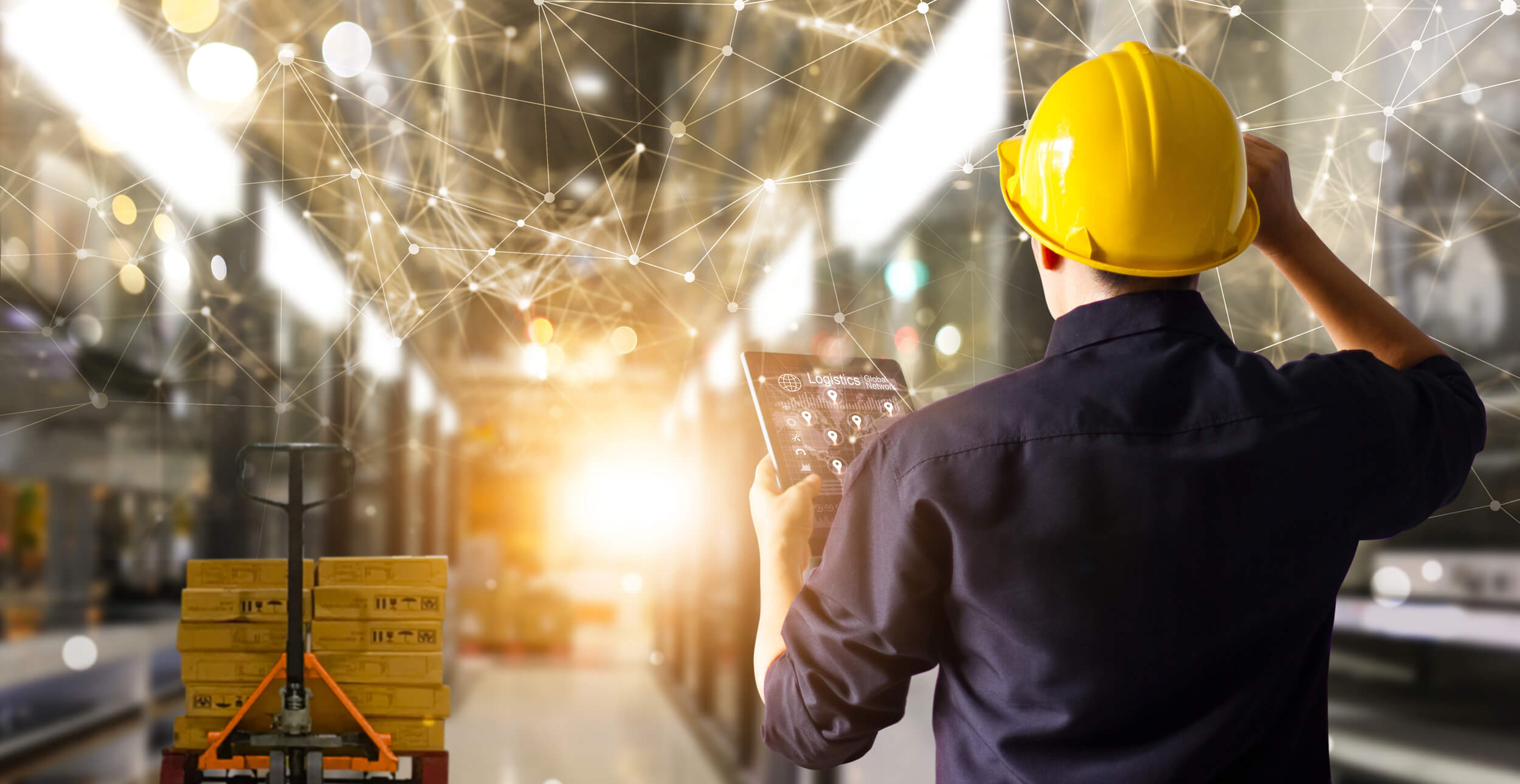
Supply chain management (SCM) involves managing the flow of goods, services, and processes required to produce a final product. As a supply chain manager, your goals include cutting costs, managing efficient production, and improving customer experience through error-free internal processes.
The problem? A rising eCommerce demand and the pandemic exacerbated supply chain challenges. Dealing with these new external challenges is tricky because we have little control over them, but managing some disruptions is possible with the right supply chain strategy and tools.
