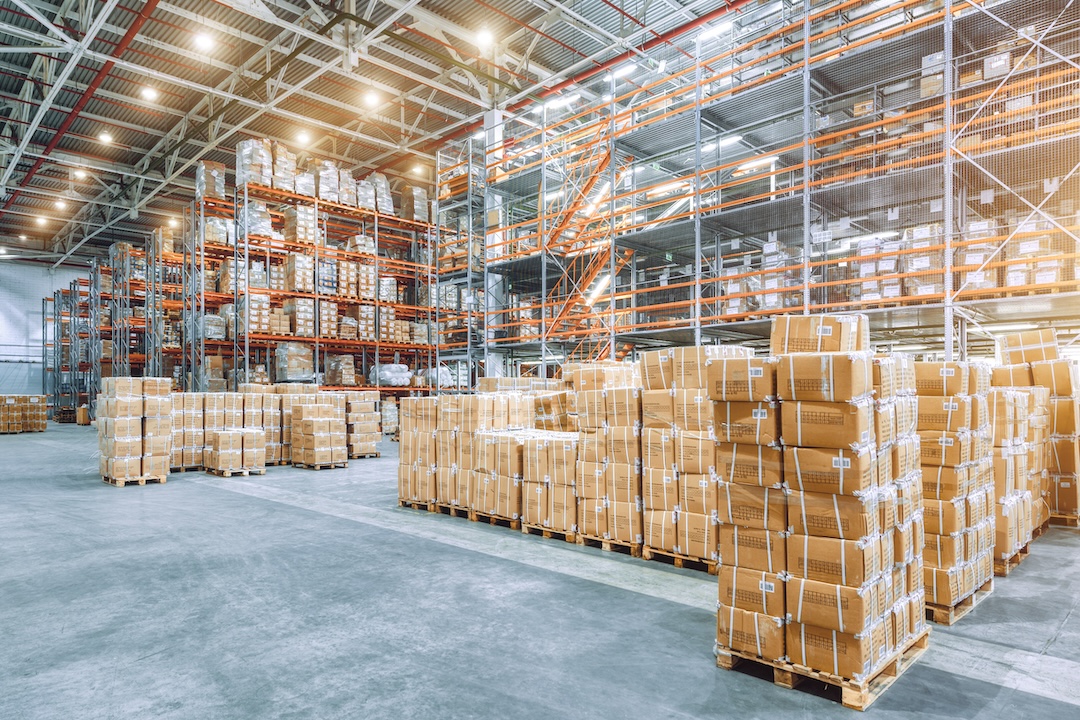
Even the best-laid plans can go awry, and the world of industrial maintenance is no different. Picture this: You've crafted a robust preventive maintenance strategy with perfect schedules. Yet, your team is still stuck in reactive cycles. If this sounds familiar, you're not alone.
Recently, MaintainX released the 2024 State of Industrial Maintenance Report—a comprehensive analysis of critical trends in today's industrial maintenance landscape. We uncovered some interesting findings, like the unplanned downtime paradox and new ways to tackle the skilled labor shortage.
One trend that stood out was the preventive maintenance intention-action gap. Our analysis of survey results showed that while most facilities (87%) use preventive maintenance strategies in some form, more than half (56%) spend the majority of their maintenance time on unplanned work.
In this post, we’ll look at what’s driving this trend and what it could mean for the future of industrial maintenance, as well as explore how companies can better bridge the gap between intention and action.
Preventive maintenance is on the rise
First, the good news: 86.8% of respondents to our survey reported actively using preventive maintenance. Encouragingly, predictive maintenance (PdM) is also gaining significant traction. Our survey found that PdM is the third most commonly utilized maintenance program, with nearly one-third of facilities (30.2%) reporting its use.
The widespread implementation of predictive and preventive maintenance shows that facilities understand the importance of scheduled maintenance in minimizing downtime and optimizing equipment lifespan. It’s no longer just about avoiding problems but maximizing efficiency.
Woody Rogers, Maintenance Supervisor at Cintas, echoes this fact: “We strive to operate higher than the standard,” he says. “So it’s critical for us to stay ahead of any issues that might impact asset performance or uptime. By monitoring and analyzing historical and real-time data that we collect on the conditions of our assets, we’ve been able to proactively identify, detect, and fix issues before they become bigger problems.”
A troubling gap between intention and action
Despite the popularity of preventive maintenance strategies, facilities still rely heavily on run-to-failure maintenance. Over half of responding facilities (59%) spend less than half of their time (41%) on planned maintenance activities.
