
As budgets tighten and supply chains remain unpredictable, asset reliability has become more critical than ever for manufacturers and facilities.
The better you understand the reliability of your assets, the more effectively you can stock parts and schedule PMs–and this is the key to keeping production lines running.
But to improve anything, you must first be able to measure it. And many maintenance managers simply lack the information about when and why their machines fail. Either their team isn’t tracking downtime properly, the data isn’t easy to access, or it’s unclear what action needs to be taken. More often than not, all three of these problems exist simultaneously.
To help solve today’s biggest asset management challenges, we’ve released new functionality that makes it easier than ever to measure and improve asset performance–without sinking hours into spreadsheets.
Asset Health Insights delivers pre-built reporting dashboards that provide instant visibility into your most problematic assets and why they fail.
This helps you to:
- Increase asset availability by addressing the biggest causes of unplanned downtime
- Improve your PM plan by better understanding what work to prioritize on each machine
- Make better budget decisions by seeing how much your “bad actors” are costing you
“This new reporting provides a comprehensive breakdown of issue-specific downtime,” said Brandon Bath, senior facilities manager at Take 5. “We can now see what our major issues are, and can start creating action plans to do better when it comes to downtime.”
As part of today’s release, we’ve also made it easier than ever for technicians to record asset downtime as part of their usual workflow. This allows you to improve the quality and consistency of the data captured on the shop floor, leading to more useful insights.
Improve your PM plan by identifying problem assets
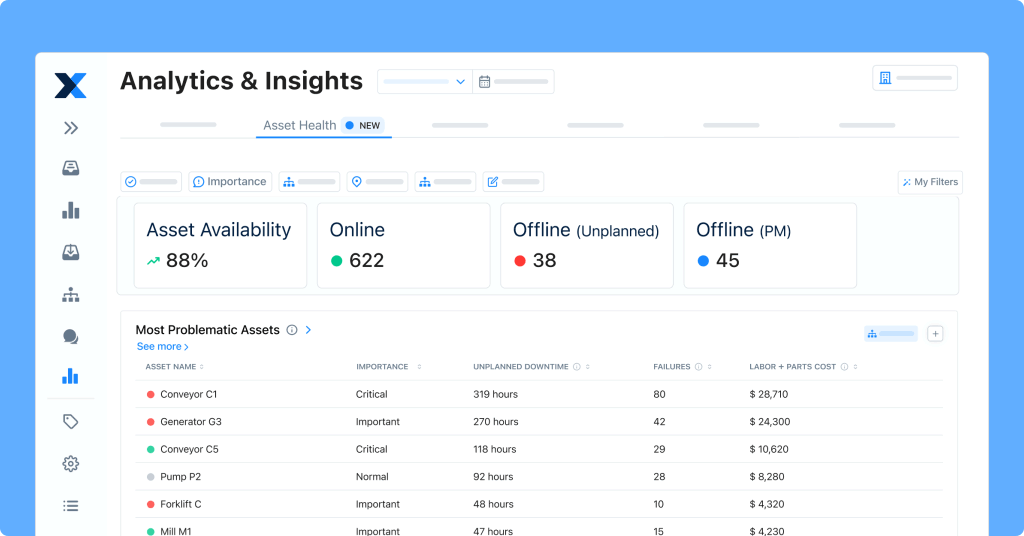
Asset Health Insights enables you to quickly identify the machines that cause the most unplanned downtime and cost the most to maintain. This information helps you to make data-driven decisions on where to prioritize work and plan capital expenditures.
The Most Problematic Assets report helps you to identify your “bad actors” based on parts and labor costs, failures, downtime hours, and more. You can sort your assets by the problem indicators that matter most to you, to help you spot machines that need a different PM strategy or need to be replaced altogether.
With Unplanned vs. Planned Downtime, you can see what proportion of the downtime on your assets is planned, and how much is unplanned. This allows you to measure the success of your PM plan on each asset, and identify opportunities to become more proactive with certain machines.
Boost reliability with root cause analysis
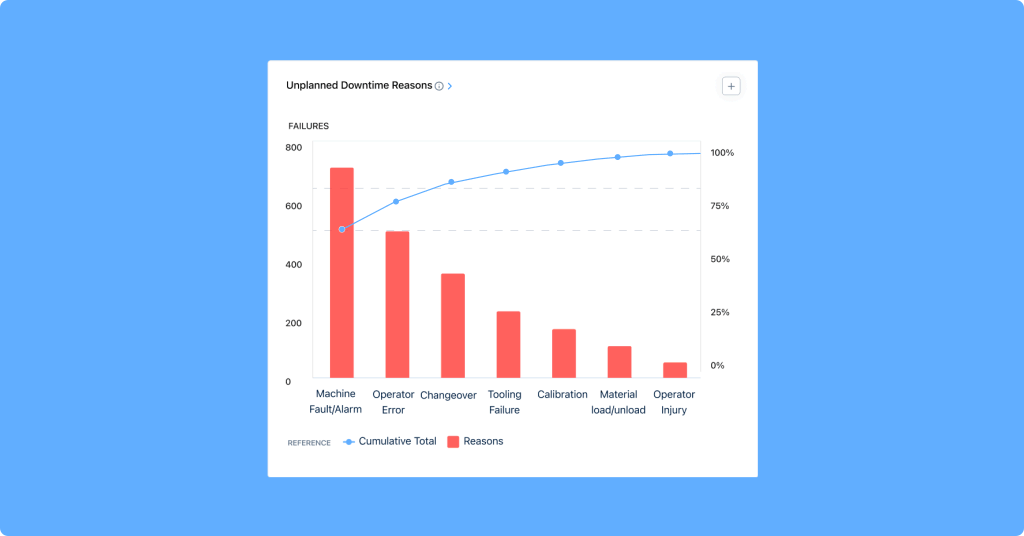
When you can’t quickly see why your machines are failing, you’ll continue to just fix the symptoms instead of addressing the root cause. Asset Health Insights makes root cause analysis easier than ever by allowing you to see which specific issues cause the most unplanned downtime and require more proactive attention.