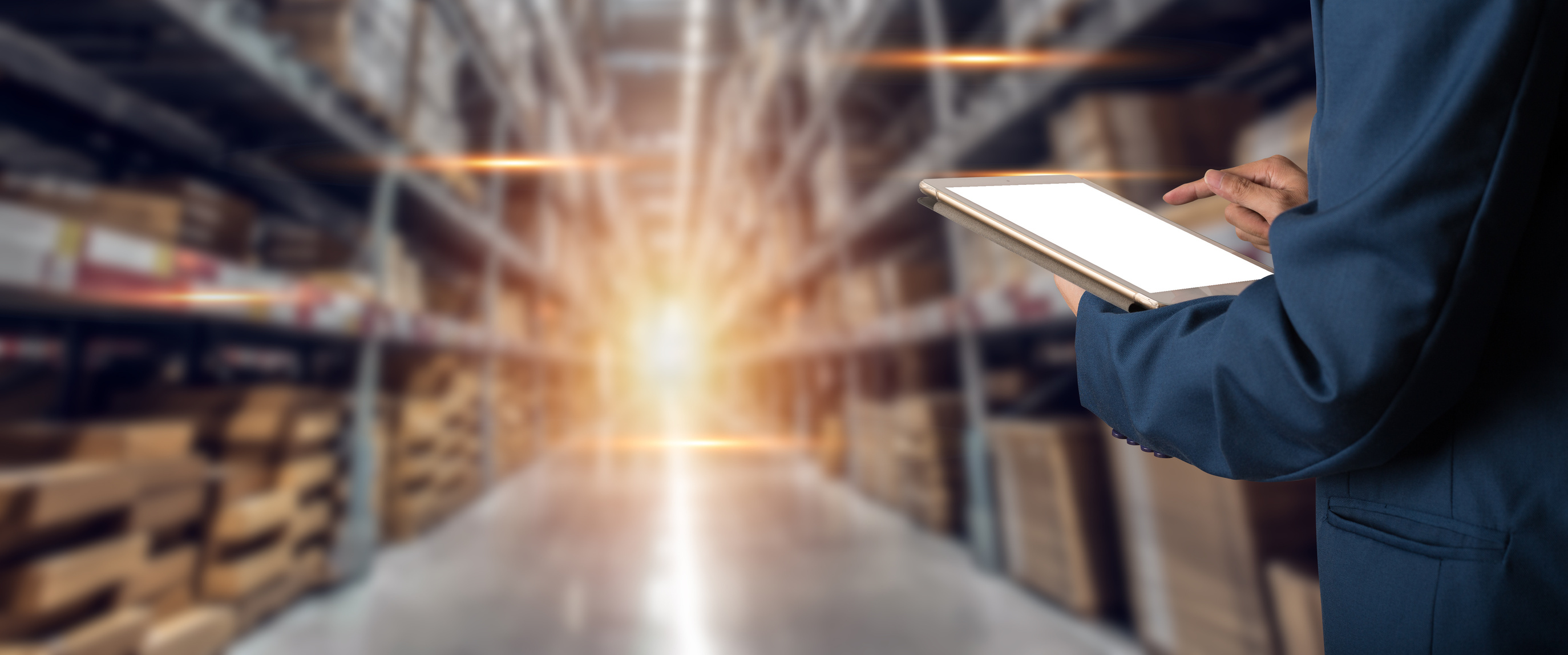
What Causes Supply Chain Disruptions in Manufacturing?
Supply chain disruptions can be caused by various external and internal factors, including pandemics, natural disasters, price instability, improper maintenance, or inefficient processes. However, these causes ultimately result in challenges like running out of inventory (when causes are external) or equipment downtime and information gaps (when causes are internal).
This guide explains why a CMMS (computerized maintenance management system) is an excellent tool in your supply chain toolkit to help overcome some challenges.
“The increasing frequency and magnitude of supply chain disruptions over the past decade have exposed weaknesses in most companies’ supply chain models.”
Bain & Company
Challenge 1: Spare Parts and Raw Materials Inventory Management
The COVID-19 pandemic put manufacturers and B2B eCommerce businesses in a tough spot. Supply chain managers found themselves juggling inventory-specific challenges like managing spare parts and raw material shortages, sourcing the right items at the right price and time, and finding reliable distributors.
