instead of pushing big, disruptive changes, focus on empowering your frontline employees to drive continuous improvement efforts. You may want to lean on Kaizen principles to inspire the implementation of small, consistent improvements that compound over time.
The Japanese Kaizen productivity framework includes five principles: know your customer, let it flow, go to Gemba (the location of the problem), empower people, and be transparent.
Whatever process improvement system you rely on, just remember that operational excellence will never be a “set it and forget it” goal. Maintaining any type of competitive advantage takes consistent effort.
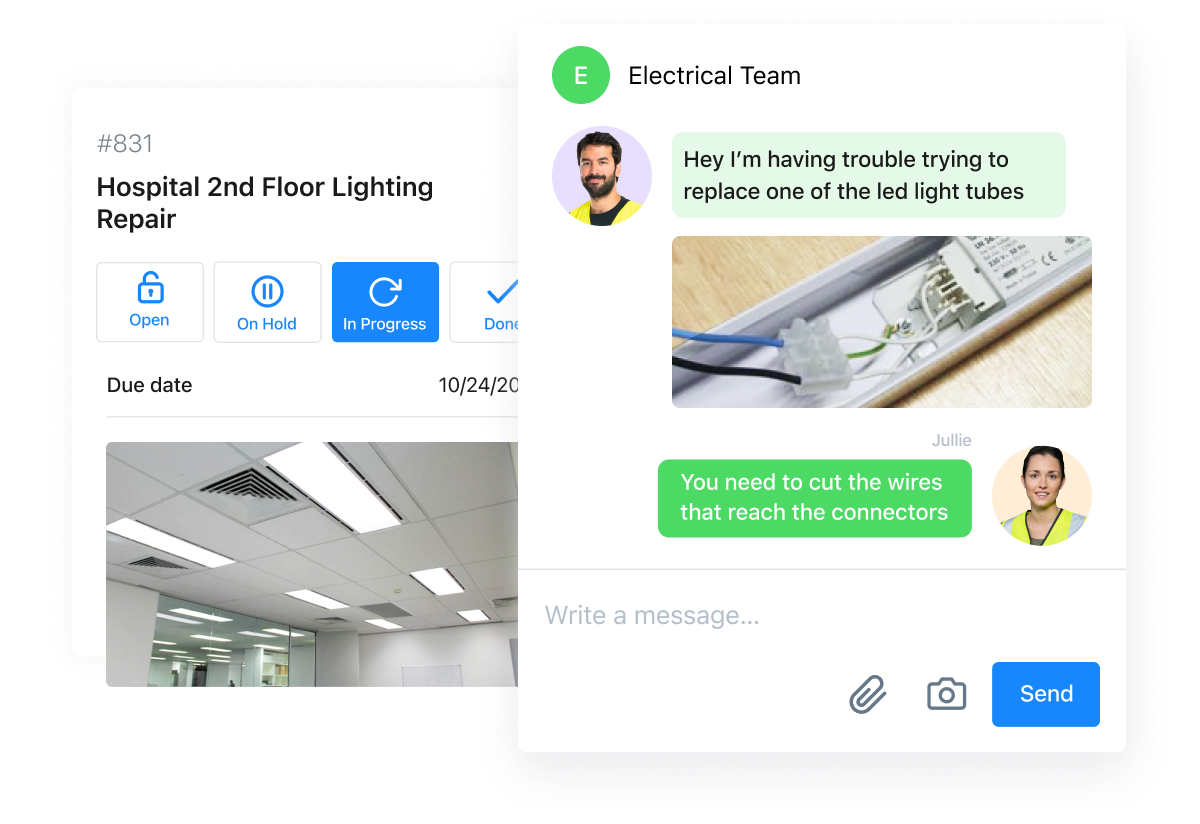
5. Use Business Messaging Apps for Real-Time Communication
Another increasingly important element of operational excellence is maintaining quick horizontal communication. This means workers within every department should be able to interact with upper management quickly, and vice-versa, in real time.
Open communication channels ensure teams can quickly troubleshoot customer, supplier, and internal issues with confidence. If your organization considers email to be its primary method of communication, we recommend upgrading to business messaging apps.
Not only do these software platforms provide instant communication, but they also allow for instant PDF, photo, and file sharing. These features streamline data records management and policy accessibility. However, MaintainX is the only CMMS with chat functionality.
A variety of enterprise chat solutions are now available. Modern smartphone apps accommodate both private and group instant messaging.
6. Implement Six Sigma
Six Sigma is a set of tools and techniques organizations can use to deliver better products, services, and value to customers. According to the American Society for Quality, 82% of Fortune 100 companies use Six Sigma to reduce defective product averages significantly.
The Six Sigma framework includes the acronym DMAIC for reducing product defects:
- Define: Define the problem by analyzing process boundaries.
- Measure: Evaluate the effectiveness of routine processes.
- Analyze Determine the root cause of identified problems.
- Improve: Revise processes to eliminate or minimize product defects. Assess, design, and test various solutions until you achieve desired results.
- Control: Update systems to monitor the new process for improvement.
