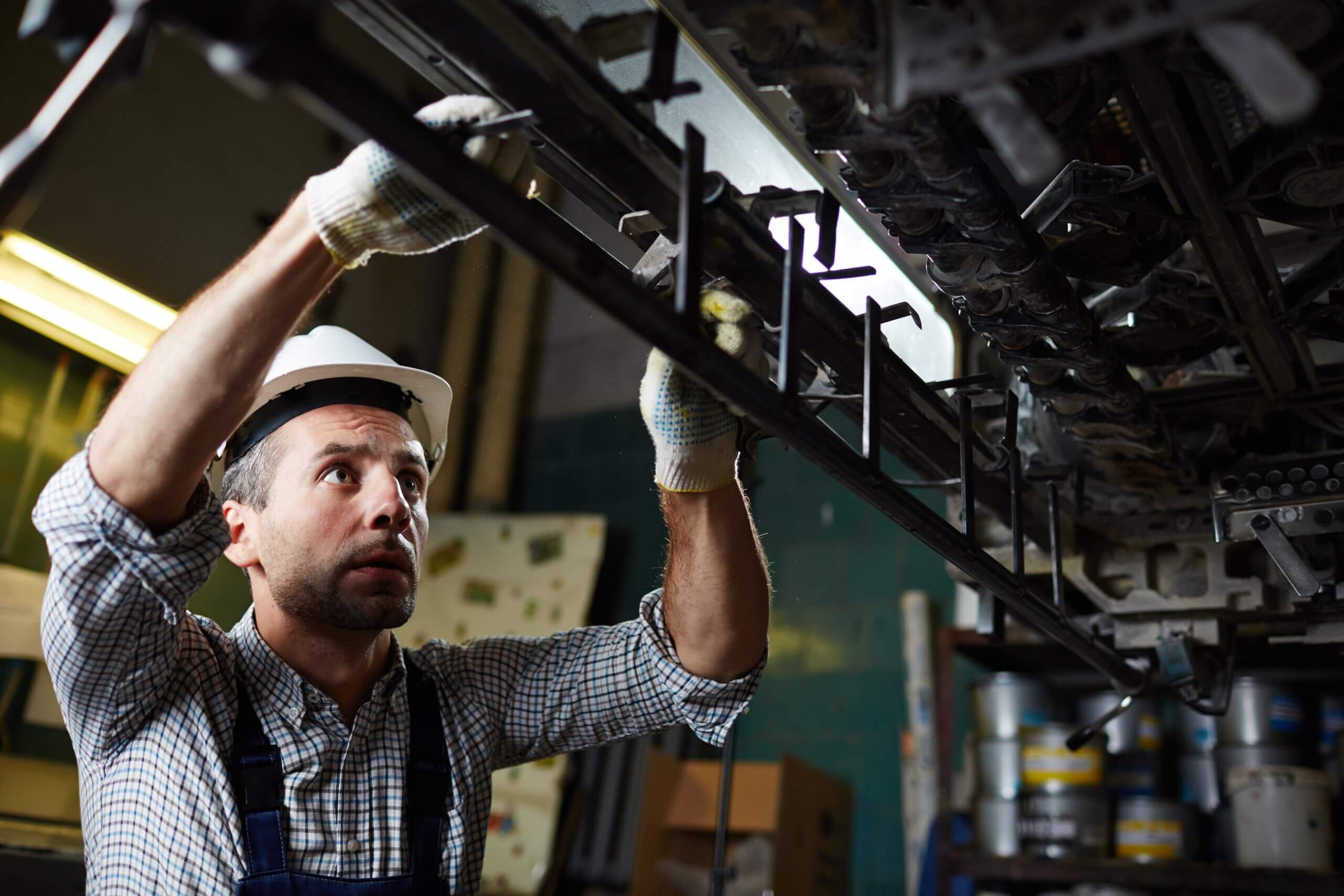
If you came to this page with the question, “How does preventive maintenance save you money?” you’re in the right place. Here, we’ll delve into how strategic PM programs can reduce unnecessary O&M spending. We’ll also discuss the strategy’s additional benefits, before reviewing how to calculate a PM savings estimate for your organization. Is your organization spending too much on reactive maintenance?
