Failure Mode and Effects Analysis (FMEA) is the process of assessing the potential causes and impacts of equipment failures. It’s a proactive, data-driven, and team-oriented method for identifying the relative effect of various failure modes on productivity goals.
FMEA is also referred to as failure modes, effects and criticality analysis (FMECA), and potential failure modes and effects analysis.
FMEA Basics
The American Society for Quality defines Failure Mode and Effects Analysis (FMEA) as a process analysis tool for identifying all possible failures in product, design, or production processes. It’s a step-by-step approach to studying the many ways an asset might fail (failure modes) and the consequences of those failures (effects analysis).
Maintenance professionals use the tool to prioritize maintenance depending on how serious the consequences of a failure are, the frequency of occurrence, and how easily failures can be detected. It’s also used to document knowledge and actions about the failures to enable continuous improvement.
Through FMEA, they can uncover four key elements:
- Failure Modes: The unique ways an individual asset and its components can fail.
- Effects of Failure: The potential operational outcomes of each failure mode.
- Cause of Failure: The possible root causes of identified failure modes.
- Analysis of Failure Modes: The measurement of failure mode severity and frequency.
Failure modes describe specific ways that assets and their components can fail. For instance, the failure modes for a centrifugal pump can be mechanical failure, hydraulic failure, corrosion, or human error.
Effects of failure describe the consequences of an identified failure mode. Consequences can include a negative impact on the overall productivity, profitability, asset reliability, and safety.
Causes of failure don’t always solely affect the asset in question and can affect larger operational systems and entire departments. It’s important, therefore, to assess the risk of each failure systematically as part of a thorough a_nalysis of failure modes._
The US military first developed Failure Mode and Effects Analysis (FMEA). NASA then adopted it, and its use has since spread to other industries such as healthcare, automotive, mining, and oil, among others.
The Benefits of FMEA
The FMEA method of analysis enables maintenance teams to clearly link potential asset failures with corresponding consequences. Essentially, it’s a bottom-up approach to maintenance in which specific data points pave the way toward a more general plan of action.
This means performing a thorough failure mode examination of each asset component, identifying its potential causes, and cataloging the associated effects on O&M goals. When executed correctly, businesses can map out the most efficient ways to maintain critical assets.
FMEA is one of the most effective methods for proactively identifying problems and devising cost-effective ways to solve them. It provides a structured approach for evaluating, tracking, and making continuous O&M improvements.
FMEA is associated with several benefits, including:
- Providing a structured and documented way to select designs with a high probability of improving production and safety.
- Enabling maintenance professionals to prioritize maintenance based on the likelihood of particular equipment failures and their impact on production, safety, and budget.
- Improving the quality, reliability, and safety of standard operating procedures (SOPs).
- Utilizing the collective knowledge of team members in writing SOPs.
- Minimizing the cost of failures by proactively mitigating problems.
The 10 Steps of Failure Mode Effects Analysis (FMEA)
As previously mentioned, FMEA is a step-by-step approach to identifying all of the potential ways an asset may fail and the consequences of each failure. Here is an overview of the 10 steps of conducting a Failure Mode Effects Analysis (FMEA) outlined by FMEA Training.
1. Get Organized
Outline the process at hand, including its basic features, desired functions, construction, materials, and assembly. This exercise will require gathering a team of process owners, system designers, and internal stakeholders experienced in remedying failures. You may even want to involve customers or suppliers to gain additional insights.
Get clear on exactly what should be included and what should be left out. You may find it helpful to create a process flowchart or table when identifying individual process components.
2. Brainstorm Potential Failure Modes
Review available data to identify every conceivable way an asset and its parts could fail. Make your list as comprehensive as possible—the more potential scenarios envisioned, the better.
3. List Their Potential Effects
List what could happen if each of the aforementioned failure modes occurs. Stretch your thinking to include every possible impact on organizational bottom lines, routine processes, production, and stakeholder safety. Expect to uncover multiple outcomes per failure.
4. Designate Severity Rankings
It’s not unusual for failure modes to cause chain reactions that influence multiple operational components. However, events seldom carry the same weight in terms of consequences.
For example, a burnt-out light bulb in the mailroom isn’t as disruptive as a company-wide Internet outage. The greater the impact on safety and/or finances, the higher the severity ranking it should receive.
5. Designate Occurrence Rankings
Next, rank your failure modes by frequency of occurrence. How often do you have reason to suspect each event will occur? Identifying common causes of failure can help determine the relative occurrence of failure modes.
Always keep in mind that one failure mode may have many potential causes.
6. Designate Detection Rankings
What are the chances you will be able to detect failure before it occurs? A high detection ranking means the failure mode or effect is not detectable and occurs without warning.
7. Calculate the Risk Priority Number (RPN) for Each Failure Mode
Each element—severity, occurrence, detection—should be assigned a value on a 1 (best) to 10 (worst) scale. The cumulative effect of each failure element is what’s called a Risk Priority Number (RPN). Multiply your three elements to arrive at the RPN:
Risk Priority Number (RPN) = Severity x Occurrence x Detection
8. Strategize a Preventive Maintenance Program
Moving forward, develop a proactive maintenance schedule to reduce the risk of equipment failure. Prioritize your failure modes from highest RPN to lowest RPN. It’s worth emphasizing that it’s nearly impossible to address every potential failure. Instead, focus on addressing the potential failures that would most jeopardize production goals, stakeholder safety, and customer satisfaction.
9. Take Action
Focus your energy on eliminating or minimizing high-risk failure modes first. Gather information, conduct experiments, consider process or design improvement, make changes to functions, and assign maintenance activities to your team.
10. Recalculate RPNs
Think of your FMEA as a “living resource” and consistently update it with documentation of actions taken. Periodically recalculate your RPNs to evaluate program progress and make changes as needed.
Examples of FMEA Questions
Below are examples of useful FMEA questions:
- Function or Process Step: What is the function, step, or item being analyzed?
- Failure Type: What exactly has gone wrong?
- Potential Impact: What is the impact of the failure type described above?
- Severity Ranking: How severe is the effect on the customer?
- Potential Causes: What can cause the function or process steps to go wrong?
- Occurrence Ranking: How frequently is this likely to occur?
- Detection Mode: What controls are in place to detect or prevent failure?
- Detection Ranking: How easy is the failure or its effects to detect?
- Risk Priority Number: What is the risk priority number for the failure mode?
These questions are by no means exhaustive but are meant to serve as a launchpad.
Streamline FMEA with MaintainX
FMEA is a valuable work order prioritization tool with benefits that include improved asset reliability, optimized maintenance costs, and increased customer satisfaction.
MaintainX enables manufacturing teams to share crucial data points, enhance team communication, and glean insights from user-friendly advanced reporting. Our work order software consistently receives high marks for usability, comprehensiveness, and value on third-party review sites.
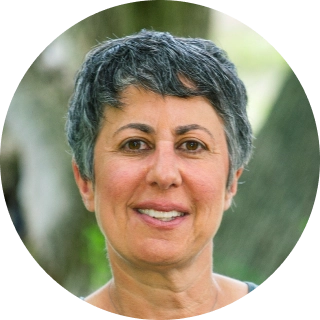
Caroline Eisner
Caroline Eisner is a writer and editor with experience across the profit and nonprofit sectors, government, education, and financial organizations. She has held leadership positions in K16 institutions and has led large-scale digital projects, interactive websites, and a business writing consultancy.
See MaintainX in action