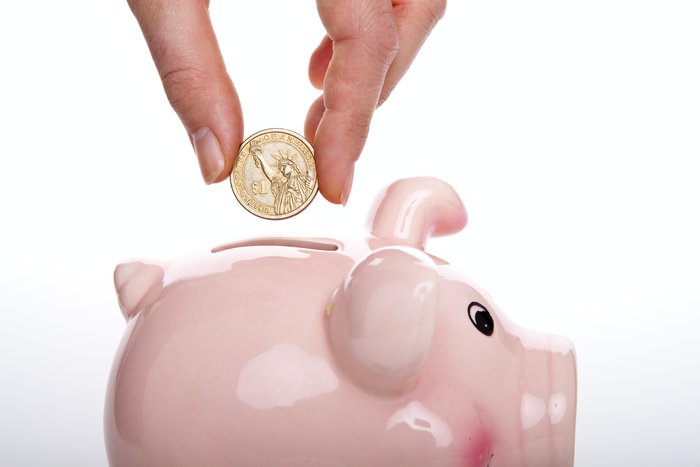
It’s no secret that expensive pieces of equipment require routine care. The best facilities preventive maintenance programs consistently monitor assets so they will perform longer. We know that the less often you have to replace assets, the more capital your facility has to invest in things like hiring top talent, developing new products and services, and expanding grounds in the future.
However, if you fail to perform your manufacturers’ recommended routine maintenance, you could be looking at costly downtime expenses.
Unsurprisingly, the number one reason for unscheduled downtime is aging equipment. What is the “not-so-secret” secret to prolonging facility asset longevity? Organized AND realistic facilities preventive maintenance (PM) programs that can save your business as much as 12 to 18 percent in costs.
In this post, we’ll cover everything strategic preventive maintenance can do for your facility and the steps you can take to launch a successful PM program.
What Are Facilities Preventive Maintenance Programs?
Preventative maintenance (PM), or scheduled maintenance, is a type of maintenance that’s regularly performed on facility assets in order to minimize the likelihood of equipment failure.
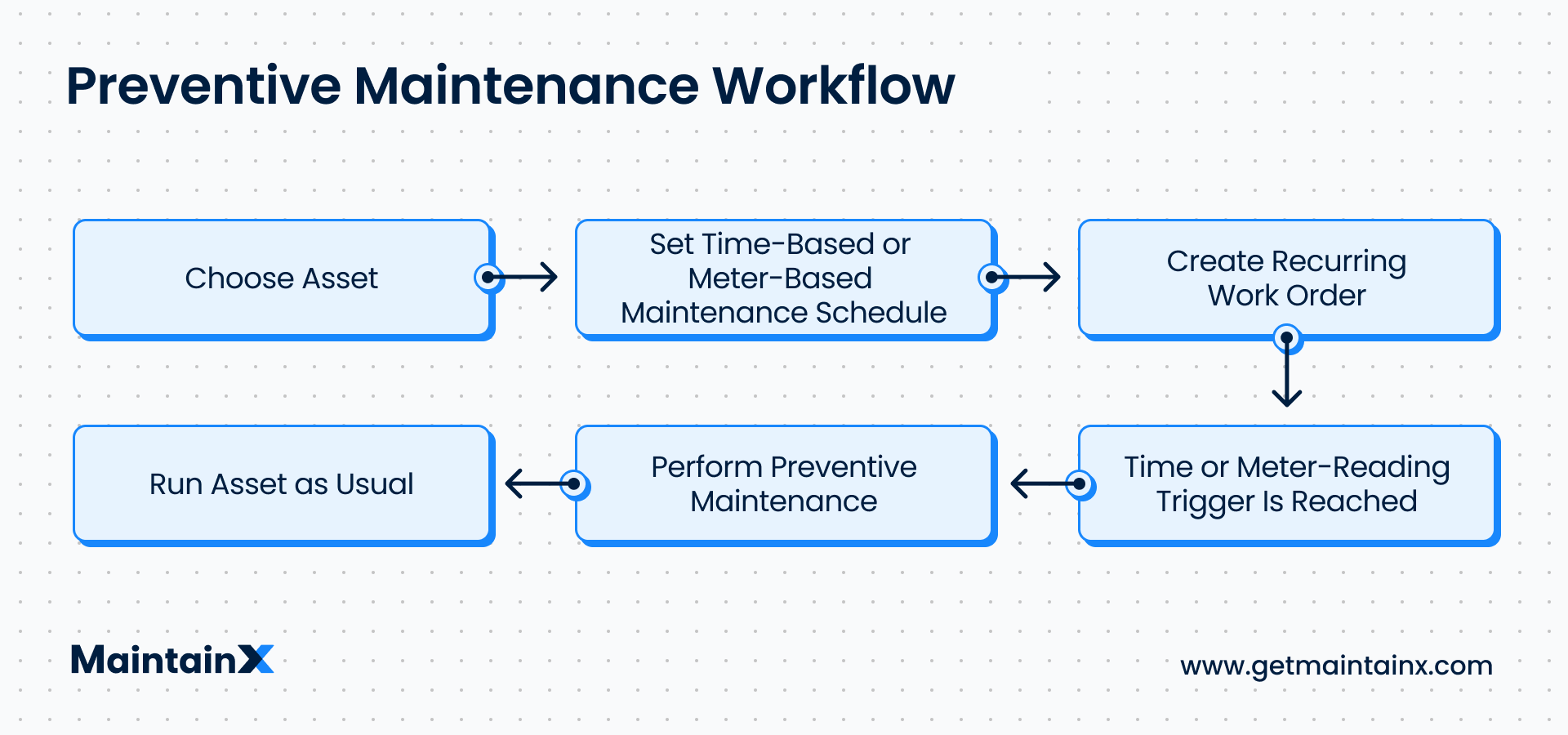
Facilities preventive maintenance programs revolve around scheduling routine tasks to extend asset lifespans. Depending on the type of facilities you run—government buildings, college campuses, industrial plants, rental properties—PM tasks can vary dramatically. However, most PMs are centered around cleaning, lubricating, and replacing parts. Implement preventive maintenance checklists with regular inspections to stay on top of maintenance tasks.
Facilities preventive maintenance programs are centered around two primary goals:
- Reducing unnecessary downtime, which usually impacts production times, customer experience, and outsourcing expenses.
- Extending asset longevity so organizations don’t have to make expensive new purchases sooner than necessary.
This is why facilities preventive maintenance programs revolve around recurring scheduling; often with help of facility management or work order software. Facility management can digitally assign recurring work orders to technicians who then check equipment, perform regular maintenance, and make repairs as needed. If you’re thinking that sounds simple that’s because it is, in theory. Unfortunately, a large number of facility management teams are stuck in a reactive maintenance mode because they mistakenly assume they can’t afford to make the switch.
