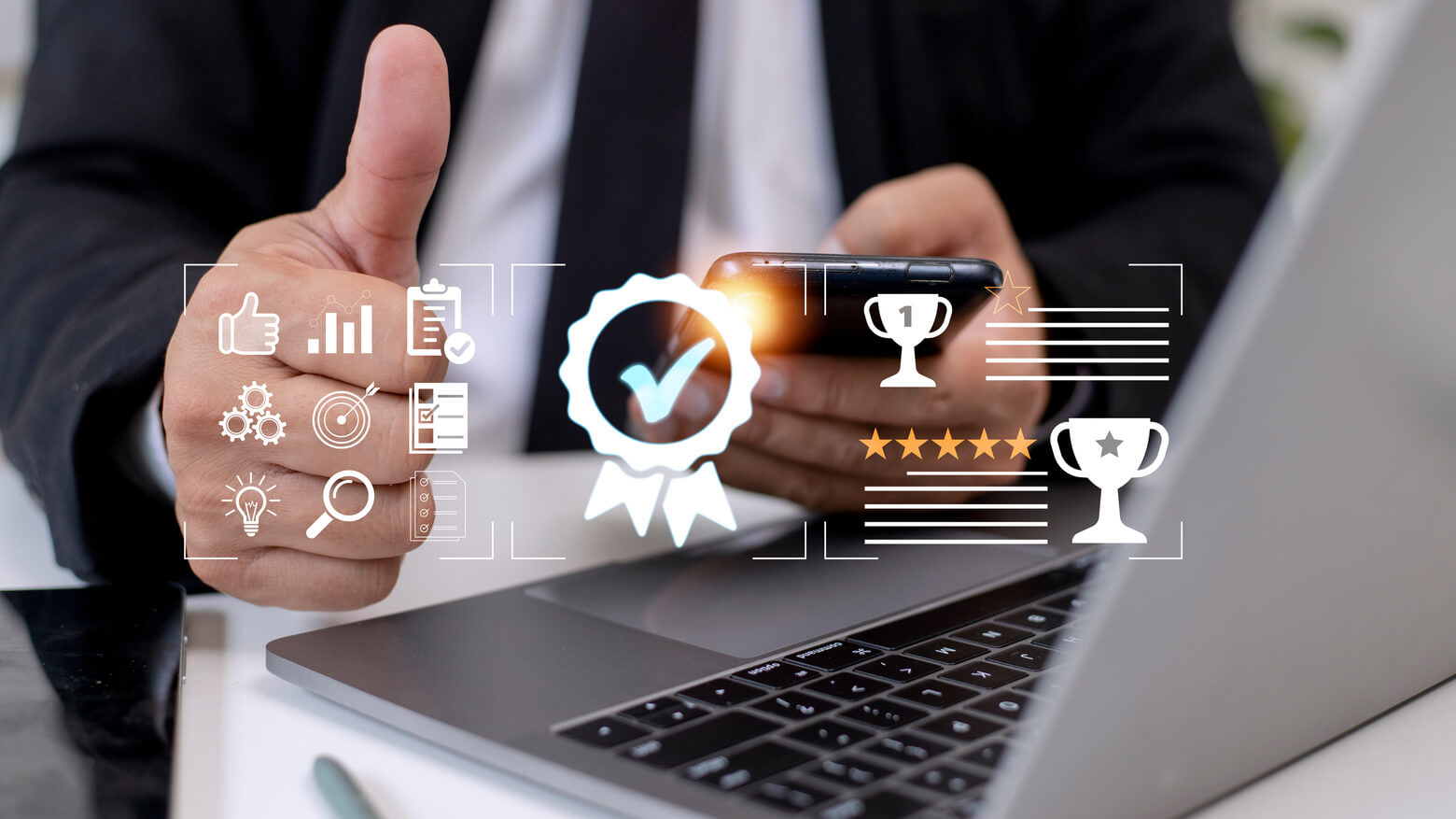
Despite global supply-chain challenges, certain world-renowned brands continue to experience monumental growth.
Amazon, Nike, and Lockheed Martin are just some of the companies that consistently seem to report gains when other organizations appear to be struggling.
After the first quarter of 2021, each one of these organizations reported multi-billion-dollar increases in net earnings.
While it’s hard to answer with complete accuracy, and without peeking underneath the hood, one characteristic stands out: a commitment to process improvement.
