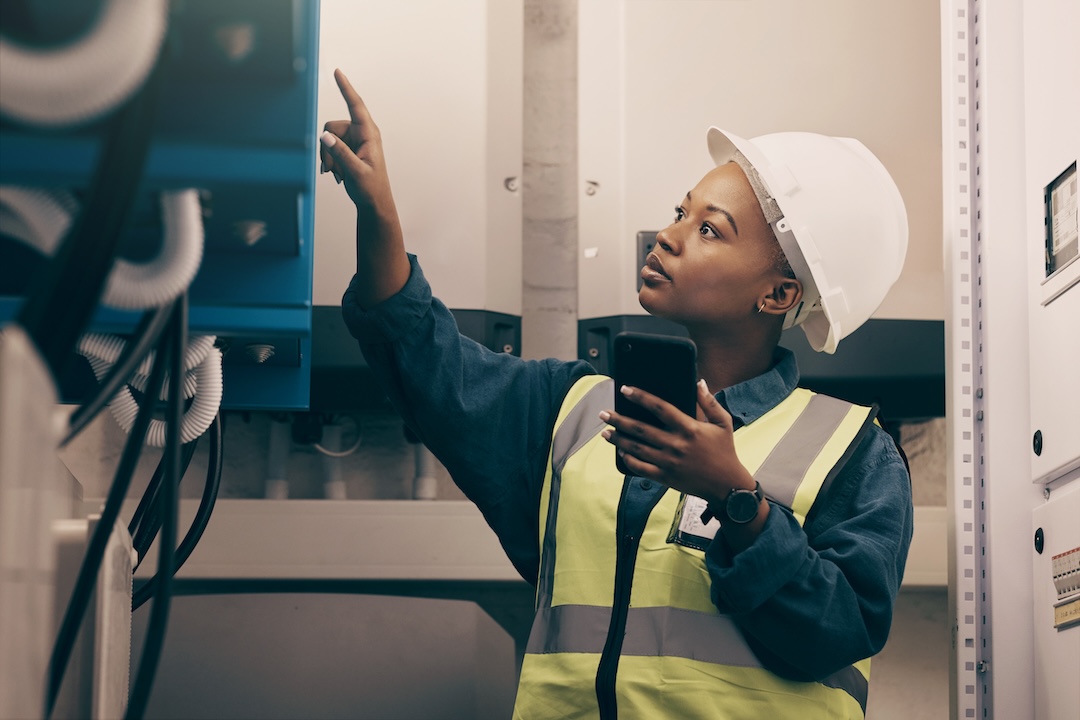
Over the past few months, MaintainX has been working to get a pulse of today’s industrial maintenance landscape. Through deep research, conversations with a wide swath of industry professionals, and our own expert knowledge, we’ve put together MaintainX’s inaugural State of Industrial Maintenance Report.
