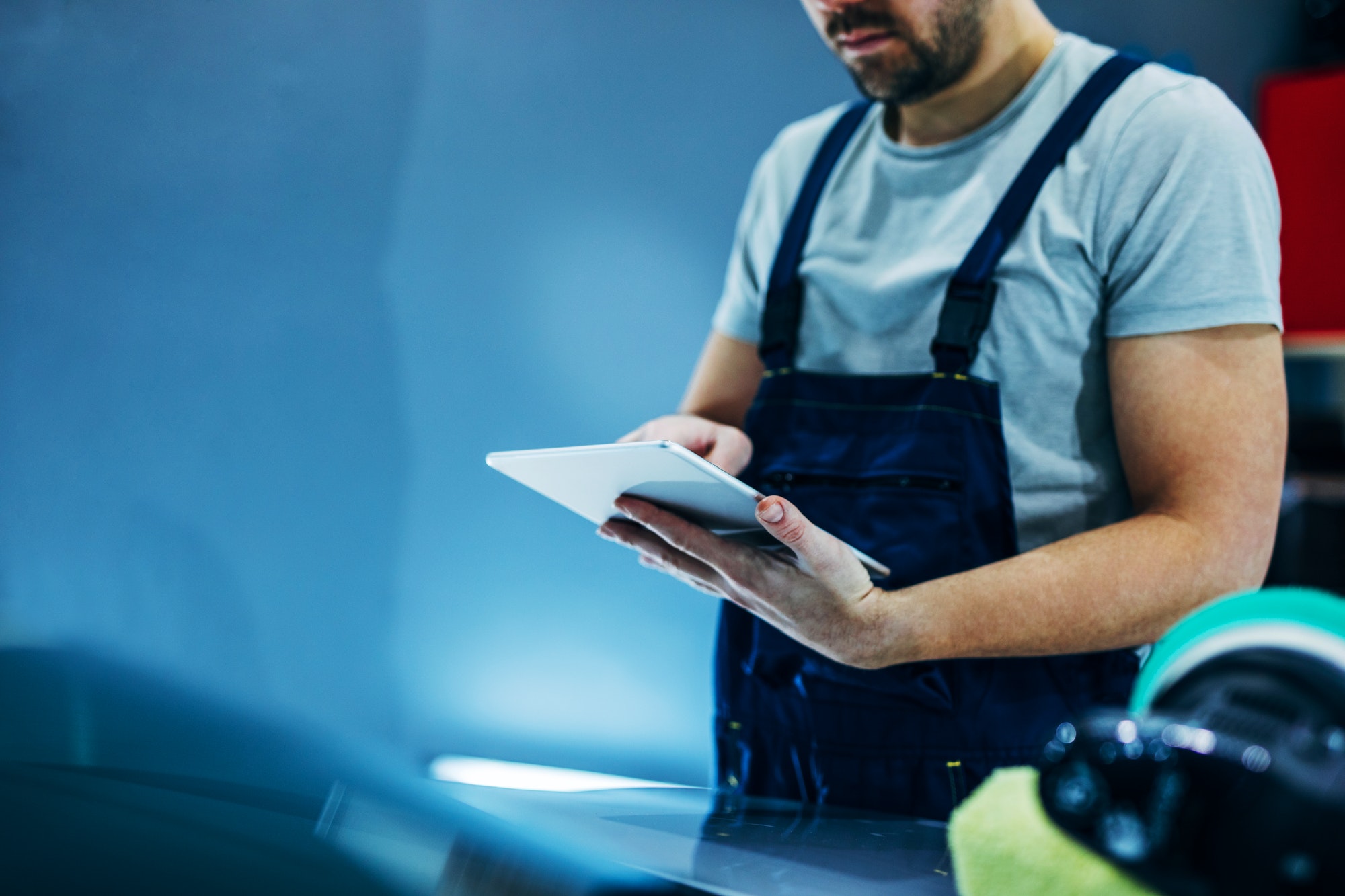
Most operational leaders are familiar with CMMS— computerized maintenance management systems that centralize maintenance information, automate work order scheduling, and facilitate better O&M decision-making.
However, as with most technologies over the past two decades, much has changed in terms of CMMS functionality, versatility, and convenience.