Company leadership within each organization has gone on record saying they credit much of their success to using Lean Six Sigma, among other O&M principles.
In other words, these organizations take consistent action to eliminate waste, streamline standard operating procedures (SOPs), and strengthen corporate sustainability.
How to Increase Profitability with Process Improvement (and Save Time)
This post will define process improvement, provide examples of process improvement in action, and extend valuable tips for implementing minor O&M improvements that yield significant wins.
We’ll also introduce you to computerized maintenance management system (CMMS) hacks that MaintainX clients—McDonald’s, Hilton, and Marriott—use to save up to 20 to 30 hours per week on maintenance management.
Let’s dive right in.
What Is Process Improvement?
Process improvement refers to the business practice of pinpointing, evaluating, and modifying existing business processes to yield better outcomes.
The primary goal of process improvement is to reduce human errors, wasted resources, and inefficient ways of doing things to enhance productivity. You may also hear the terms business process re-engineering, business process management (BPM), and continual improvement process (CIP) when discussing process improvement initiatives.
Businesses integrate process improvement into their operations to optimize business performance, improve end-user experiences, and meet industry best-practice standards. Practice doesn’t necessitate reinventing procedures that are already working.
Rather, it entails periodically evaluating SOPs to identify more efficient ways to increase productivity without sacrificing safety compliance and quality control.
What Process Improvement Techniques Are Available?
They say, “A picture is worth a thousand words,” but it’s more like tens of thousands. Some studies suggest that “the human brain processes images 60,000 times faster than text, and 90 percent of information transmitted to the brain is visual.”
Translation: It’s extremely difficult to remember, and communicate, every single detail involved in a complex procedure without visual representations!
Various forms of process visualization help management more quickly and thoroughly define multi-step processes.
This is why despite the numerous process improvement methods available, most of them involve using some type of visual aid. Of course, process visualization can be as simple as quickly jotting down a list of procedural steps.
With that said, here are the most common process improvement techniques that organizations use to optimize workflows.
1. Kaizen

Kaizen is a Japanese phrase often translated as “change for the better.” The technique focuses on five primary elements: teamwork, personal discipline, improved morale, quality circles, and suggestions for improvement.
It wasn’t until organizational management consultant Masaaki Imai applied the term to maintenance management that O&M professionals became familiar with Kaizen.
When used in conjunction with a Total Productive Maintenance (TPM) strategy, Kaizen can reduce equipment downtime, increase productivity, and curb unnecessary spending.
TPM includes several components, including preventive maintenance, early equipment management, and ongoing technician training that support autonomous maintenance decision-making.
Click here to learn more about Kaizen.
2. PDCA Cycle

PDCA is an acronym for Plan, Do, Check, Act. In 1993, W. Edwards Deming, who is often referred to as “the father of quality control,” published this critical-thinking model based on the scientific method.
Following the PDCA system is pretty simple. Just identify your workplace problems (plan), implement your chosen solutions (do), evaluate their effectiveness (check), and modify your future plan based on the data (act).
As the circle diagram above suggests, PDCA is meant to be an ongoing process. Managers within every department can use the framework to redesign processes, products, and services; define repetitive workflows, and structure problem-solving initiatives. Ideally, the more times you repeat the PDCA cycle, the stronger your processes will become.
Click here to learn more about the PDCA Cycle.
Process Mapping

Process mapping is a workflow tool that enables users to visualize needed process improvements. It’s also known as a process model, functional flowchart, process chart, and process flowchart.
Process maps are constructed in several different ways. Post-it notes, pen/paper, tablet drawings, and software programs all offer distinct advantages and disadvantages.
The important thing is to visually illustrate every potential decision involved in the process from start to finish.
Simply, identify the problem, brainstorm its associated activities, and plug the sequence of steps into shapes (i.e., ovals, rectangles, parallelograms, etc.). Connect the sequence of events with directional lines that indicate what happens first, second, and so on.
Click here to learn more about process mapping.
4. Six Sigma

Six Sigma includes a set of process improvement techniques originally geared toward the manufacturing industry. Motorola Engineer Bill Smith developed the practice during the late 1980s.
The practice borrows its moniker from the statistics methodology of representing units of standard deviation as “σ” or “sigma.”
Six Sigma supports process improvement with two methodologies: DMAIC—define, measure, analyze, improve, control— and DMADV—define, measure, analyze, design, verify. Both processes support improving quality control through empirical decision-making.
