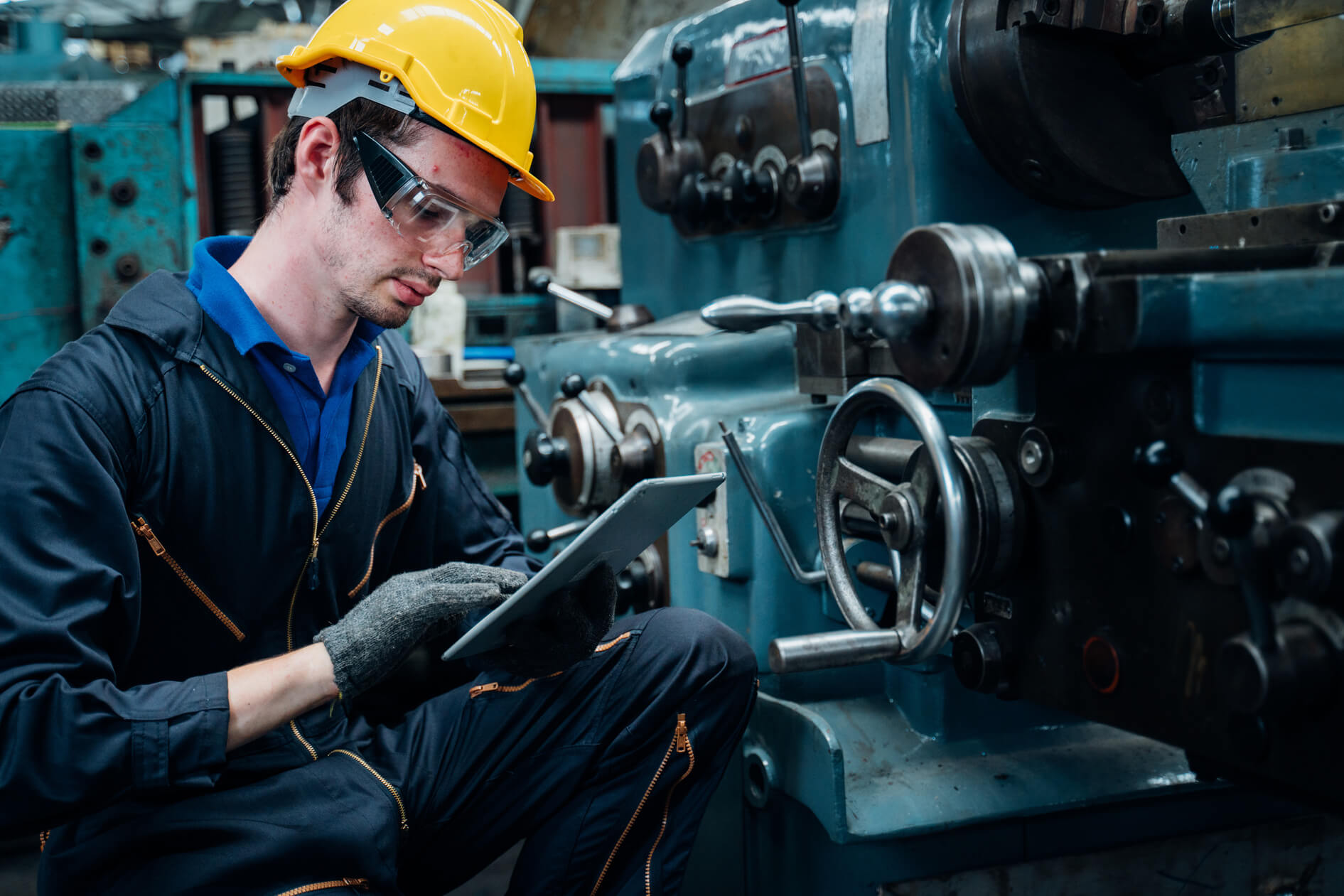
There is a lot of discussion across industries and platforms about increasing production and maintenance efficiency in manufacturing.