The result? Inefficient internal processes, delayed production, and unhappy customers. Monitoring supply and demand and foreseeing major shifts in availability is critical. Unfortunately, only 22% of companies have a proactive supply chain network.
Maintaining a supply network on a spreadsheet requires manual work. Instead, you can use a CMMS to maintain your vendor network and build supply chain resilience. You can manage multiple vendors in real time to minimize the risk of supply chain disruption.
When the global supply chain is thrown off track, the inventory management capabilities of a CMMS will help ensure you have the right spare parts and raw materials needed to move through the production value chain without friction. Inventory and maintenance optimization is crucial when the economy shifts locally and globally.
At the same time, you don’t want to invest too much in inventory. Excess inventory increases the risk of obsolescence and ties up working capital you can use for financing other current assets like accounts receivables. So procurement simply for the sake of procurement isn’t really sustainable. Likewise, staying on top of inventories across departments can be tedious unless you use technology like a CMMS.
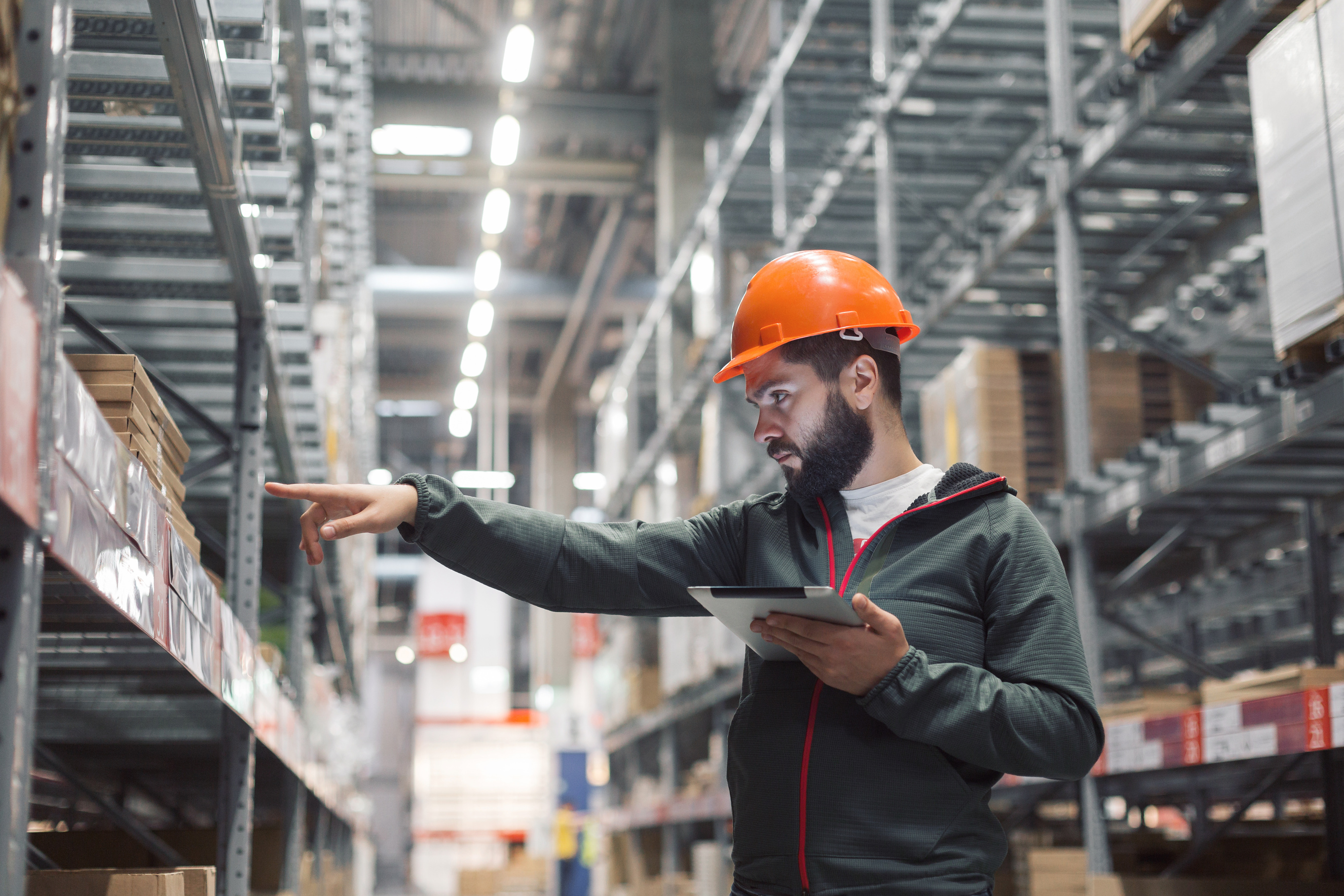
Challenge 2: Equipment Downtime
Various factors contribute to your overall supply chain performance. Forecasting raw material needs and stocking up to avoid disruption is a good starting point. Still, you can’t use those materials if one of your Maintenance, Repair, and Operations (MRO) items stops working or is unavailable.
