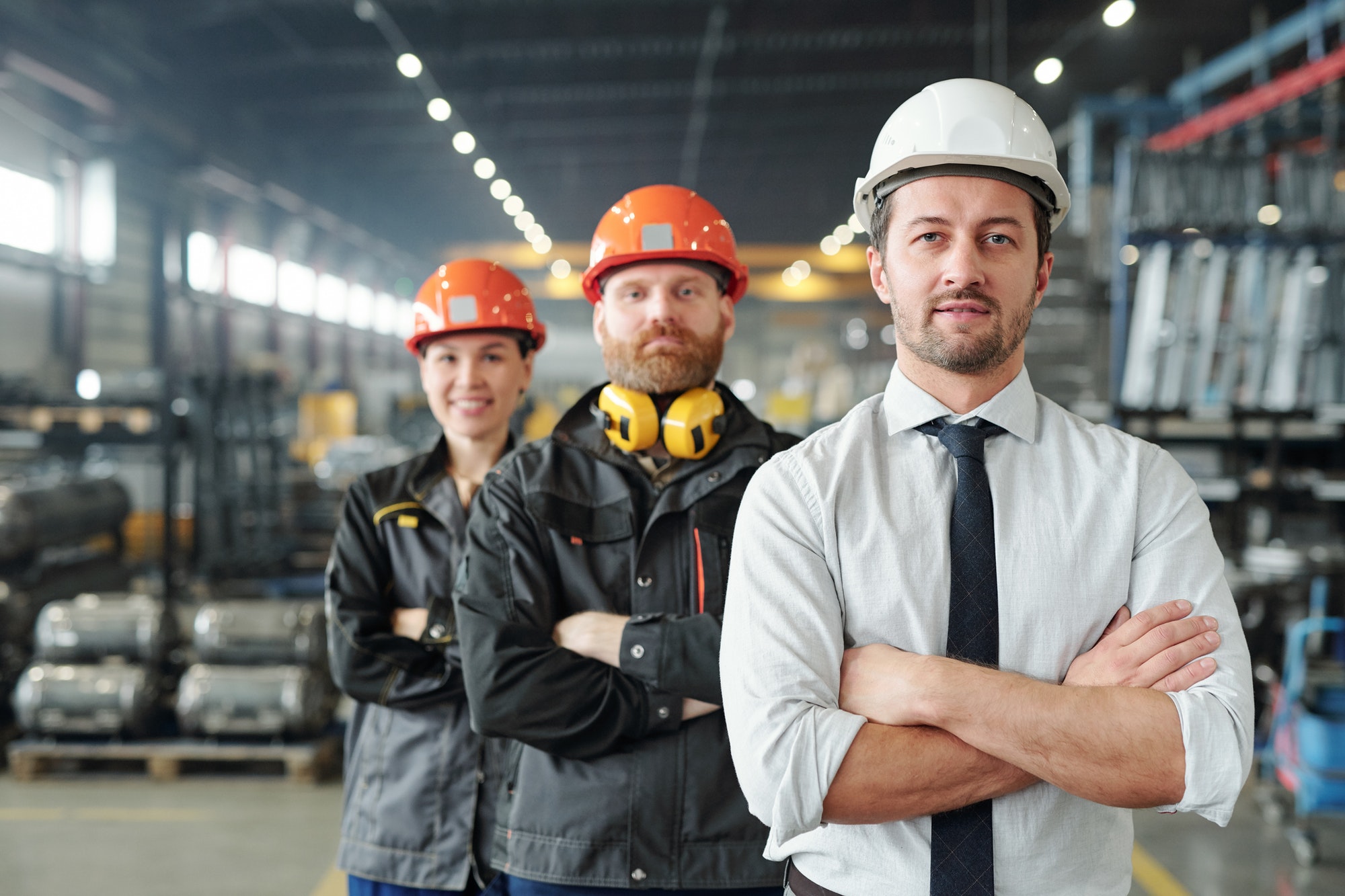
In the most direct terms, Levels of Service (LOS) refers to the quality of a given service. It is a critical part of asset and maintenance management and is used to develop and implement infrastructure management strategies to optimize the value gained from business assets.
LOS can be relatively broad in scope, depending on your business, as it considers the performance of physical assets and intangible parameters. These intangible parameters can include customer expectations and satisfaction.
Other parameters may include safety, quality, quantity, responsiveness, expenditures, availability, and environmental acceptability. Generally, the specific parameters will reflect the intersections of the various goals of your particular organization.
Think of it this way: when you consider the aggregate expectations of your stakeholders, customers, management, and end users, what would optimum service quality look like for them? What are their expectations? What would it mean for those expectations to be met?