“Organizational champions” rely on verifiable data to inform maintenance scheduling as opposed to assumptions, guesswork, and anecdotal evidence. Due to its complexity, Six Sigma is best suited to companies with more than 500 employees and ample resources for ongoing training.
Click here to learn more about Six Sigma.
5. Total Quality Management (TQM)

Total Quality Management (TQM) involves the continual process of identifying, reducing, and eliminating operational errors to ensure customer satisfaction. Like Kaizen and Six Sigma, TQM also has ties to Japanese manufacturing best practices.
However, TQM differs because it doesn’t focus on how to reduce defects in the supply-chain process. More than anything, TQM is a workplace cultural standard. It requires a managerial commitment to ensure employees continuously seek to improve their skills in effort to produce on-demand products and services.
As reported by ASQ, the eight principles of TQM include customer focus, leadership, people involvement, process approach, systematic approach to goal setting, continual improvement, factual approach to decision-making, and mutually beneficial supplier relations.
Closely related to TQM is the ISO 9000 certification—an official acknowledgment of having implemented a set of standardized tools and quality control practices as recommended by the International Standards Organization. Many organizations believe TQM lays a strong foundation for achieving ISO 9000 certification.
Click here to learn more about Total Quality Management.
6. 5S Model
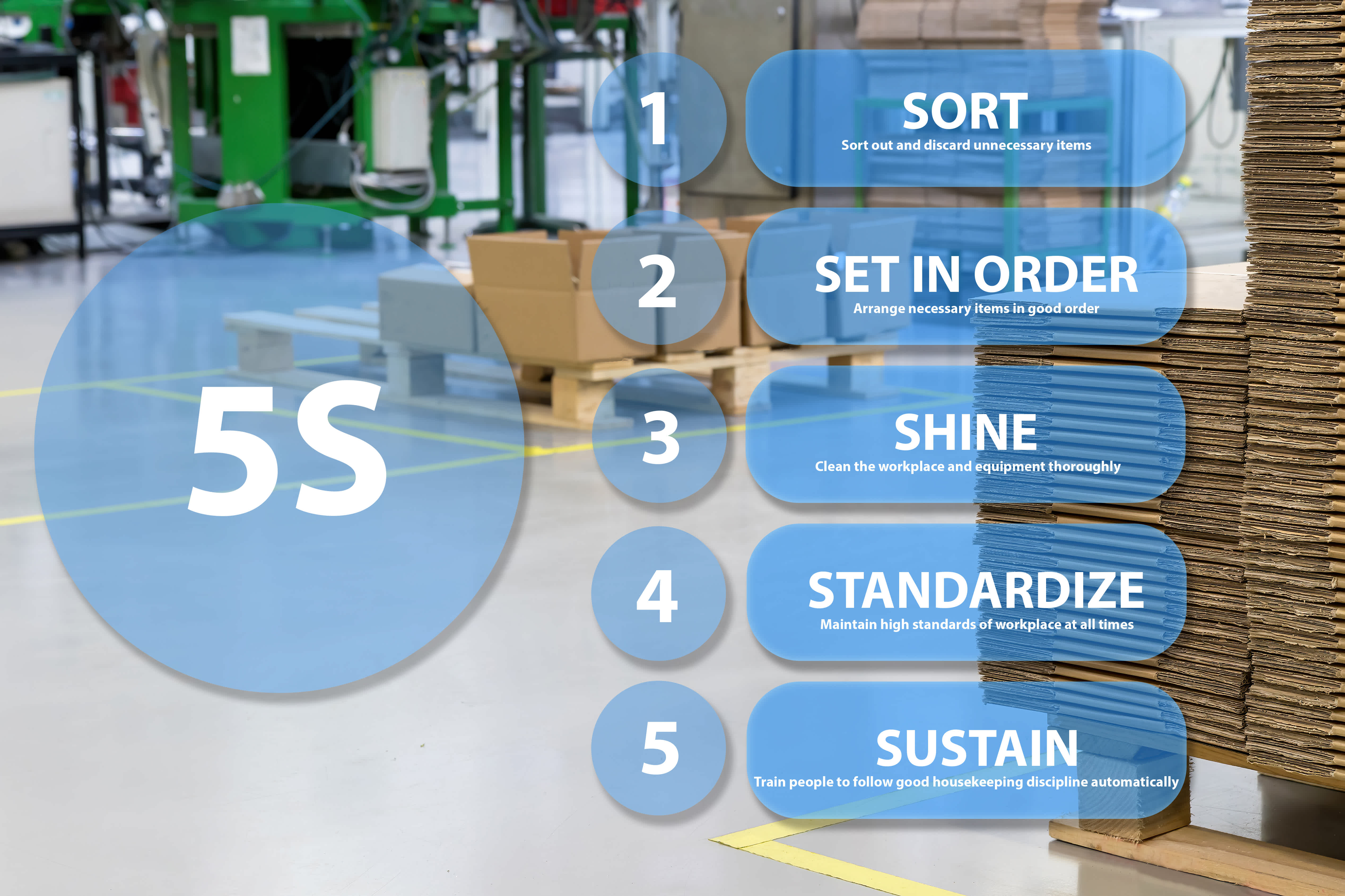
The 5S Model is another process improvement technique based on Japanese philosophy. 5S aims to sort, straighten, shine, standardize, and sustain workspaces for superior efficiency. In simple terms, it’s an organizational plan of attack for maintaining a clean work environment.