According to maintenance expert Sandy Dun, if you’re allocating anywhere near 40 percent of your monthly O&M budget on unplanned maintenance you should re-strategize.
Performing preventive maintenance (PM) on critical assets can save your company big bucks. PM programs are especially crucial for industrial organizations—manufacturers, warehouses, and power plants— that rely on complex machinery to serve customers every day.
An emergency breakdown, for example, can set facility production targets back for hours, if not days. Some studies even estimate the financial impact of manufacturing downtime to be as much as $5,600 per minute! With that said, even small- and medium-sized businesses can reap substantial savings by optimizing their maintenance scheduling plans.
What Is Preventive Maintenance?
Have you ever heard the medical slogan “Prevention is better than the cure?”
Many facilities managers run preventive maintenance systems under the same philosophy. Practicing PM isn’t about eliminating all equipment problems as much as preventing larger ones from taking place.
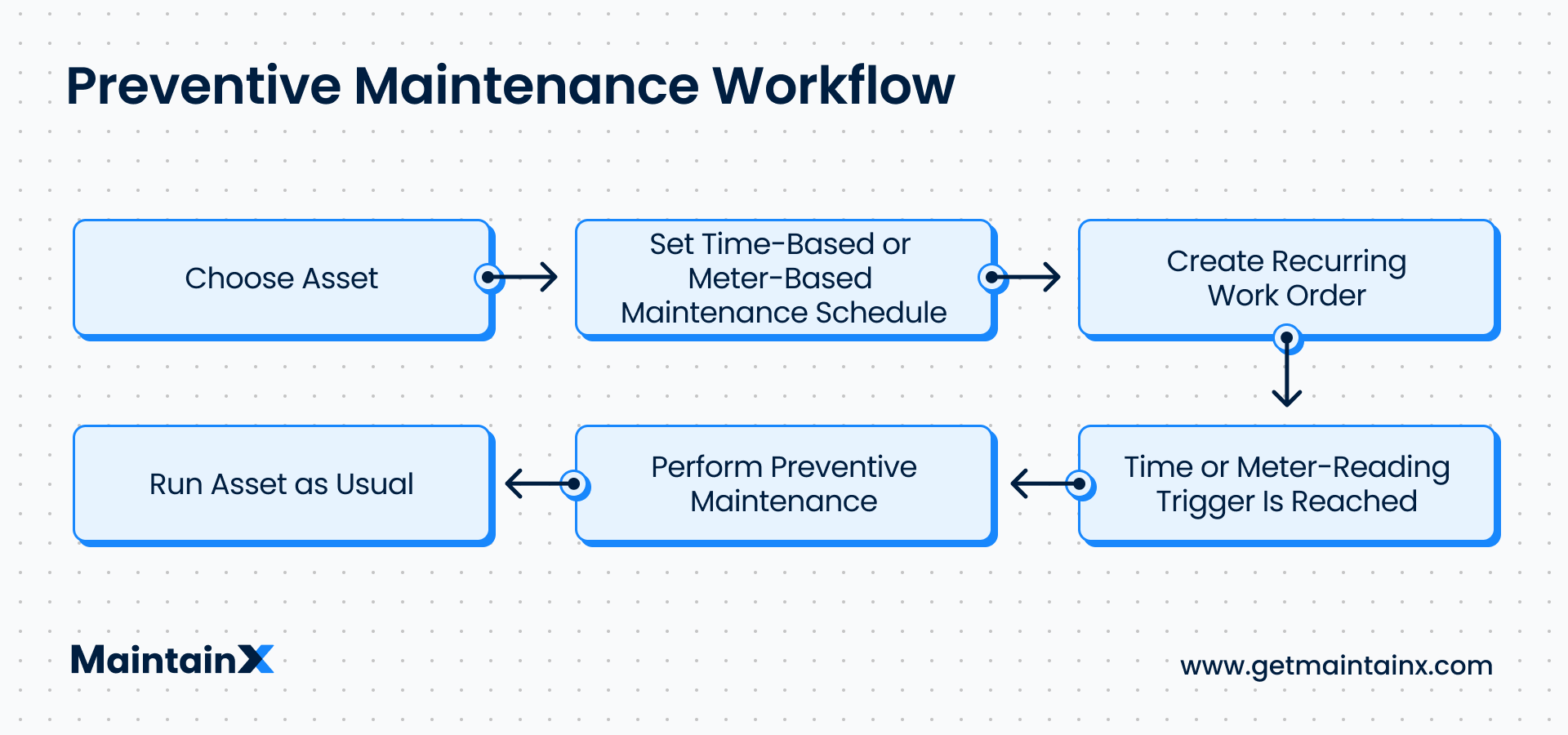