Companies across industries are increasingly under pressure to get more done in less time. This push for greater productivity translates to increased uptime, decreased downtime, and tighter maintenance operations. In this article, we’ll review some of the biggest changes happening right now in mobile CMMS software solutions.
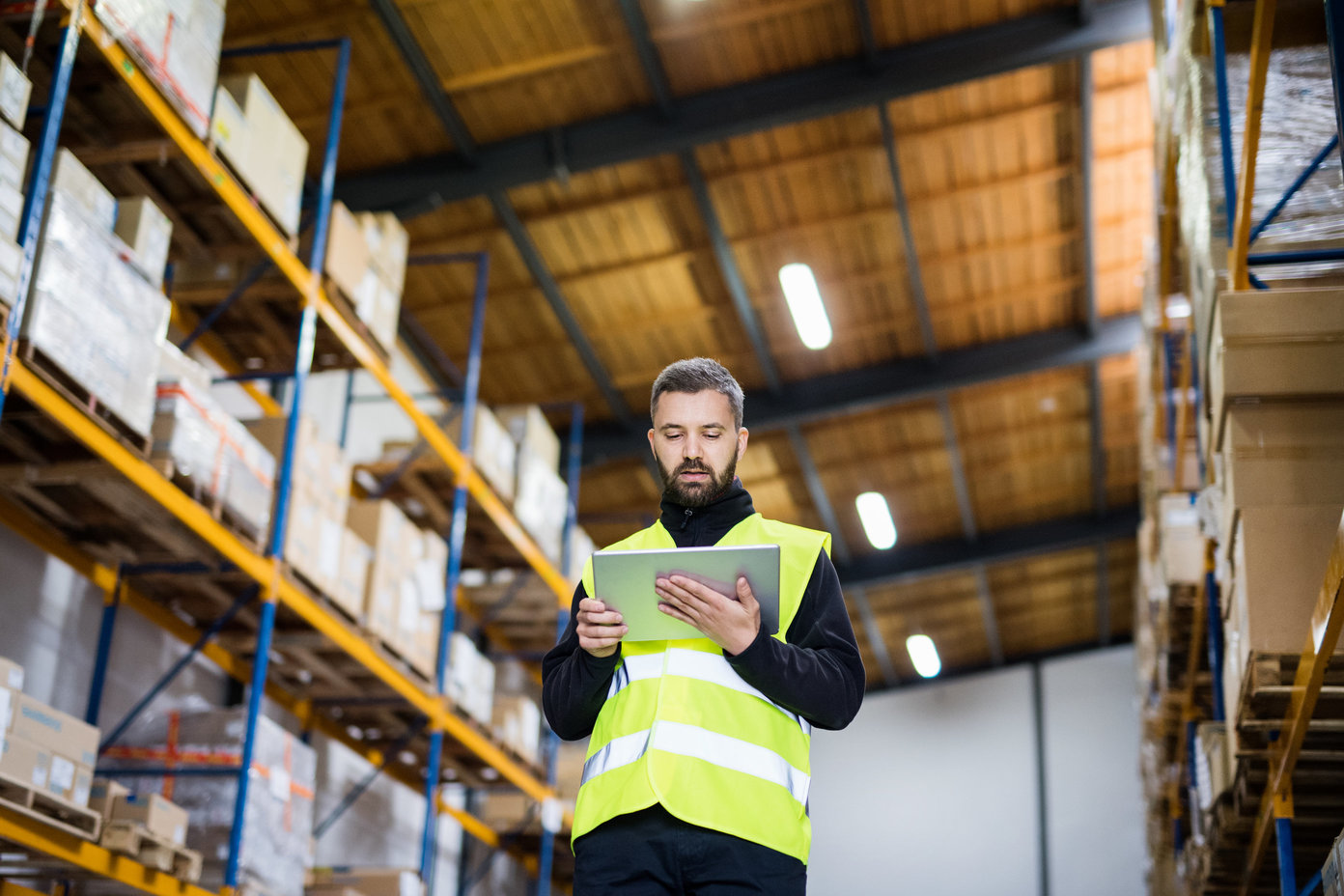
Modern CMMS across Industries
One of the biggest changes in modern computerized maintenance management software is the ability to store data in the cloud. Modern CMMS utilizes multiple servers that translate into smartphone, tablet, and desktop accessibility.
