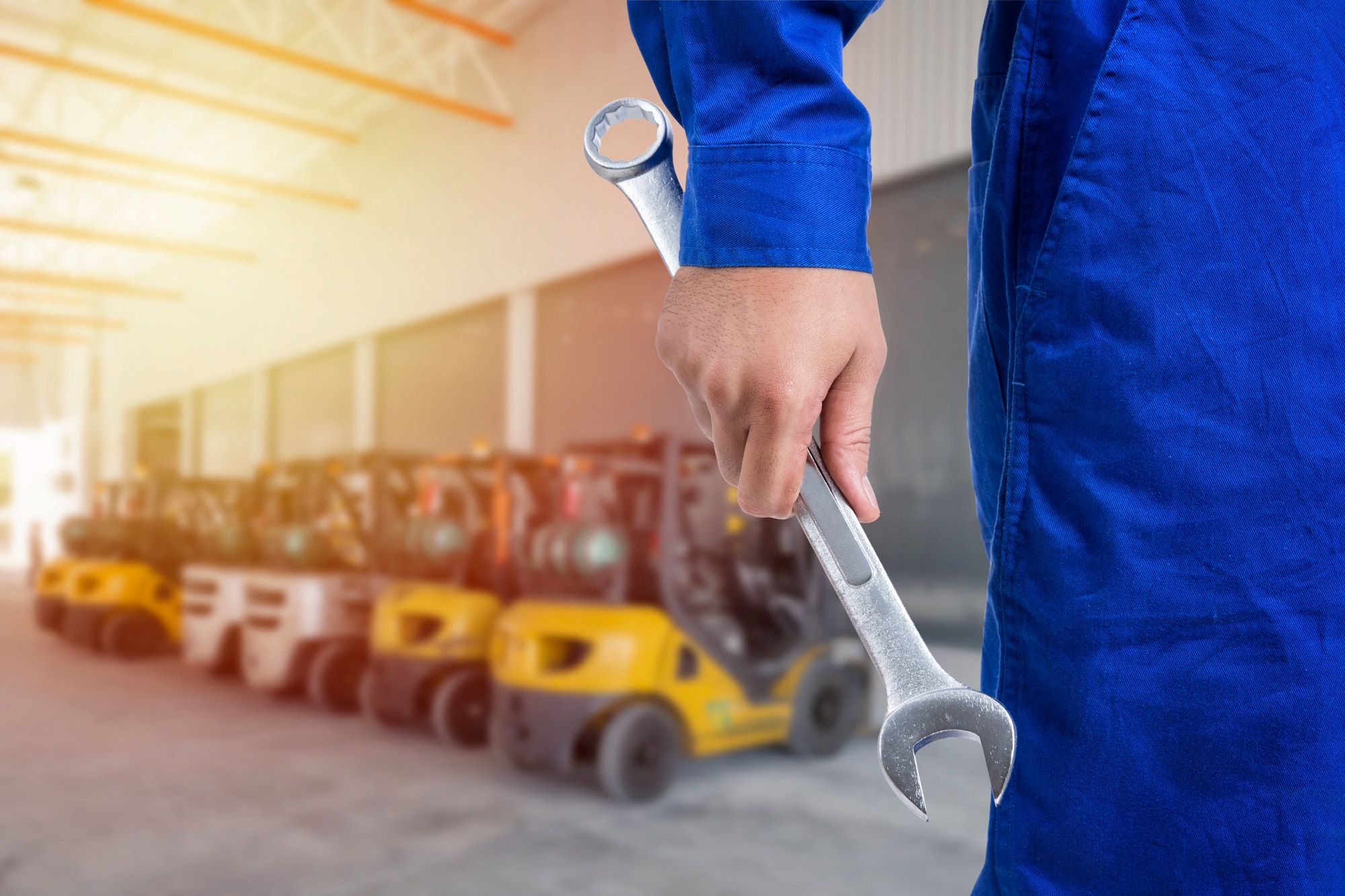
Forklifts are crucial to warehouse productivity and, therefore, so is forklift maintenance.
Without them, workers would have to lift heavy loads with manually powered hoists for hours every day. Even worse, they would have to carry items long distances across warehouse facilities.