It should come as no surprise that nowadays production efficiency involves the smart integration and automation of new technologies, machining centers (CNCs), and the Internet of Things (IoT).
Integrating Manufacturing Maintenance Efficiency Strategies
With the complexity of global production today, organizations are turning to new digital solutions to keep pace with today’s swift-moving and changing environments to meet customers’ demands.
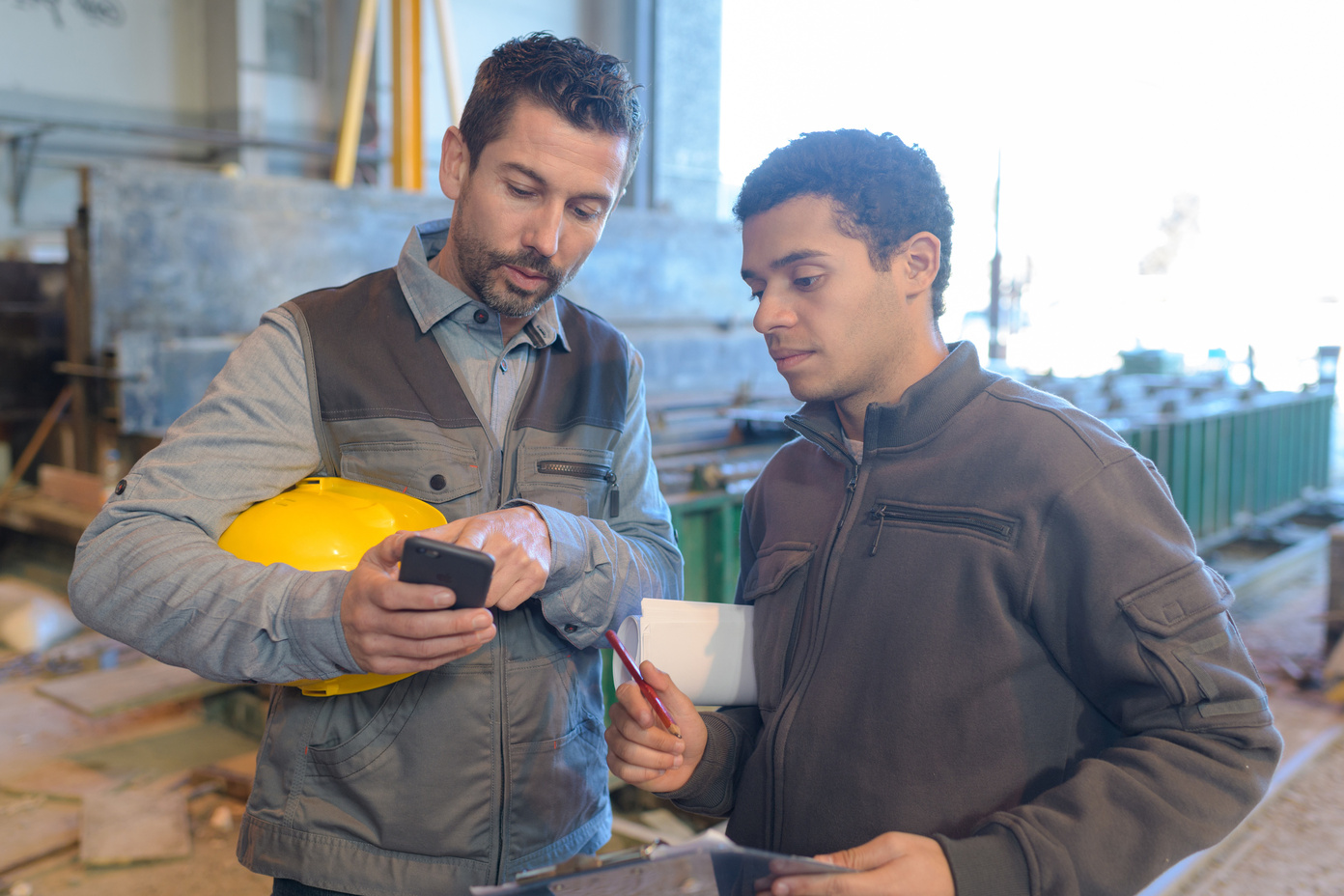
A maintenance strategy is a systematic approach to maintaining assets in prime working condition for efficient production. Asset Condition monitoring involves equipment maintenance checks, data analysis—of KPIs, failure rates, performance, and costs—and the repair or replacement of faulty equipment.
