In the world of facility management, not all maintenance is created equal. Some tasks are proactive and scheduled to prevent issues, while others are reactive, addressing unexpected breakdowns. While proactive (or preventive) maintenance is the gold standard, in practice, there will always be some balance between that and reactive maintenance. This balance can significantly impact a facility's efficiency and costs, and is often measured by a key metric known as the planned maintenance percentage.
Planned maintenance percentage (PMP) refers to the percentage of overall maintenance time that goes into planned maintenance activities. It’s usually measured against the total amount of time spent on maintenance in a given time period.
Calculating planned maintenance percentage is important for organizations who want to optimize their maintenance strategies and overall operational efficiency. It helps you understand how well your maintenance planning is going, and gives you insight into cost-effectiveness, resource allocation, and equipment longevity. By tracking this metric, you’ll be able to make data-driven decisions to improve maintenance practices, ultimately leading to better performance and significant cost savings.
In this article, you’ll learn all about PMP—why it’s useful, how to calculate it, and how to improve your team’s PMP.
What is planned maintenance percentage (PMP)?
Planned maintenance percentage (PMP) is a maintenance metric that illustrates the number of planned maintenance activities compared to all organizational maintenance activities. It measures the time spent on planned maintenance tasks expressed as a percentage of the total maintenance time within a given period.
Maintenance managers can calculate PMP at weekly, monthly, or yearly intervals. Regardless of what interval the calculations happen, it’s essential to find the right balance between preventive and reactive maintenance work orders—experts recommend an ideal 80:20 ratio.
Why PMP is useful
Regular PMP calculations are a simple way to keep tabs on overall maintenance program effectiveness. Are you following an effective preventive maintenance program, or are you playing catch-up by constantly putting out fires? A low PMP indicates you spend too much time on reactive maintenance. In such cases, you need to thoroughly review your maintenance workflows, equipment history, and root causes as needed. PMP is also useful because it:
- Enables data-driven decisions on maintenance processes, schedules, and resource allocation. As we’ve established, low figures suggest ineffective planned maintenance, indicating that you should rethink your maintenance strategy. Since the ideal preventive maintenance to reactive Maintenance ratio is 80:20, a PMP score of 80 puts you in a good place, and lower figures are a sign you need to pay closer attention.
- Helps maximize asset reliability while controlling maintenance costs. If you’re spending too much time on unplanned maintenance, this would imply your assets are breaking down more often than not. Having this clearly expressed as a number helps you take steps to prevent these breakdowns. You can eliminate inefficient maintenance workflows, implement new ones, and increase asset availability by identifying problems before they develop.
How to calculate planned maintenance percentage (PMP)
To calculate PMP, you need two key pieces of data. The first piece is the total amount of time your team or facility spends on planned maintenance activities within a given period. Planned maintenance refers to maintenance work that you plan, document, and schedule beforehand, and not simply in response to equipment breakdowns.
The second piece of data you need is the total amount of time you spend on all maintenance activities within the specific period. These hours should include the time your team spends on both planned and unplanned maintenance.
Planned maintenance percentage formula
To calculate your PMP, divide your total hours spent on planned maintenance activities by the total number of hours spent on all maintenance activities within a given period. Then, multiply the number by 100 to get your PMP percentage.
PMP = (Planned maintenance hours / Total maintenance hours) x 100%
3 examples of planned maintenance percentage
Below are a few examples of PMP calculations:
1. Water utility example
A water utility company spent 1,200 hours total on all maintenance activities during the first quarter of 2024. Of those 1,200 hours, 980 hours went into planned maintenance tasks.
PMP = 980 ÷ 1,200 = 0.817
= 0.817 x 100
= 81.7%
2. Automotive industry example
An automotive factory spends 500 hours per month performing maintenance. Planned maintenance makes up 400 of those hours.
PMP = 400 ÷ 500 = 0.8
= 0.8 x 100
= 80%
3. Fleet management example
A fleet management company spent 200 hours on maintenance, with 175 hours spent on planned maintenance, in one month.
PMP = 175 ÷ 200 = 0.875
= 0.875 x 100
= 87.5%
Because all those PMP figures are at 80% or above, we know these facilities are in ideal maintenance territory.
It’s worth emphasizing that calculating PMP requires facilities to properly document all of their maintenance hours—both planned and unplanned. Using accurate or incomplete data compromises your calculations and can lead to you making the wrong changes to your processes. Whether using pen-and-paper, spreadsheets, or maintenance software, ensure you maintain robust data at all times.