The idea is to throw out unnecessary items, ensure everything has a place, and create a sense of order that facilitates efficient workflows. Many businesses use 5S as one element within a broader methodology known as “visual control.”
Visual control is a business management technique that involves using visual signals, as opposed to written instructions, to communicate with increased efficiency.
The 5S model is part of the Lean manufacturing philosophy that serves to produce consistent operational outcomes in the most efficient manner possible.
Click here to learn more about the 5S Model.
7. Cause and Effect Analysis

Cause and Effect Analysis involves using a fishbone diagramming method to identify the likely causes of a workplace problem. These diagrams, named after their resemblance to the skeleton of a fish, help reveal potential roadblocks in work processes.
To solve a problem, write the problem in a box on the left-hand side of a piece of paper. Then, draw a line from the box to the opposite side of the paper. Next, draw several lines extending outward from the horizontal line.
Write down overarching factors that could be contributing to the problem on top of the horizontal lines. In a manufacturing facility, such factors may include inventory management, machine operators, and so on.
Finally, drill down to uncover the potential influencing factors within each category. Brainstorm the probable causes related to each factor. Repeat the process until you’ve identified all potential causes and sub-causes.
Click here to learn more about Cause and Effect Analysis
8. Value-Stream Mapping (VSM)

Value-Stream Mapping (VSM) is a Lean-management method for outlining the series of events that take place between product design and final delivery. The objective of VSM is to maximize productivity—without compromising quality standards—and to minimize waste.
VSM illustrates critical task steps, quantifies time expectations for each stage, and identifies opportunities to eliminate operational redundancies. When effectively executed, the technique facilitates clear communication, continuously improves processes, supports workplace cultural evolution, and provides insights into productivity bottlenecks (e.g., excess inventory, production constraints, delays).
What most differentiates VSM from the other items on our list? It can be used to create a visual representation of what’s happening from the customer’s perspective. Thus, VSM is especially useful for identifying the value of products and services.
Click here to learn more about Value-Stream Mapping.
9. Kanban

Finally, Kanban is a tool used to create process workflow visualizations that strategize how to mitigate potential bottlenecks. Yes, Kanban is another Japanese term on our list of process improvement techniques! It literally translates to_“signboard.”_
Though Taiichi Ohno is credited with creating the workflow improvement method for the manufacturing industry, David J. Anderson later adapted it for the IT industry in the early 2000s. Today, the methodology is widely used across industry lines to make gradual improvements within departments from marketing to human resources.
The six primary elements of Kanban include visualizing workflows, limiting work in progress, managing workflows, developing standard operating procedures (SOPs), implementing feedback loops, and improving collaboration.
Click here to learn more about Kanban.
Examples of Simple Process Improvements
Despite the seeming formality of the techniques mentioned above, process improvement doesn’t have to be complicated. At the end of the day, it’s all about how to streamline operational procedures, reduce waste, and improve management routines.
Successful businesses integrate process improvement strategies as part of periodic operational audits to ensure continuous refinement over time. Below are examples of how businesses of all types and industries most often use process improvement methods to enhance operational outcomes:
1. Onboarding
Did you know that it takes employees about 8 months to reach maximum performance capacity? And that one-fourth quit before reaching their one-year milestone? With this in mind, it’s no wonder companies are increasingly looking for ways to improve new hire training programs.
