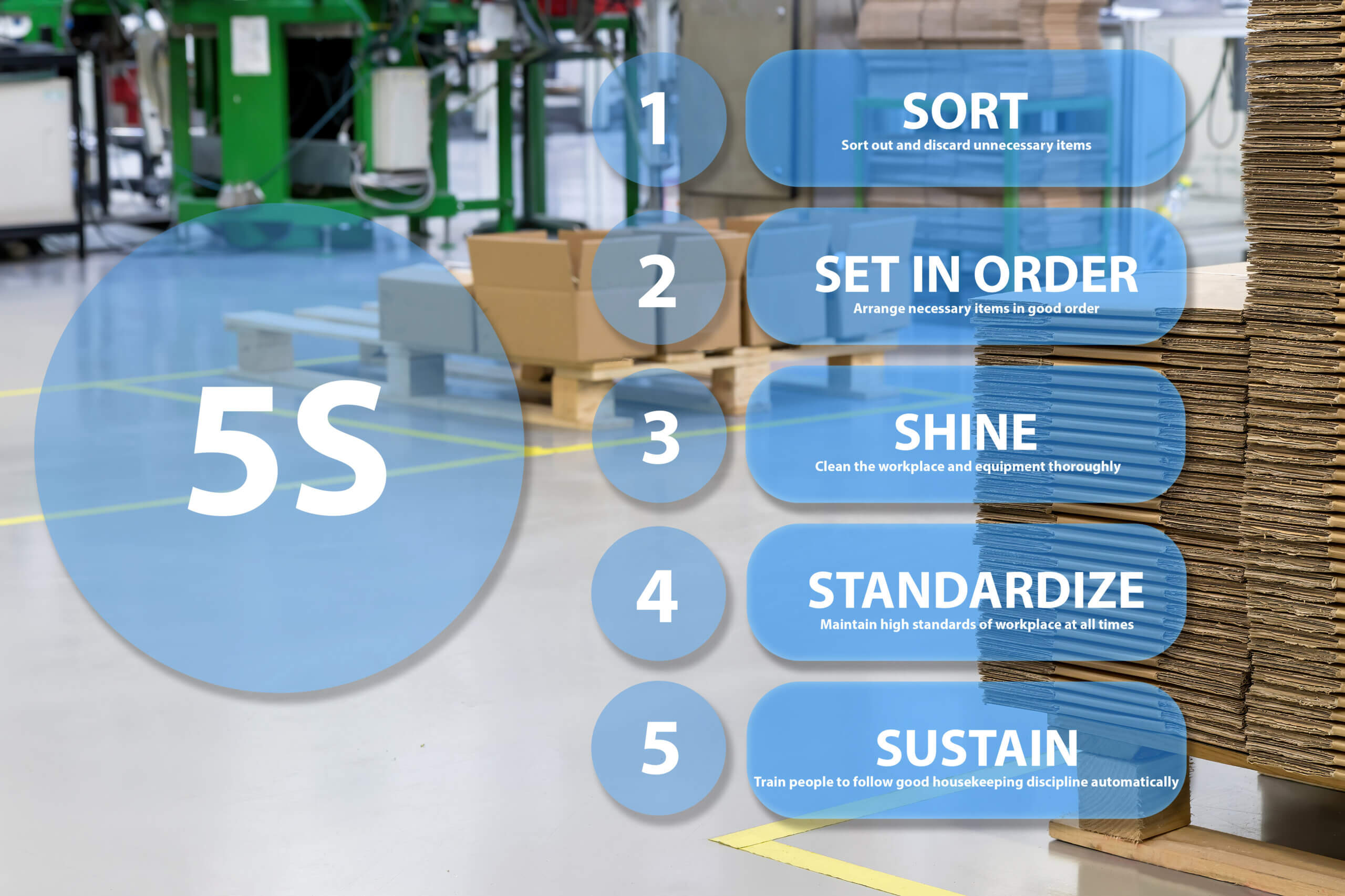
What’s the best method to apply towards maintenance? Of all the maintenance strategies out there, which one should you adopt? Preventive maintenance with standard operating procedures? Condition-based or predictive maintenance with meter-based triggers? Reactive maintenance with emergency procedures? ’s hard but if you’re thinking of strengthening your manufacturing maintenance plan, consider a 5S audit.
There’s so much information out there, with so many options, that sometimes it can seem overwhelming. The truth is every principle or system has its pros and cons, and what really matters is your business.
