Whether downtime is planned or unplanned, it always affects your bottom line and ability to meet production targets and delivery times. In fact, according to the State of Industrial Maintenance 2024 report, the average cost of an hour of unplanned downtime hovers around $25,000 and can skyrocket to over $500,000 for larger organizations.
That’s one reason why understanding maintainability is so important. Using equipment and assets that can be repaired quickly and put back into service as soon as possible is a key indicator of efficiency in the manufacturing sector.
In this article, we explore what maintainability is, how it differs from reliability, and how you can improve your KPIs by measuring and tracking maintainability over time.
What is maintainability?
Maintainability measures how quickly your manufacturing or maintenance team can detect and pinpoint an issue, repair it, and restore the asset’s functionality after this downtime.
This measure is expressed as a KPI metric known as “Mean Time to Repair” (MTTR). MTTR is the average time required to repair a problem on an asset. It measures the time required to restore an asset to its normal functioning state after a problem is identified and is sometimes confused with reliability.
Reliability vs. maintainability
Although they sound similar, reliability and maintainability refer to separate measures that dovetail with availability.
Reliability refers to how likely an asset is to perform as expected, without failure, under normal operating conditions. This absence of unplanned downtime makes for a very reliable asset. Conversely, an unreliable asset experiences frequent unexpected failures.
Maintainability is the speed and ease with which the asset can be put back into service when it experiences a failure.
These two factors together can affect availability. Availability is simply whether your asset or system is functioning and, therefore, available to do the work. Availability can be negatively impacted by:
- Blown-out maintainability times
- Unreliable equipment
- And, of course, planned downtime when an asset is scheduled to be unavailable.
If you’re looking to improve efficiency across your facility, consider the interplay of these three factors and experiment with different approaches to using all three as efficiency indicators.
What impacts maintainability?
Since maintainability measures how quickly technicians detect, locate, and restore asset functionality after downtime, ensuring technicians have the tools and resources to make the repair quickly is vital. Here are some examples of what could impact their preparedness.
Poor record keeping or missing resources
In the manufacturing sector, where every facility has tons of plant, machinery, and automation equipment, the drawings, operation manuals, and parts for those assets need to be readily available and well organized.
A technician’s ability to restore functionality and get an asset back into service can be heavily impacted by out-of-date or missing manuals, incorrect drawings, or a disorganized filing system. And, as we know, time is money.
If your organization is lacking in this area, creating a standardized operating procedure (SOP) or even just a central repository for maintenance documentation can help technicians and mechanics do their work more efficiently.
Lack of training
Training and continuous improvement programs can also help reduce maintainability times. For example, a confident and knowledgeable maintenance technician will likely identify an issue faster and conduct a repair more swiftly than team members who have not been trained on the equipment.
To counter this, make sure your organization has a regular training program to identify potential skill gaps and support your team in becoming more adept in its role.
Aging assets
Maintainability requirements vary based on asset criticality, repair costs, accessibility, and the complexity of the equipment. The age of your equipment also affects its maintainability: older equipment may still be considered reliable most of the time, but this doesn't necessarily mean it is easily maintainable.
Older assets can present more challenges because they are less likely to have IoT connectivity or onboard early warning sensors that indicate impending issues. A lack of electronic diagnostic sensors can increase the MTTR by blowing out fault-finding times for technicians, and make it harder to see critical historical data that can help with swift maintenance action. Plus, depending on an asset’s age, it can be hard to source new parts when something breaks—especially in a timely manner.
Equipment complexity
Assets that are very complex to repair and maintain, or that are made up of one large system rather than smaller individual assemblies or modules, are typically harder to maintain.
Modular systems—or those designed for interchangeability—are generally simpler to work on since they are designed for easier disassembly and reassembly. Some modular assemblies can be repaired while other parts of the asset continue functioning under normal specified conditions. Taking only part of an asset offline like this reduces the impact on production.
How to measure maintainability
A simple way to improve efficiency is to start measuring maintainability over time. As we saw earlier, maintainability can be expressed as the time it takes between knowing an issue exists with an asset and putting that asset back into service.
Therefore, it makes sense to have your production, manufacturing, and maintenance teams immediately record the time and date when a problem is first detected and then when it is back online.
This measurement is known as Mean Time to Repair (MTTR), and it can be used as a baseline to improve asset efficiency and assess equipment value.
Measuring maintainability with MTTR
To accurately calculate MTTR, you need reliable data from maintenance work orders, which is where a maintenance app for tracking downtime can help. Reports pulled from your computerized maintenance management software (CMMS) can give you the total maintenance time for an asset and the number of repairs made over the same period. Armed with this data you can then calculate MTTR for each asset.