Reactive Maintenance (aka wait until it’s broken)
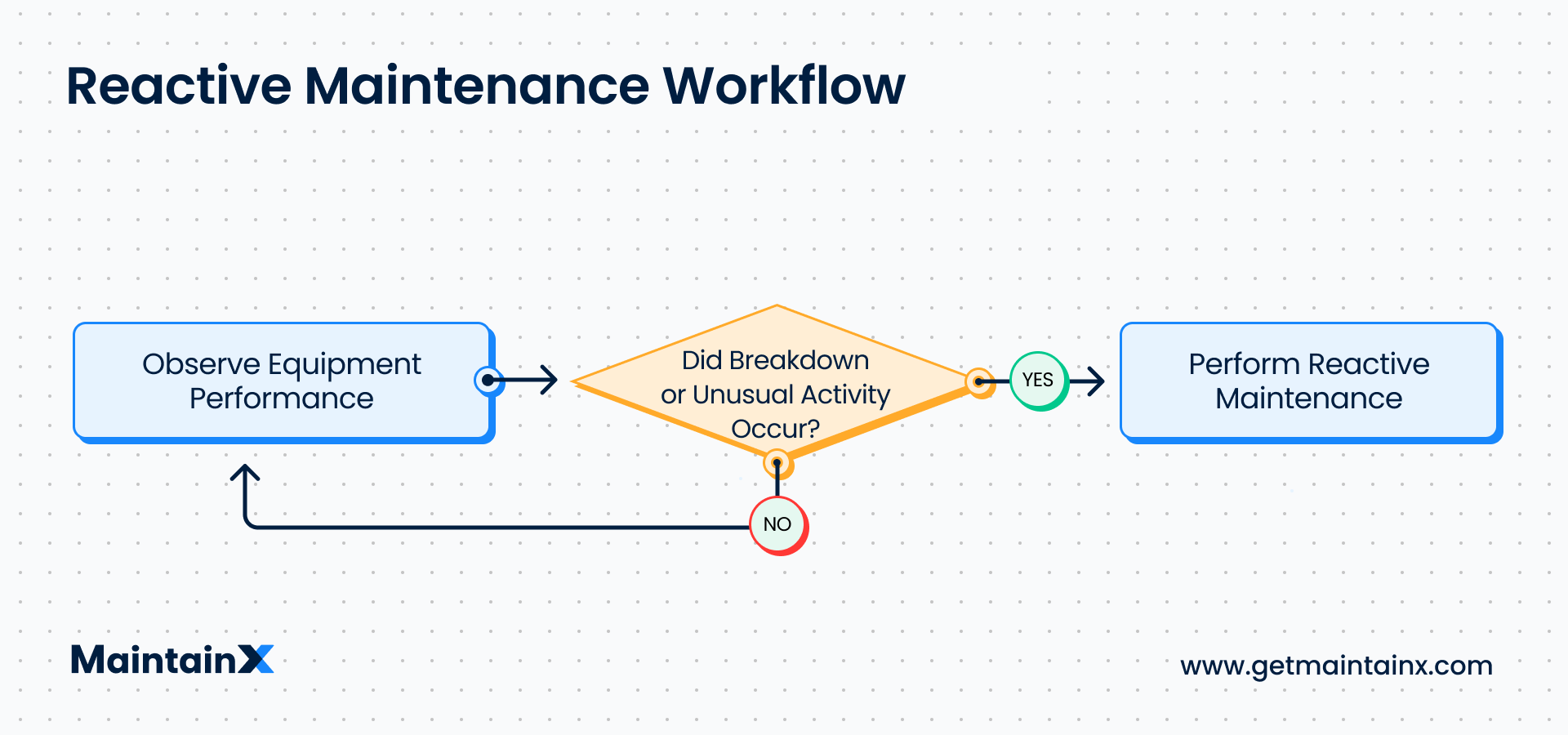
Technicians practicing reactive maintenance don’t inspect equipment until it breaks down or they happen to notice a parts malfunction. According to the Schneider Electric report, Predictive Maintenance Strategy for Building Operations: A Better Approach, 55 percent of U.S. companies exclusively practice reactive maintenance.
Translation: They wait for something to break before fixing it. As previously mentioned, running equipment for failure is expensive! Some studies suggest reactive maintenance could cost up to 10 times as much as a structured maintenance program. Translation: Exclusively practicing reactive maintenance isn’t cost-effective because it results in unplanned expenses.
Facilities don’t just lose money on malfunctioning equipment; they waste funds on costs associated with lost productivity, overtime labor, and spare part/storage purchasing. However, reactive maintenance should not be performed on every asset. Effective preventive maintenance programs aren’t centered around planning for every asset. A good rule of thumb for determining whether or not to perform preventive maintenance on a particular asset is to ask yourself: Would the associated costs of performing PM be less than the cost of failure for this particular asset?