High-level maintenance programs typically mix several different maintenance strategies based on the needs of individual equipment.
However, managers often adapt manufacturing industry maintenance strategies for equipment to meet unique needs, goals, and budgetary constraints.
Cost Effective Manufacturing Maintenance
The optimal balance between costs and asset performance and what is most cost effective is, therefore, different for each company.
However, in many cases, shifting from reactive or corrective maintenance to preventive maintenance can improve the ratio between the two elements.
Evaluate every aspect of your production line. Pay special attention to measuring throughput—the average number of units your company produces in a given period. This measurement will highlight any issues you have with specific machines.
Another essential metric to review is your capacity utilization. This measurement involves calculating the capacity of your total manufacturing output per factory at any given moment.
Analyzing capacity utilization allows you to see which production lines are operating at their highest possible output.
Both metrics illustrate precisely how costly equipment downtime can be and why increasing maintenance efficiency is crucial.
For example, if the standard output rate is $500,000 worth of widgets every hour, the difference between a maintenance mechanic taking 15 minutes to repair a broken conveyor belt versus 30 minutes is critical. The difference could cost your company $125,000.
Implementing Preventive Maintenance with CMMS
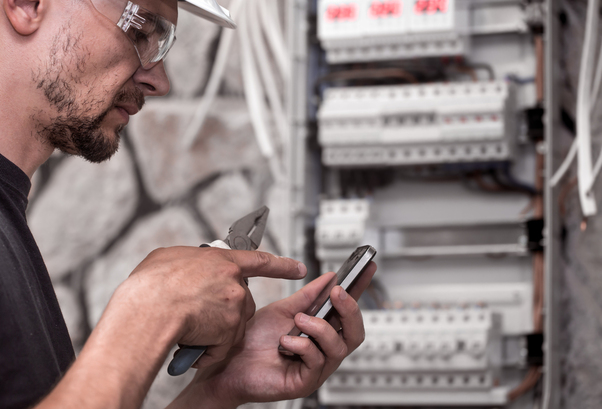
Preventive maintenance helps organizations increase maintenance efficiency by reducing unplanned downtimes, increasing asset reliability, minimizing maintenance costs, and improving manufacturing operations. While launching a preventive maintenance program may seem complicated, it is simple if you effectively plan for it.
Studies suggest manufacturing companies can save an average of 12 to 18 percent in costs by investing in preventive maintenance (PM). Facilities that are entirely reliant on reactive maintenance can save even more. In other words, every dollar spent on preventive maintenance will save nearly five dollars on expenses. Common Preventive Maintenance
Preventive maintenance minimizes equipment downtime, improves asset lifespans, and lowers maintenance costs. It is a simple, direct, and systematic way to improve asset reliability.
The most common preventive maintenance tasks include:
- Inspections
- Cleaning
- Lubrication
- Adjustments
PM tasks are performed regularly to reduce the likelihood of failure throughout an asset’s normal operating conditions. Operational and maintenance managers schedule PM tasks according to manufacturer recommendations, average asset life cycles, or historical behavior patterns.