To put this burden into perspective, forklift capacities range from 3,000 to 70,000 pounds on average. Thus, organizations that value productivity, profitability, and forklift safety procedures must prioritize forklift maintenance as if their businesses depend on it—because they do!
The best way to ensure forklift reliability is to follow a preventive maintenance program. Warehouse managers, forklift drivers, and forklift maintenance technicians must learn how to properly maintain facility equipment to prevent downtime.
The good news? Setting up a maintenance plan for forklifts doesn’t have to be difficult.
This article will share our five best tips to increase the useful life, reliability, and efficiency of your organization’s beloved forklifts.
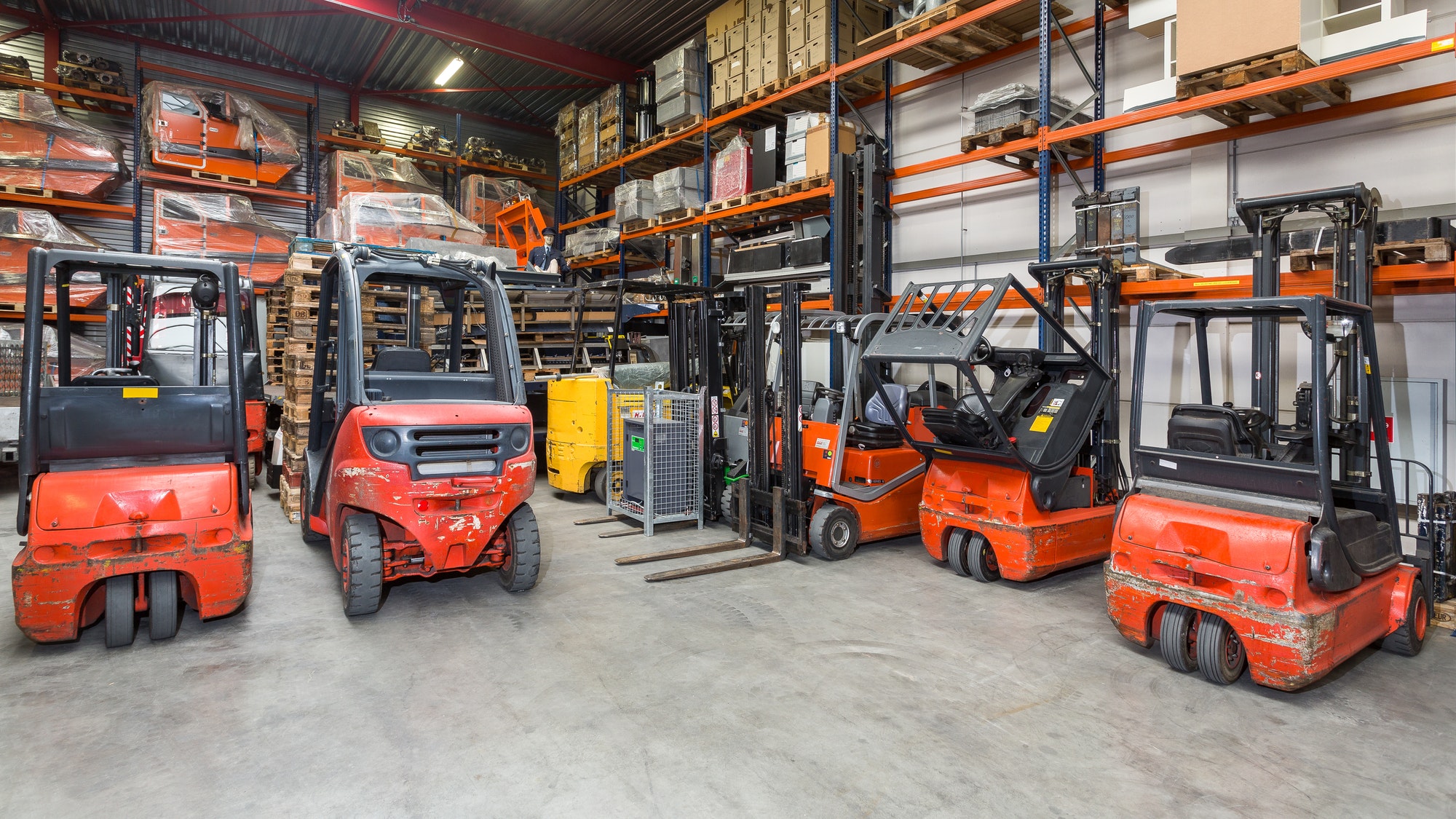
Benefits of Forklift Maintenance
Forklift maintenance is one of the most important tasks warehouse managers can schedule to ensure their teams meet production goals. It ensures that forklifts are operating correctly, safely, and at full capacity. Benefits of proactive forklift maintenance include:
- Enhanced Productivity: Consistent preventive maintenance translates to increased forklift uptime. This one is self-explanatory: the more your department can move heavy materials without interruption or downtime, the more items your team can produce per hour.
