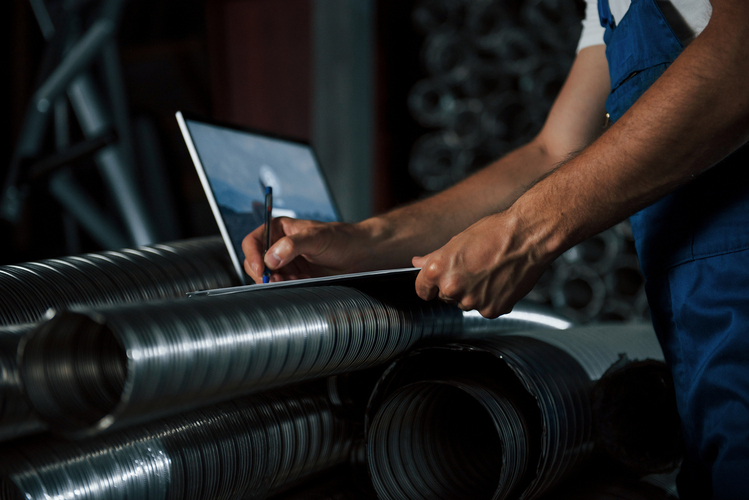
The best way to improve maintenance efficiency is to use facility preventive maintenance checklists and work order software programs. In this article, we’ll review what steps to take before creating procedures, how to make checklist templates, and what items to include. We’ll also run through preventive maintenance (PM) basics.
The average American spends a lot of time indoors. Throughout the day, we walk in and out of office buildings, educational facilities, and public buildings before returning home. Of course, if facility managers succeed, we’re none the wiser.
However, the minute an HVAC unit breaks down in mid-July, our facility manager might just become our best friend. But top-notch facility managers do more than change lightbulbs, clean floors, and respond to equipment breakdowns. They also help organizational leaders maximize asset longevity, enforce safety regulations, enhance energy efficiency, and potentially save millions.
Facility Preventive Maintenance
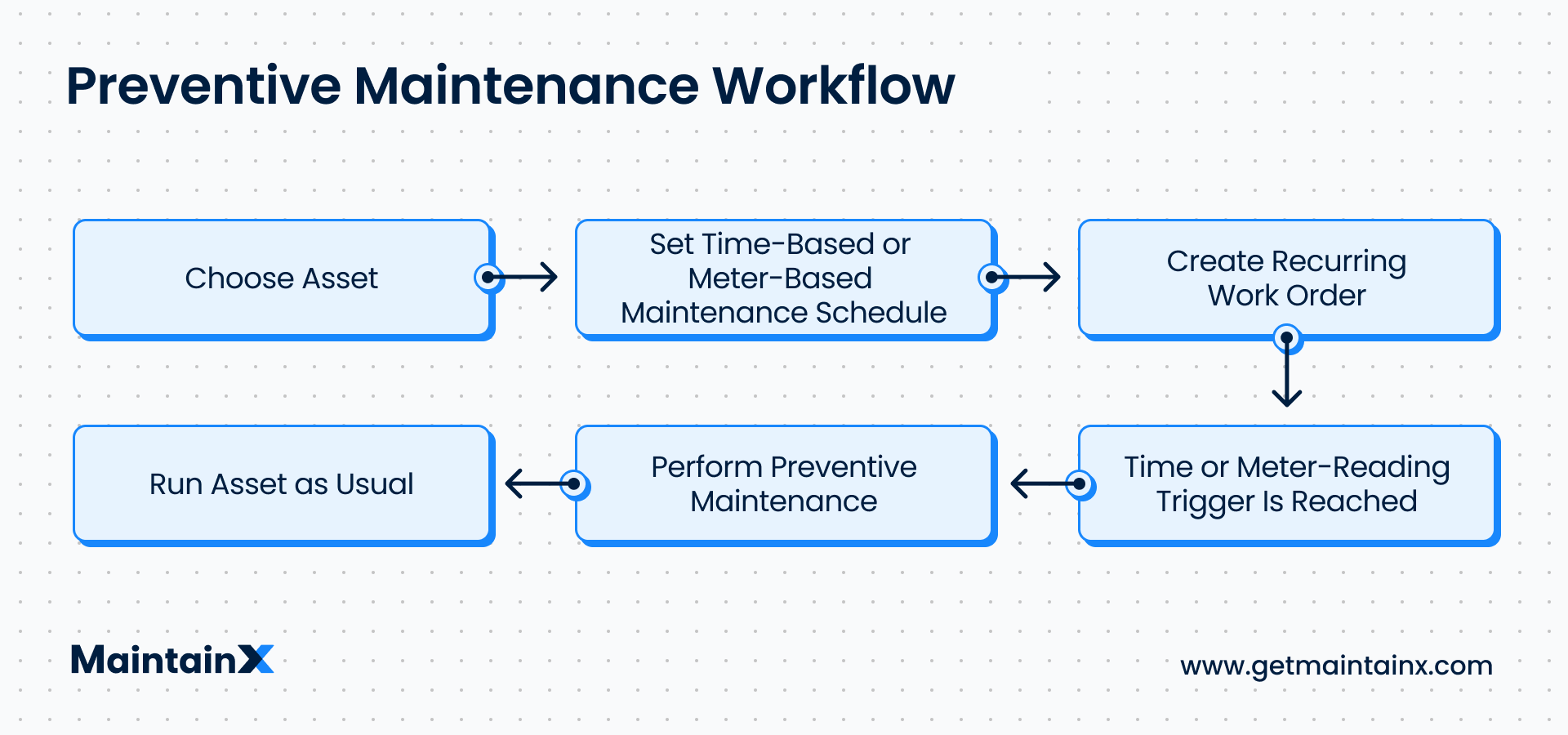
Facility preventive maintenance is the practice of predicting and preventing equipment failure before it happens. Also called planned maintenance, this upkeep method requires facility technicians to conduct routine inspections and care for assets to ensure uninterrupted reliability. Operational managers often use facility preventive maintenance checklists to ensure technicians correctly care for important assets.