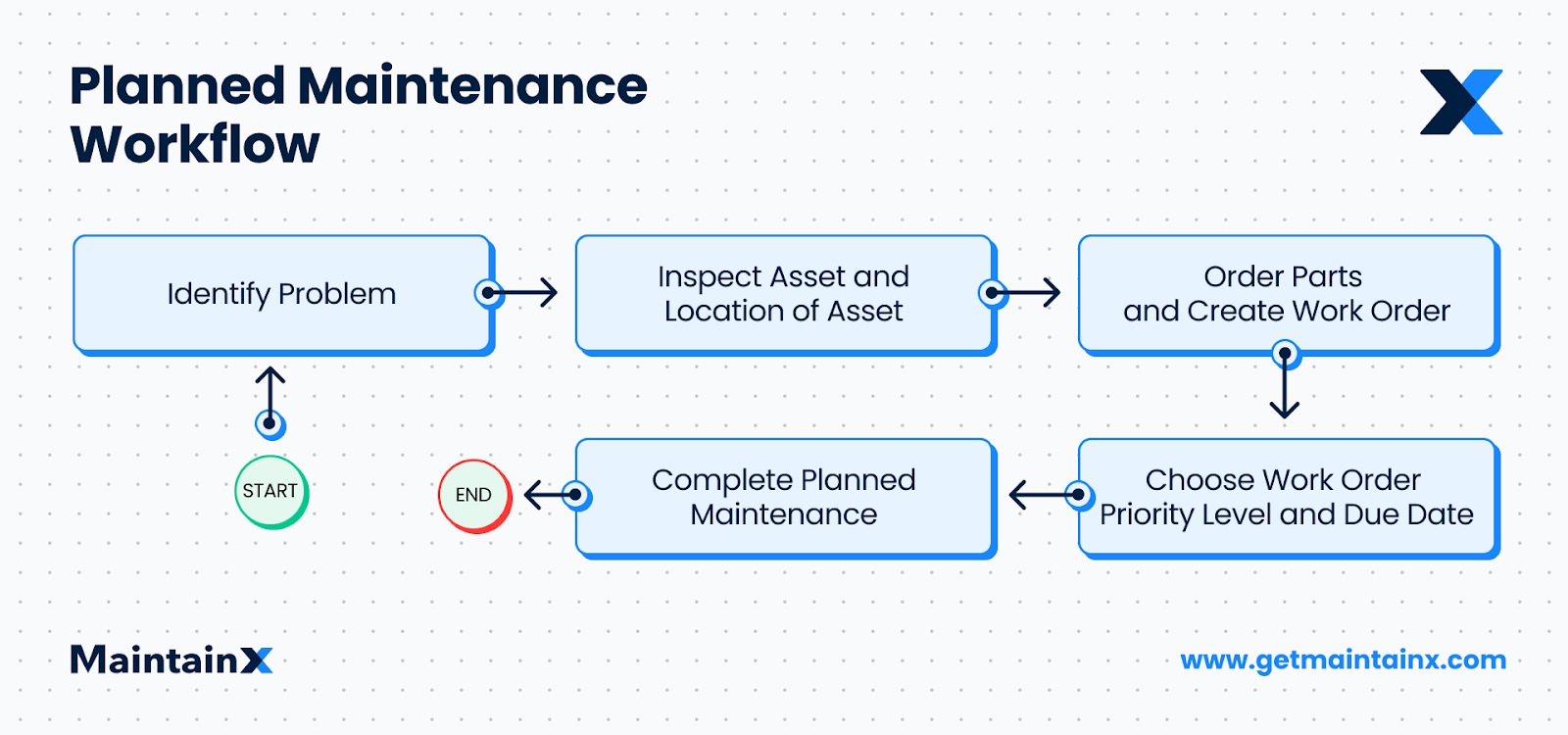
5 tips for improving planned maintenance percentage
As we’ve established, higher PMP values suggest that you are in control and are getting ahead of breakdowns and malfunctions. As such, lower PMP values don’t simply look bad on paper—they also indicate increased asset malfunction, which leaves you at risk of downtime and increased losses. Any organization that wants to improve its maintenance processes should work on improving its PMP. Here are a few tips to get started:
1. Make a plan for each asset
Knowing which kind of maintenance an asset requires to remain effective is crucial. Conduct a criticality analysis, determine asset failure modes, and calculate mean time between failure (MTBF) to better understand your assets’ behavioral patterns and develop effective maintenance programs for higher PMPs. One way to simplify this process is by using software that automates this analysis for you. MaintainX, for example, is a computerized maintenance management system (CMMS) that provides out-of-the-box reporting functionality to simplify your KPI tracking. You can access customized dashboards that display metrics like MTBF at a glance.