The Clinical Engineering Handbook defines preventive maintenance as maintenance carried out according to predetermined technical criteria, indicated in the instructions for use or manufacturers technical documentation, with the intention of reducing the likelihood of equipment failure or degradation of a service rendered.
Essentially, the practice includes performing all categories of upkeep that can potentially prevent losses due to equipment damage or failure.
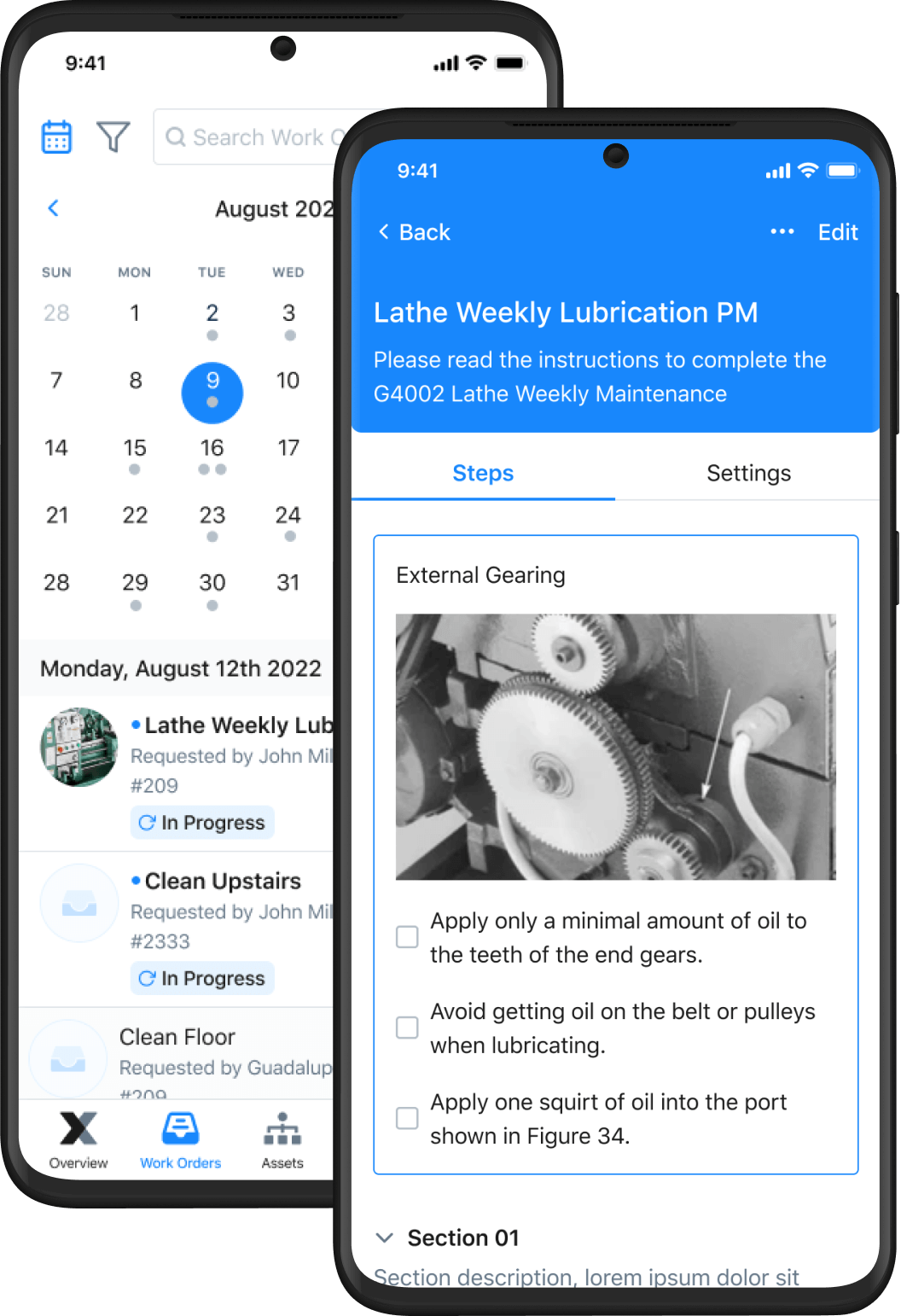
Computerized Maintenance Management Software (CMMS) is an excellent tool to help organizations manage tasks efficiently. Features allow easy handling of maintenance operations, support cost-effective decisions, and improve communication among team members.
Managers also can use CMMS software to identify and address extraneous spending patterns. While material, labor, and overhead expenses are direct costs, indirect costs like lost parcels, late deliveries, and high energy costs can be identified and addressed via advanced reporting.
No matter the task, the primary goals of preventive maintenance are always to reduce equipment downtime, increase reliability, enhance safety, and optimize O&M budgets.