Six Sigma’s success depends on accurate data collection, definable business goals, and a Lean manufacturing approach. Scientific thinking coupled with responsive action most often yields measurable improvements.
7. Strengthen Organizational Culture
Maintaining world-class operations is dependent on teamwork, integrity, accountability, and problem-solving. Proactive attitudes start at the top and trickle down.
Depending on your industry, this can mean enforcing flexible work policies, continuing education initiatives, and competitive employee benefits packages. Take care of your employees, and they will take care of you.
Examples of Operational Excellence
Here are a few examples of operational excellence in practice across industries.
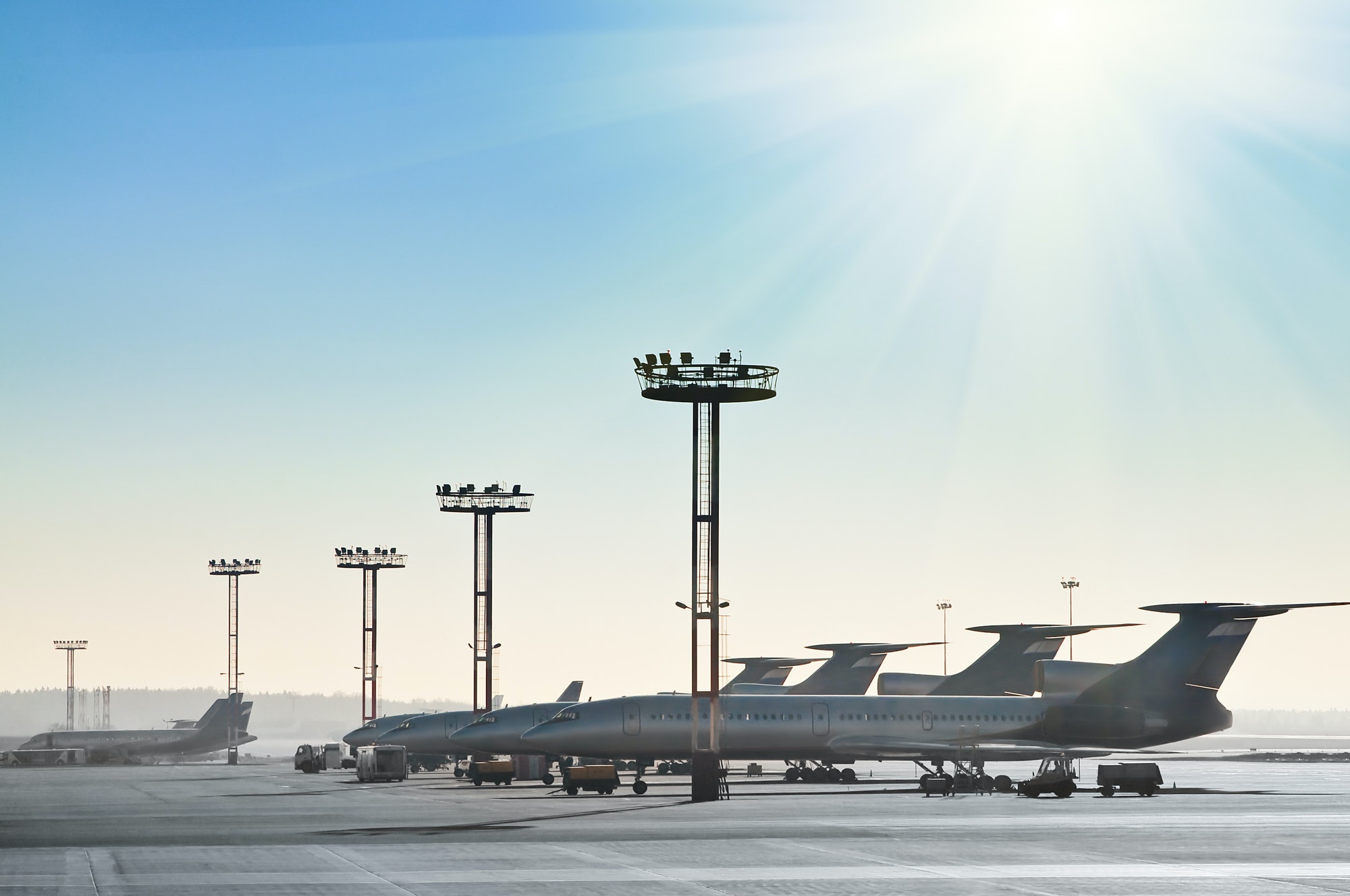
1. Aviation Industry
Did you know you’re more likely to be struck by lightning than be in a plane crash? The probability of a plane crashing is one to 5.4 million.
One reason flying is exceptionally safe is that the aviation industry has continually invested in operational excellence. Every year, major airlines improve maintenance programs, safety checks, SOPs, and staff training.
2. Automobile Industry
Toyota is one of the largest carmakers in the world, with a revenue of $248 billion. It was also the first automobile manufacturer to produce more than 10 million vehicles in a single year (2012).