2. Improve emergency breakdown responsiveness
Unplanned downtime is inevitable, but you can make it easier to handle when it does happen. One crucial element is ensuring your team has everything they need to make quick repairs, from tools to spare parts. This is easier said than done, so ensure you use the right tools to optimize your parts inventory management. If you’re using software, look for features like barcode scanning to locate parts, automated low-quantity alerts, and automatic reordering to ensure you never stock out again.
3. Establish and improve total productive maintenance (TPM)
Total productive maintenance (TPM) is a methodology that suggests everyone within the organization is involved in asset maintenance. It means equipping workers with clear standard operating procedures (SOPs), providing maintenance training, and giving people the authority to quickly perform repairs confidently. TPM also ensures maintenance teams are notified of issues early enough to plan for them. Take advantage of tools like MaintainX’s digital and collaborative SOPs and checklists to ensure technicians complete maintenance tasks faster and without confusion.
4. Create effective schedules
Optimizing maintenance schedules is another way to improve PMP. Improving your maintenance schedule begins with creating an accessible system to catalog asset data, service history, and repair costs. The more accurate historical data you have at your disposal, the more effectively you can schedule both time and usage-based PM tasks. The ultimate goal is to always anticipate the ideal number of staff, inventory, and task time you will need throughout each shift.
5. Improve schedule compliance
Schedule compliance is a maintenance metric used to measure the percentage of scheduled maintenance activities completed on time. You can improve schedule compliance by scheduling work appropriately, ensuring proper documentation of all necessary procedures, and planning tasks with employee skill levels in mind.
Use MaintainX to help improve PMP
Ready to improve PMP and optimize your maintenance program as a whole? MaintainX offers a range of features to help streamline your workflows, capture relevant data, and ensure you never run out of necessary parts. Use MaintainX for:
Robust reporting: Generate actionable insights to make data-driven decisions about your maintenance program. You’ll be able to identify and eliminate or improve inefficient programs while doubling down on the efforts that are working.
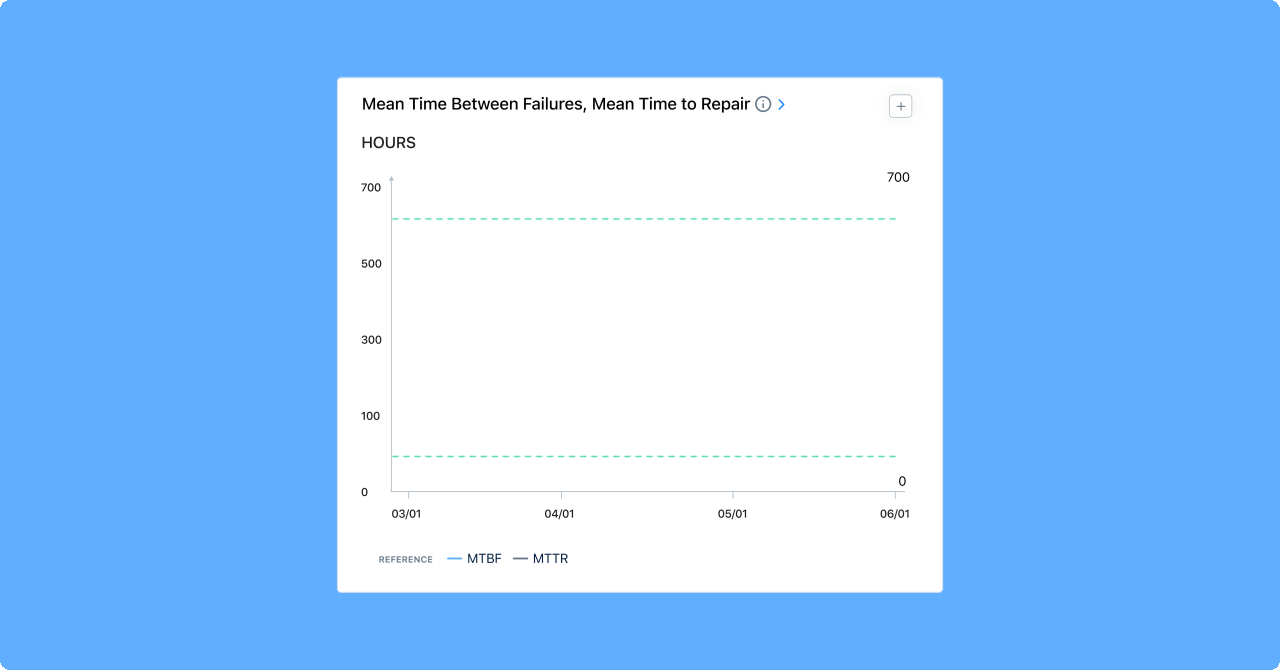
Parts inventory management: MaintainX’s Global Parts module allows you to centralize inventory data for easy management. Manage inventory, vendor data, and purchase orders, all in one easy-to-use system. You’ll be able to eliminate stockouts and ensure you have parts on hand to perform maintenance when needed. This way, you’ll avoid prolonging your downtime due to missing parts, and you can escape expensive rush orders.