What would ideal safety ratings be? Optimum output quality? Levels of Service refer to how operations are organized and managed to deliver optimum service to stakeholders.
“The global skills shortage is not going to ease in the short-term. . . . But technology-led solutions can optimize technician utilization and customer service delivery to mitigate the impact.”
DC Velocity
Levels of Service and Maintenance Management
Levels of Service are used in various industries and sectors to optimize businesses. For example, Departments of Transportation can apply LOS to the quality of traffic flow of a highway system by measuring parameters such as road geometry, speed and travel time of vehicles, and traffic volume.
Department of Transportation planners, for instance, also consider general road conditions when determining service levels for highway maintenance work.
For example, a road maintenance Level of Service should not be that road surface conditions, potholes, rutting, and excessive water runoff are fine unless they present a safety hazard. On the other hand, an excellent Level of Service is optimally maintaining on-and-off ramps, reducing stormwater drainage, activating snow plowing, patching potholes quickly, and scheduling yearly lane striping, all of which increase driver satisfaction and safety.
In air transport, the IATA creates LOS parameters using passenger satisfaction and queueing times to airport security into account.
When it comes to maintenance operations, there really is no set LOS methodology. However, managers can measure maintenance service levels using the same concerns regarding optimal business output.
For example, what are the business goals, and how do maintenance activities help support them? Who are the business stakeholders–internal or external clients–and how do we optimize maintenance plans to meet their expectations? Is routine maintenance enough?
By defining different Levels of Service, we can identify, for example, which type of maintenance plan—preventive, condition-based, reliability-centered, etc.—to implement.
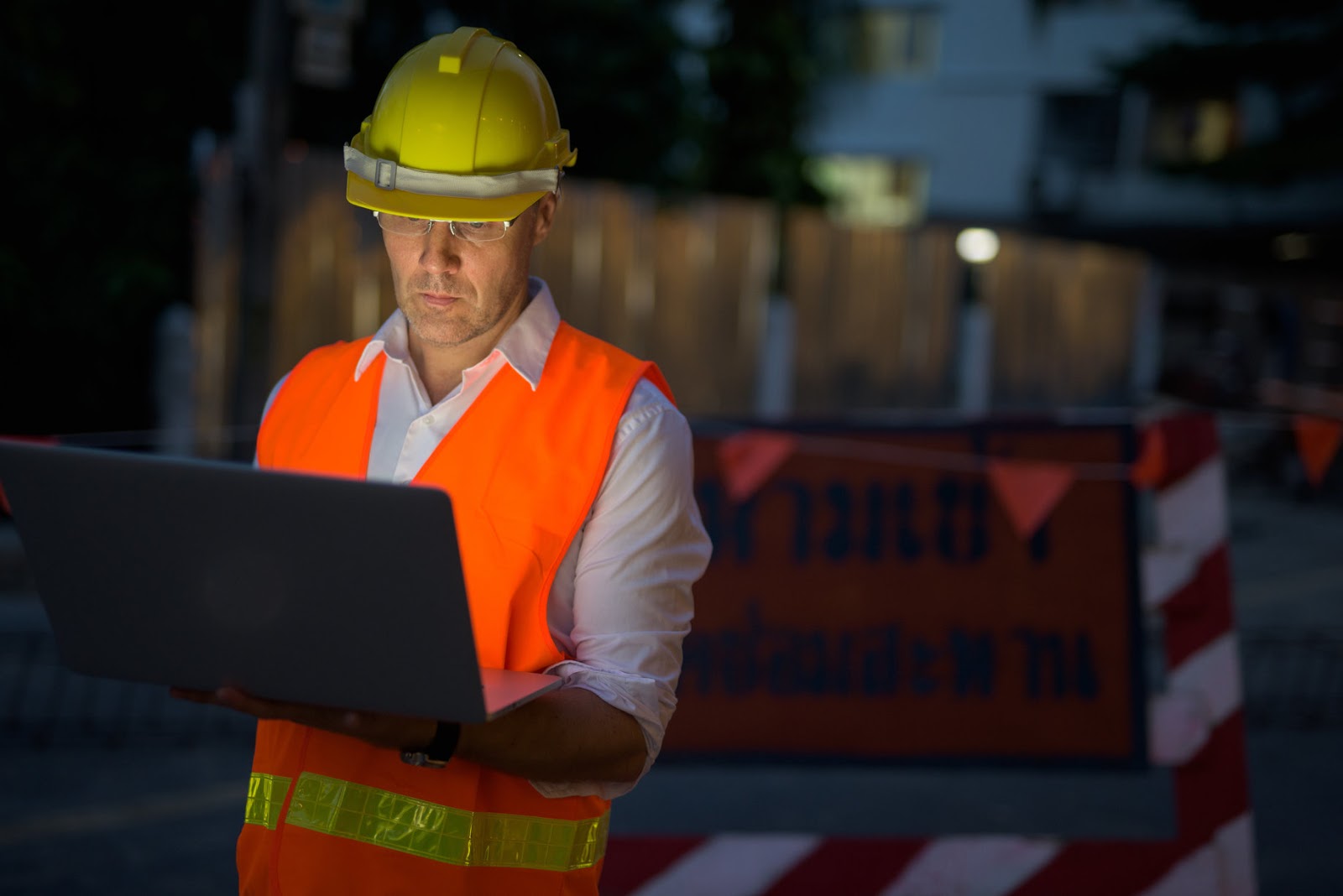
Defining Levels of Service
Suppose you’re part of a maintenance team. In this case, it may seem like a lot of trouble defining your Levels of Service, especially if you already have a robust maintenance program based on strong KPIs and preventive maintenance or routine planned maintenance.