Unlike reactive maintenance, preventive maintenance doesn’t involve waiting for inconveniences; instead, it enforces the scheduling of preventive care based on the manufacturer’s guidelines, historical data, and usage data.
The result? Controllable maintenance costs that won’t catch you by surprise!
“In most industries, the cost of maintenance is between 10 and 25 percent of total operating costs. Maintenance efficiency is an important factor in this as typically more than half the cost is labor. Improving maintenance efficiency has a positive impact on reliability—so companies can cut costs without risking performance.”
McKinsey
Four Categories of Facility PM
Four Categories of Facility Preventive Maintenance can be divided into four categories: inspection, detection, correction, and prevention. Here’s a summary of what each step entails:
Inspection
Facility inspections happen for two reasons: to ensure assets are safe to use and to keep equipment operating at optimal performance levels for as long as possible. Routine checks reduce the likelihood of accidents in the workplace and provide greater liability protection. Inspections can happen daily, weekly, monthly, or annually.
Detection
While a team member is changing a part or conducting a general inspection, they may notice an unanticipated issue. Instead of the hidden problem taking everyone by surprise a few months down the line, the technician will report the issue to management.
Correction
Once the issue has been reported in the form of a maintenance request, the facility manager can assign the new work order. This will remedy the problem before it worsens or causes a total shutdown.
Prevention
The more inspection records and maintenance notes you acquire, the more you can improve your PM scheduling and prevent future equipment hiccups.
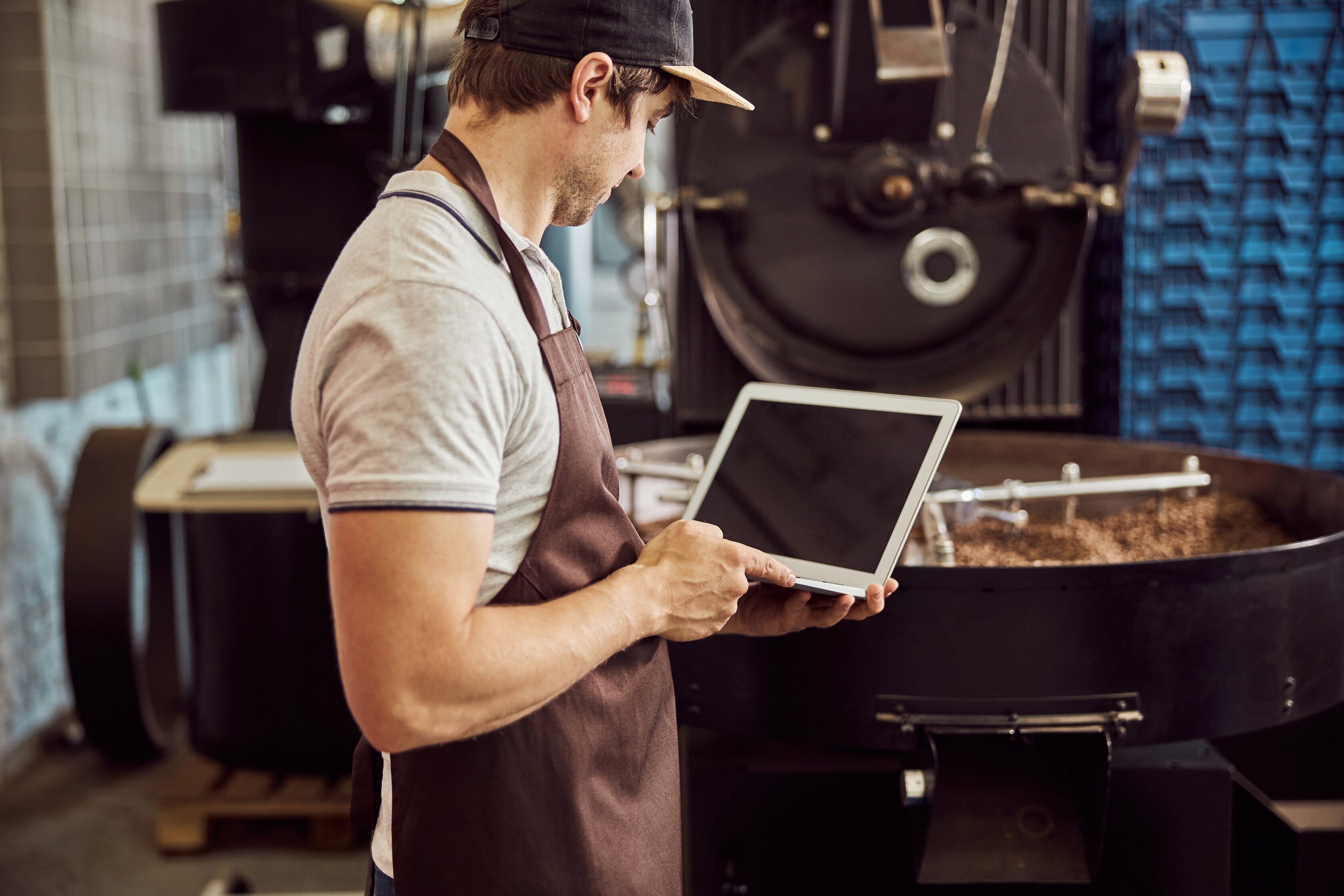
It’s worth mentioning that not all facility systems should be included in a PM program. Managers should only include the most critical asset systems in which they deem preventive maintenance more cost-effective on a life-cycle basis. Digitizing facility preventive maintenance checklists organizes the process.
Components not included within a PM strategy should remain candidates for “run-to-failure” repair. Generally, this consists of noncritical components that you can repair or replace easily via a quick service visit. Want to learn more about the practice of facility maintenance?
Click here to read Your Guide to Choosing Facility Maintenance Work Order Software.
Benefits of a Facility PM Program
Here’s a summary of what facility management teams can expect to accomplish after implementing strategically planned maintenance programs:
- Decreased equipment downtime
- Decreased number of costly repairs
