
Maintenance management is the practice of maintaining a company’s critical assets and resources to ensure that production is as effective and efficient as possible and that resource use is maximized to its fullest extent. The best maintenance management sets SMART goals to keep everything on track: from budget to production to maintenance.
Simply put, a robust maintenance management program helps a company reduce equipment and maintenance issues and prevent unplanned downtime, leading to business interruption and lost profits. Therefore, a big part of any maintenance management plan is setting goals for your program and then working to achieve them.
In this post, we’ll discuss maintenance program goals that your company can set and strategies for your maintenance team to achieve them. But first, here’s a closer look.

Studies show that you are 40% more likely to accomplish a goal if you write it down. In other words, if you want your company to change, create goals around these changes.
We suggest following the SMART goal-setting process, in which each letter of this acronym stands for a different strategy related to goal setting. That is, for your team to be able to meet established goals, the goals need to be:
- S: Specific
- M: Measurable
- A: Attainable
- R: Relevant
- T: Time-bound
This goal-setting strategy helps you establish goals that are both practical and reasonable. SMART goals also help justify the allocation of additional resources or staff members to help meet the goals you’ve set.
“Well-designed performance goals can help your team align their work activities with the company or department’s overall strategy.”
Forbes
Maintenance Goals
What are tangible maintenance goals that companies should consider implementing? Here’s a closer look at companies’ standard maintenance goals and why they’re so important for maintenance technicians and asset management. We encourage you to set SMART and specific goals around these more general ones based on how your company currently performs.

Eliminate Unplanned Downtime
According to a report in Forbes, unplanned downtime costs industrial manufacturers a combined $50 billion per year when you factor in lost revenue, paying overtime to make up for order backlogs, and the cost of repairs to get equipment back up and running.
To reduce or eliminate unplanned downtime, your company should have a robust system in place to ensure that equipment is maintained and tuned up accordingly. A good preventive maintenance (PM) plan is also one of the easiest and most affordable goals to attain. PM just takes discipline and proactive thinking to stay on top of routine maintenance activities and improve asset reliability.
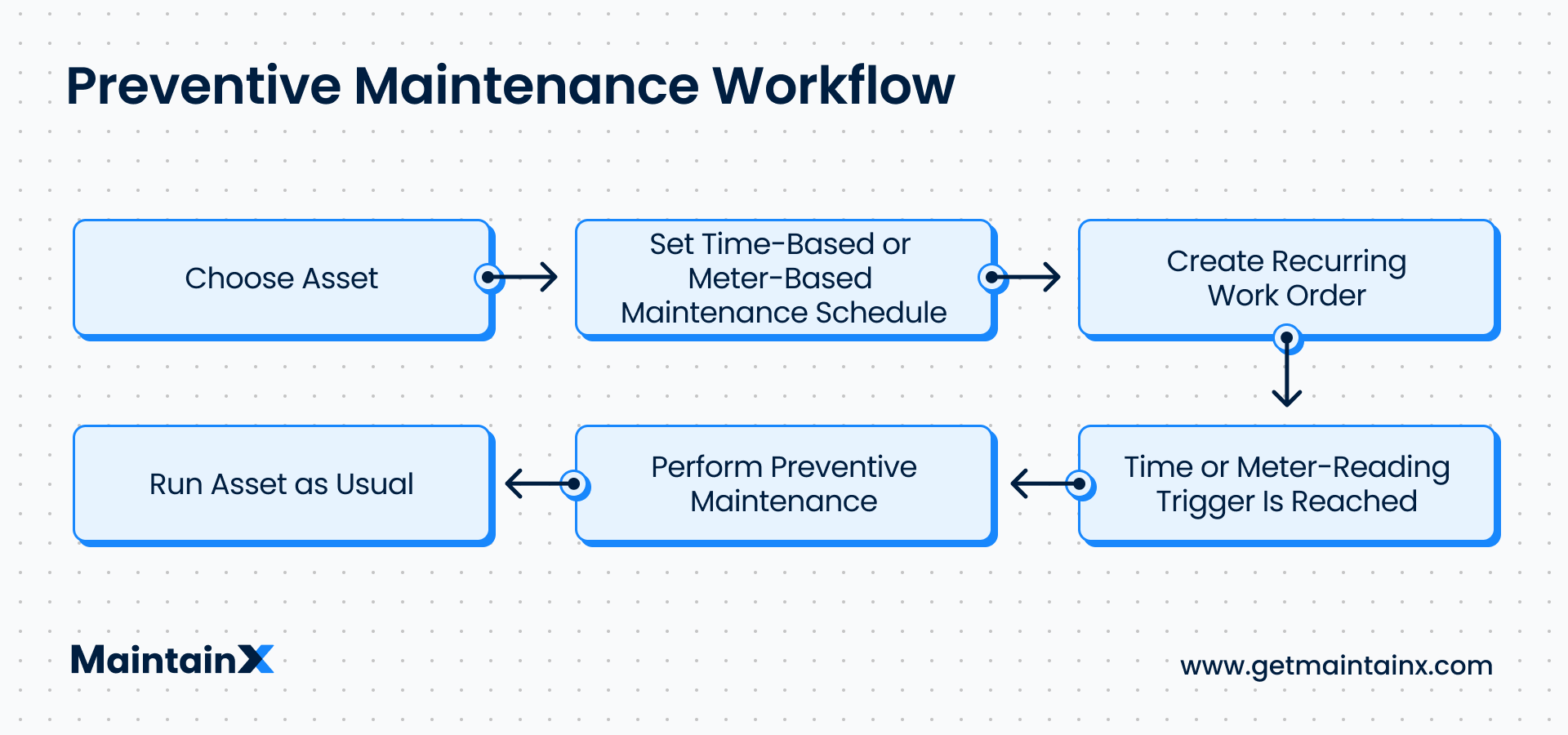
Other strategies to help eliminate unplanned downtime include predictive maintenance and condition-based maintenance. Implementing any of these maintenance plans to minimize downtime helps ensure your operations run efficiently and effectively. They also will result in a significant decrease in maintenance costs and will extend equipment life.
It’s always better to be proactive than have to practice reactive maintenance work after something goes awry.