However, properly defining your Levels of Service can do much more than optimizing your maintenance services. We always want to perform at optimal levels, get the most value from operations, and reduce waste. Defining our Levels of Service helps us track just how well we’re doing and take note of places where we might be falling short, which is the first step toward improving.
Sure, keeping track of your maintenance levels is a benefit, but it will also help ensure your company’s competitiveness within the industry. Perhaps, more importantly, defining your Levels of Service helps improve your company’s maintenance performance measures, with the potential to outpace your competitors.
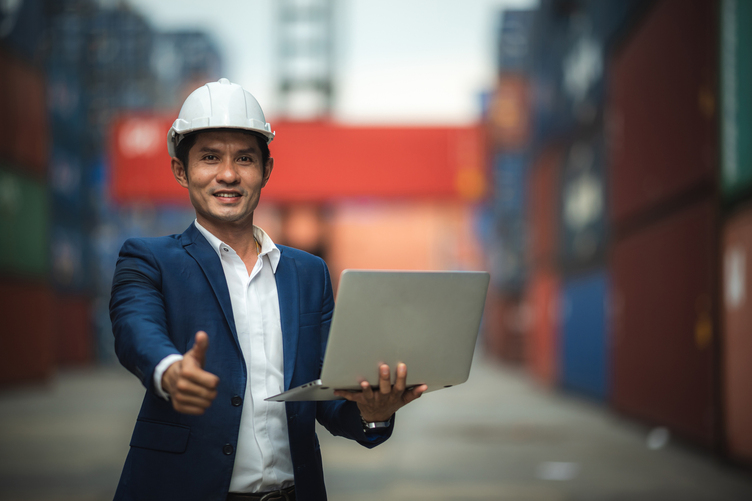
Levels of Service and Stakeholders
Another reason to manage your Levels of Service is to ensure stakeholder satisfaction. To do so, keep track of stakeholder requirements, how well the requirements are being met, and adjust as required. When thinking of stakeholder satisfaction, consider both internal and external stakeholders.
Internal Stakeholders
What internal clients have a stake in your team? Compliance? Finance? Human Resources? What are their expectations from your department?
Figuring out the answers to these questions is the first step in knowing what metrics to use to benchmark your team’s performance.
External Stakeholders
Outside of your company, who are the stakeholders? In addition to clients and end users, consider the minimum standards guiding service providers in your industry.
These may include the requirements of industry regulatory bodies and state/federal compliance expectations. For example, are there industry limits on the number of people who can be on the production floor at a time? Specifications for protective gear for staff? Guidelines for waste disposal?
Considering these will help define a robust set of criteria.