- Enhanced facility user experience and satisfaction
- Increased staff productivity (less time putting out fires)
- Reduced overtime expenses; more efficient use of staff hours
- Improved safety and reduced risk for occupants and staff
- Increased life expectancy of assets, eliminating the need for replacement
- Increased average ROI of 25 to 300% after one year of implementation
While there are many benefits to implementing a facility preventive maintenance program, the most surprising may be the astronomical amount of money some organizations save within one to five years of implementation. A 2016 study estimated the cost of unplanned downtime across all businesses at $260,000 an hour. While the average is likely skewed by manufacturing facilities with more sophisticated asset investments, no facility should assume they can’t reap savings by curbing premature breakdowns.
As the Federal Facilities Council explains, facility managers who don’t take charge may find themselves stuck in cycles of reactionary fixes, high expenses, and accelerated deterioration
The Role of Work Order Software (CMMS)
Of course, the best way to manage a maintenance and repair program—that your team won’t abandon six months later—is to invest in work order software. The good news is that today’s best programs are scalable, user-friendly, and require no long-term commitments. Some of them even allow maintenance team members to create facility preventive maintenance checklists from the convenience of their smartphones. Even better? They are free to low cost.
According to a McKinsey & Company survey, the strength of an organization’s maintenance strategy is the most reliable indicator of performance. Running an effective maintenance and repair program involves many moving parts, including tracking incoming requests, scheduling tasks, preparing budget estimates, projecting facilities maintenance requirements, determining resource allocations, drafting preventive maintenance checklists, and more.
This is where work order software comes into action. Also referred to as Facility Management Software (FMS), these platforms allow managers to draft, assign, and monitor work orders; maintain asset backlogs; accept maintenance requests from occupants; control inventory; and improve organizational efficiency.
The most commonly used alternatives to FMS are spreadsheets, whiteboards, and paper stacks. Even now, a surprising number of facility management teams still rely on outdated facility management methods.
Conveniently, modern cloud-based software has evened the playing field for companies of all sizes. Today’s task management apps are more affordable, secure, and easier to use than ever. Monthly small business plans range from $10 to $150 per user, depending on the provider.