As Amy Hirsh Robinson, principal of The Interchange Group, told SHRM:
“Onboarding is a magic moment when new employees decide to stay engaged or become disengaged. It offers an imprinting window when you can make an impression that stays with new employees for the duration of their careers.”
Consider how many resources your organization could save if new hires weren’t wasting time trying to understand routine procedures, managerial expectations, and workflows. Like any other business process, management can streamline onboarding sequences for efficiency.
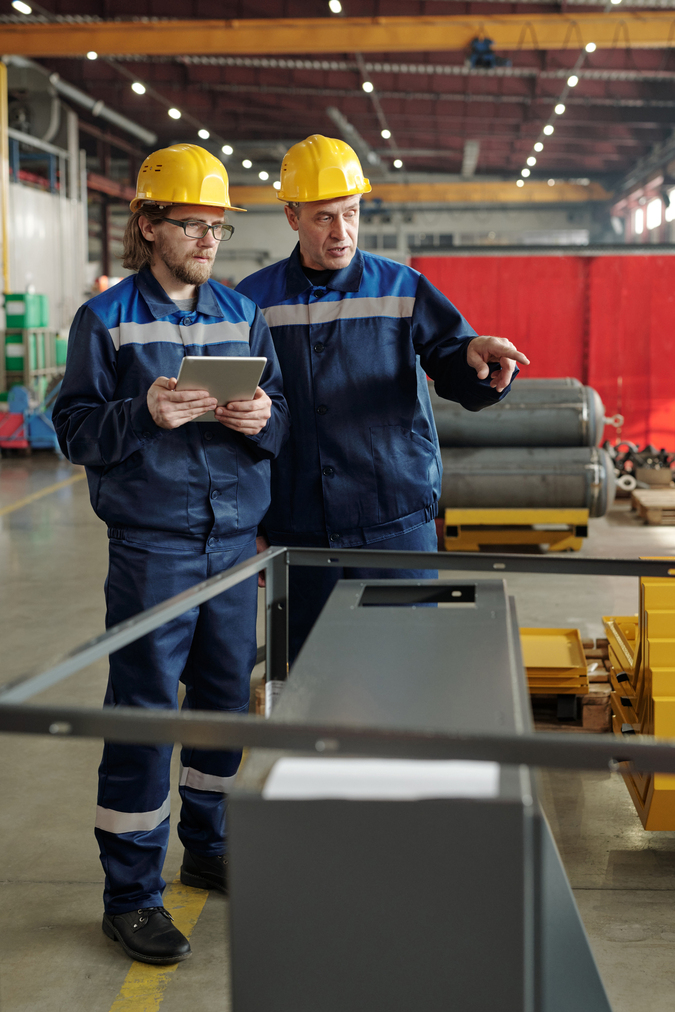
Analyze your current procedure for ineffective training steps, paperwork redundancies, and communication mishaps that may waste resources. You may be surprised at the patterns you find.
2. Cost Cutting
At the end of the day, the primary goal of any business is to make a profit. For this reason, looking for opportunities to reduce unnecessary expenses is integral to improving operations. Managers should examine several different types of costs: hard costs, soft costs, and cost avoidances.
Hard costs are the easiest to quantify because of their tangibility. They include material, overhead, and employee-related expenses.
Alternatively, soft costs relate to incremental changes made to both improve customer satisfaction and, potentially, sell more products over time. Examples include reducing bottlenecks, improving product reliability, and eliminating waste.