Types of Preventive Maintenance (PM)
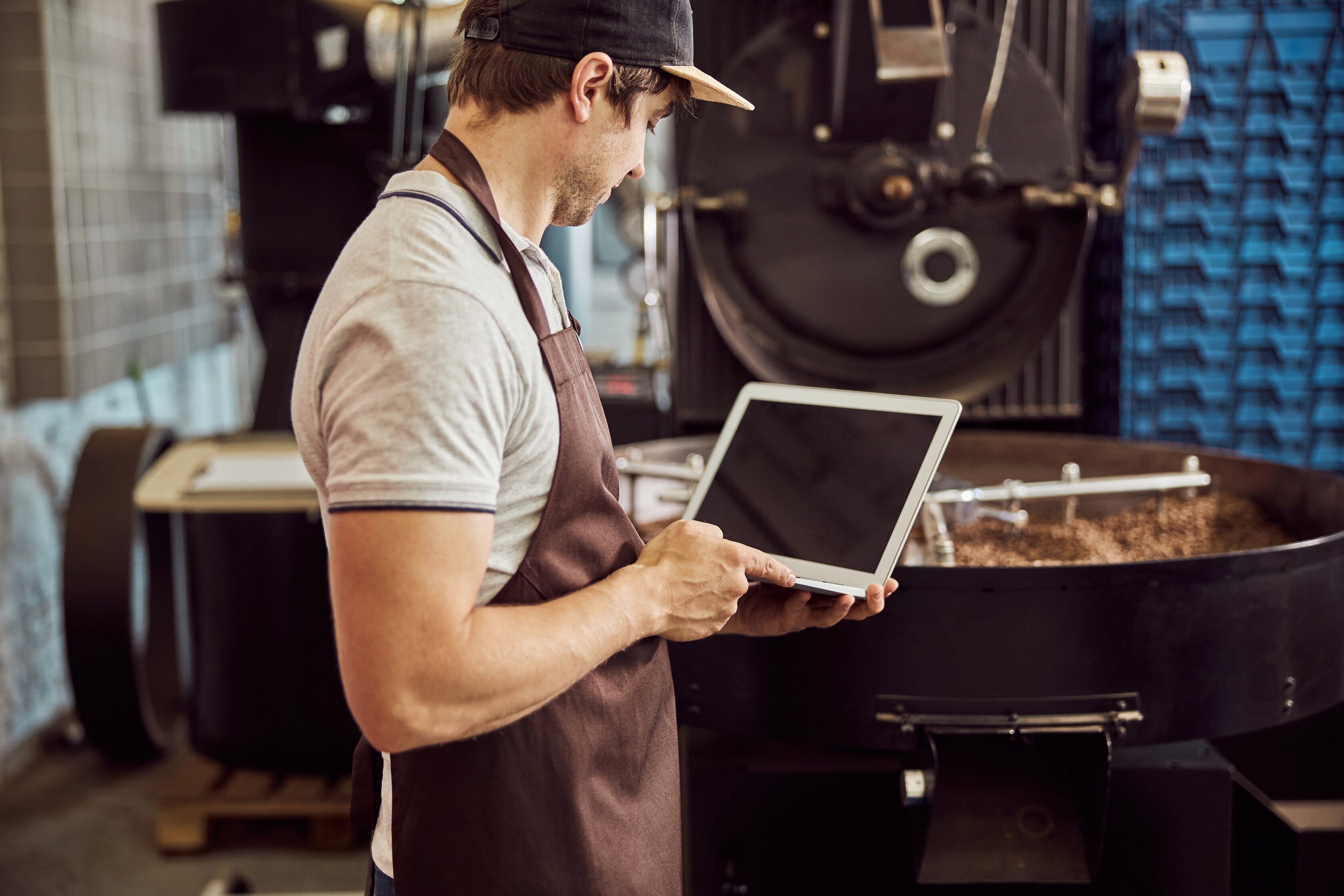
Preventive maintenance tasks that promote maintenance efficiency reduce unplanned downtime. Maintenance tasks generally fall into four broad categories.
Periodic maintenance includes preventive maintenance tasks performed at scheduled intervals. They can be performed weekly, monthly, quarterly, or annually. For example, you can change your engine oil every three months. Equipment manuals usually contain the recommended maintenance schedules for an asset.
Periodic maintenance also is referred to as time-based maintenance.