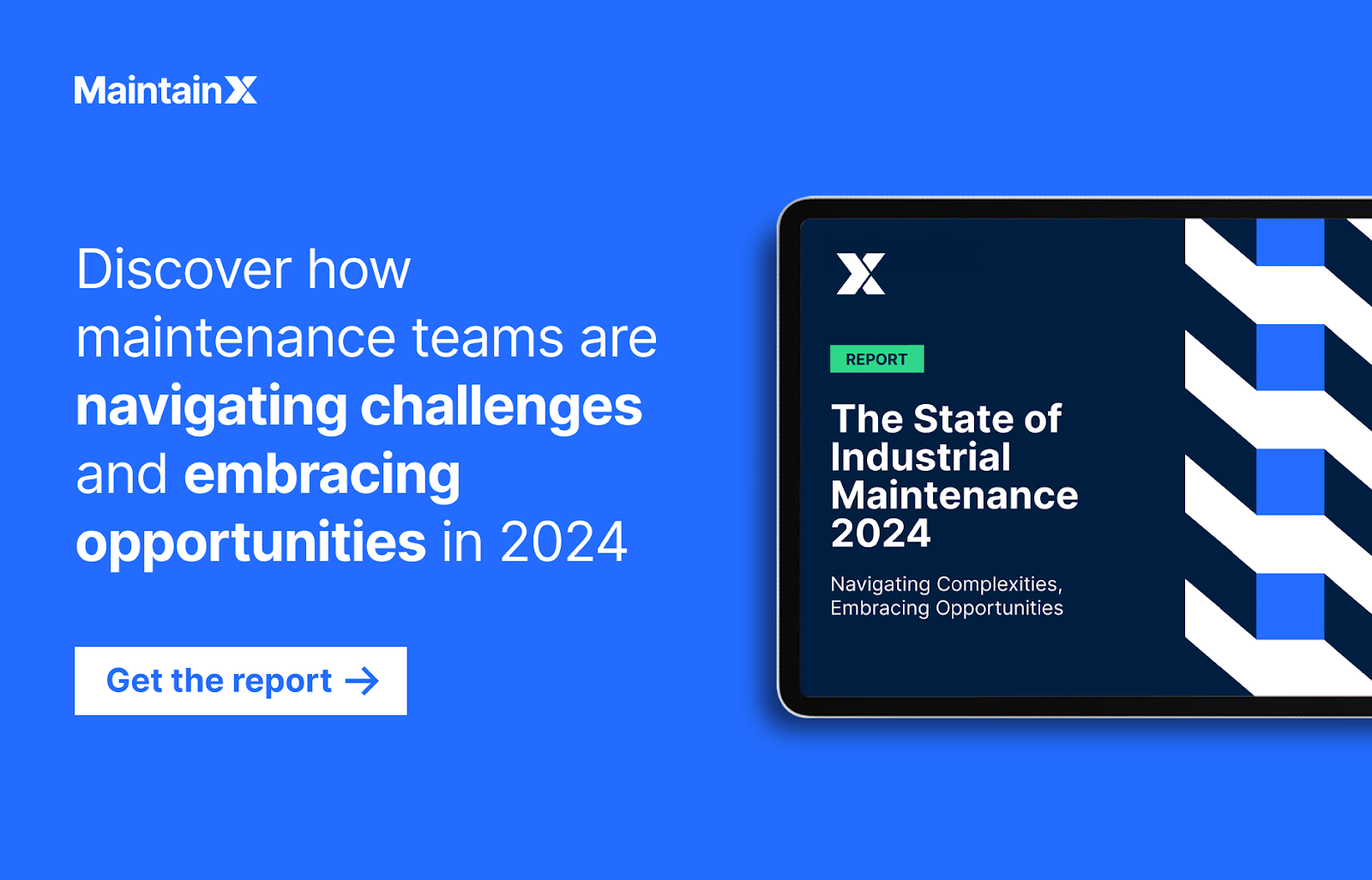
The 2024 State of Industrial Maintenance Report explores key trends shaping industrial maintenance and offers strategies to overcome pressing industry challenges. One of the most surprising insights is what we’re calling the “unplanned downtime paradox.” To put it simply, despite most companies (85.2% of respondents) experiencing less unplanned downtime, a significant portion (29.4%) say the costs of unplanned downtime are rising.
In this post, we’ll delve into our findings about what’s driving this unexpected trend and what it could mean for the future of industrial maintenance.
The good news: Declining incidents of unplanned downtime
While the escalating costs of downtime raise alarms, the reduction in unplanned downtime incidents is good news. Reasons for this include:
Proactive maintenance strategies: 65% of respondents agreed that proactive maintenance has been the best way to keep unplanned downtime at bay.
Modernizing assets: In 2023, companies increased investments in plants and production facilities by 63%—the biggest jump since 1951. 43% of MRO professionals credit these strategic investments in replacing aging equipment for the decrease in unplanned downtime.
Investments in training: Improving the quality and frequency of training was the third most frequently selected reason (27.3%) for the decrease in unplanned downtime in the last 12 months.