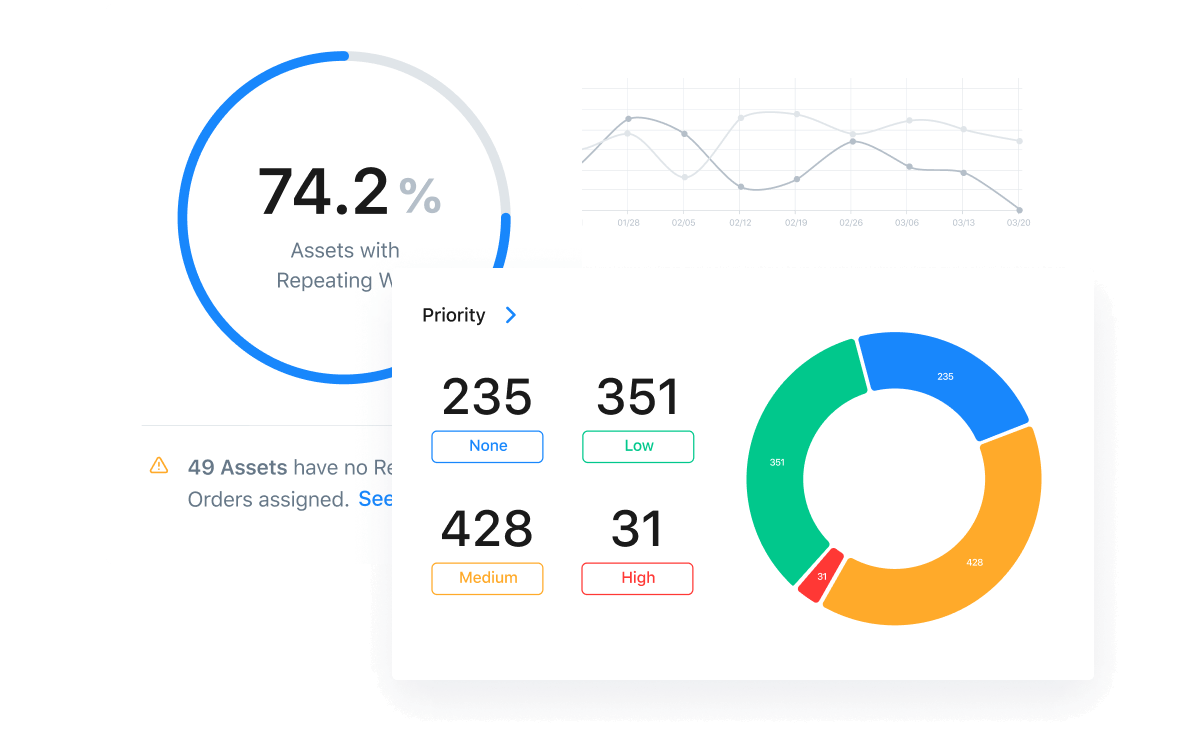
Cost avoidance is often related to preventive maintenance (PM) efforts. For example, say a maintenance technician identified and permanently repaired an equipment issue that might have otherwise halted production for days. We recommend using a computerized maintenance management system (CMMS) like MaintainX to schedule recurring work orders, implement digital SOP checklists, and demonstrate cost avoidance with advanced reporting charts.
3. Reducing Communication Issues
Lastly, improving team communication is an essential form of process improvement. Streamlining communication between employees, departments, and management reduces the likelihood of procedural errors.
Both Cause-and-Effect Analysis and process mapping can be useful for visualizing complex communication workflows. Effective ways of reducing communication issues include reducing contact touchpoints between departments, minimizing the number of emails sent, and using business messaging apps.
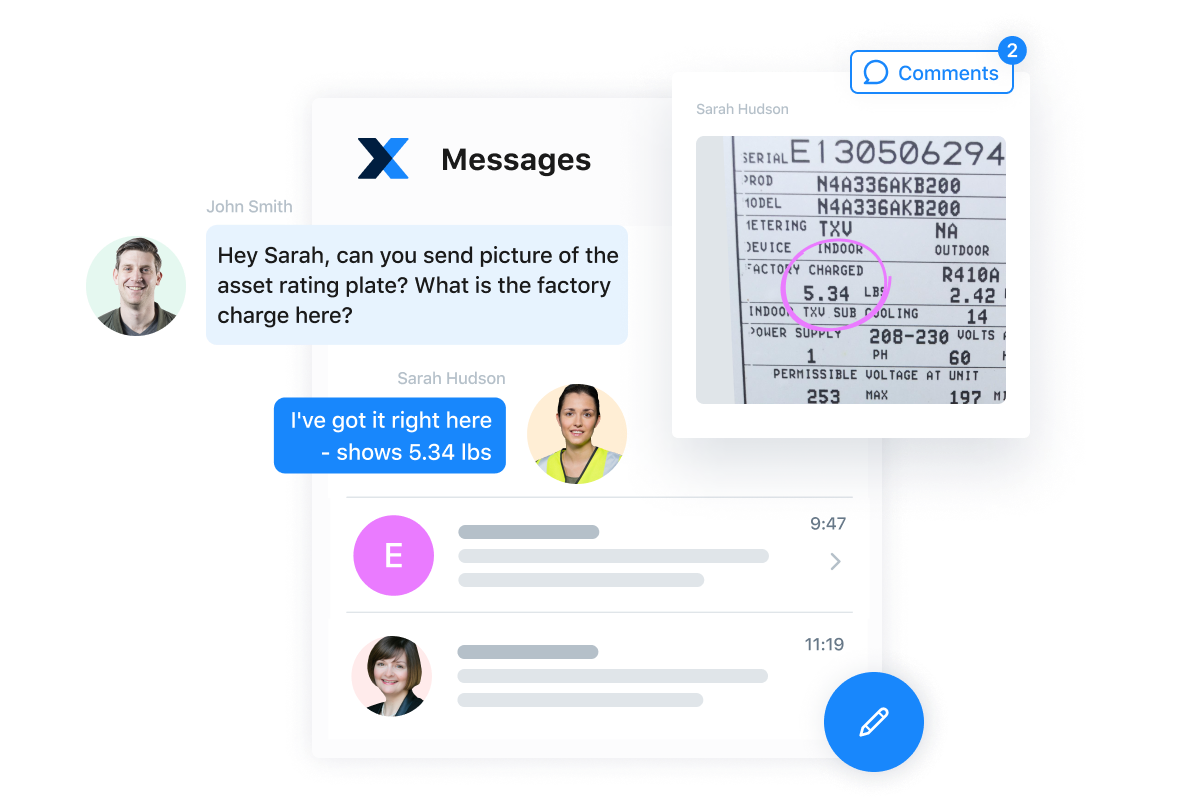
Other examples of common process improvement tasks include upgrading service quality, improving product quality standards, reducing delivery times, and reducing billing cycles.
In our next sections, we’ll look at some common questions about process improvement.
Process Improvement vs. Quality Improvement
As organizations worldwide strive to provide the best possible experiences for their customers and compete with “efficiency machines” like Amazon, it’s becoming increasingly common to stumble upon terms like process improvement and quality improvement.
Often, publications use the terms interchangeably. However, there is a slight difference between the two. We’ve already described what process improvement means: finding opportunities to streamline business operational processes and reduce waste.
Quality improvement, on the other hand, refers to a systematic approach to improving customer experiences. The concept specifically refers to improvements made to procedures and policies designed to meet defined quality standards. In other words, it supports organizations in consistently providing high-quality products and services.