- Extended Useful Life: Well-maintained forklifts have longer service lives. The longer you can keep your forklifts running, the longer you can delay expensive replacements. According to Toyota Forklift, a new vehicle with standard capacity can range from $20,000 to $50,000 on average, depending on its features. Forklift preventive maintenance helps ensure forklifts reach their average useful life of 10 years.
- Ensured Safety: Every business in the U.S. is obligated under OSHA regulations to provide workers with safe working environments. Forklift preventive maintenance is essential to preventing injuries and fatal accidents. For example, a control system failure could cause the machine to shake unexpectedly, thus causing the machine operator to lose control. Scheduled vehicle inspections allow workers to identify and remedy equipment hazards before they become catastrophic incidents.
- Reduced Repair Costs: Beyond helping companies save money by prolonging equipment useful life, forklift PM helps avoid costly repair expenses. It’s a known fact in equipment maintenance that long-standing issues come with higher repair costs.
- Maintained Resale Value: According to Beroe, more than 75 percent of forklifts are bought on a lease agreement. These organizations must exercise due diligence to avoid incurring heavy fines at the end of their lease periods. Alternatively, those who own their vehicles should practice PM to recoup their maximum investments.
Forklift Maintenance: 5 Tips to Keep Them in Great Shape
Classifying forklifts as indispensable to the global economy is not an overstatement.
Manufacturers, distributors, and material suppliers all depend on the vehicles to keep supply chains moving. Unfortunately, these massive machines take a heavy pounding.
Workers use the machines non-stop for lifting, lowering, and moving huge pallets. Over time, the constant repetitive movements place a strain on equipment parts.
Before we delve into our best forklift preventive maintenance program tips, let’s quickly review the benefits of PM.
Now that we’ve discussed the key benefits of forklift maintenance, here’s how to keep your forklifts in optimal condition:
1. Service Forklifts Every 3 Months
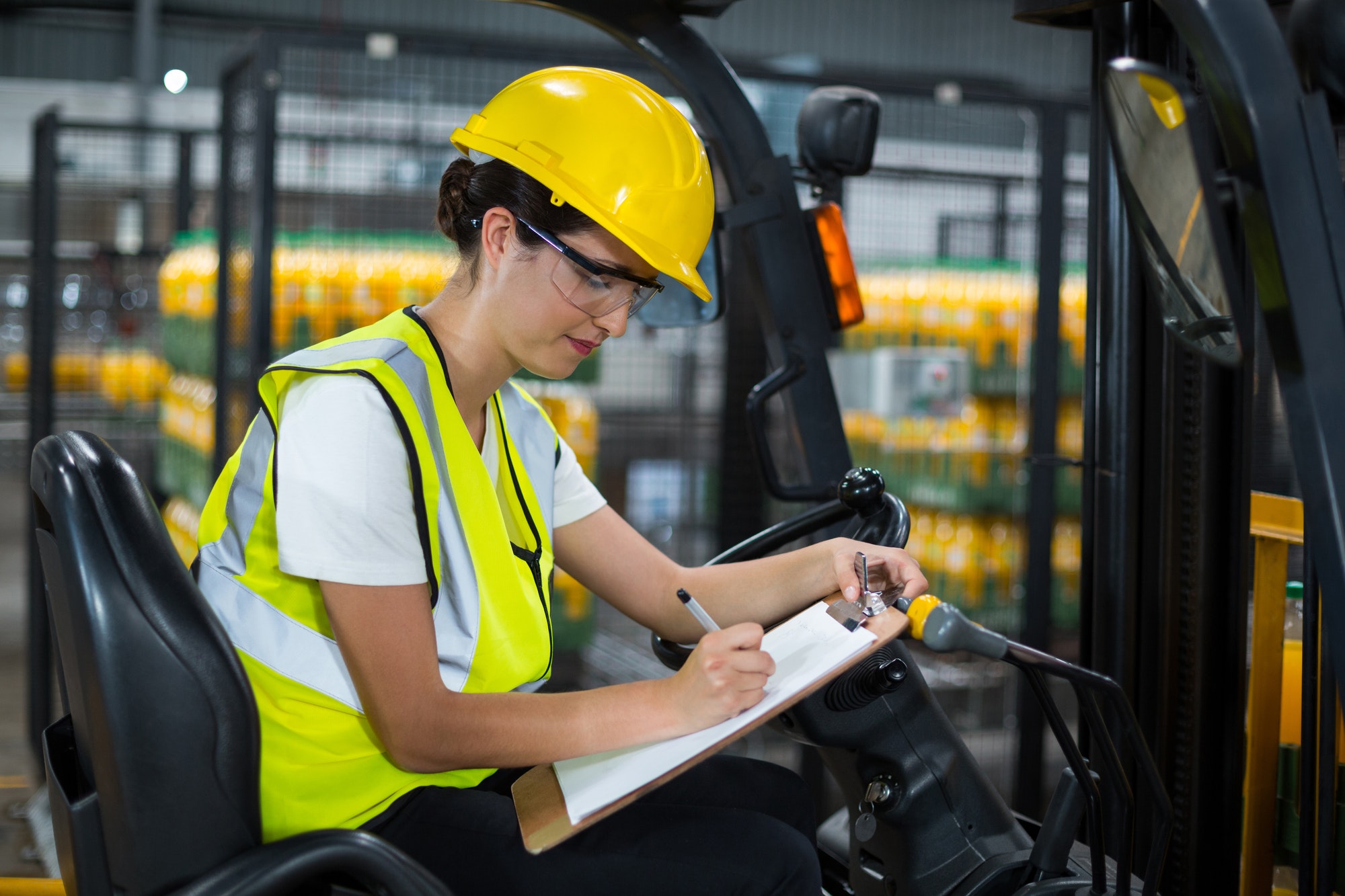
Regular forklift servicing helps resolve small issues before they become big ones. Experts recommend servicing vehicles every three months, while others suggest performing PM every 250 hours of operations. Translation: there is no one-size-fits-all guideline.
Several factors influence forklift servicing intervals, including:
- Manufacturer Recommendations: Every forklift comes with an operator’s manual. The manual usually includes the recommended service interval from the manufacturer. Of course, the recommended interval varies by the type of forklift and manufacturer. Always follow manufacturer’s recommendations to get the most out of your machinery.
- Service History: Analyze your forklift’s maintenance history to uncover unplanned breakdown patterns. How often does it undergo repairs for a particular issue? How frequently was it serviced in the past year? In addition, consult with the machine operators who use the forklifts in question.
- Operating Environment: Did you know that forklifts used in challenging work environments require more frequent servicing? Examples include chemical plants, recycling facilities, and food processing plants, among others.
- Usage Hours: Again, consider how many hours your team uses your vehicles per week. The more hours they run above manufacturer averages, the more in between TLC they require.
- Fuel Type: Electric forklifts require less frequent PM compared to internal combustion forklifts because they have fewer moving parts than their complex counterparts.
With that said, take care not to continue performing preventive maintenance past your machine’s useful life. Just because a forklift is operable, doesn’t mean it’s worth maintaining! Track your PM costs to ensure it makes sense to continue upkeep as opposed to replacing it.
2. Familiarize Yourself with Common Issues
Next, familiarize yourself with the equipment issues most likely to affect your forklifts. Before operating, machine operators should run through inspection checklists to ensure everything is working as it should.