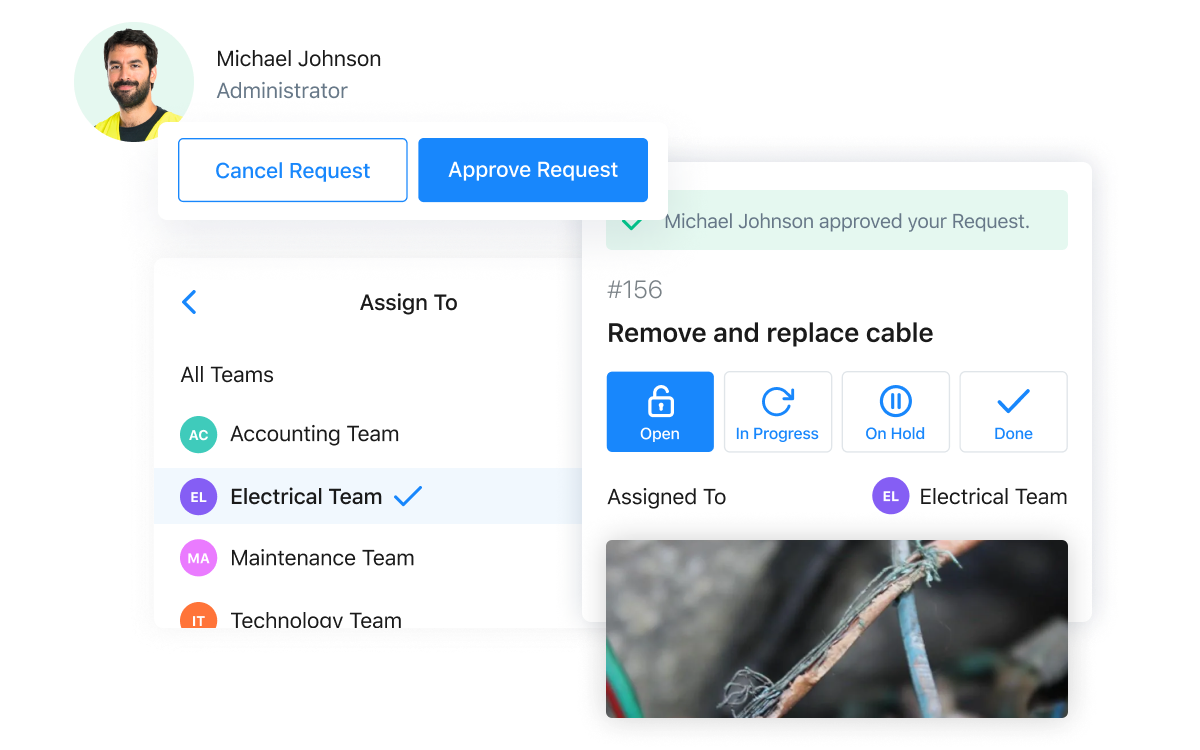
How Does Preventive Maintenance Save You Money?
Well-thought-out PM programs reduce unnecessary spending associated with unplanned breakdowns in four primary ways:
1. Reduces Unplanned Downtime Risks
We’ve all heard the saying “Time is money.” However, the phrase rings especially true when it comes to the cost of equipment downtime.
Downtime refers to the total amount of time machinery is out of order. It’s either the result of an unplanned breakdown (e.g,. a forklift battery dies) or a planned shutdown (e.g., a technician lubricates conveyor belt parts per a facility’s monthly maintenance schedule).
The primary advantage of planned downtime is in the word planned. Maintenance managers can either schedule downtime to take place outside of production hours or distribute maintenance tasks to minimize disruptions as much as possible.
Alternatively, unplanned downtime often results in emergency maintenance. To remedy equipment malfunctions as quickly as possible, downtime forces busy organizations to spend extra money outsourcing machine specialists, paying technicians to work overtime, and/or paying rush-shipping fees to order missing parts.