Reduce Work Order Backlog
Late and overdue work orders often result from unplanned downtime and playing catch-up when equipment returns online. Work orders also back up because of general inefficiency as well.
Knowing this, facility managers should implement strategies to streamline regular maintenance and minimize equipment failures. A streamlined company produces its end product on time and within budget for its customers.
Improve Compliance and Safety
Companies need to comply with OSHA regulations. Some industries are more regulated than others. All industrial companies go through auditing processes to ensure they work to the proper standards. Keeping data on equipment to support this process and reaffirm compliance is a huge help. Failure to do so can result in unplanned downtime or, worse, being shut down.
Enhance Product Quality
The quality of products or services is key to business success. Quality products and services aren’t just critical to earning repeat business from customers. They’re also essential to a firm’s bottom line and profitability. Think of it this way: when you consider the aggregate expectations of your stakeholders, customers, management, and end users, what does optimum quality look like for them? What are their expectations? What would it mean for those expectations to be met?
How to Reach Maintenance Management Goals
How do you achieve your maintenance management goals? Any plan should start with a robust CMMS (computerized maintenance management system). These systems are designed to help companies streamline maintenance and maintenance department activities. Benefits associated with a CMMS platform include:
- Creating an inventory of all your equipment, work orders, and scheduled maintenance to automate practices.
- Creating a centralized equipment maintenance schedule. This doesn’t just involve individual shop floor pieces of equipment, but HVAC equipment, fire alarms, and more.
- Creating maintenance checklists and procedures for staff to follow. These include everything from standard operating procedures to lockout tagout practices and other metrics and KPIs (key performance indicators).
- Analyzing robust reporting data to assess current goals and make improvements moving forward.
- Creating a digital record of activities to help companies stay in compliance with federal and local regulations and support audits.
- Managing inventory, spare parts, and vendors all from your mobile device.
Setting maintenance goals for your maintenance team and then taking the proper steps to achieve them significantly benefits your business. You’ve probably heard it before: it starts with adopting robust CMMS software to complement these efforts.
Ready to use a CMMS to digitize your maintenance goals?
FAQs
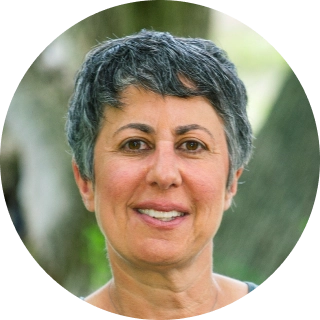
Caroline Eisner is a writer and editor with experience across the profit and nonprofit sectors, government, education, and financial organizations. She has held leadership positions in K16 institutions and has led large-scale digital projects, interactive websites, and a business writing consultancy.