The cost of unplanned downtime is on the rise
Despite fewer incidents, the financial hit from unplanned downtime incidents is climbing. Almost 30% of respondents noted a concerning increase in the cost of unplanned downtime over the past year. So, while these disruptions may be happening less often, they’re taking a bigger bite out of the budget when they do.
On average, an hour of unplanned downtime costs a facility around $25,000. For larger organizations, this can skyrocket to more than $500,000. In short: a marginal decrease in unplanned downtime may not be enough to offset the growing cost per incident.
The good news is the cause isn’t a mystery—let’s examine the reasons for this paradox next.
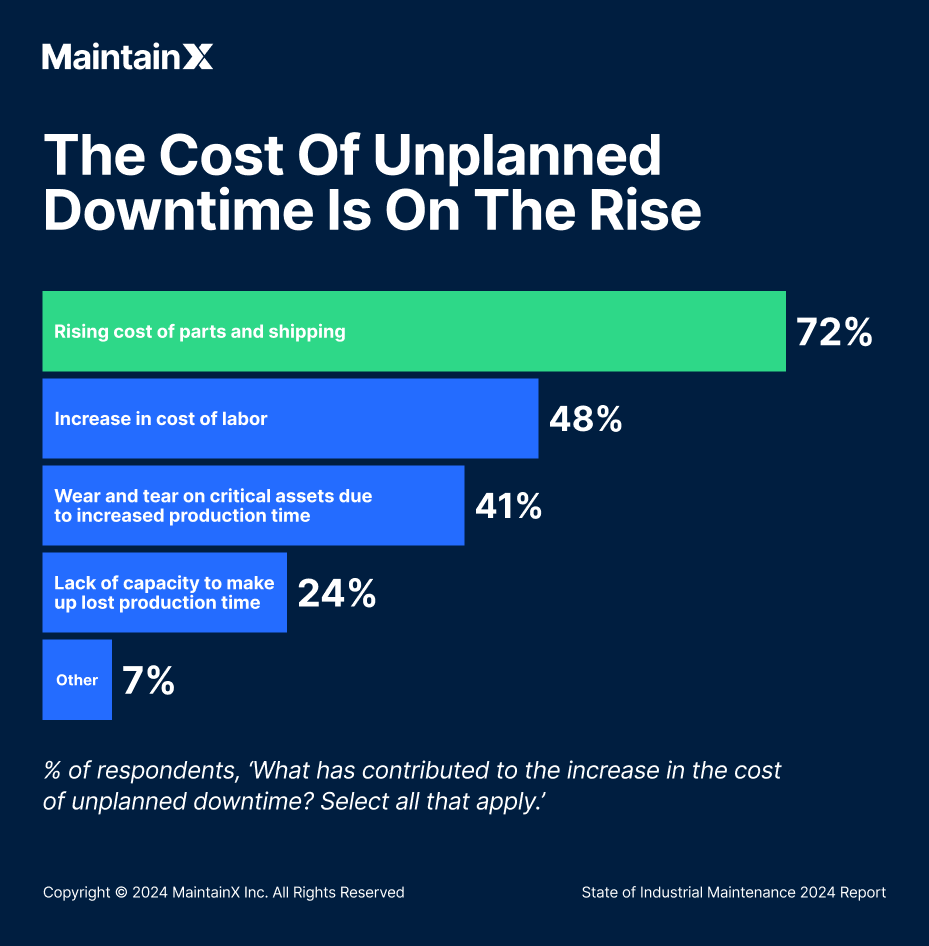
Inflation and supply chain challenges
72% of respondents attributed the increased cost of unplanned downtime to rising parts and shipping costs.
Justin Foat, Fleet Maintenance Manager at Herlache Truck Lines, explains: “Everything’s gotten more expensive and longer to procure. Inflation has significantly increased the cost of parts and raw goods, from tires to doors, that we need to maintain our fleet.”
Inventory expenses
Shipping costs have been declining since their peak during the pandemic, but now they’re climbing again. The Red Sea shipping crisis has thrown a wrench in commercial shipping, and attacks on vessels have led to a drop in maritime activity. As a result, freight rates and shipping insurance costs are shooting up.