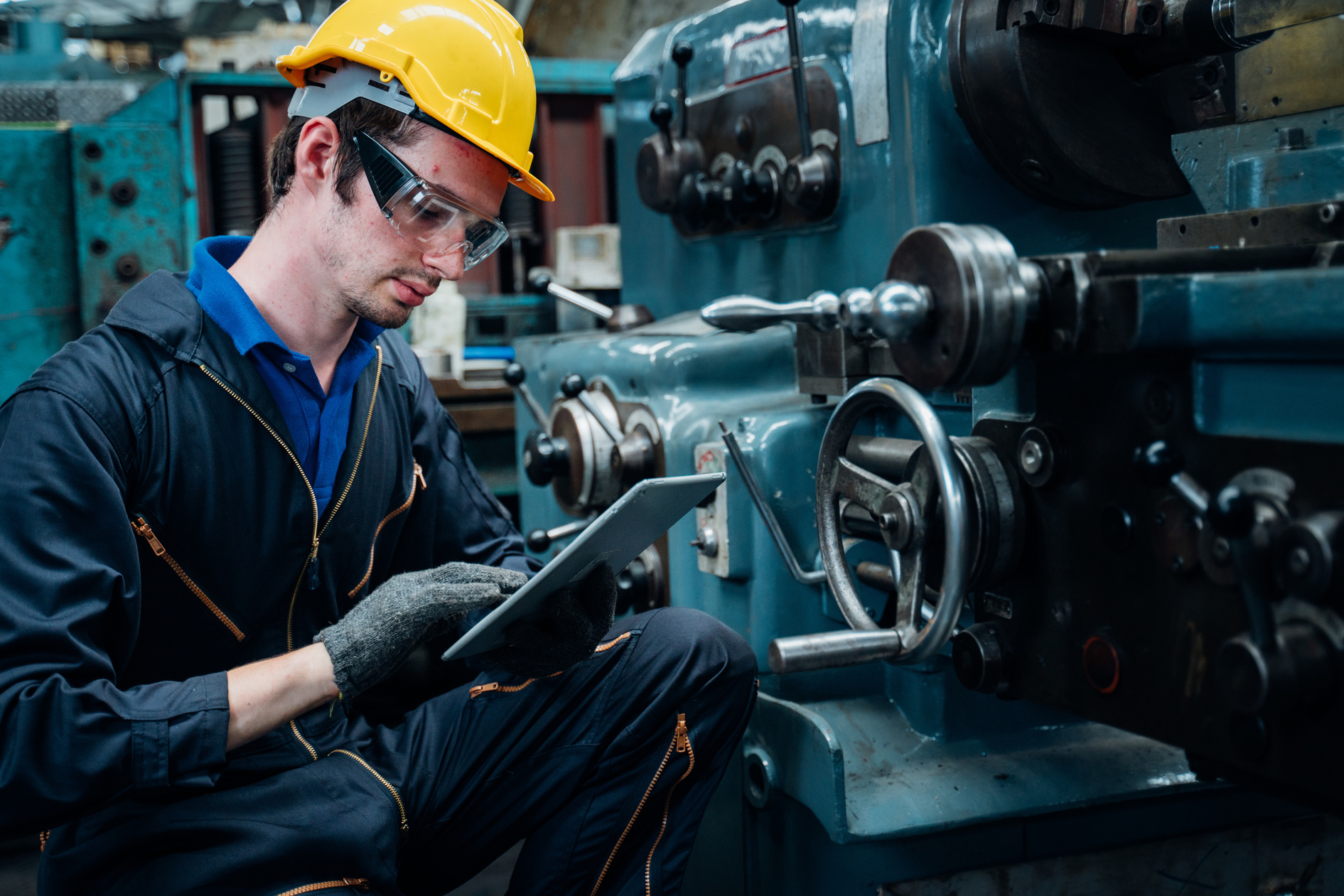
Organize an Asset Database
Before you begin creating facility preventive maintenance checklists, you need to know which assets are under your care. Successful preventive maintenance programs are dependent on maintaining up-to-date inventories of facility assets. How else will you keep track of which recommended maintenance tasks your teams should complete and by when?
Use a simple spreadsheet or FMS platform to document the following information about each asset under your care:
- Name
- Serial number
- Manufacturer
- Barcode
- Location
- Category
- Notes
Do we really need to track everything?
The answer is no, you only need to list equipment that would cause extreme duress in the event of a breakdown. Collecting this information will help you determine how assets are serving your facilities over time. Smaller organizations may want to track anything under $500 in value, while larger companies may prefer tracking anything over $5,000.
Once you have a working inventory list, you’re ready to assess particular maintenance and replacement requirements. You can find this information in the manufacturer’s guidelines. A good FMS platform will cross-reference your asset database with your preventive maintenance scheduling. Not only does this feature streamline the facility management process, but it also provides insightful analytics that promote more cost-effective decision-making.
Want to read more about tracking facilities assets?
