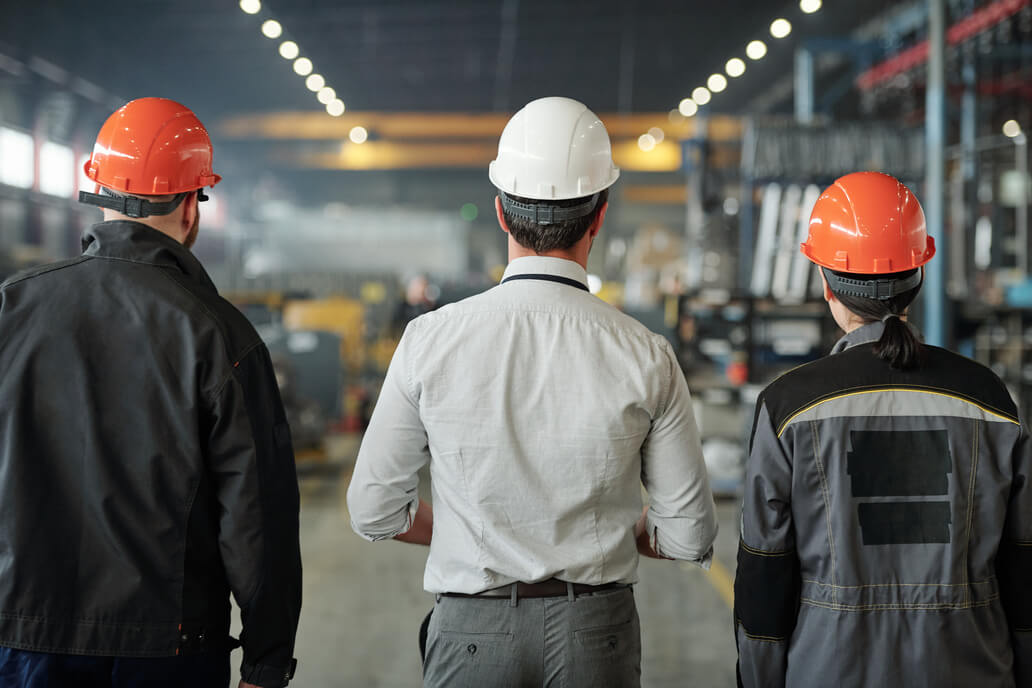
Improve Efficiency with a Gemba Walk
A Gemba Walk is a structured and process-driven walk around a warehouse, production facility, or manufacturing plant.
Stemming from Kaizen and Lean processes, the Gemba walk is a great addition to your preventative maintenance, asset management, and facilities management processes.
What Does Gemba Mean?
So what is “Gemba” anyway?
Gemba is derived from a Japanese word that means “the real place” or “the place where value is created.”
For manufacturers, this might be the factory floor, and for FM professionals, the plant room. Your “real place” is typically the coalface of your operation where you physically produce value for your customers. For example, your production line or the work area where you conduct equipment maintenance is where you produce and maintain value.
This definition gives insight into how critical a Gemba Walk is to uncovering process improvements and efficiency gains in your facility.
Covering a series of specific steps, a Gemba Walk allows maintenance teams to gather direct knowledge and feedback from their operations, with the goal of process improvements.
However, a walk without a plan won’t deliver the actionable insights you can use to improve your operation. You need a structure to follow which we’ve illustrated in the following steps (along with some points on what not to do during a Gemba Walk).