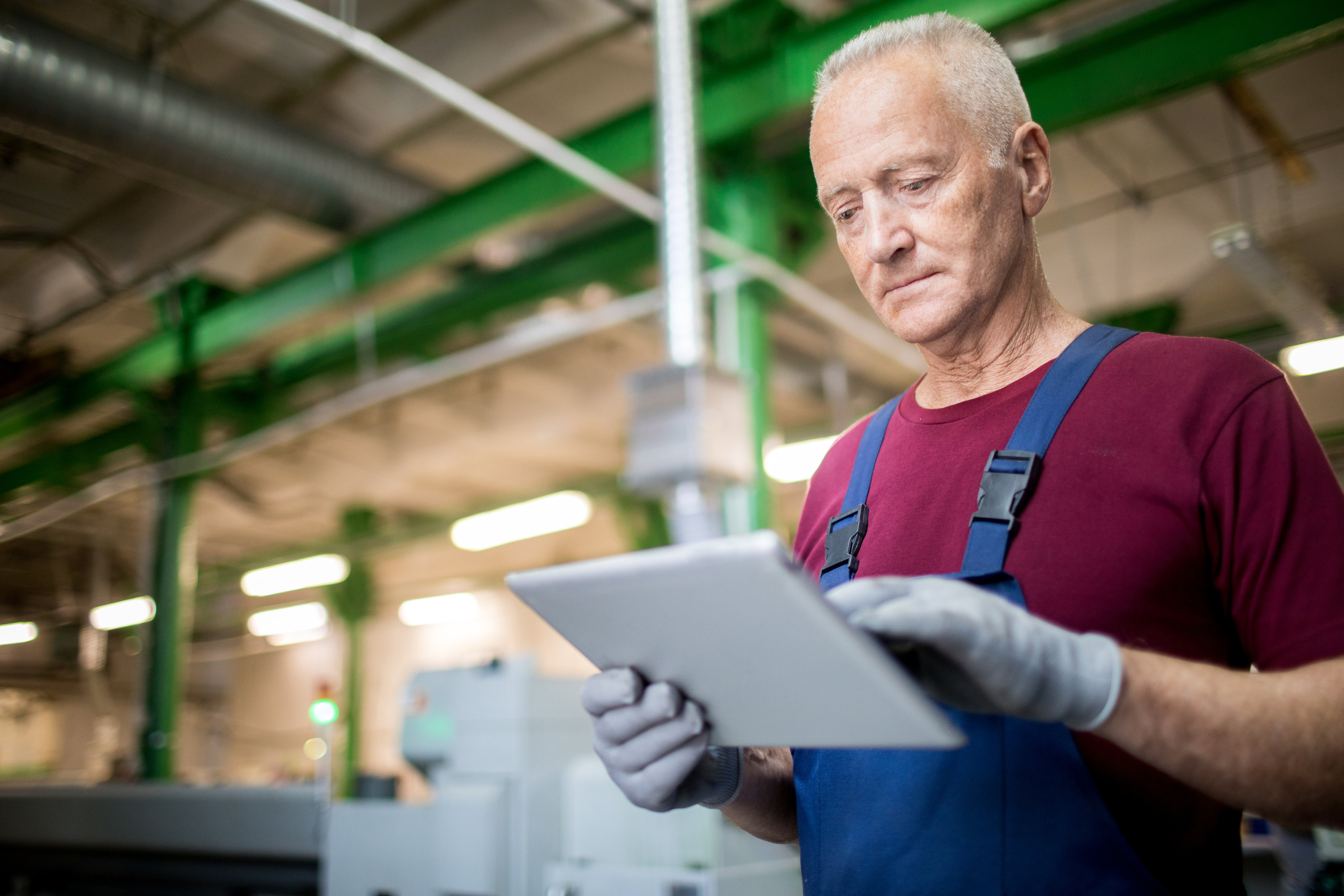
Top 5 Benefits of Facilities Preventive Maintenance Plans
1. They reduce costs
The term downtime, or outage duration, describes the period of time when a system stops working as designed. Though most folks associate the term with a remote network of IT servers, it can apply to any sort of equipment failure. Downtime could be caused by an old air filter, door locks, a worn-out bearing, or any number of production part malfunctions.