With that said, process improvement and quality improvement go hand-in-hand. Process improvement techniques can help generate ways to eliminate root causes, while quality improvement audits can help identify defects and inefficiencies.
Managers can apply most of the process improvement techniques mentioned in this article (e.g., Kaizen, PDCA, value-stream mapping) to quality improvement projects.
Process vs. Workflow
Similar to the confusion between process improvement and quality improvement, folks sometimes mix up processes vs. workflows. A process refers to a logical sequence of activities necessary to deliver a product, decision, or information to key stakeholders.
Alternatively, a workflow refers to the steps taken to complete a given task. Workflows allow data, information, and documents to flow across organizational lines. Simply put, workflows provide a blueprint for employees to follow every time they begin a task.
The major difference between the two terms is that processes are strategic, while workflows are tactical. Processes support specific business goals. Examples of processes include providing custom clothing alterations, designing electric motors, and onboarding new employees.
Conversely, workflows include the tactical steps of how to complete the processes. At MaintainX, we call workflows “procedures,” and we make them available to our app users in the form of customizable digital checklists. Automation is the key to both process and workflow success.
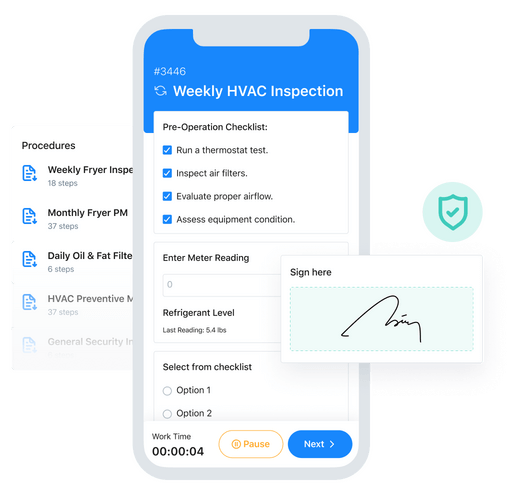
Creating a Process Improvement Plan
A process improvement plan outlines how to improve business processes for better efficiency. It’s often just one component of an overall project management plan, guiding how teams can analyze and develop measurable improvements. You can develop a process improvement plan by taking the following seven easy steps:
1. Outline
The first step to creating a process improvement plan is to write down the specific processes you want to fine-tune. Break them into overarching categories (i.e., inventory management, maintenance, shipping) before mapping out every step involved within each process.