Meter-Based maintenance, also known as performance-based maintenance, maintenance scheduling is based on equipment usage variables. Such assets usually have meters or counters to measure usage milestones. An example of meter-based maintenance is changing the engine oil every 3,000 miles.
Predictive Maintenance (PdM) is an advanced form of PM that uses sensor devices and data analysis tools to predict the optimal time when assets should receive maintenance to prevent failure. The goal of PdM is to perform maintenance just before failure occurs to eliminate the risk of under-or over-maintenance.
An example of PdM is using vibrational analysis on high-rotating machinery to detect imbalance, misalignment, or bearing wear. A fluctuation in machine vibrations triggers maintenance work.
Prescriptive maintenance is similar to PdM as they both rely on data to make maintenance decisions. However, with prescriptive maintenance, machine-learning software gathers and analyzes equipment conditions to recommend specific maintenance actions. This helps to minimize operational risks and increase overall operational and maintenance efficiency.
For example, sensors or other artificial intelligence (AI) software will recommend adjusting the barometric pressure in a processing tank in the event of a thunderstorm to avoid high pressure in the tank.
Creating SOPs to Increase Maintenance Efficiency
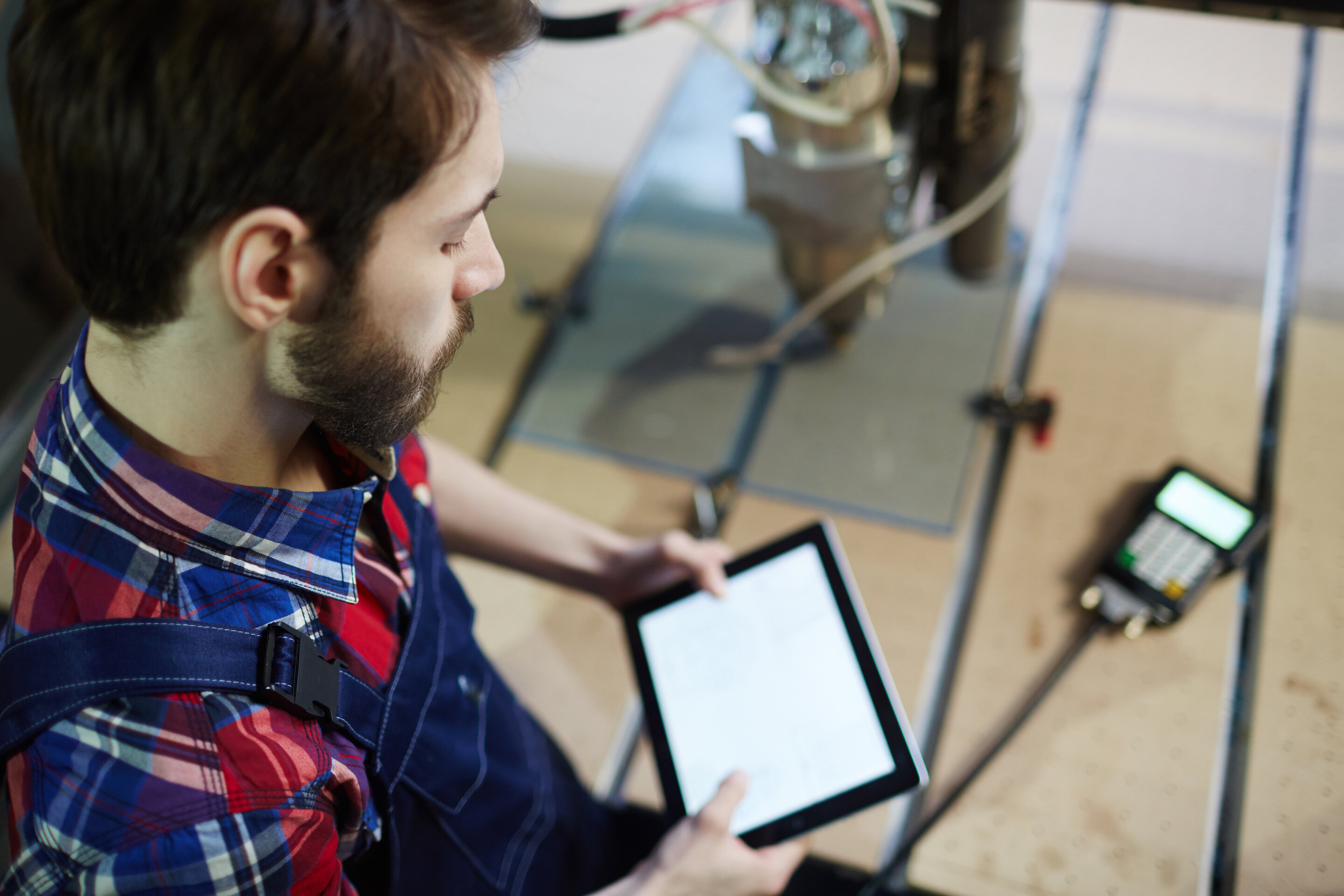
We recommend that organizations create standardized work Instructions to ensure that all processes are timely, consistent, and repeatable. Evidence suggests organizations need to automate their processes to stay competitive.