Here’s what happens when facilities function without any sort of periodic maintenance plan in place:
- Unplanned downtime halts production, causing missed deadlines and disappointed customers.
- Employees sit around on the clock, waiting for operations to resume.
- Technical staff is paid overtime to work on failed equipment.
- Professionals are outsourced in the event staff members are unavailable.
- Management pays expedited shipping fees to get emergency parts delivered.
Of course, facility managers who practice preventive maintenance schedules mostly avoid these issues. Why? Because there are, virtually, no emergency situations with preventative maintenance. Equipment shutdowns can be scheduled for time periods that won’t impact worker productivity, customer service, or product output. Of course, the larger the organization the higher the potential for cost savings via planned maintenance.
If you haven’t been routinely tracking asset history in some kind of database, definitively answering that question may be tough. Reserve preventive maintenance for your facility’s most expensive and integral assets when in doubt.
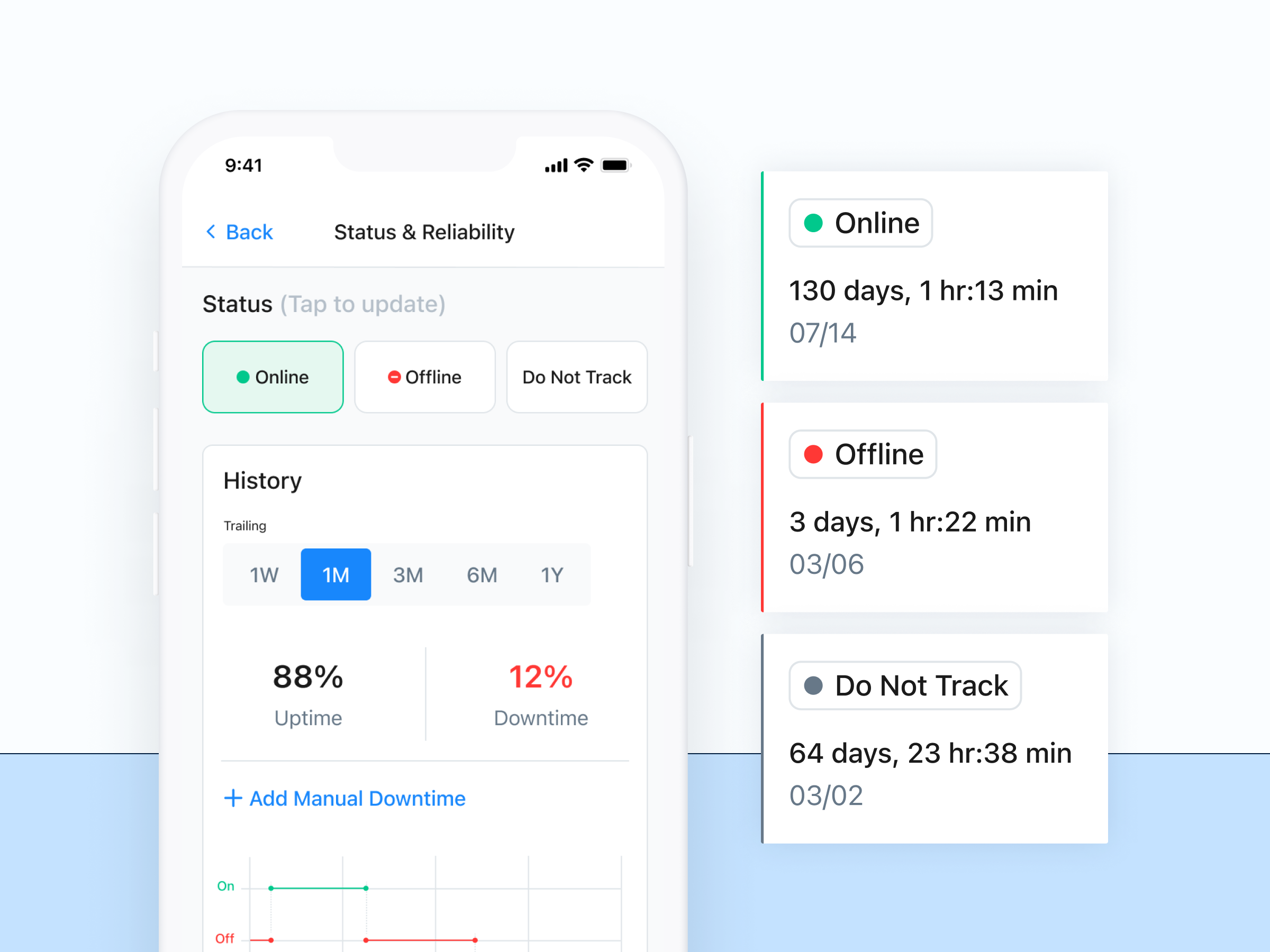
2. They decrease downtime
For the reasons mentioned above, downtime is one of the most critical metrics in maintenance management. Downtime is simply when a machine or asset is not operating according to design.
According to one survey, unplanned downtime cost 46 percent of companies $50K per hour and 28 percent of companies $250K per hour, on average. Despite recent technological advancements, many facilities and manufacturers work with machinery that is more than 15 years old.
For this reason, it’s not unusual for parts to either become unavailable or take weeks to deliver from overseas. Understanding equipment availability, and consistently following suggested maintenance schedules, can mean the difference between several hours and several weeks of unnecessary downtime. Imagine if such an event happened during the holiday season. Translation: Unexpected downtime could negatively impact incoming revenue during your facility’s highest production quarter of the year!