For best results, leave no detail unaccounted for when dissecting your processes. Though time-consuming, getting a handle on exactly what is happening within each operational area is essential to everything that comes next. The more information your team has cataloged about each task, the more effective your team’s recommendations will be.
2. Assess
After mapping out every step of your processes, perform an analysis to identify underlying issues you could eliminate or improve upon. Take a closer look at each step to determine if employees are executing steps as efficiently, cost-effectively, and safely as possible.
Some of the most common problems identified at this stage include over-allocation of resources, inefficiencies, employee scheduling, and product delays. Remember: you want to address the root cause of the problem. A root cause analysis is helpful to get to the bottom of things.
3. Reconfigure
Next, reconfigure your process steps to prevent future occurrences of identified issues. Invite members of the organization who are involved directly with the process to provide feedback.
Doing so will ensure that your process improvements are realistic, achievable, and accepted. Why? Because employees have hands-on insights into task details from working on the job day in and day out. Developing workflows while sitting alone in a corner office is a recipe for failure!
Ensure all of your procedures are organized into step-by-step workflows that leave no room for misinterpretation. In addition to writing clear work instructions as part of a digital checklist, you may also want to attach PDF manuals, policies, and diagrams to provide further clarification.
Next, create a timeline for task completion. Again, we recommend relying on SOP software like MaintainX to digitally assign checklists, increase transparency, and automate scheduling. Now, you’re ready to put your new process improvement plan into action!
4. Review
No business initiative is complete without a plan to track, evaluate, and tweak ongoing processes. Consider scheduling a periodic review of previously implemented process improvement measures to ensure your team’s long-term success. Track relevant KPIs, talk to team members, and course-correct workflows as needed.
5. Communicate
Finally, the better the communication between team members, the better the results. Eliminating communication barriers is paramount to ensuring processes are completed on time. You never know what unanticipated situations may arise that result in employee confusion.
As previously mentioned, implementing a user-friendly business messaging app will ensure everyone is on the same page throughout the day. Look for a chat app that includes private messaging, group messaging, and work order commenting for the best results.
Training Options
Whether your organization has already landed on the process improvement technique of its dreams or is still weighing its options, you may want to invest in professional training.
If you’re leaning toward implementing formal techniques like Lean Six Sigma, we recommend signing up for a training program that focuses on that specific modality. Several independent providers and universities offer online courses at this time. If you’re seeking something more generalized, check out these courses below:
- BPM Essentials: The institution offers a Business Process Model and Notation (BPMN) method and style training course. You can also take the certification exam for BPMN 2.0 standard.
- BPM Institute: The Institute offers Business Process Management Professional (BPMP) certification in addition to other certification programs.
- BPTrends Associates: The BPTA is one of the most recognized process improvement institutions globally. Its curriculum is well known and adopted by several reputable organizations, such as the International Institute of Business Analysis (IIBA) and the Association of Business Process Management Professionals (ABPMP).
You also can find excellent resources on process improvement at online course sites like Coursera, Learning Tree International, Watermark Learning, and Udemy.
Streamline Operations with CMMS
Committing to continuous improvement isn’t that different from any other operational undertaking. It requires thoughtful planning, scheduling, and progress tracking. The good news? You don’t have to manage dozens of important details!
MaintainX streamlines process improvement by providing management with a centralized platform for digitizing, assigning, and managing standard operating procedures. It also facilitates team messaging, enhanced reporting transparency, and automated preventive maintenance scheduling.
To top it off, it’s the most user-friendly mobile CMMS app in the marketplace today. If you’re ready to experience the simplicity of MaintainX, just click the link below.
FAQs
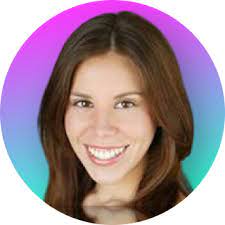