Use a mobile computerized maintenance management system (CMMS) like MaintainX to create a digital standard operating procedure like the one shown below:
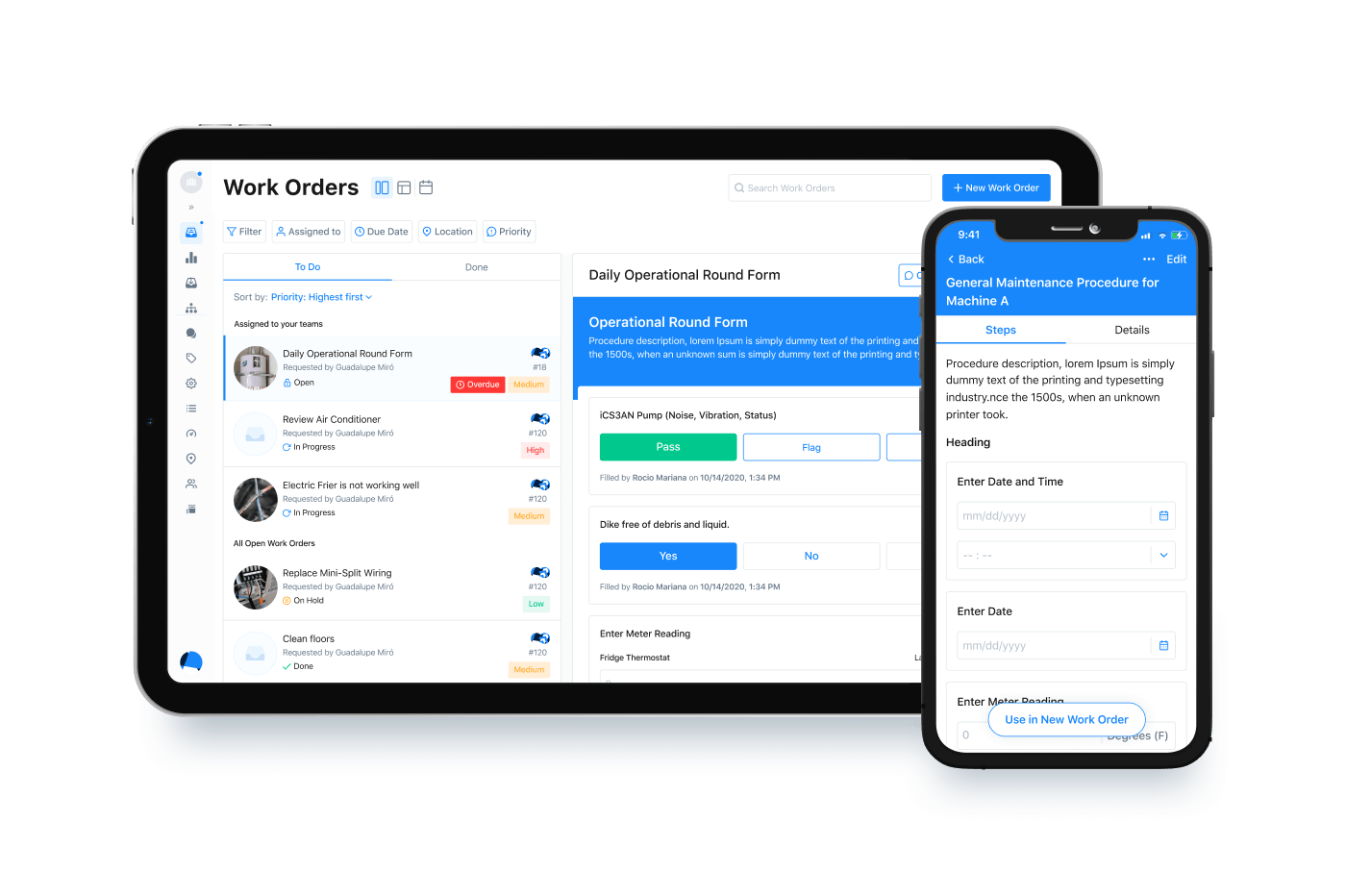
A general forklift maintenance procedure will include the following checkboxes:
- Faulty brakes, turn signals, accelerator, and parking brake
- Rusty, cracked, bent, or worn-out forks and mast
- Low battery charge levels for electric forklifts
- Cracked or damaged hydraulic lines
- Scarred or pitted lift cylinders
- Unresponsive steering wheel
- Components filled with debris
- Deflated and damaged tires
- Malfunctioning seat belt
- Loose nuts and bolts
- Oil leaks
Remember to encourage workers to catalog forklifts as “inoperable” upon finding any issue, no matter how small!