Standard operating procedures (SOPs) make it easy for employees to reference work instructions, policies, and checklists. Additionally, digitization allows managers to track SOP implementation, quality assurance, and maintenance efforts.
1. Use CMMS for SOP Automation
Digital SOPs make life easier for organizations of all types and sizes. They streamline manufacturing processes, reduce operational and total costs, and provide real-time updates on task completion. Using manufacturing Standard Operating Procedures, managers can standardize preventive maintenance processes and quality assurance plans across teams, facilities, and functions.
From how a new piece of equipment runs to how a manager audits performance, an SOP will always make repeatable processes more efficient.
With digital SOP, management can quantify and organize every process that workers use. It is not only about the shop floor. Automate the SOP for how the front office receives production updates from the floor. Digitize the SOP to alert the warehouse maintenance team that products are ready to ship.
An SOP can even standardize how a team communicates. Streamlining internal communications creates production efficiencies across the company.
2. Automate Repetitive Tasks First
Not sure where to begin? Start by documenting your organization’s most repetitive tasks. Routine, manual tasks provide an easy opportunity for automation to free up time and resources. These tasks may include daily cleaning procedures, routine maintenance tasks, and worker opening/closing processes.
In the end, repetitive tasks should be included in automated workflows.
3. Use Employee Input to Outline Processes
Upon closer look, you may notice that most broad employee assignments contain small steps within them. For this reason, the employees who regularly perform specific procedures should plan, develop, and write the first draft of the SOP. After all, they are the “subject-matter experts” (SMEs), most familiar with the procedures.
The same employee who writes the SOP should then work through the written procedure to make any necessary changes. The writer may need to clarify the text and add graphics to increase clarity and ensure compliance.
Once the initial draft is complete, assign secondary employees and managers to review the SOP. Those familiar with the procedure may notice a missing or complicated step that can be broken into smaller ones. Once an SOP is in final draft form, organizational leaders can review it for quality assurance and make final changes.
An SOP should not be complicated. The simpler it is, the more effective it will be. Write digital SOPs in simple, straightforward, and actionable language that everyone can understand.