Labor costs
Higher labor costs are making unplanned downtime even more expensive. Nearly 48% of respondents blamed rising labor spending for the spike in downtime costs. With prices for housing, food, and other essentials climbing, wages have gone up too. To top it off, the skilled labor shortage is making it tough to fill positions, causing delays across the board.
Deteriorating asset health
As demand surged after the COVID-19 pandemic, many facilities pushed their critical assets harder to keep up. However, according to the 2021 State of Manufacturing report by Oden, while demand shot up by 25–50%, most manufacturers could only boost capacity by 6–10%. Now that the backlog is clearing, the toll on equipment is clear—parts are wearing out faster, and repairs and replacements are more frequent. 40.6% of respondents cited wear and tear on critical assets as a major reason for increasing downtime costs.
How facilities are responding
MRO professionals have already been taking significant steps to combat these increasing costs. Some of these steps include:
Improving inventory processes
Rising costs have highlighted the need to improve MRO inventory management. 58.9% of facilities that successfully cut the cost of unplanned downtime credit their success to better parts inventory management.
Learn how to create a digital inventory management system
Evolving maintenance strategies
With inflation driving up equipment costs and supply chain disruptions extending lead times, teams want to extend equipment life through proper maintenance. Better maintenance can reduce the risk of unexpected breakdowns and keep aging assets running until replacements arrive. This way, teams can avoid the expensive route of completely replacing their aging equipment.
Improving quality and frequency of training
Over a quarter (28.3%) of respondents dealing with aging equipment plan to enhance their training programs. As Jeremiah Dotson, Equipment Tech Manager at Amfab Steel shares, “You won’t always have the luxury of replacing aging equipment. By teaching technicians about the machines and walking them through the documentation, we ensure everyone has the know-how to handle and fix failures when they happen.” Just like the previous step, this approach will help keep equipment in better condition and running for much longer, preventing the need for costly replacements.
The path forward with MaintainX
If this paradox makes one thing clear, it’s that a balanced approach is crucial for success. Decreasing incident numbers can lull you into a false sense of security, so it’s important to maintain a holistic view of operations at all times.
“Ready access to critical maintenance data has been a game-changer for us. It’s been the catalyst for the evolution of our maintenance program at Univar.
By combining the data with hands-on experience and knowledge, we’ve been able to make assessments of parts that we should carry in order to help with uptime (instead of waiting for parts to come in), optimize maintenance schedules, and make better, data-driven decisions around budget and labor allocation.” — Christopher Wilcox, Maintenance Manager at Univar Solutions
Data-driven decision-making is key: By leveraging advanced analytics and predictive maintenance technologies, facilities can better address potential issues and optimize resource allocation.
Want to get the full insights? Download the report today.
The State of Industrial Maintenance Report contains exclusive insights from 1,200 maintenance, repair, and operations (MRO) professionals about the ever-evolving maintenance landscape. Download the full report to discover the key trends shaping industrial maintenance in 2024 and beyond, including:
- The top threat to undisrupted operations.
- Strategies top-performing facilities use to address skilled labor shortages.
- The surprising gap between preventive maintenance implementation and adoption.
- Key metrics and KPIs that facilities commonly monitor to measure performance.
Don't let your facility fall behind. Equip yourself with data-driven strategies to optimize maintenance, lower costs, and enhance efficiency.
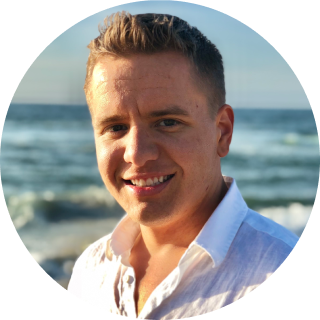
Nick Haase is a co-founder for MaintainX and is responsible for designing and leading the go-to-market strategies. He is a subject-matter expert in emerging CMMS technologies.