Field workers can now access modern CMMS software from their personal mobile devices. Everything from reading meters to capturing electronic signatures to using barcodes and uploading photos to track, manage, and maintain assets can be done anywhere with a WiFi connection.
SaaS providers have further altered the playing field by introducing scalable, monthly price plans, automatic app updates, and more robust maintenance program features. Translation: It’s now more affordable to implement world-class preventative maintenance programs, digitize standard operating procedures, and enhance regulatory compliance than ever before.
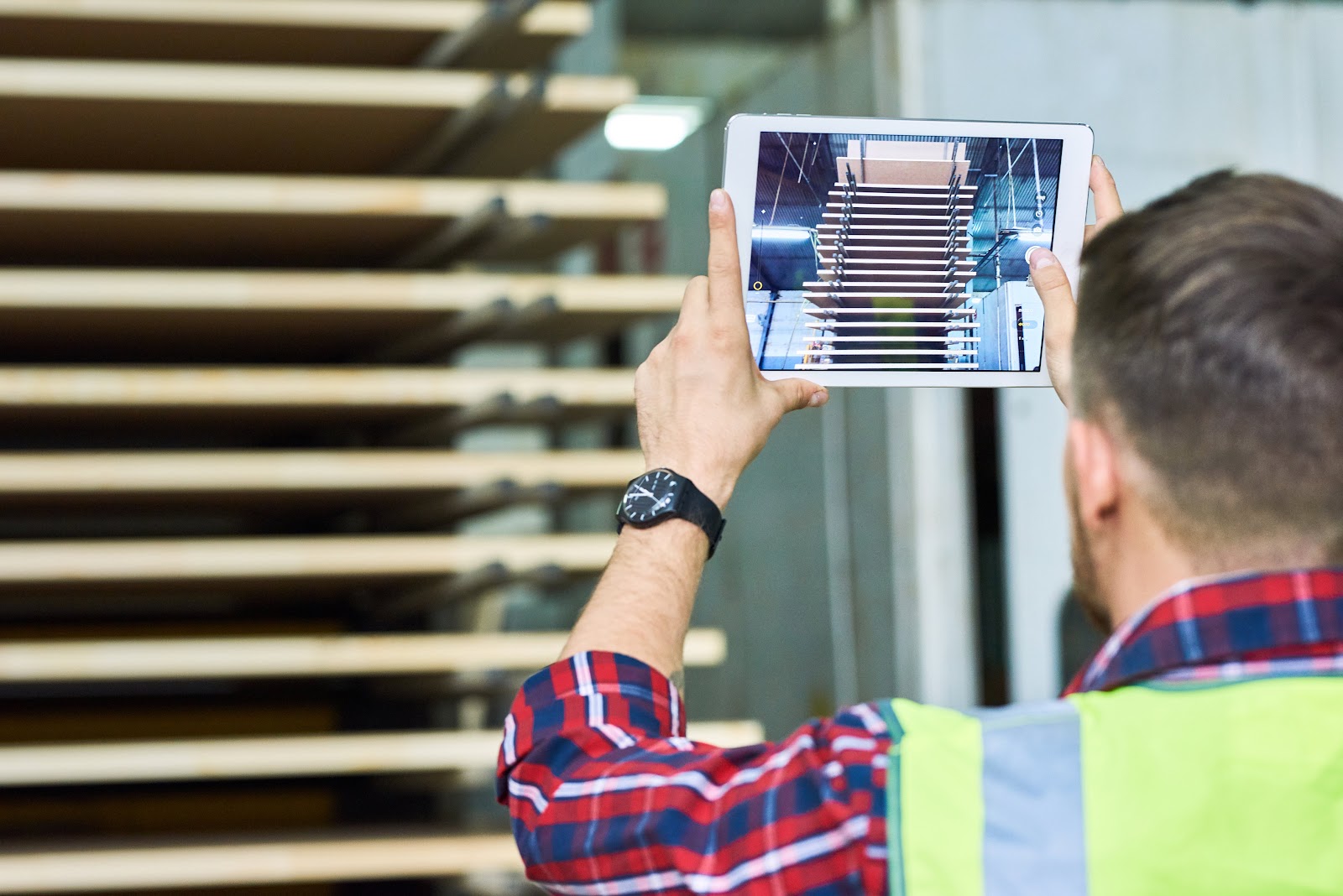
CMMS Software Capabilities
Most CMMS systems allow maintenance departments to streamline asset information, preserve maintenance history, and automate maintenance schedules with the ultimate goal of extending asset lifecycles and reducing downtime. With that said, mobile data entry is the secret to taking maintenance work efficiency to the next level.