Combine these expenses with potential profits lost because of production delays and you can see why preventive maintenance makes sense.
2. Increases Operational Efficiency
Operational efficiency is the measure of resources put into a business vs. the number of benefits gained. O&M costs that impact operational efficiency include the purchase and maintenance of company equipment.
Preventive maintenance makes it possible for companies to cut down on extra costs by preventing reactive maintenance. Also known as “run-to-failure,” this type of maintenance refers to tasks performed after a piece of machinery has already broken down.
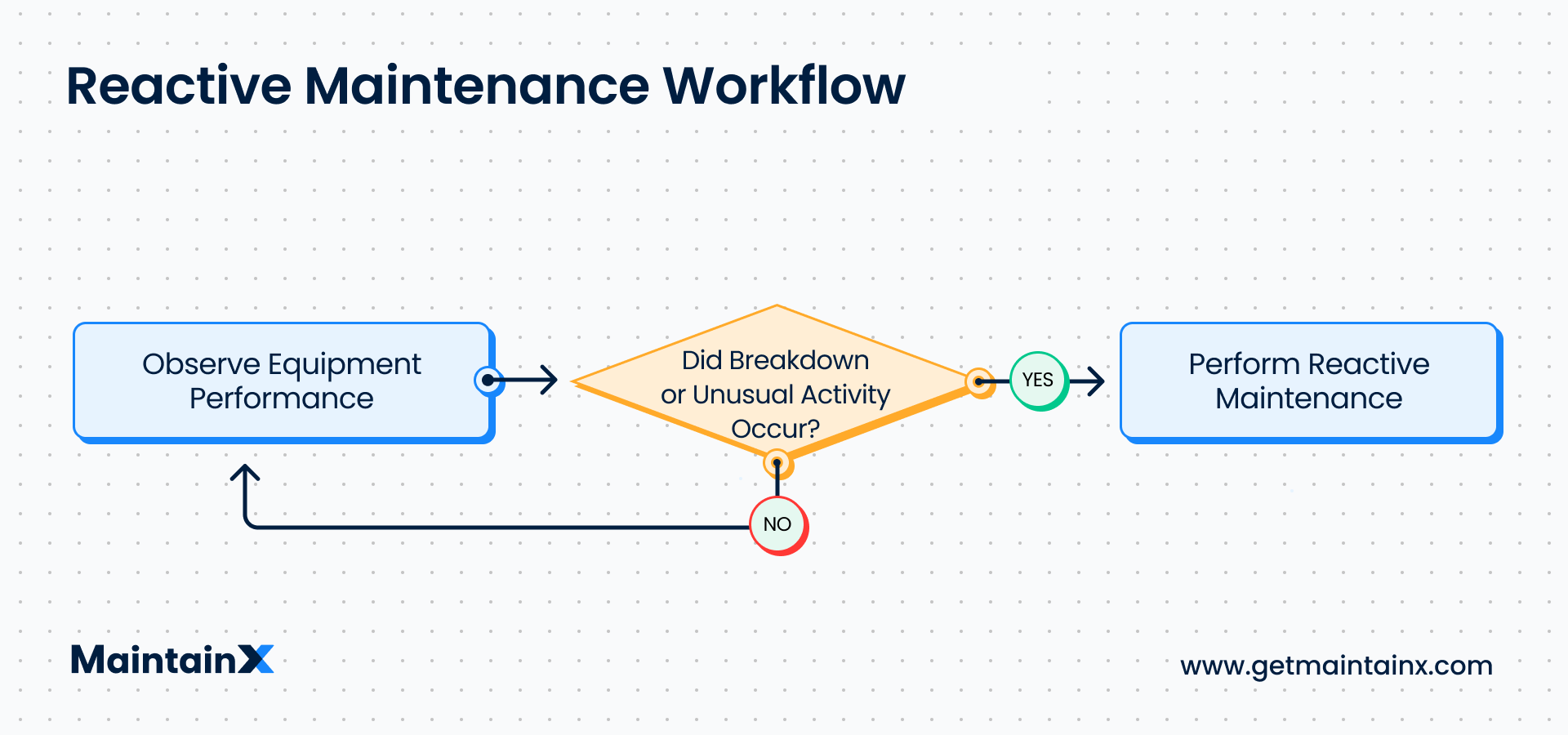
Unfortunately, unexpected breakdowns typically involve the malfunctioning of several equipment parts. The expense of critical parts combined with the cost of overtime, as well as outsourced servicing, often translates to severe financial losses.
Performing recommended upkeep on equipment according to time and/or usage triggers allows technicians to remedy small issues before they cause major shutdowns. This foresight mitigates costs associated with both emergency maintenance expenses and lost productivity due to downtime. PM schedules help organizations maintain high levels of operational efficiency with fewer running costs.
3. Increases Equipment Useful Life
Imagine having consistently reliable equipment that runs smoothly for many years without the need for replacement. You can make the most out of your investment by practicing PM.
As you reduce a machine’s unplanned breakdowns, you increase its Useful Life. A tangible asset’s Useful Life is defined as the period of time a company can expect a machine to remain functional and earn revenue.
Many factors can impact the ideal time span of ownership, including an asset’s age, its environment, and how often it runs. Physical and economic impact factors that affect equipment useful life are:
- Physical Factors: Asset expiration date, wear-and-tear, decay, and unexpected events like fire, flood, and theft.
- Economic Factors: Changes in asset demand, asset replacement with a more efficient version, and unforeseen physical/technical degradation.
The bottom line: maintaining equipment according to recommended guidelines can extend its longevity by years, thus saving thousands of dollars in early-replacement costs.