We recommend you craft your 5S audit based on your company’s needs. You’ll know your audit is working when you can imagine hitting an 80:20 ratio, with 80 percent preventive and only 20 reactive maintenance.
“If you want to get serious about wringing out significant waste and supercharging your processes, then you should get serious about lean improvement tools.”
StrateChi
What Is the 5S System?
The 5S audit checklist is a lean framework for creating a more efficient workspace. It is an approach to identify and implement potential improvements in the workplace. It is based on the idea that an optimized work environment will lead to better work processes.
By extension, more efficient operations will lead to better products. It is a form of quality management and a fundamental principle of lean manufacturing. Specifically, the methodology flows from the kaizen philosophy of continuous improvement. Implementing this in your work area involves the following steps from a set template. The steps involved in 5S are:
- Seiri (Sort)
- Seiton (Set in order)
- Seiso (Shine)
- Seiketsu (Standardize)
- Shitsuke (Sustain)
Let’s take a closer look at what they mean.
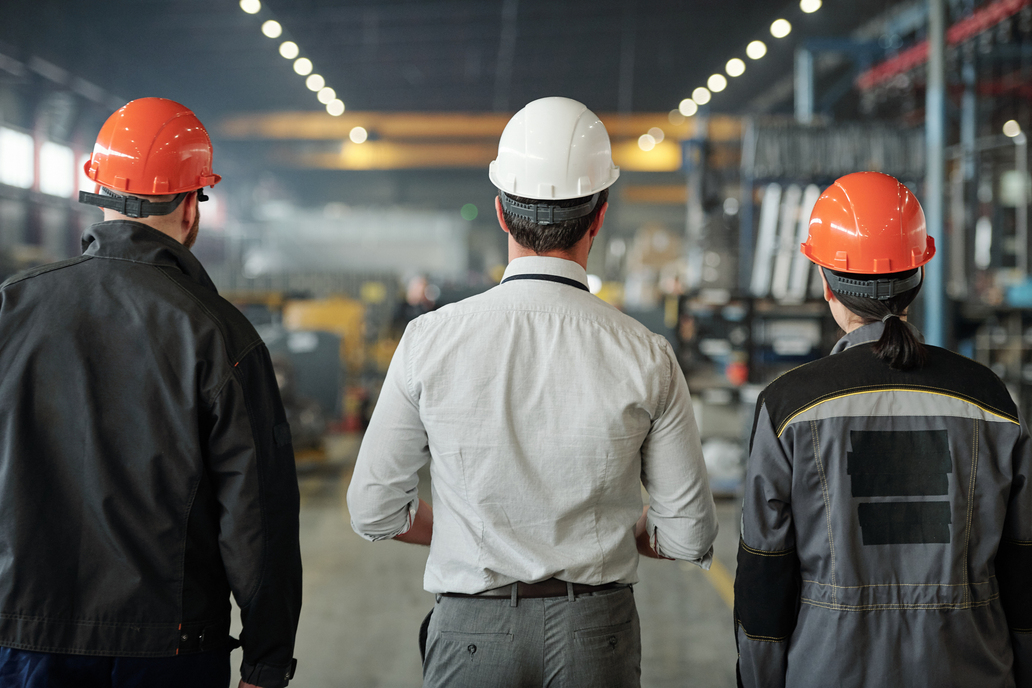
Steps in the 5S Audit
Sort
When running a 5S program, the first step is to sort through a work area. The first step is a Gemba walk, where you look at everything from work materials to decorations to identify necessary and unnecessary items. “Gemba” is a Japanese word for “the real place” and refers to getting your own boots on the ground with your team to see firsthand what they are working on. Are there any unnecessary tools around? Are pallets not being used? Machines that only run for a month a year? Label unnecessary items with red tags before transferring them to storage areas.
Set in Order
After deciding what to keep and what to remove, organize the remaining items to determine how to store them. Label items for easy identification. Apply color coding to simplify the inventory process and ensure you can locate items when needed. Consider applying QR or barcodes to find them with a CMMS like MaintainX. Use floor markings to ensure walkways and storage paths lead you to the items.