Click here to read The 20 Most Common Types of Assets Facilities Management Must Track
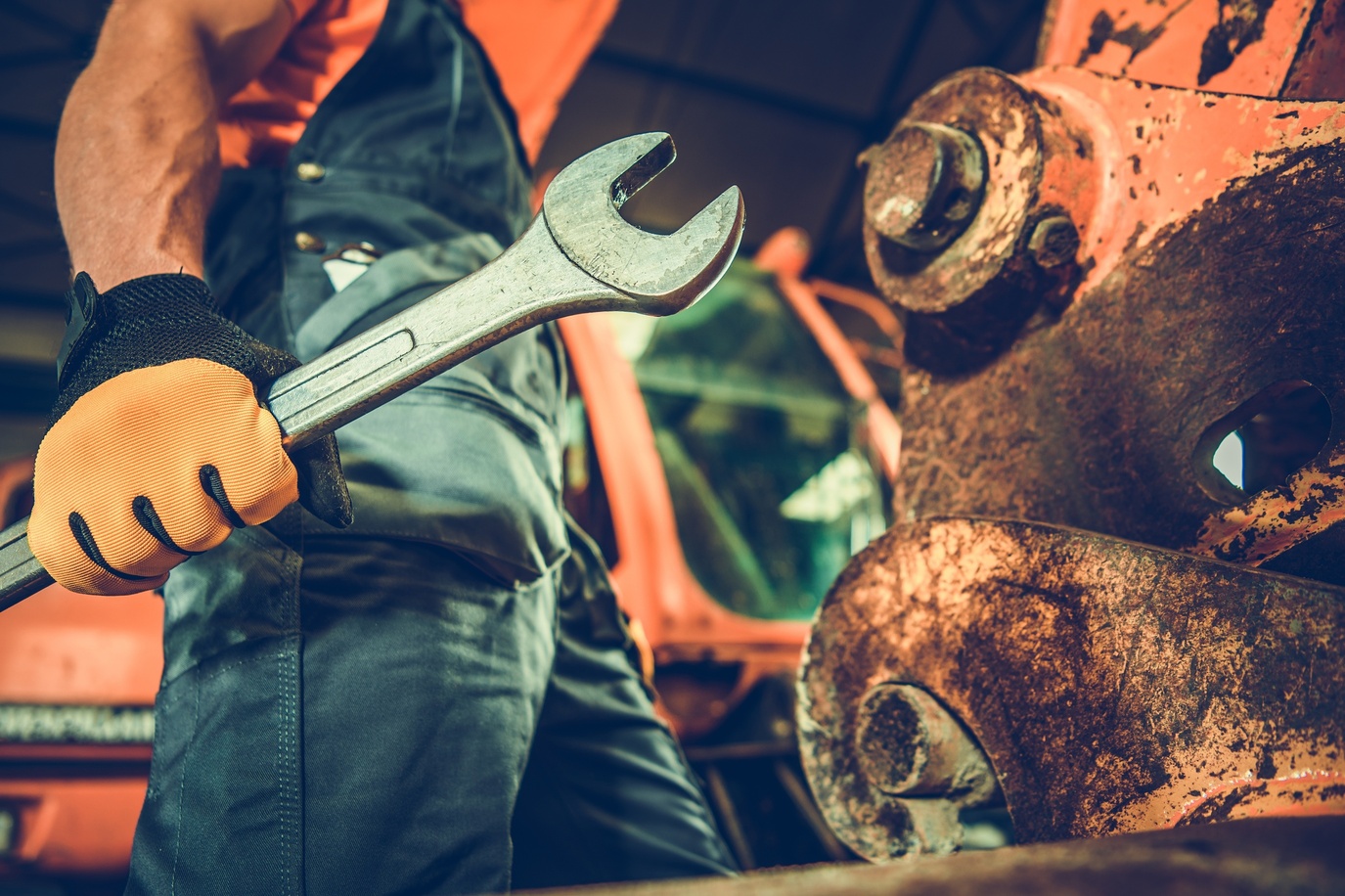
Build Facilities Preventive Maintenance Checklists
Obviously, no two facilities are completely alike. You might manage a commercial office, a plant, or a government building. Each of these properties will have overlapping needs, while simultaneously requiring distinct PM checklists. However, you can break most facilities’ PM checklists into these zones:
- Roofing
- Lawn Maintenance
- Building Exterior
- Building Interior
- Plumbing
- HVAC
- Electrical
- Lighting
Create a separate checklist for each category, including additional ones for safety and maintenance supplies. Though it may seem like a lot of upfront work, taking the time to draft thorough facility preventive maintenance checklists will pay big dividends in the long run. Remember, you want to avoid the costs of emergency repairs, replacements, and lost productivity due to downtime!
The best way to structure checklists is with the help of subheadings. Break down complex tasks into multi-step processes that are easy to follow. And don’t be afraid to integrate photographs, color codes, and attached procedures to break up the redundancy of long pages (more on that in a moment). These elements will make your facility’s preventive maintenance checklists more reader-friendly.