Click here to download MaintainX’s general forklift daily maintenance checklist—it’s FREE.
3. Grease Forklifts Regularly
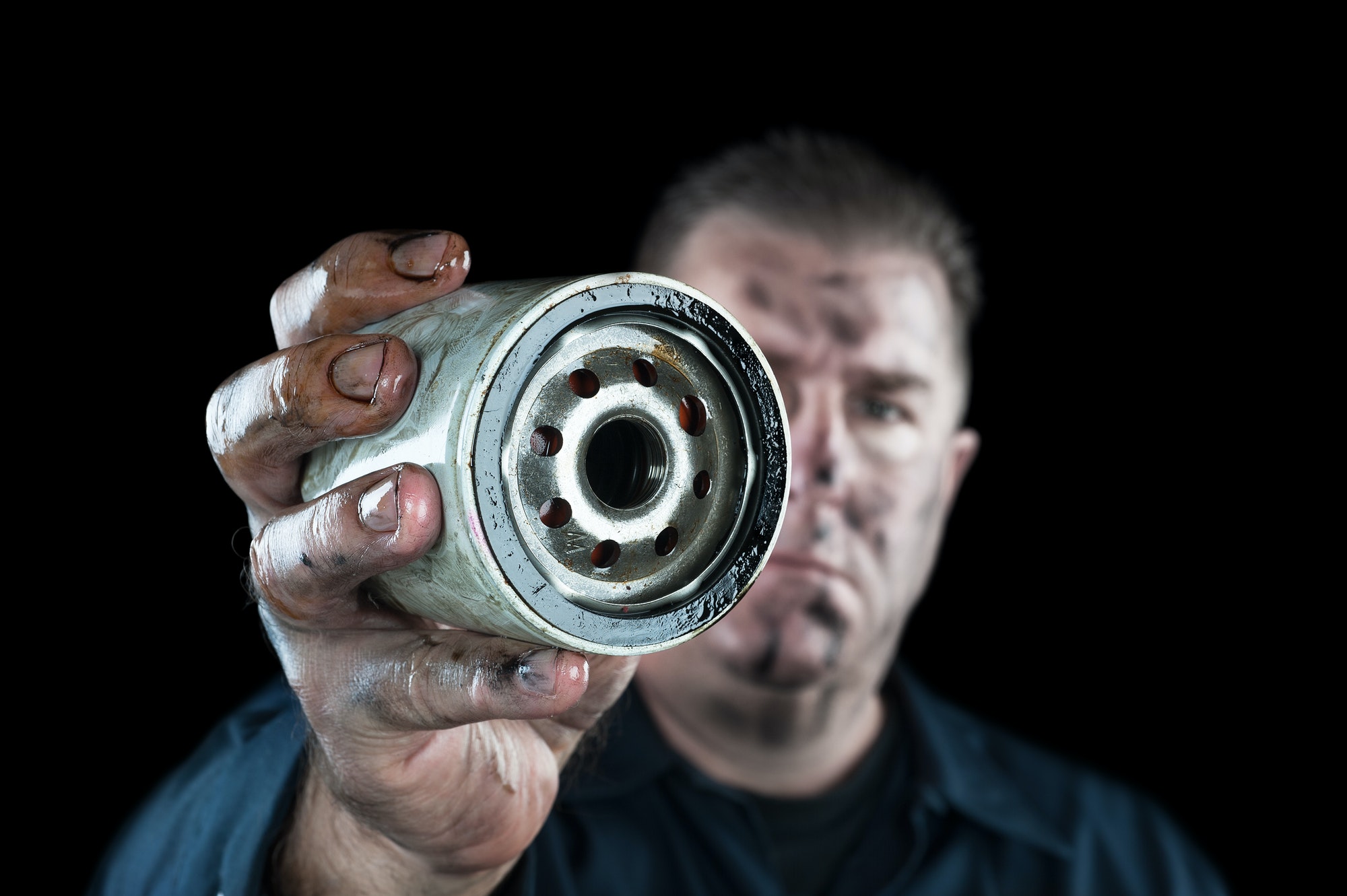
In addition to conducting daily inspections for common issues, prioritize the regular greasing of facility forklifts. Grease your forklifts once a week to reduce friction between moving parts.