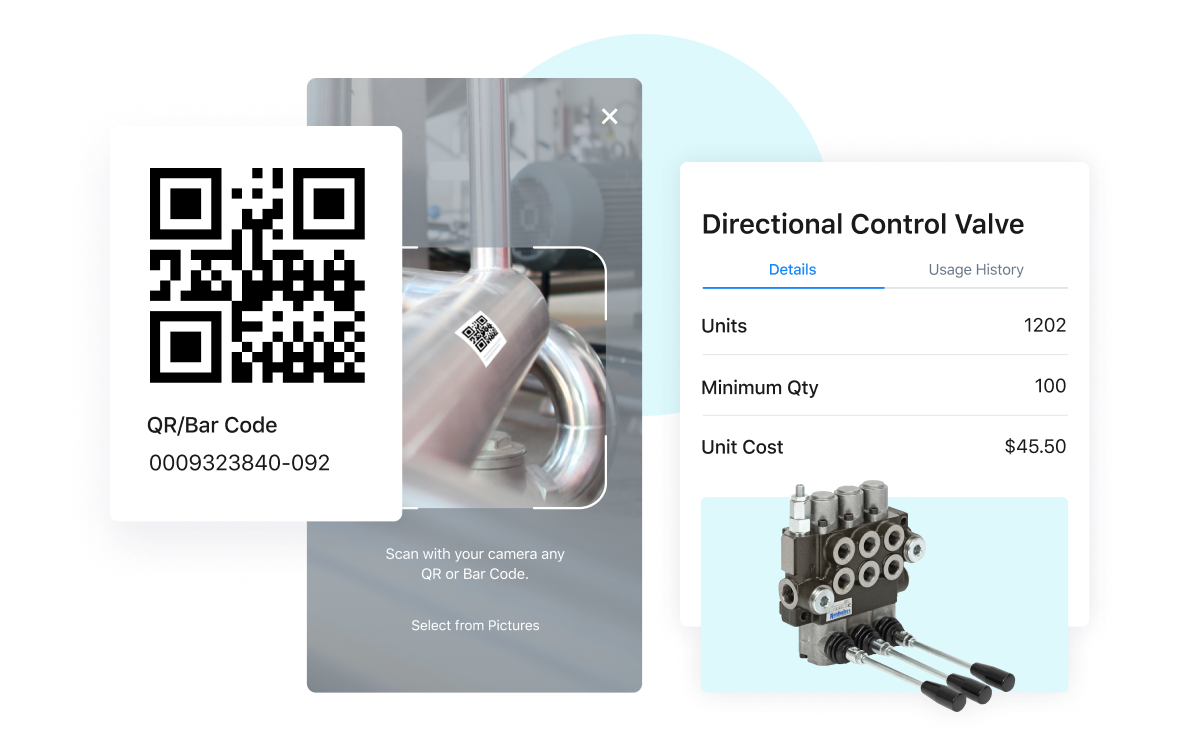
Shine
This doesn’t literally mean making things sparkle, but it refers to keeping workstations and general work areas clean. The important thing here is functionality. So instead of aesthetic cleanliness, think more about keeping workspaces free of obstruction and clutter. It also includes carrying out maintenance on any work equipment used.
Standardize
As stated, you’ll likely be looking to craft a specific system for your organization or team members. When doing this, you’ll need to establish your 5S standards and make sure your audits follow set procedures.
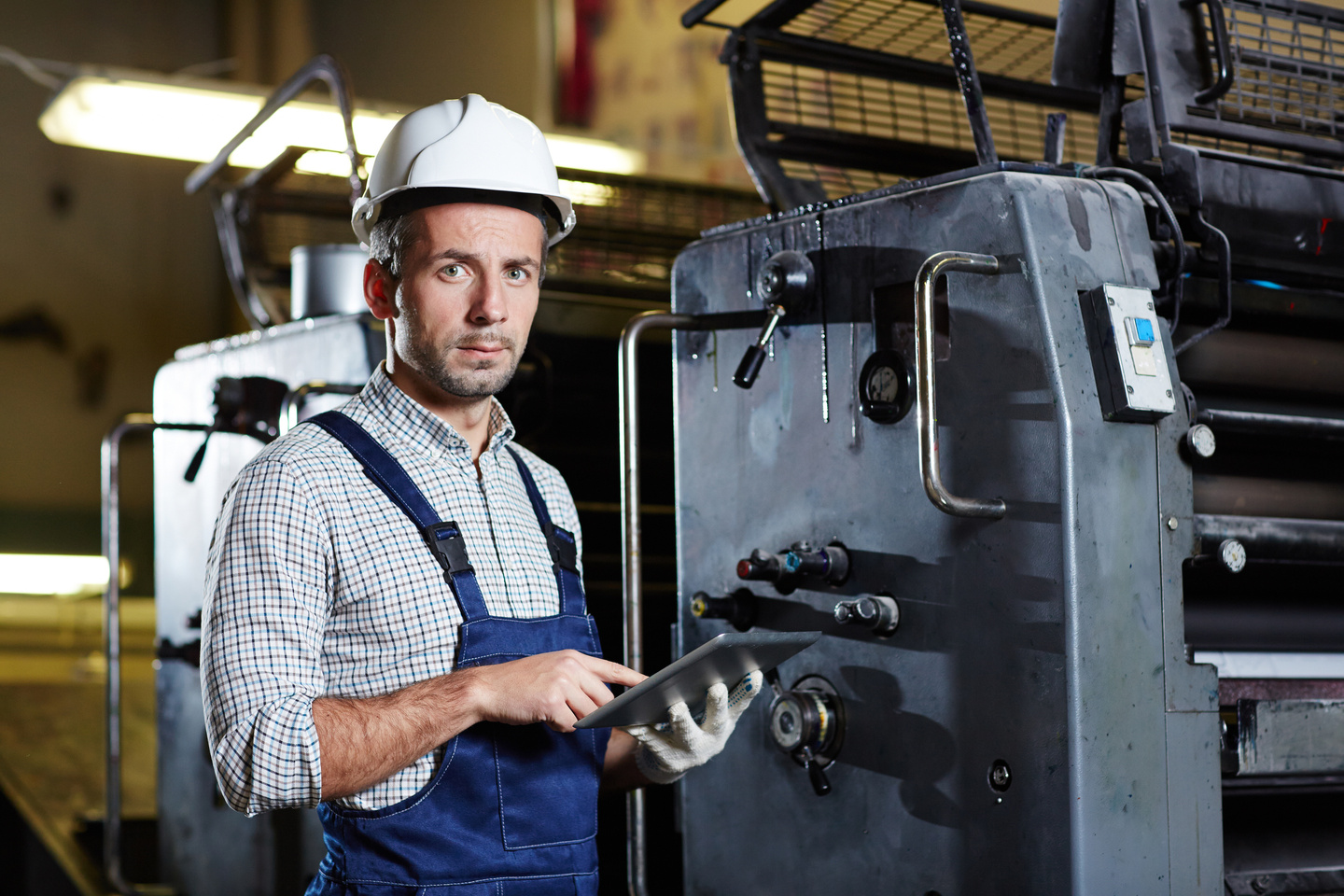
Sustain
After establishing your processes, you’ll want to sustain your efforts through consistent implementation and reiteration. You’ll want to do things like create cleaning schedules along with other more thorough maintenance activities.
“Improvement usually means doing something that we have never done before.”
Shigeo Shingo, Toyota Production System Expert
Why Carry Out a 5S Audit?
Conducting a 5S audit will help your company identify areas to improve in terms of organization and cleanliness. The audit also can identify hazards and safety issues. By regularly conducting 5S audits, you will be able to ensure that your company’s workplace is well-organized, efficient, and safe for all employees.
In addition to these benefits, a 5S audit can help you improve your company’s overall performance and profitability. By carrying out regular 5S audits, you can improve your company’s maintenance workflows:
In summary, implementing a 5S system will help you to:
- Reduce waste
- Optimize inventory and storage space
- Improve preventive maintenance standard operating procedures
- Improve worker safety
- Improve maintenance and production workflows
Get MaintainX to Optimize Your 5S Audits
Despite the many benefits of the 5S system, your teams may find 5S challenging to sustain the effort. When is the best time to conduct audits—every week, month, or quarter? And how do you know your efforts will yield time and cost improvements?
MaintainX CMMS, with its myriad capabilities and features, can streamline the process for you. With MaintainX, you can:
- Establish an action plan
- Schedule your actions
- Schedule audits
- Digitize audit forms and SOP templates
- Track Key Performance Indicator (KPI) data over time, and in real time (!)
- Automate preventive maintenance standard operating procedures
- Support your teams with real-time training
MaintainX is available on desktop and mobile app, giving users unprecedented control and real-time connectivity right from the palm of their hand.
FAQs
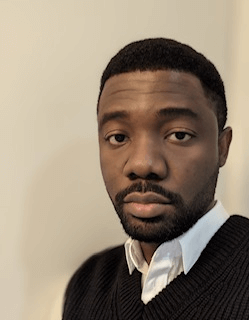
Lekan Olanrewaju is a content writer with years of experience in media and content creation. He has held positions at various media organizations, working with and leading teams at print magazines, digital publications, and television productions.