When equipment stops working, you incur both explicit and implicit costs. For example, you may end up producing below your expected production efficiency levels, losing sales, and paying wages for idle time. Collectively, unplanned downtime costs industrial manufacturers $50 billion each year.
You can minimize downtime with preventive maintenance. Likewise, condition-based maintenance works best with an internet-connected device on or near equipment that sends real-time data to a CMMS. For example, thermal or ultrasonic sensors can monitor equipment’s heat emission levels or sound. These IIoT devices help implement predictive maintenance.
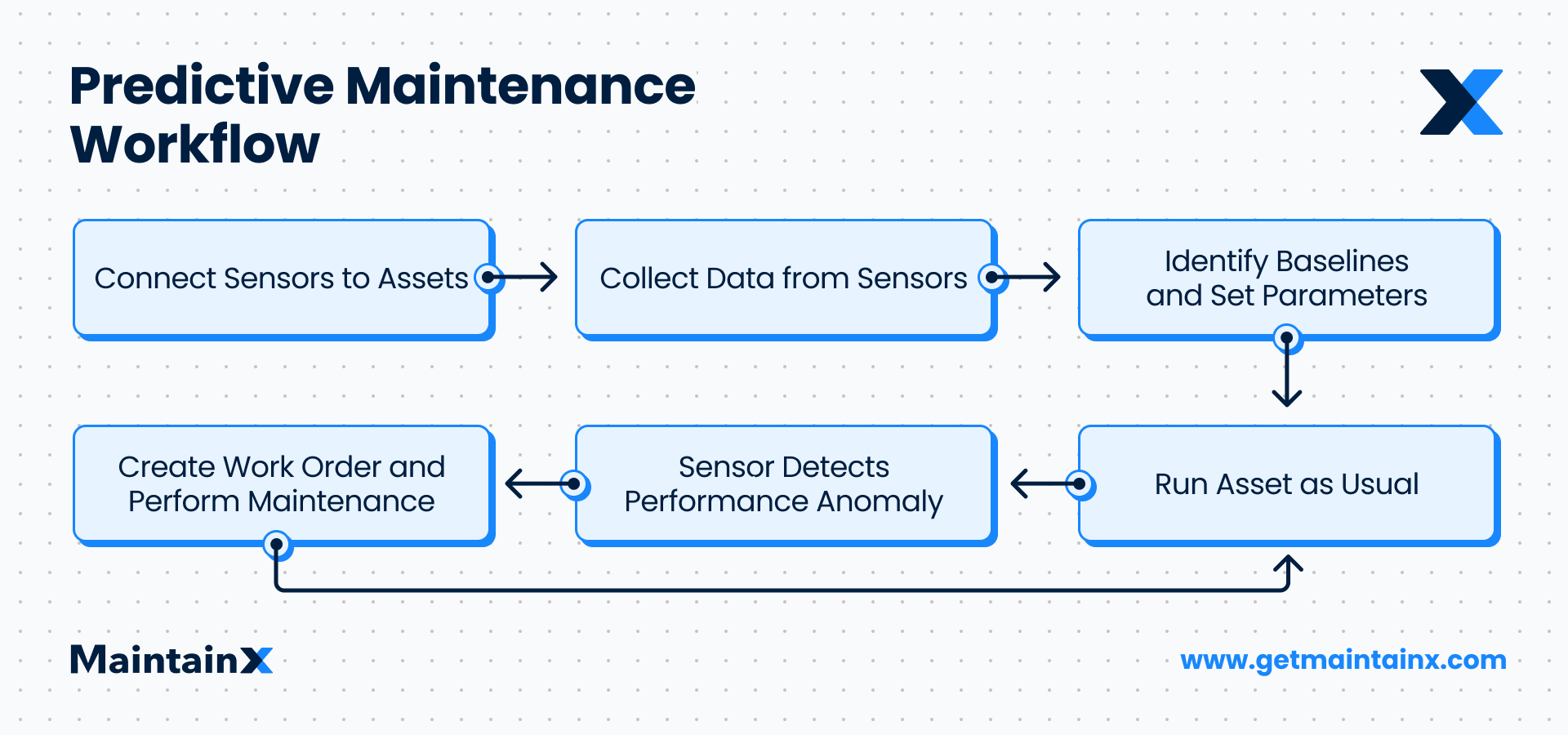
The CMMS centralizes the data collected from IoT devices, allowing you to automate maintenance scheduling. With a CMMS, stakeholders can monitor maintenance activities and asset lifecycle, optimizing maintenance planning to realize a competitive advantage over competitors that rely on traditional methods. Most importantly, you’ll ensure equipment failure doesn’t cause additional stress to an already fragile supply chain.
Challenge 3: Information Gaps and Recordkeeping
Many supply chain disruptions are due to information gaps. For example, a lack of inventory visibility can cause production and maintenance slowdowns. Also, you can’t place emergency orders quickly if you don’t have a readily available list of vendors with their prices and lead times. Even if you have this information in an Excel spreadsheet (or worse, on physical paper), you’ll waste time manually sorting through vendors.
A CMMS, like MaintainX, can host a list of vendors, service providers, and outsourcing partners. You can filter and sort this data based on your needs. MaintainX also gives you access to real-time inventory levels, so you’re always aware of the parts available and any expected inventory shortages.
Picture this: when a manager working on the shop floor notices a raw material may run out before the new stock arrives, they can contact the vendor directly from the CMMS using their mobile phone. Then, the manager can create a purchase order right from the CMMS. The flow of information is organized, fast, and efficient.