Forklift Parts to Grease:
- Steering linkage and kingpins
- Steer-axle mount pivot pins
- Upperside shift bushings
- U-joints and slip yoke
- Lower bearings
- Chain pulleys
- Forks
- Wheels
Not only will this small action increase your forklifts’ lifespans, but it will most certainly minimize downtime!
4. Conduct Due Diligence on Forklift Expenses
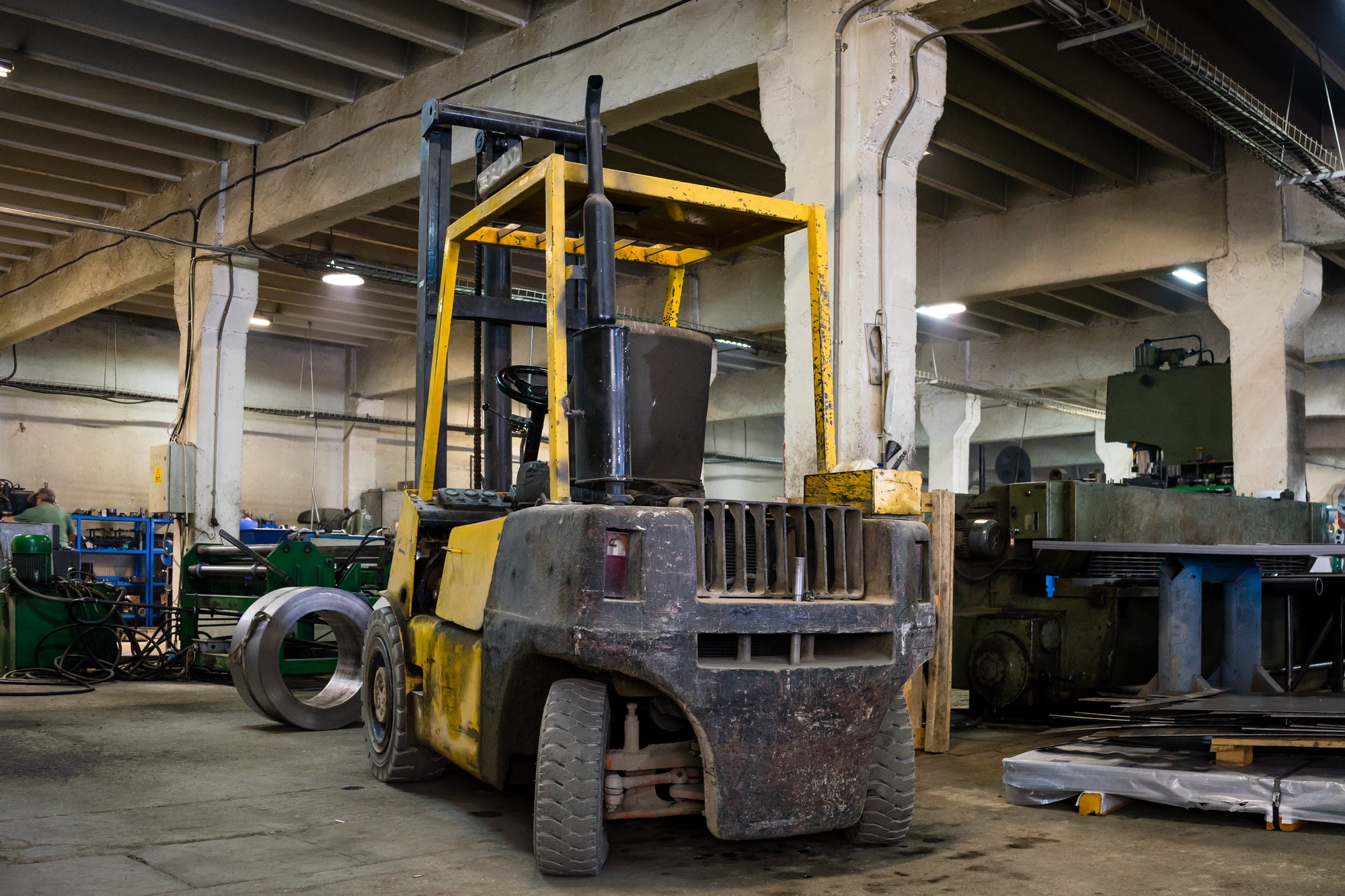
As mentioned above, several actors impact ideal forklift servicing intervals. This means that the cost of maintaining these high-dollar machines can vary substantially from one organization to the next. Maintenance costs also tend to be higher for older forklifts than for newer ones.