The Unplanned Downtime Reasons report ranks the biggest causes of unplanned downtime across your organization or within a select group of assets. This helps you focus your PMs and parts orders on the highest-impact problems. You can also drill down into each failure cause to see which machines are the most affected.
A Cumulative Total line helps you prioritize work by telling you what proportion of your total failures can be attributed to a select group of causes.
Unearth problems faster with real-time monitoring
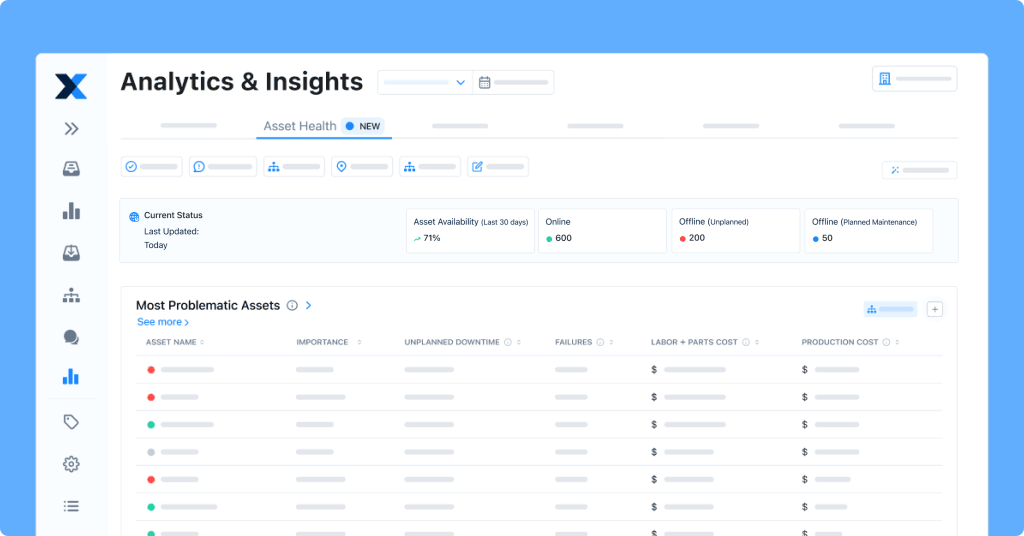
You also can use Asset Health Insights to get a real-time snapshot of how your assets are performing.
The Current Status report shows how many of your assets are currently online and offline, and calculates your asset availability for the past 30 days. This helps you to unearth issues that might need to be addressed right away, and provides an instant answer to the question, “How are we doing today?”
Simplify asset management, from the shop floor to the top floor
The tracking and monitoring tools within MaintainX provide maintenance managers with clear steps they can take to increase uptime and address root causes of failure.
Easy-to-use mobile workflows and IoT integrations make it possible to record instances of downtime accurately, at the moment it occurs, along with valuable root cause context.
With Asset Health Insights, this data becomes quickly accessible and actionable, both for maintenance managers, purchasers, and company leadership.
To learn more about Asset Health Insights, book a demo today.
FAQs
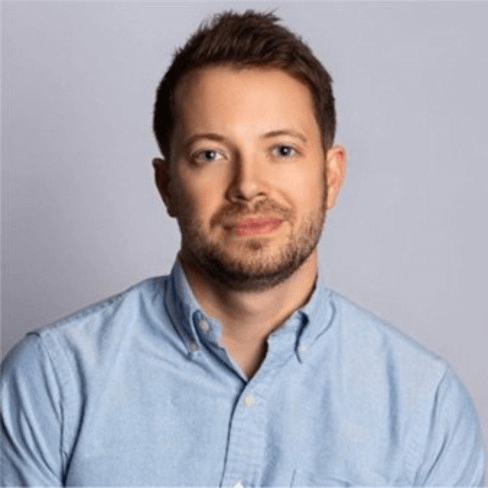
Colin Strachan is a Senior Product Marketing Manager at MaintainX, with a background in journalism and almost a decade of experience in SaaS marketing. In the past few years, he has worked with some of the world’s largest enterprises to adopt software that empowers their employees to work more effectively.