Industry PM Checklists
General Building and Interior
- Mark all exits clearly and add additional signage if complicated.
- Test smoke and carbon monoxide detectors and change batteries yearly.
- Check condition of floors, ceilings, and walls.
- Check for leaks or water damage in bathrooms and ceilings.
- Check that doors lock and unlock easily.
- Ensure stairs and railings are not loose.
- Check that lights are working, replacing bulbs as needed.
- Conduct routine pest inspections and treatments.
Building Exterior
- Walk the perimeter.
- Check condition of sidewalks and parking lots for potholes.
- Check condition of windows.
- Clean debris from roof and gutters.
- Clean up any trash or debris on building grounds.
- Monitor condition of exterior paint and siding.
- Check decks and patios for rot or loose railings.
Electrical
- Clean and re-torque electrical connections.
- Make sure electrical panel is accessible.
- Check wiring periodically and remove any fire hazards.
- Replace fuses as needed. Include extra fuses in supplies.
- Make sure meters are clean and well-lit.
- Check if automatic and manual switches are operating properly.
- Inspect electrical connections and boxes for overheating.
- Test outlets for proper operation.
- Ensure batteries work in flashlights and smoke and carbon monoxide detectors, and test instruments work properly.
- Check condition of cover plates for cracks and proper tightness.
- Ensure exhaust fans are clean and functioning properly.
- Clean and lubricate overcurrent devices as needed.
- Check all fusible switch units to make sure that all fuses are from the same manufacturer and are of the same class and rating.
*A licensed electrician should execute a proper inspection of your electrical systems every 3 to 5 years.
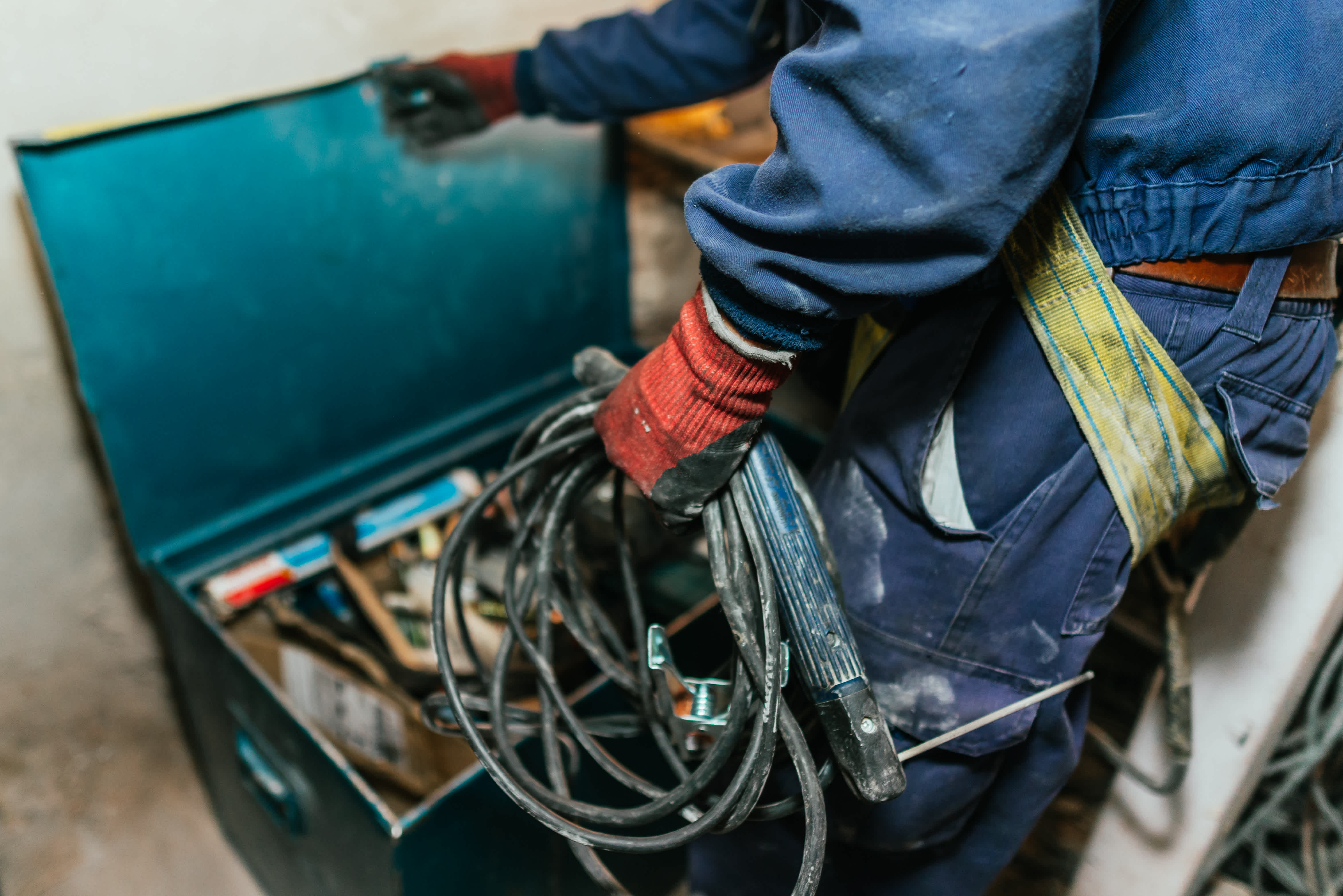
Plumbing
- Inspect all plumbing for any leaks or unusual noises at least once a year.