Additional risks that impact automation infrastructure are security, safety, and quality. You can better equip your facilities by conducting an asset risk audit to determine potential asset problems and solutions. As the saying goes, “The best offense is a strong defense!”
3. They increase equipment efficiency
This one is pretty simple—facilities' preventive maintenance programs also increase equipment efficiency, which increases overall performance. Take your personal vehicle, for example. Change your oil every 5,000 miles, or according to the manufacturer’s guidelines, and the engine will perform significantly better over time. Without the thick oil causing friction in between parts, your vehicle will require fewer service visits over the long haul.
4. They improve safety
Equipment running in subpar condition poses a risk to employees, vendors, and customers. Machine failure can lead to hazards and safety concerns, like fires. Translation: Unexpected failures present real workplace risks and liabilities. With this in mind, facilities' preventive maintenance programs can reduce on-the-job injuries and potential lawsuits.
5. They increase reliability
Finally, planned maintenance programs increase your brand’s reputation for reliability. In today’s competitive economic landscape, most businesses can’t afford to miss deadlines, disappoint customers, and generate negative online reviews. Facilities operating within the B2C industry can provide more consistent customer experiences with PM plans. Conversely, facilities operating within the B2B industry can set more realistic purchase order timelines and foster stronger relationships with suppliers and clients alike.