Modern CMMS solutions help your business reduce costs associated with work order management by organizing workflows and giving insight into the status of each asset. This ultimately improves the bottom line of your organization by providing insights into resource allocation beyond paper.
Choose CMMS features that:
- Tracks resource, budget, and labor costs for every component
- Creates real-time reports of ongoing maintenance tasks
- Generates regulatory compliance checklists
- Supports inventory management
- Keeps track of all unscheduled and scheduled maintenance activities
- Tracks and filters historical records of completed work orders
- Stores information from technical procedures and documentation of assets
- Offers time and cost tracking functionality by work order
- Supports iOS and Android mobile apps
Industries Benefit from CMMS
Industries can benefit from connecting workforces and providing deskless workers with the tools and customized reports they need to feel empowered and engaged. The following are just a few of the industries that benefit from CMMS.
The best modern CMMS software can assist technicians and managers alike to perform their daily ongoing tasks more efficiently by providing real-time data on their assets.
Manufacturing
Using modern CMMS, manufacturing companies and manufacturing plants can standardize preventive maintenance processes and quality assurance plans across teams, facilities, and functions. From the way a new piece of equipment runs to how a manager audits performance, repeatable processes can always be made more efficient with digitized standard operating procedures and work orders. CMMS is fast becoming crucial to achieving efficiency on the line, uniform performance of both machines and workers, products that meet quality controls, and state and federal regulatory compliance measures.
Machine downtime is a common issue for production lines, manufacturing maintenance teams, and plant managers. There is no easy way to overcome this. However, downtime is variable, and reducing your mean-time-to-repair is a reasonable goal. Modern CMMS software systems provide preventative maintenance functions, optimized spare parts inventory levels, improved scheduling and planning, and measurable regulatory compliance.
Education
Digitized school facility maintenance plans can focus on campus day-to-day operations and long-range school management priorities. Campus preventive maintenance activities and tasks mean much more than just fixing broken equipment for faculty and students. A well-managed modern CMMS provides evidence that school facilities are, and will be, cared for according to quality assurance plans and regulations.
Universities, college campuses, and schools need to adhere to and comply with many strict regulations and rules. The benefits are actually many for example: ensuring preventive maintenance, faster response time, improved workflow management, improved asset tracking & reporting, better communication, and improved performance.
Hotels
Augmenting the customer’s experience is the biggest priority in the hotel industry. Facility managers in this industry strive their best to ensure that their equipment and facilities are up and running smoothly round the clock. CMMS can benefit the hospitality industry with a managed daily inflow of tasks, improved asset tracking, improved response time, minimal equipment downtime, lower maintenance costs, etc. Hotel maintenance management requires the ability to generate work orders and schedule preventive maintenance.
Restaurants
Modern CMMS reduces the time owners and managers need to spend on inefficiencies. Completed checklists provide proof of good service, cleanliness, meal preparation, and preventive maintenance of kitchen appliances.
Digital SOP and work orders reduce the time spent on training and reduce reactive maintenance. Standard Operating Procedures prepare staff for OSHA and food regulatory compliance inspections.
Warehousing and Facilities Management
In warehousing and facilities management, modern CMMS combines supply-chain processes and technology to increase efficiency and productivity and helps manage efficient warehouse processes by managing inventory and storage information throughout operations.
Owners and managers can remotely monitor warehouse quality assurance plans, safety rules, and industry compliance regulations. Automating warehouse work orders and standard operating procedures gives managers accurate, real-time information at their fingertips.
In today’s age, facility and maintenance managers can’t keep track of all phone calls, e-mails, and spreadsheets manually. CMMS software is the ultimate solution to handle these problems easily.