- Apply bearing lubrication once a year on domestic water booster and circulation pump systems.
- Fire-test water heaters and boilers periodically.
- Lubricate condenser fan motor bearings of drinking water chillers. Make sure oil in compressor oil reservoir is drained and replaced.
- Check sump and sewage ejection pumps. Replace as needed. Lubricate exposed pumps at least once a year.
- Make sure adequate hot and cold running water is available in all sinks and tubs.
- Check drain connections to sanitary sewer.
- Install backflow devices when necessary, such as with handheld showerheads.
- Make sure low-water shut-off is functioning properly.
- Make sure sink traps and building traps are clean to prevent slow drainage.
HVAC
- Clean air intake when necessary.
- Change air filters monthly or bi-annually.
- Check for excessive noise or vibration when blower motors are running.
- Check if condensate drain pans are draining properly.
- Ensure motors and ductwork are clean.
- Check flexible duct connectors for cracks and leaks.
- Check screws, latches, and gaskets in need of repair or replacement.
- Check pumps; bearings must be lubricated once a year.
- Inspect condition of all electrical hardware as well as connections.
- Make sure safety controls and equipment are working properly.
- Make sure all guards and access panels remain secure.
- Check operation of interior and exterior units.
- Clean damper operators.
- Ensure any mineral buildup inside water heater is minimized.
- Drain boiler to remove any accumulated sediment.
- Clean or replace boiler’s oil filter once a month.
- Ensure thermostat is calibrated correctly.
Safety
- Ensure fire extinguishers are present where required.
- Ensure fire escapes and stairs are free of obstructions.
- Ensure chemicals are disposed of according to the instructions.
- Ensure chemical products are sealed, clearly labeled, and stored.
- Determine if first-aid kits are well-stocked.
- Ensure safety signs and equipment labels are visible and in good condition.
- Check and clean respirators.
- Check smoke and carbon monoxide detectors.
- Check fire alarm system.
- Check condition of fire escapes.
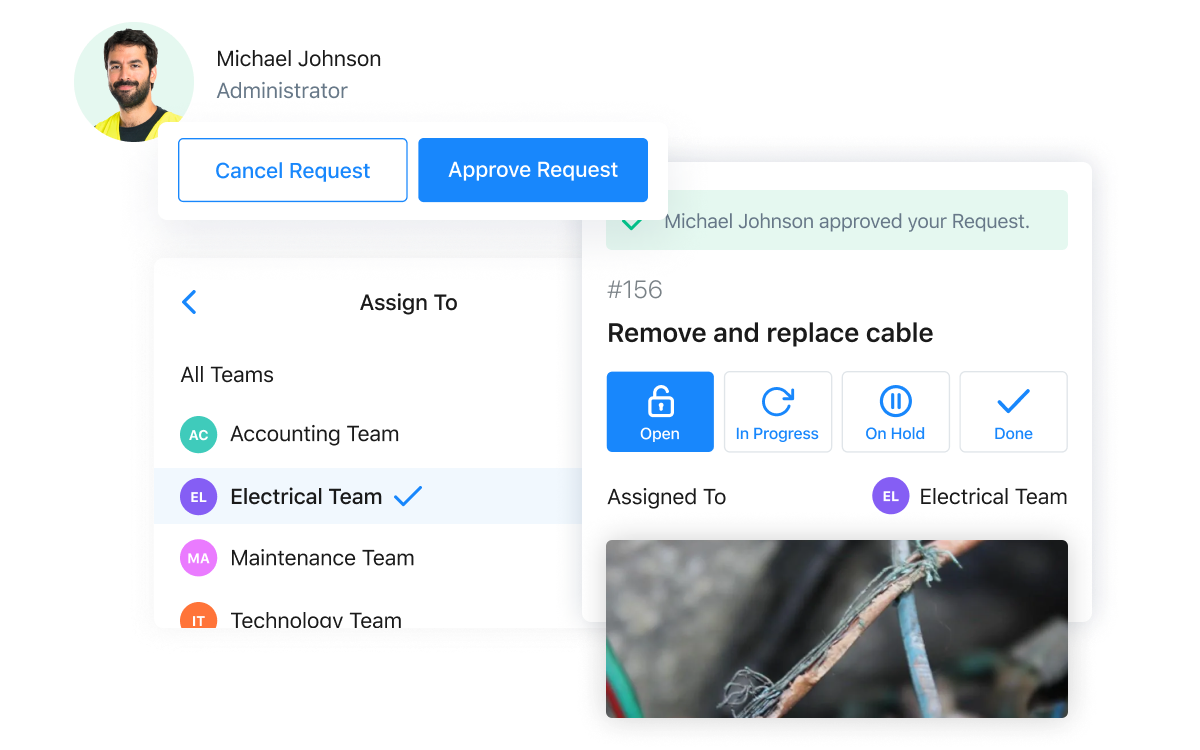
Facility PM Checklists Templates
Once you’re finished mapping out your facility’s preventive maintenance checklists, it’s time to digitize them. We recommend downloading MaintainX for this step because it’s fast, free, and user-friendly. It’s available for use on desktops, smartphones, and tablets.