4. Improves Customer Service
Still wondering: how does preventive maintenance save you money? Customer opinion is paramount to success in today’s marketplace. Thus, today’s most profitable and productive businesses have one thing in common: unparalleled customer service.
In the era of Amazon Prime shipping, customers expect high-quality services delivered on time. Consistency, trustworthiness, and quality are three elements that turn companies into reputable brands people trust. Achieving this outcome requires equipment reliability.
When executed correctly, preventive maintenance programs lead to more loyal customers and referrals. Why? Because reliable equipment translates to reliable customer experiences.
Whether you’re a hotel seeking to provide guests with comfortably air-conditioned rooms or a manufacturing facility wanting to fulfill shipments according to promised timelines, PM helps ensure consistent equipment functioning. With the increasing trend of social media engagement, one disappointed customer can cause serious damage to an organization.
History is rife with examples of competing fledgling businesses experiencing both wild success and colossal failure because of good and bad customer service. In summary, PM is an important cog in the wheel of long-term customer satisfaction.
How to Measure Preventive Maintenance Effectiveness
How do you know if your PM program is saving you money post-launch? Measure your efforts with key performance indicators (KPIs). The following KPIs are industry standards for measuring baseline performance of PM efforts:
Planned Maintenance Percentage (PMP)
PMP is a maintenance metric that measures the number of planned maintenance tasks in comparison to all maintenance tasks. Managers can refer to this metric regularly to keep tabs on PM program progress and identify opportunities to reduce reactive maintenance. To calculate planned maintenance percentage, divide your total hours spent on planned maintenance activities by your total number of hours spent on all maintenance activities within a given period. Then, multiply the number by 100 to get your PMP percentage. use the following equation:

Preventive Maintenance Compliance Rate
The PM compliance rate comprises the number of completed planned tasks vs. the total number of planned tasks. To calculate, divide your total number of completed PMs by your total number of PMs within a given period. Then, multiply the result by 100 to calculate your schedule compliance percentage.
PM Compliance = (# of completed tasks ÷ number of scheduled tasks) × 100
Keeping track of the exact number of executed PM tasks using paper work orders can be daunting. Consider employing a Computerized Maintenance Management System (CMMS) to digitally track completed PMS for easy access.
Scheduled Maintenance Critical Percentage
Scheduled maintenance critical percentage (SMCP) quantifies the tasks your team isn’t performing on time. Delayed PM implementation can result in equipment damage and increased expenses. Calculate SMCP by:
SMCP is calculated by adding the number of days scheduled maintenance is late to the number of days in a maintenance cycle. Divide your result by the number of days in the maintenance cycle and multiply that number by 100 to arrive at a percentage.

Cut Costs with Preventive Maintenance
If you visited this article with the question, “How does preventive maintenance save you money?” we hope to have answered it.
Businesses can’t thrive until O&M costs are minimized with optimized maintenance scheduling. Preventive maintenance is an effective strategy used globally to reduce downtime, increase productivity, and minimize emergency maintenance repair costs.
The best way to organize a CMMS program is with the support of user-friendly computerized maintenance management system (CMMS) software. MaintainX is a top-rated CMMS platform and the world’s only mobile CMMS with chat. The app is completely free to download, and all Premium Features are free for 30 days.
FAQs
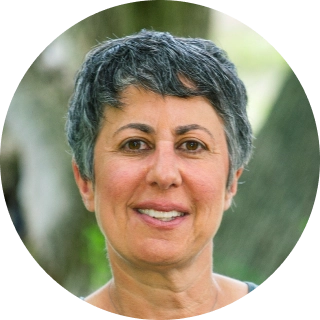
Caroline Eisner is a writer and editor with experience across the profit and nonprofit sectors, government, education, and financial organizations. She has held leadership positions in K16 institutions and has led large-scale digital projects, interactive websites, and a business writing consultancy.