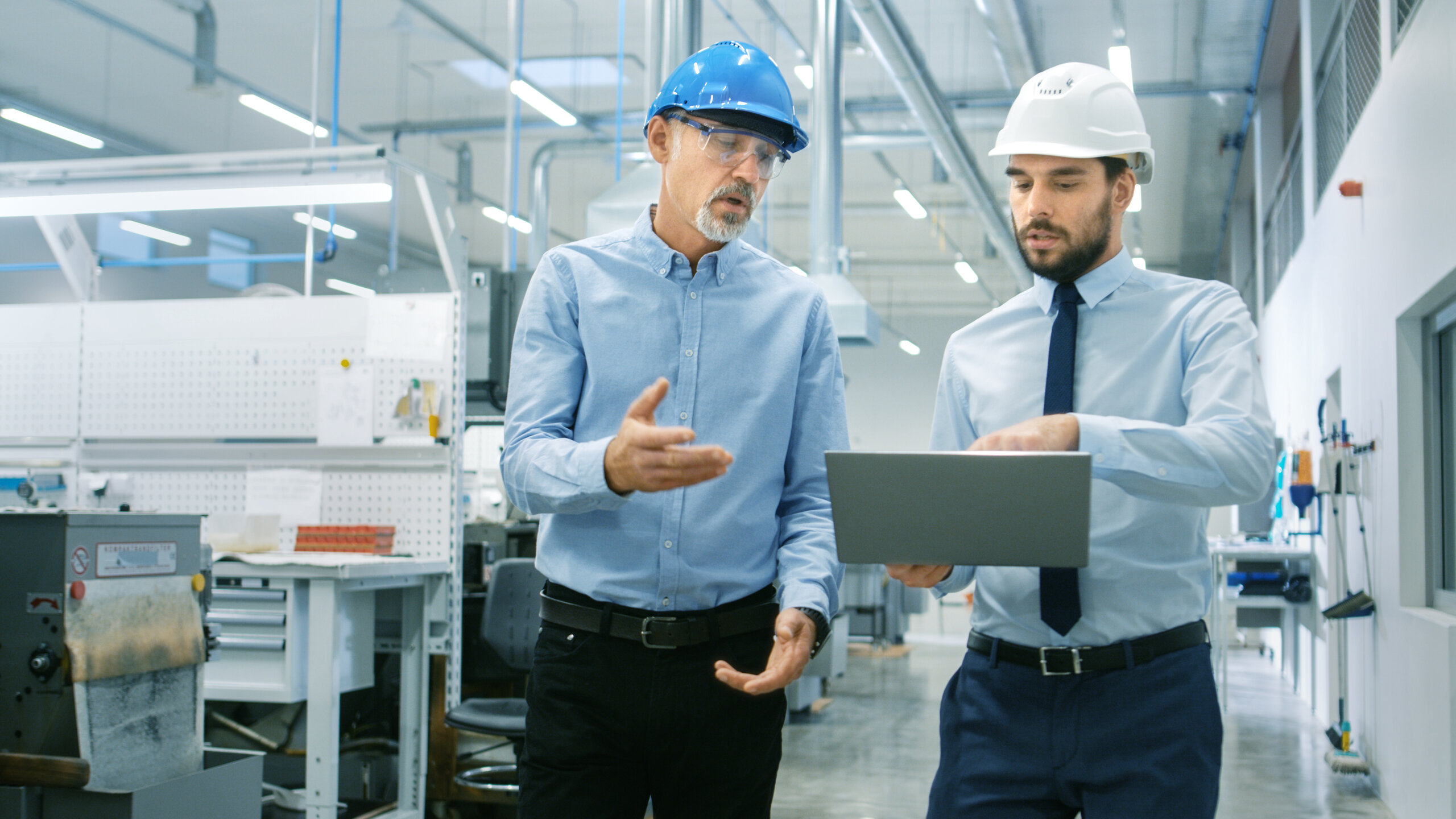
6 Steps to Conducting a Gemba Walk
Depending on the size and complexity of your workplace, your Gemba Walk should take anywhere from 15 minutes to an hour.
This is generally enough time to ask your team questions and write down comments and observations. Take note of any potential follow-up points that you’d like to come back to later.
Here’s a simple step-by-step process to help you plan and conduct a successful Gemba Walk.
1. Set a Regular Time and Communicate It to the Maintenance Team
It’s a good idea to conduct your Gemba Walk once a week. Create a regular time in your calendar and make employees aware of what’s going on.
Keep everyone informed of what is taking place and why. Otherwise, staff on the ground may feel uncomfortable and may subconsciously change their work processes. Especially if they feel they are being judged on their performance.
2. Prioritize One Area to Focus On
Rather than attempting to observe everything all at once, pick a single area in which you’d like to make improvements, such as safety or cost-efficiency.
Going too broad may result in lengthy walks that lack focus. This lack of focus can cause your team to disengage and lose interest in giving constructive feedback.
For the best results, keep it short, sharp, and to the point.
3. Ask good questions
Communicating with your team is vital to the Gemba Walk process. Have a pre-prepared list of questions for your maintenance team. Be sure to frame the questions with curiosity rather than blame.