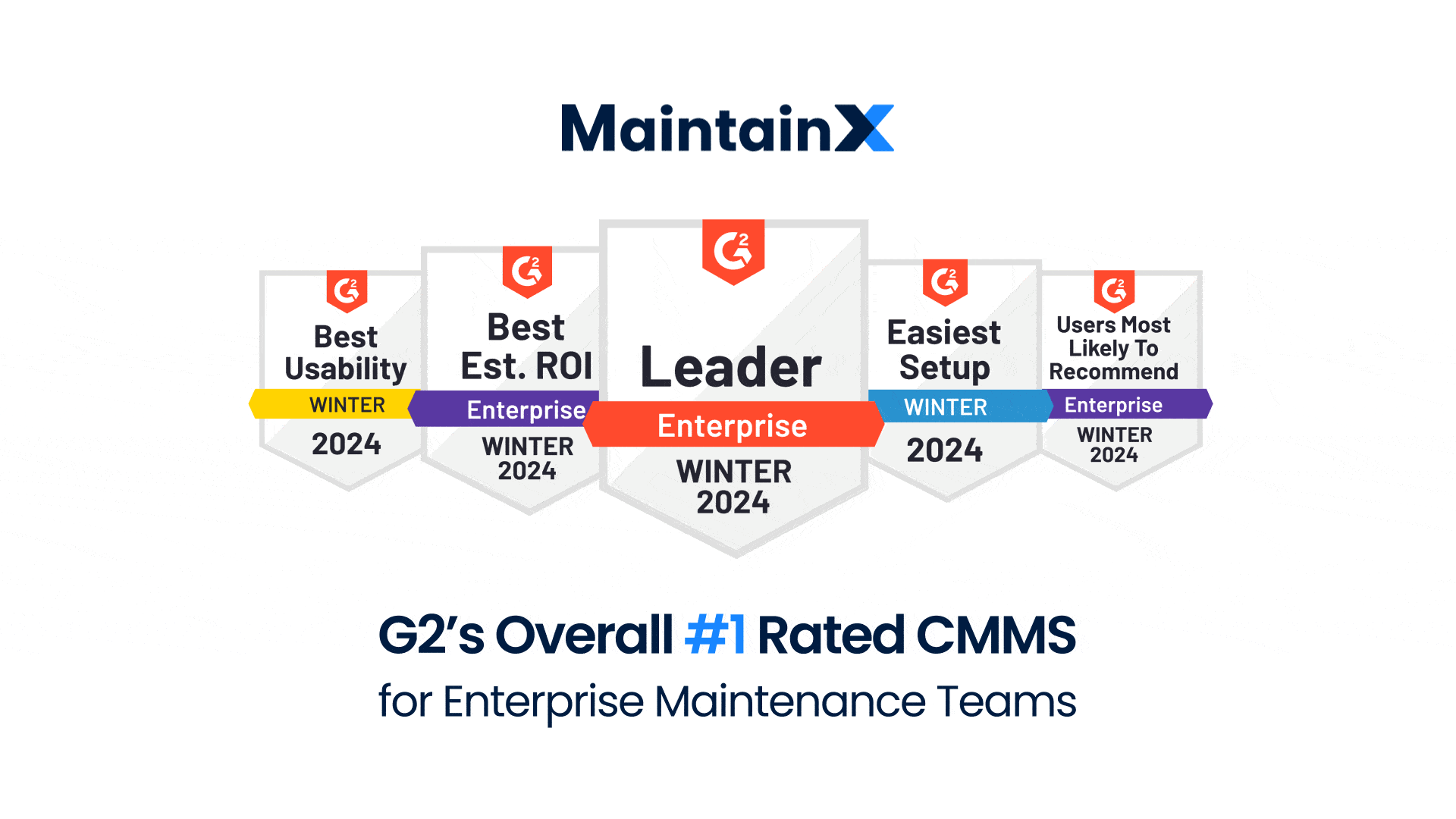
Simplify Facility Management with PM Software
Does it feel like your facility maintenance team is always playing catch-up? If so, it’s time to say goodbye to a pure corrective maintenance framework and embrace the benefits of preventative maintenance. Creating a preventative maintenance plan can be therapeutic for facility managers.
If you’re ready to streamline the work order process and enhance communication between workers, we recommend implementing a PM program with the support of work order and asset management software. Based on our experience, most facilities recoup their investment within the first year.
MaintainX is a task-management app designed to lighten the load of facility management teams. It’s completely free to download and includes everything you need to begin creating work orders, communicating with staff, tracking assets, and identifying cost-saving opportunities right away.
FAQs
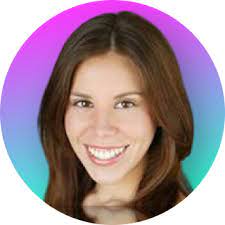