When work instructions contain the optimal steps needed to perform a process, companies realize improvements in a variety of areas, including:
- Product consistency
- Product quality
- Operator safety
- Process throughput
Automating Manufacturing Maintenance
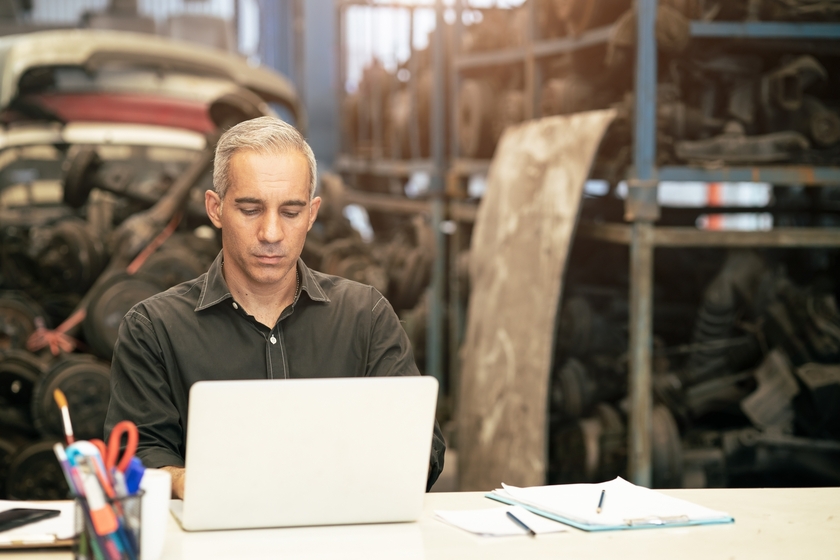
Effective planned preventive maintenance (PM) programs deliver substantial savings by increasing maintenance efficiency. Studies show preventive maintenance can save a manufacturing facility as much as 18 percent in maintenance costs.
Scheduling routine maintenance based on usage or time triggers reduces the likelihood of unplanned equipment failures that translate to emergency maintenance expenses.
1. Asset Inventory
Preventive maintenance is an excellent strategy for keeping critical assets in good working condition. However, the real cost-savings in PM come from fine-tuning your organization’s PM schedule over time.
Manufacturers’ recommendations do not always provide foolproof guidelines to obtain asset reliability. Workplace environments, machine usage patterns, and more can uniquely impact equipment behavior over time.
Beyond the importance of maintaining detailed asset inventories for accounting records, consistent recordkeeping can reveal opportunities to optimize spending patterns.
As routine maintenance is performed, keep track of service dates, labor costs, parts used and spare parts, and current conditions. Also, note the asset’s criticality to production and safety.
2. Asset Prioritization
It is nearly impossible to place all essential assets on initial PM programs. Stay realistic by creating an asset hierarchy for your organization’s most critical assets.
An asset hierarchy is a logical index of every machine and component that is critical and illustrates how the action of one machine can affect another. Maintenance teams can use the tool to track machines more easily, schedule PMs efficiently, and identify the root cause of failures quickly.
Prioritize assets that significantly impact production, have high maintenance costs, require regular maintenance, or pose safety hazards. As you begin to realize the return on investment (ROI) of your assets, gradually add more assets to the PM program.
3. Preventive Maintenance Schedule
A PM schedule lays out when proactive maintenance activities are performed on a given piece of equipment. When developing your PM schedule, select a day and time for maintenance that does not disrupt production. Base PM schedules on one of two metrics:
- Time: You can base your PM schedule on time and perform maintenance after a set period of time. For example, your fleet of vehicles can undergo maintenance every three months.
- Usage: For usage-based PM schedules, track usage metrics such as operating hours and production cycles. Maintenance activities are then performed when certain milestones are met. For example, schedule your fleet of vehicles for maintenance every 1,000 miles instead of every three months.
PM schedules usually depend on a work order system. A work order is a document that provides details about a maintenance task and outlines the process to complete the task.
4. CMMS Software
Most effective PM programs have one thing in common: a Computerized Maintenance Management System (CMMS) the entire team feels comfortable using. Maintenance planners can create, implement, and track recurring work orders via user-friendly dashboards.
Additionally, CMMS simplify, automate, organize, and optimize O&M. Turns out that 58 percent of facilities rely on CMMS to manage their maintenance operations.
Using modern, cloud-based CMMS can help overcome these implementation challenges. Unlike traditional on-premise systems, cloud CMMS is available over the Internet and, therefore, easier to set up, access from anywhere, and manage the database.
Modern CMMS like MaintainX also provide regular updates and better database security.