Moreover, the purchase order automatically creates a record trail, eliminating redundant business processes like printing purchase orders, maintaining paper records, and even filing them in an office cabinet. CMMS creates an information-rich ecosystem where you can view, edit, and update information on the go—you don’t need to track metrics manually.
“For decades, companies have embraced globalization and lean supply chain operations. . . while bringing down costs and reducing inventory. But the inherent weakness and vulnerability of this model have been exposed by a decade of supply chain disruptions that grew in frequency and magnitude.
Bain & Company
Effective Supply Chain Management and CMMS
Information overload is real and hard without a tool to compile and organize the information effectively. In addition, supply chain managers need to organize and supervise a range of maintenance and production processes. Setting up parts inventory initiatives, maintenance automation, and partnerships with an organization like MaintainX will help you meet customer demands. That’s where a CMMS like MaintainX can help.
MaintainX helps avoid stockouts. It allows you to calculate reorder points and set up low inventory alerts, so you always order stock when you’ve reached a specific level to avoid surprises. MaintainX also stores vendor information you can sort or search through quickly on your mobile device. Get an alert, find a vendor, and create a purchase order—it’s that simple.
In addition to supply chain challenges, MaintainX helps you control your maintenance activities, create checklists for work orders, and set up standard operating procedures. Get started on spare parts inventory management for free.
FAQs
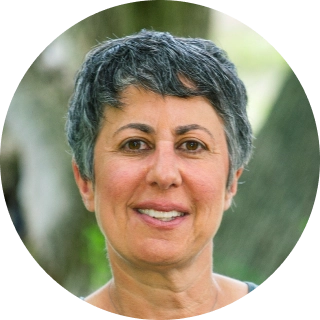
Caroline Eisner is a writer and editor with experience across the profit and nonprofit sectors, government, education, and financial organizations. She has held leadership positions in K16 institutions and has led large-scale digital projects, interactive websites, and a business writing consultancy.