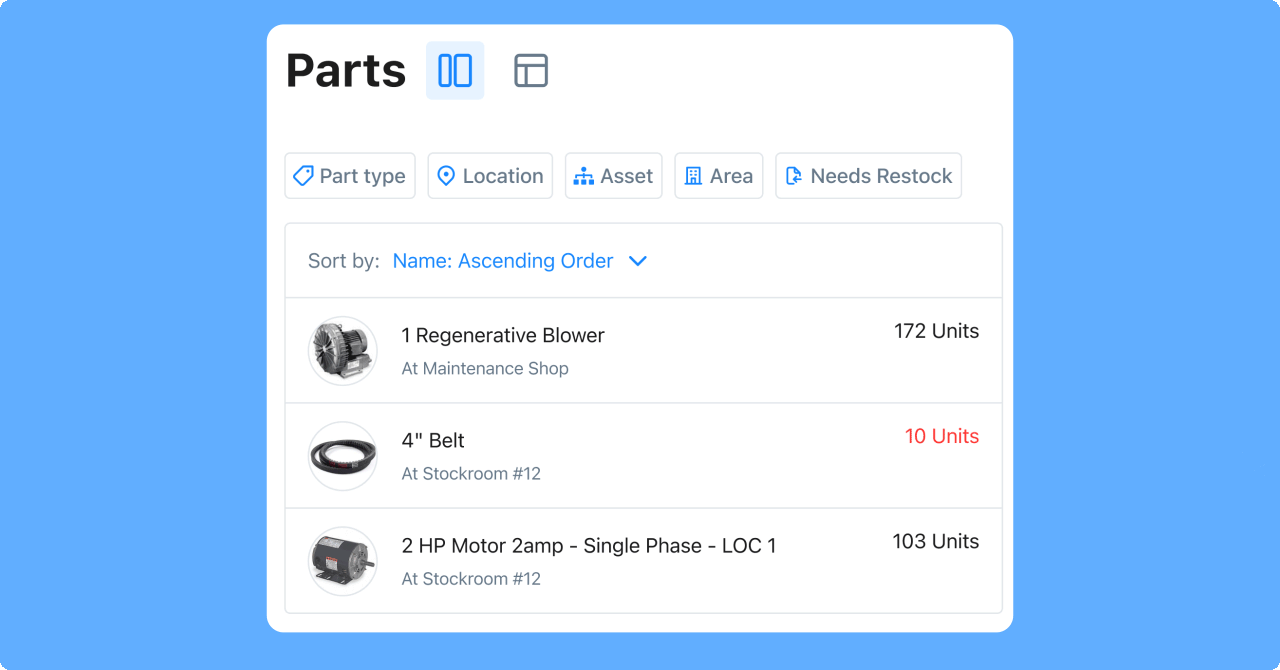
Streamlined SOP management: In addition to digital SOPs and a global procedure library, MaintainX’s AI-powered procedure generator allows you to easily create new SOPs by simply supplying a few key details. You’ll save critical time and generate an SOP draft you can customize and edit to your specifications.