As the pioneer of Lean manufacturing via the Toyota Production System, Toyota continually breaks records and drives laps around its competitors because of its commitment to operational excellence.
3. Healthcare Industry
Healthcare providers focus on efficiently using resources, eliminating unnecessary procedures (and mistakes), and improving health outcomes.
For instance, Johns Hopkins University Hospital developed a five-step safety checklist program to promote the safety of intensive-care-unit patients using central-line catheters. Process improvement initiatives like these demonstrate a commitment to operational excellence.
How to Measure Operational Excellence
No operational initiative is complete without an evaluation process in place. Therefore, management should schedule time every month, quarter, and/or year to review program effectiveness.
The success metrics you choose to measure will depend on your unique goals. However, your metrics should provide qualitative and quantitative evidence of progress.
Common initiatives track increased customer satisfaction, decreased equipment downtime, minimized product defects, reduced workplace accidents, improved equipment reliability, increased profitability, and higher employee satisfaction. The specific key performance indicators (KPIs) tracked should be personalized to your initiatives.
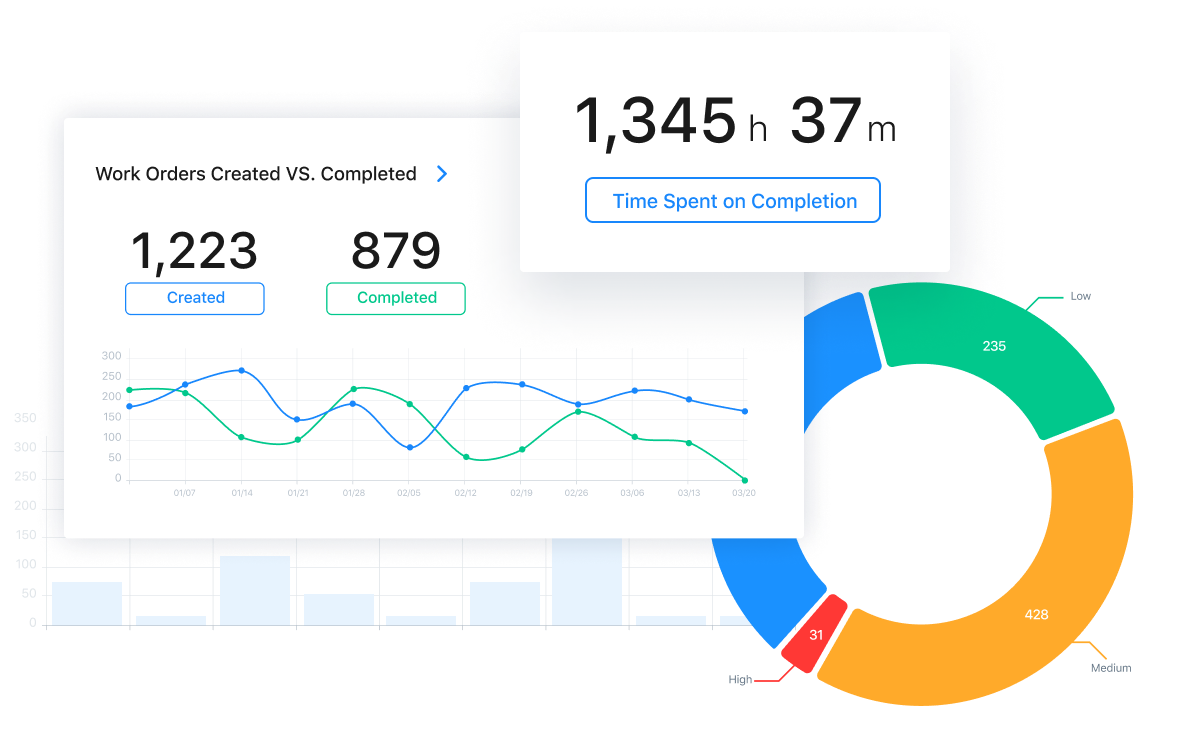
Get a Competitive Edge with MaintainX
Prioritizing operational excellence is more important than ever.
Training, empowering, and equipping employees is integral to long-term success in a fluctuating work environment. If you’re ready to streamline your organization’s maintenance department, we invite you to check out MaintainX.
Our computerized maintenance management system (CMMS) provides operations managers with everything they need to automate recurring work orders, standard operating procedures, parts inventory management, and asset management.
We believe it’s the most elegant, mobile CMMS in the marketplace today, and we’d love for you to try it. Ready for a business transformation?
FAQs
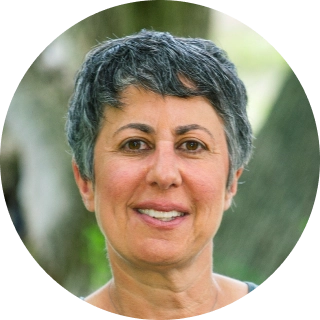
Caroline Eisner is a writer and editor with experience across the profit and nonprofit sectors, government, education, and financial organizations. She has held leadership positions in K16 institutions and has led large-scale digital projects, interactive websites, and a business writing consultancy.