With that said, it’s good to form a rough estimate of how much you expect to spend maintaining your forklift per quarter. This information will enable you to develop a more accurate O&M budget. It will also help determine when to replace your machinery for the greatest long-term cost savings. This brings up a common question:
How Much Does Forklift Maintenance Cost?
According to Atlas Toyota, the average cost of maintaining a forklift during its first year of usage is 48 cents per hour. This estimate assumes the vehicle operates for 1500 hours annually and receives recommended PM eight times that year.
The estimate also assumes that replacement parts are covered under warranty so you only pay the cost of labor. During the second year, expect maintenance costs to increase to $1.48 per hour. Manufacturers often recommend more complex maintenance procedures and the replacement of key components at this time.
What Is the Cost of a Forklift?
According to the Forklift Pro, a brand-new forklift can cost between $15,000 and $100,000. The following factors usually influence the cost:
- Manufacturer and brand
- Maximum lift height
- Weight capacity
- Fuel type: electric or internal combustion forklift
- Operating costs, such as type of engine, heavy-duty lifting, etc,
- Attachments and accessories
New Forklifts vs. Used Forklifts
Used forklifts, on the other hand, usually cost about half as much as new ones. Despite being cheaper than new forklifts, facilities are sometimes hesitant about purchasing used equipment. As outlined by MidColumbia Forklift, there are instances when buying used is the better deal, including when:
- You want a specific forklift style your operators are already accustomed to using
- An authorized original equipment manufacturer (OEM) can offer a better deal
- You have a sudden need for a forklift
Of course, nothing beats the certainty of purchasing a new vehicle from a quality standpoint.
5. Operate Your Forklift Efficiently and Safely
Forklift maintenance begins with proper handling skills. No matter how much preventive maintenance you perform, frequently misused machines will break down.
In addition, requiring your team to know what they’re doing is just plain smart. According to Injury Facts, 79 percent of workers were involved in fatal forklift accidents in 2019. Unfortunately, many of these incidents could have been avoided had the machine operators engaged in recommended protocols.
Every effective forklift preventive maintenance program should begin and end with enforcing compliance with forklift safety procedures.
Click here to read: How to Operate a Forklift Safely.
Streamline Forklift Maintenance with MaintainX
As previously mentioned, forklifts are a huge business investment! Follow the aforementioned tips to keep your forklifts running properly for as long as possible.
In addition, we recommend using a computerized maintenance management system (CMMS) like MaintainX to track forklift operating hours, maintenance history, and pending work orders. The best part? You may not have to reinvent the wheel when creating your PM checklists.
MaintainX’s Global Procedure Library includes thousands of downloadable templates free of charge. Click here to download our general forklift daily maintenance checklist.
FAQs
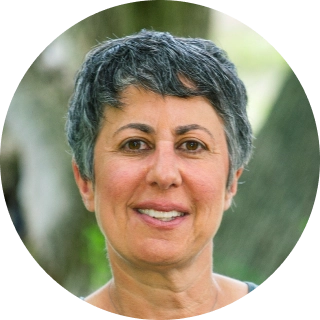
Caroline Eisner is a writer and editor with experience across the profit and nonprofit sectors, government, education, and financial organizations. She has held leadership positions in K16 institutions and has led large-scale digital projects, interactive websites, and a business writing consultancy.