MTTR = Total Maintenance Time ÷ Number of Repairs
For example, if an organization spends 20 hours total on unplanned maintenance for an asset that broke down 4 times in one year, the asset’s MTTR is 5 hours.
How to improve maintainability
If you find a machine with a higher MTTR than expected, this can help you identify a more significant fault in the overall system—like a compatibility issue or a design flaw. Addressing the overarching system fault, rather than just a small link in the chain, will lead to better performance for the entire system, increased efficiency, and improved maintainability.
However, issues like this can fall through the cracks without the tools, software, or processes to track these failures. A CMMS system integrated with your ERP software can give you better visibility into problems that can hinder maintainability.
Identify failures in real time
Connecting IoT-enabled assets to a CMMS system can help you automatically identify failures and immediately raise work orders for repairs or other maintenance activities. Instead of waiting for machine operators to report a problem, or for your production line to halt, digital sensors can alert maintenance managers that repairs are urgently required, minimizing downtime and helping you get the asset back online quickly.
Identify root causes of common failures
Repetitive failures increase the time and money spent on an asset and hamper organizational efficiency. If an asset fails, causing unexpected breakdowns, getting to the crux of the issue can help you gain cost efficiencies in the long run.
Tracking the frequency of failures—or time between failures—for an individual asset can also lead to better root cause analysis and overall system optimization. By using MaintainX’s reporting tools and analytics dashboards, you can take a deep dive into each asset’s history to pinpoint underlying problems and address systemic issues.
Enhance predictive maintenance strategies
MaintainX integrates with IoT sensors to collect real-time data on asset conditions, such as temperature, vibration levels, operating pressure, and a range of other data points. This data, combined with OEM recommendations, can be used to predict when maintenance should be performed, reducing unplanned downtime.
Streamline maintenance processes
Use MaintainX to create, assign, and track digital work orders in real-time. This ensures that all maintenance tasks are documented, standardized, and easily accessible. Maintenance managers can also incorporate SOPs and checklists into work orders within MaintainX, which ensures that maintenance tasks are performed consistently and according to best practices, every time.
Improve inventory management
An accurate record of all parts and supplies provides clear visibility into current stock levels and usage rates. This helps in avoiding shortages and overstock situations. With MaintainX, maintenance managers can set up low inventory alerts within the software to automate the reordering processes. This ensures that critical parts are always available when needed, reducing maintenance delays and decreasing MTTR.
Increase uptime with MaintainX’s CMMS
Tracking and recording maintenance activities using MaintainX CMMS gives you key insights into the maintainability of your assets so you can create positive and lasting improvements in your organization.
By using MaintainX reports to analyze maintainability, you can: identify patterns and trends and see accurate data on uptime and downtime, MTTR, reactive vs. preventive maintenance, asset utilization, and more.
Create digital work orders on the spot in response to identified failures or issues. Manage inventory allocations to streamline maintenance activities. Reduce breakdowns by optimizing preventive maintenance for your equipment, increasing maintainability and reducing unscheduled downtime.
To learn more about MaintainX's capabilities, book a demo or try MaintainX for free.
Maintainability FAQs
A highly maintainable asset typically has a low Mean Time to Repair (MTTR). This means maintainability strongly correlates to how quickly and easily a machine is to service or repair, how readily available parts are, and how much skill is required to make the repair.
Maintainability costs can be calculated by analyzing the Mean Time to Repair (MTTR) for each piece of equipment. High MTTR generally means the asset is more expensive to maintain than an asset with low MTTR. However, the cost and availability of spare parts and the skill level of technicians required to adequately repair the equipment also need to be considered.
Reactive maintenance and repetitive corrective maintenance on a perpetually failing asset aren’t the best way to do business. Failure modes, high maintainability, and unexpected maintenance costs all reduce production efficiency, which results in a higher asset lifecycle cost.
Predictive maintenance involves planning ahead of time to service an asset. When taking this approach, the asset is shut down as close as possible to when the work is actually carried out, and technicians are prepared with the necessary replacement parts. Minimizing the time that the asset is out of service helps to reduce its MTTR and minimize downtime, positively impacting maintainability.
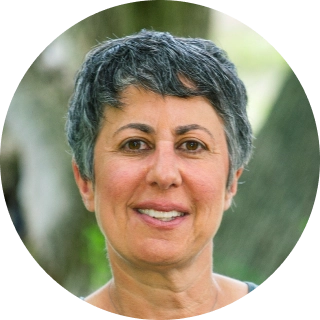
Caroline Eisner
Caroline Eisner is a writer and editor with experience across the profit and nonprofit sectors, government, education, and financial organizations. She has held leadership positions in K16 institutions and has led large-scale digital projects, interactive websites, and a business writing consultancy.
See MaintainX in action