Also, another great benefit of using MaintainX to create your digital facility’s preventive maintenance checklists? MaintainX comes with advanced reporting features that allow managers to maintain audit trails of who has worked on which checklists, for how long, and how much money was spent on PM.
Create a PM Accountability System
Once you have finished drafting your checklists, you’ll want to create an accountability system to ensure team members follow through. Obviously, the best way to ensure work orders are completed is with clear communication.
While paper sign-offs work for smaller companies, they often get lost in the hustle and bustle of medium- and large-sized facilities. Workflows that involve updating spreadsheets with checklist sign-offs hours after completion make it difficult for management to identify outstanding requests at any given moment.
This is yet another instance where software comes in handy. Most platforms automatically create timestamps of completion after technicians mark work orders as “closed.” And if someone notices an unforeseen maintenance issue, they can quickly create a new request in real-time.
MaintainX is the only app that takes maintenance communication a step further by providing integrated chat functionality. Team members can instant message one another within individual work orders and in separate chat threads. This allows both facility managers and employees to keep one another in the loop while maintaining easily retrievable communication references.
Task Management
Remember, these are general facility preventive maintenance guidelines. Your individual facility will necessitate unique checklists based on your asset inventory. Once you’re finished designing your facility maintenance checklists, it’s time to schedule and assign them to team members.
Depending on the assets at hand, your checklists could be daily, weekly, monthly, or yearly. Preventive maintenance can be scheduled using a time-based approach, a usage-based approach, or a combination of both. High-tech facilities also invest in sensor technology that provides suggested maintenance actions based on individual asset history and moment-by-moment behavior.
Again, task management platforms can simplify the process with features that support recurring scheduling, worker assignment, and asset management integration. You can also upload and store important documentation for easy retrieval, such as O&M manuals, OSHA guidelines, warranty information, and receipts.
Digitize Your Facilities Preventive Maintenance Checklists
Drafting your initial checklists may seem daunting, but it’s a worthwhile pursuit. The advantages of consistent preventive maintenance include reduced costs, increased productivity, and greater occupant satisfaction.
With MaintainX, you can instantly see which work orders have been completed, which ones are in progress, and if any work orders are overdue. The app also shows who worked on what, providing a complete accountability trail.
The best part about a CMMS platform like MaintainX is that field technicians can update work orders and asset entries themselves, according to user permissions. MaintainX is one of the world’s only task management platforms designed for smartphone and desktop integration. Put simply, it just makes work easier.
The right software can help you save your favorite work order templates, import asset spreadsheets, and track work orders without missing a beat. MaintainX is the world’s first task-management platform designed with real-time chat. Our app provides seamless integration between smartphones, tablets, and desktop computers.
“We were trying to manage 140 pieces of equipment across seven locations using spreadsheets, emails, and text messages, and that just wasn’t getting it done,” says Mike Moody, maintenance manager. “MaintainX is the perfect tool to prevent issues from falling between the cracks.”
Are you ready to experience the MaintainX difference? Create an unlimited number of facility preventive maintenance checklists using our freemium plan.
FAQs
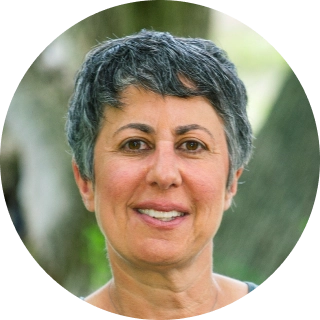
Caroline Eisner is a writer and editor with experience across the profit and nonprofit sectors, government, education, and financial organizations. She has held leadership positions in K16 institutions and has led large-scale digital projects, interactive websites, and a business writing consultancy.