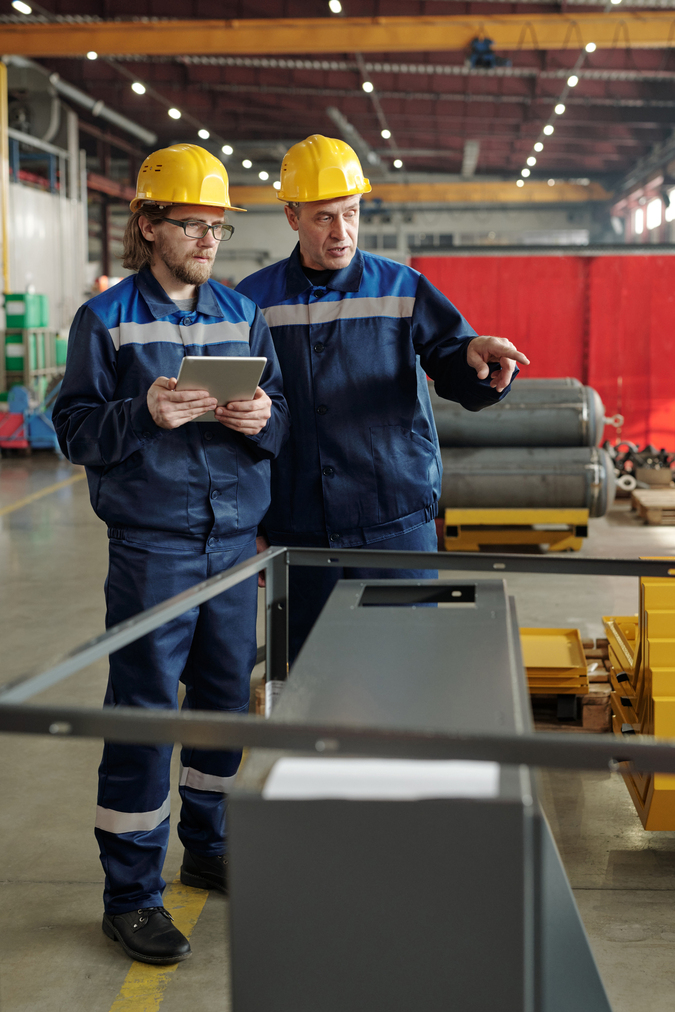
How to Define Levels of Service
The exact steps will look different for each organization, but in general, the process involved in defining your company’s levels of maintenance will include planning, implementation, monitoring, and analysis.
1. Define Maintenance Objectives, Metrics, and Needs
Defining your company’s goals, objectives, and needs goes beyond the bottom line. Look at your company’s mission, as well as any other goals. You’ll want to ask questions regarding your internal stakeholders as well.
What are the finance department’s expectations? For example, do they have revenue targets for your operations? Does Human Resources have certain attendance expectations?
Also, consider the external stakeholders. Taking all of these into account, you can build a clear picture of what the strategic goals of your operations are and what metrics you’re working toward.
2. Review Current Maintenance Performance
Measure your current performance against the set metrics. Is the team hitting the goals or falling short of benchmarks? You also may want to go a bit further and benchmark against your competitors.
In addition to your company’s goals, what else is happening in your industry? What are other industry providers doing right that you also can do? Of course, blindly following the actions of competitors is never a good idea.
However, if you’re already clear on your own company’s goals, you have specific parameters against which to benchmark your performance.
3. Set Your Levels of Maintenance Service Targets
Once you know where you stand in comparison to your business objectives and general industry standards, set your LOS targets.
First, define what parameters you want to improve, which can be anything from customer satisfaction to maintenance costs.
Second, set specific goals for each metric and a timeline for reaching them. For example, you currently may be achieving 70% customer satisfaction. So, set a goal of reaching 100% within three months, increasing by 10% each month.
4. Plan and Implement Levels of Service
Once you know what Levels of Service you’re aiming for, create strategic plans to achieve them. For example, what would increasing customer satisfaction by 10% in a month require? Are the resources readily available, or would getting them require executive buy-in?
5. Monitor and Analyze Maintenance LOS
Following the implementation of your plans, pay attention to how close you’re getting to your targets. Are your plans having the intended effect, or are new issues popping up that need your attention? It may help to define beforehand how you want to track your LOS results, as well as how frequently.
Levels of Service and CMMS
While the process outlined above is relatively straightforward, keeping track of these tasks and all the other maintenance management requirements may seem daunting, especially if the only tools you have are pen and paper. But, the good news is the maintenance industry has come a long way.
A computerized maintenance management system (CMMS) can help streamline maintenance processes and centralize information. MaintainX, for example, can be used as a work order system, allowing for easy dissemination of information, recordkeeping, and communication within teams.
This means that a robust CMMS can track the outcome of your Levels of Service methodology and centralize information regarding stakeholder expectations. MaintainX, for example, records in real-time your maintenance data, facilitating long-term tracking and analysis.
Ready to optimize your maintenance management and Levels of Service? Try MaintainX. It’s free!
FAQs
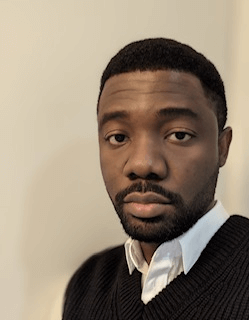
Lekan Olanrewaju is a content writer with years of experience in media and content creation. He has held positions at various media organizations, working with and leading teams at print magazines, digital publications, and television productions.