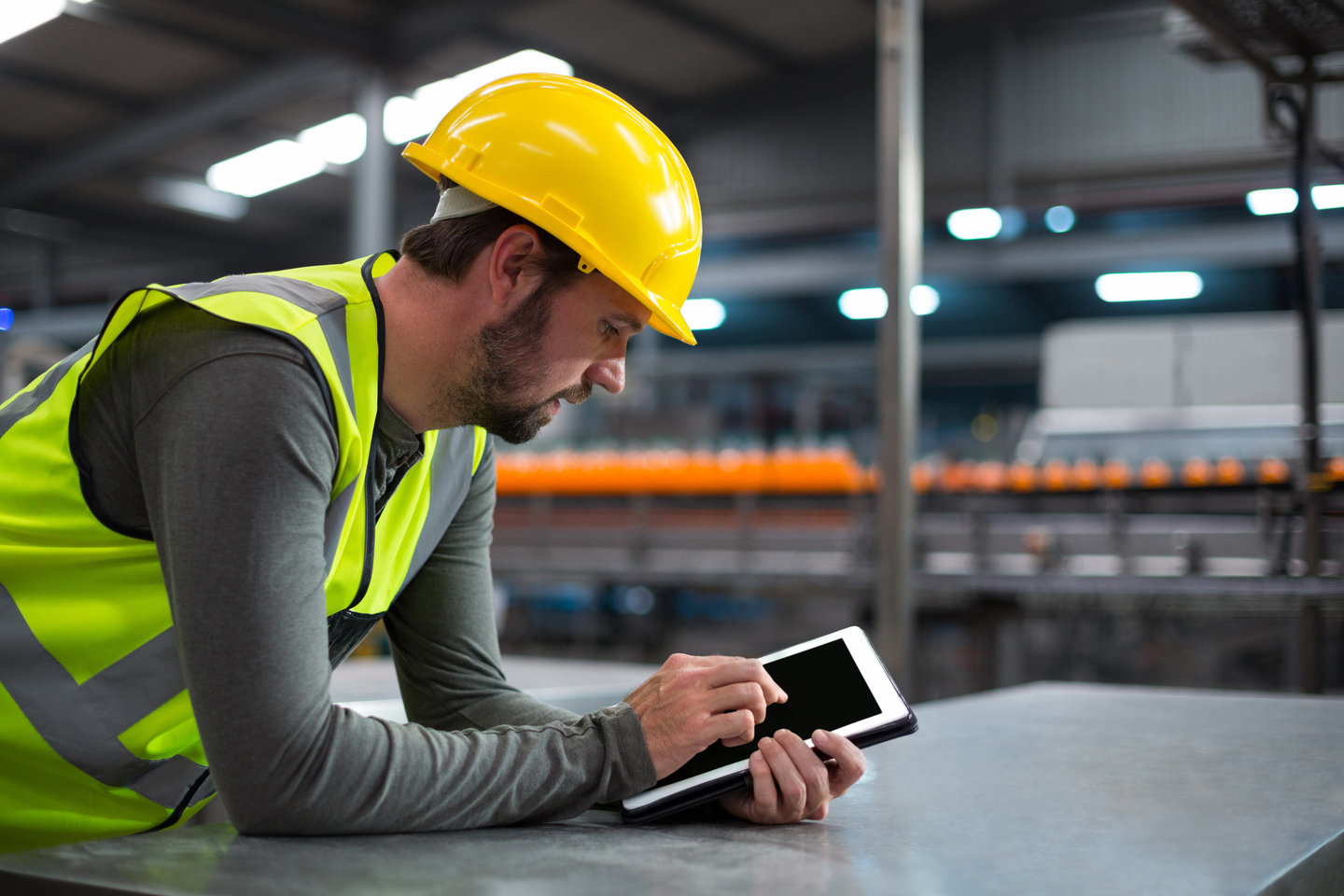
A recent PWC 4.0 Industry study noted that “Companies need to think about how they can connect their workers with the equipment, information, and processes they handle on a daily basis.”
Check us out at MaintainX to see how the best modern CMMS can get you there.
FAQs
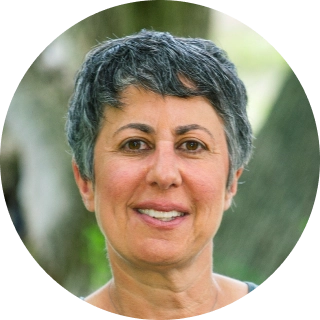
Caroline Eisner is a writer and editor with experience across the profit and nonprofit sectors, government, education, and financial organizations. She has held leadership positions in K16 institutions and has led large-scale digital projects, interactive websites, and a business writing consultancy.