Things aren’t this way because facilities don’t understand why preventive maintenance matters. In many cases, facilities want to leverage preventive maintenance but find themselves held back for the following reasons:
Unplanned factors
Sometimes, unplanned factors derail even the best of plans. “There are just some things that you can’t plan for,” says Justin Foat, Fleet Maintenance Manager at Herlache Truck Lines. “For example, during the hotter months, you can send out a truck fitted with brand new tires, have them hit the hot pavement, roll over a rock, and boom, it blows.”
Inadequate preparation
Effective preventive maintenance is impossible without the right tools. Teams need robust preventive maintenance software to help with everything from maintenance scheduling to managing parts inventory.
However, one limiting factor is a lack of proper planning. Many managers invest in these tools without considering how their teams will adopt and utilize them effectively. It’s not enough to simply introduce new software—managers must create a comprehensive plan that includes staff training, clear communication on the benefits, and ongoing support to drive adoption.
Lack of data
Another reason teams get stuck in reactive maintenance cycles is inadequate data. Without data, teams can’t stay ahead of issues and create schedules that work. “You might initially build a preventive maintenance schedule based on the manufacturer's guidelines,” says Chris Wilcox, Maintenance Manager at Univar Solutions. “However, as you perform the work and analyze the data, you may find that the manufacturer missed critical areas, and that’s leading to unplanned maintenance work.”
Turning the tide: How to prioritize preventive maintenance
To bridge the gap between intention and action in maintenance, companies need to make deliberate changes. By taking proactive steps, organizations can turn things around and see real improvements in their preventive maintenance. Here are a few ways:
Analyze past work orders to uncover new PM opportunities
Study historical work order data to spot patterns that may be costing your company. Recurring equipment breakdowns, frequent repairs, and problematic assets can signal where you need new or enhanced preventive maintenance tasks.
As Chris Wilcox says, “You need experience and data to understand the impactful things you need to perform on your equipment. By using that information, you can refine your schedule, prioritize critical tasks, and ultimately create a more effective preventive maintenance program that minimizes time spent on unplanned maintenance work."
Invest in training and education
Proper training is essential for a successful preventive maintenance program. Without it, you’ll create maintenance schedules your teams don’t adhere to and assign tasks your technicians cannot complete. Equip your team with skills to perform maintenance tasks and understand how equipment works. Also, make sure your team can follow maintenance SOPs, properly record data, and efficiently use tools like CMMS software to streamline their work.
Foster a culture of proactive maintenance
Leadership needs to champion preventive maintenance and make it a core part of the company's culture. When managers and supervisors prioritize planned maintenance and show how it can boost equipment uptime, enhance safety, and minimize stress, it encourages teams to shift away from reactive firefighting.
Implement preventive maintenance software
To make preventive maintenance easier, companies should invest in mobile-first software. Prioritize tools that automate work orders, scheduling, and tracking. By doing this, you’ll eliminate manual maintenance management and free up time for your team to focus on what matters most—keeping assets running at their best.
Turn plans into actions: Bridging the gap for preventive maintenance success
Bridging the gap between intention and action starts with a deliberate, hands-on approach. It’s about more than just having a plan—it’s about executing it effectively. By analyzing past work orders, investing in training, and shifting to a proactive maintenance mindset, companies can ensure their teams are better equipped to prevent breakdowns before they happen.
By making preventive maintenance an integral part of your culture, you're not just transforming your maintenance approach—you're redefining what's possible for your organization. You're empowering your team, fostering innovation, and positioning your company for long-term success in the face of ever-evolving challenges. You’ll also set the stage for advanced approaches like predictive maintenance that can take your facility to the next level. It all starts with implementing the right tools. Turn your plans into action with MaintainX, and kickstart the journey to a streamlined, more efficient tomorrow.
Want to get the full insights? Download the report today
The 2024 State of Industrial Maintenance report contains exclusive insights from 1,200 maintenance, repair, and operations (MRO) professionals about the ever-evolving maintenance landscape. Download the full report to discover the key trends shaping industrial maintenance in 2024 and beyond, including:
- The top threat to undisrupted operations.
- Strategies top-performing facilities use to address skilled labor shortages.
- The surprising gap between preventive maintenance implementation and adoption.
- Key metrics and KPIs that facilities commonly monitor to measure performance.
Don't let your facility fall behind. Download the report today and equip yourself with data-driven strategies to optimize maintenance, lower costs, and enhance efficiency.
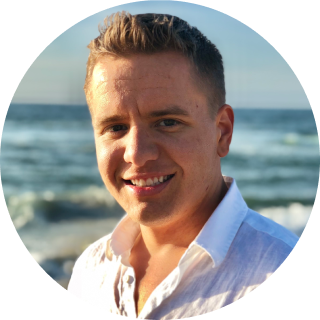
Nick Haase is a co-founder for MaintainX and is responsible for designing and leading the go-to-market strategies. He is a subject-matter expert in emerging CMMS technologies.