You might like to tailor your checklist to your business, but some good questions to start with include:
- What responsibilities do you have?
- How does your role influence the overall company goals?
- What does success look like for this task?
- Why do you complete the task in this way?
- What is working well in this task?
- Do you believe there’s a better way to do it?
- How do you complete the task when materials are unavailable?
- Is anything preventing you from doing this task to a high standard?
- What can I do to make this task easier?
- What other processes or procedures impact your ability to complete this task?
4. Observe without Judgment
Aim to record your observations without making suggestions or trying to rectify issues immediately. Simply collect notes and photos in a maintenance app so you can easily analyze your findings later on.
5. Collate, Analyze, and Share the Information
Once your walk is complete, you will most likely have a goldmine of insights to review.
Analyzing the information you’ve accrued is best done in cooperation with your management team and often with the employees themselves. The employees may offer deeper insights when you bring them into the improvement process.
This will mean your team feels true ownership of the process and can see that their thoughts and suggestions are being taken seriously. Failing to do this may mean your team eventually becomes frustrated with the regular questions and will be hesitant to keep giving you important feedback.
Gemba Walk leaders who openly share their findings, on the other hand, experience better employee engagement and more positive relationships.
6. Close the Loop
Gemba Walks can become an important part of your overall continuous improvement processes.
While they can be used in isolation, they are much more effective when implemented as part of a continuous improvement program that runs through your whole organization.
Overall, a Gemba Walk helps to foster teamwork, helps improve safety, boosts efficiency for maintenance teams, and encourages employees to be actively involved in making improvements at an individual level.
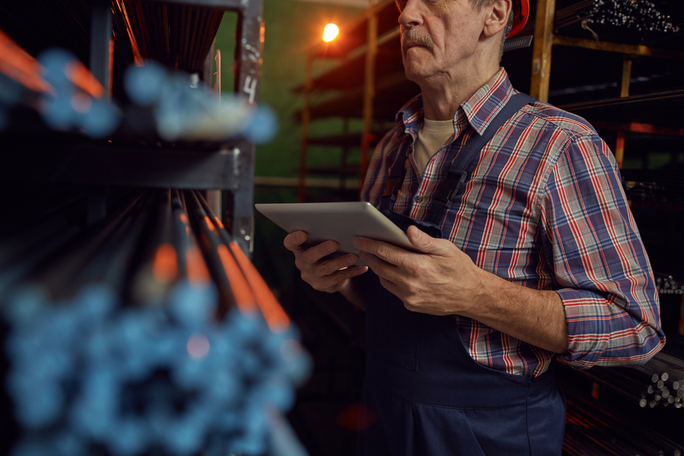
How Not to Conduct a Gemba Walk
Before you start, it’s important to understand that a Gemba Walk is NOT about finding fault with people or calling employees in for inefficient work habits.
A Gemba Walk is squarely focused on assessing the efficiency of your processes. Meaning, it’s critical to view your Walk through the lens of process improvement, not people improvement.
However, listening to people at the coalface is the key to a successful walk.
It’s often said that “the people closest to the work understand the work the best,” so collecting feedback and insights from maintenance crews, mechanics, tradespeople, and other workers at the frontlines of your operation is critical. Their comments and observations can illuminate potential issues and ideas for improvement that you may not pick up without this collaborative approach.
Ultimately, a Gemba Walk is an information-gathering exercise, not an opportunity to try to fix issues right there and then. Resist the temptation to quickly implement changes or quick fixes: the goal is to simply gather information on your current situation and save the analysis for later.