5. Team Communication
Clear and fast communication is essential for an effective PM program. Your team should always be able to communicate with each other efficiently and effectively.
According to McKinsey Global Institute, a connected workforce is more likely to post better performance. Using a mobile CMMS with in-app chat will virtually eliminate important project details falling through the cracks.
MaintainX reduces time spent clarifying details, improves access to maintenance records, and speeds up troubleshooting between technicians and managers.
6. Preventive Maintenance Plan Goals and KPIs
Your maintenance goals should clearly outline what you are looking to accomplish when you are looking to achieve them, and the metrics you will use to measure success. Your goals should be relevant to your company’s broader business goals.
Statistical benchmarks can be crucial to measuring performance improvements.
Common KPIs for measuring preventive maintenance plan effectiveness include:
- Planned Maintenance Percentage (PMP): How much time you spent on planned maintenance compared to unplanned maintenance within a given period.
- Preventive Maintenance Compliance (PMC): How many scheduled PM tasks you completed within a specific timeframe.
- Scheduled Maintenance Critical Percentage (SMCP): The impact of delayed planned maintenance activities.
- Mean Time To Repair (MTTR): The average time it takes to repair and restore an asset to full functionality.
- Overall Equipment Effectiveness (OEE): A manufacturing standard used to measure the productivity of facilities, processes, and equipment. OEE = Availability x Performance x Quality.
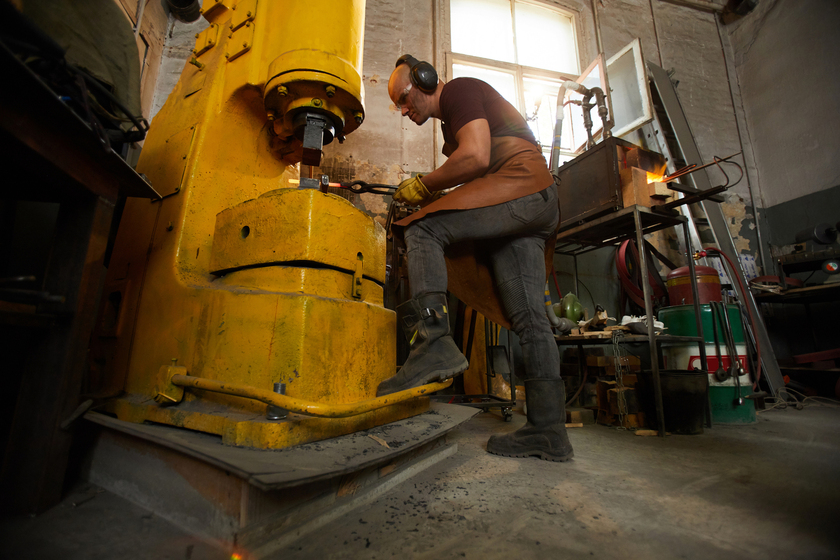
Increasing Maintenance Efficiency with MaintainX
Maintenance management and operations software, like MaintainX, provides in-depth analytics and reporting capabilities. Customizable dashboards, audit trails, and reports allow management to view completed preventive maintenance plans and regulatory SOP in real time.
Eliminate onboarding and training hurdles by automating SOP to reinforce processes, compliance, and quality.
By using a modern CMMS solution, processes can be at your team’s fingertips wherever they are, whenever they need them.
MaintainX can help build an accessible knowledge base for your employees to reference on the go and keep everyone on the same page.
FAQs
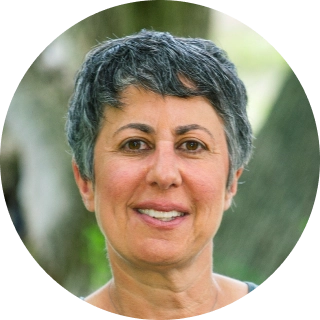
Caroline Eisner is a writer and editor with experience across the profit and nonprofit sectors, government, education, and financial organizations. She has held leadership positions in K16 institutions and has led large-scale digital projects, interactive websites, and a business writing consultancy.