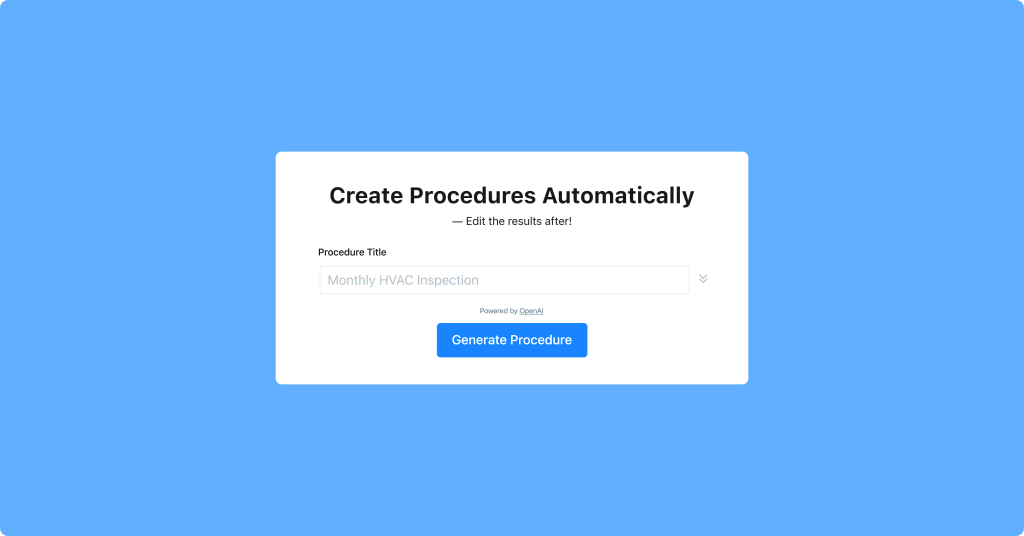
Workload-based scheduling: MaintainX’s Resource Planning module provides labor insights that enable workload-based scheduling. You’ll be able to see labor data for your staff on one screen, allowing you to make the best and most efficient maintenance schedules based on capacity.
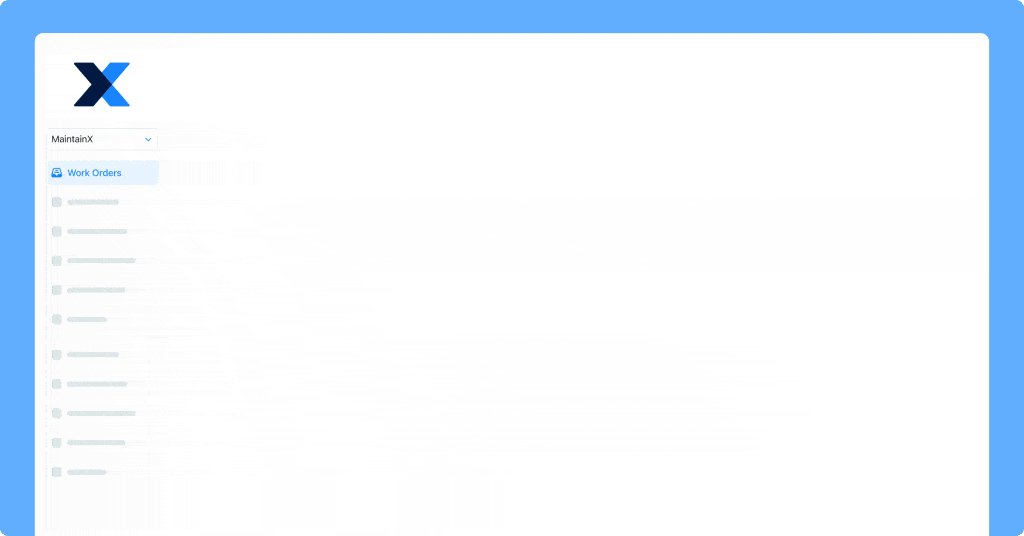
But don’t just take our word for it. Book a tour today and try MaintainX for yourself.
Planned maintenance percentage FAQs
Planned maintenance involves proactive and scheduled maintenance work that teams undertake to prevent equipment failure and keep assets in good working condition. Reactive maintenance refers to maintenance activities that teams perform after equipment fails or malfunctions. Planned maintenance aims to prevent equipment breakdowns, while reactive maintenance aims to restore equipment to working condition after a breakdown.
Aim to calculate planned maintenance percentage on a regular schedule, such as monthly or quarterly. Following this schedule helps you monitor your maintenance efficiency and implement changes if needed.
A best-in-class planned maintenance percentage will typically range between 85% to 95%. In reality, however, this is difficult to achieve, and even aiming for 80% puts teams in good standing.
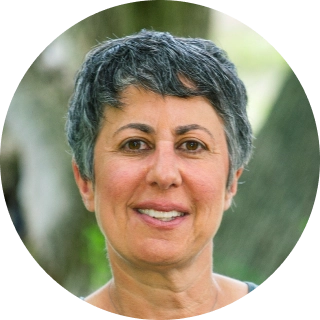
Caroline Eisner
Caroline Eisner is a writer and editor with experience across the profit and nonprofit sectors, government, education, and financial organizations. She has held leadership positions in K16 institutions and has led large-scale digital projects, interactive websites, and a business writing consultancy.
See MaintainX in action