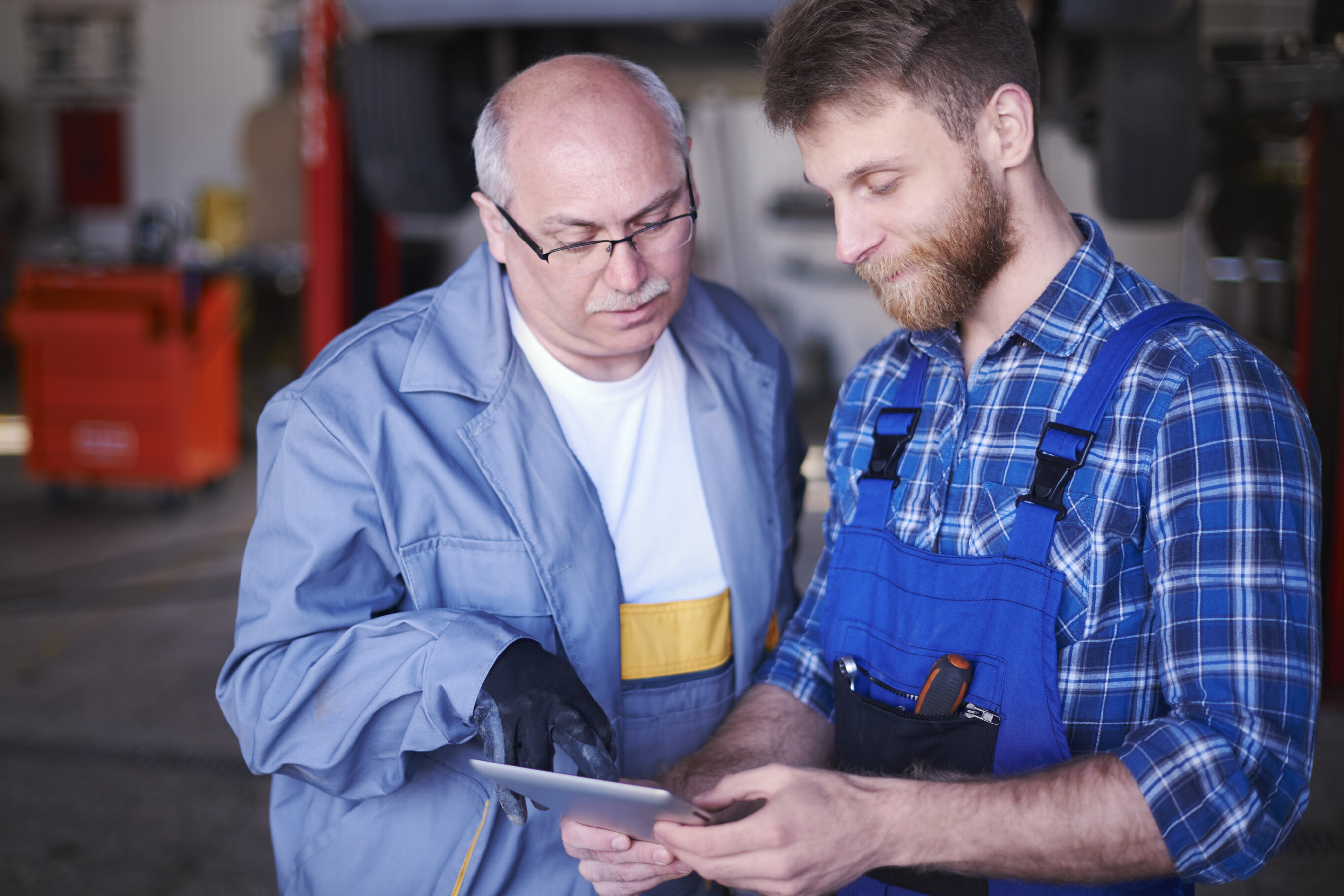
Tools to Help You Succeed
An easy way to incorporate Gemba Walks into your organization and track your progress is by downloading a comprehensive maintenance app like MaintainX. Using digital tools to your advantage will help you keep notes on your findings, track improvement metrics, and streamline operations.
And, remember, if you approach the process with a willingness to listen, respect for each team member, and a genuine interest in creating positive outcomes for everyone, the Gemba Walk will become a vital part of improving efficiency in your organization.
FAQs
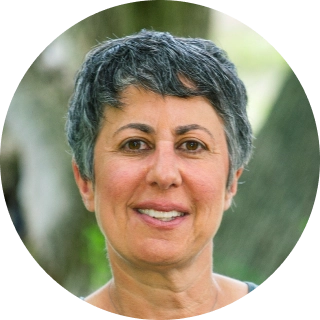
Caroline Eisner is a writer and editor with experience across the profit and nonprofit sectors, government, education, and financial organizations. She has held leadership positions in K16 institutions and has led large-scale digital projects, interactive websites, and a business writing consultancy.