
Let’s do some math:
- Four Rivers produces an average of 1,000 widgets per hour.
- Each widget is worth $100.
- The manufacturing plant experiences 1 hour of downtime each week.
How much money does Four Rivers lose each month? The answer is a whopping $400K per month. At MaintainX, we have conversations about equipment availability with clients like Four Rivers every day. Obviously, the numbers will vary based on a company’s industry, business model, and size. Industries with the highest risk of downtime costs include finance, government, healthcare, manufacturing, media and communications, retail, and transportation/utilities.
Manufacturers know that complex machinery can be fickle. However, just “hoping” a critical piece of equipment doesn’t break down at an inconvenient time is no longer good enough. The good news? Modern mobile CMMS (Computerized Maintenance Management System) analytics make it easier than ever for companies to identify cost-saving opportunities, increase equipment reliability, and reduce lifecycle costs.
“The emergence of a new generation of data processing, analysis, and visualization tools is starting to help organizations get maintenance planning under control, and take their operations to the efficient frontier.”
McKinsey
In this post, we highlight how one Fortune 500 manufacturer is using MaintainX’s advanced reporting features to cut costs. After reading, you’ll have a clearer understanding of how advanced mobile CMMS analytics can reveal insights into your organization’s unique hidden savings opportunities.
3 Ways to Cut Costs with Mobile CMMS Analytics
Do you work in the manufacturing industry? If so, you know our introductory widget scenario isn’t the least bit unusual. According to a Ponemon Institute Report, the average cost of downtime for large facilities is $9,000 per minute. Alternatively, the average cost of downtime for small businesses is estimated at $137 to $427 per minute.
Generally speaking, manufacturing and supply-chain organizations have two options for handling downtime: reduce costs or increase availability. Here’s how our CMMS’ advanced features are helping a manufacturing client achieve both:
1. Improve Work-Hour Utilization
One of the easiest ways to cut costs is via man-hour utilization. Like most organizations, our client pays its maintenance technicians based on 8-hour workdays. However, Jim, the maintenance director, often wondered: how many of those hours are actually being spent on productive tasks?
Ultimately, the company found a solution in MaintainX’s Time & Cost Tracking feature. This mobile CMMS feature allows administrators to see exactly how much time technicians spend completing individual work orders for the day compared to actual hours being worked. Numbers can be run on both individuals and entire shifts.
MaintainX’s mobile version has a convenient stopwatch feature allowing maintenance techs to track time directly for the task at hand. Additionally, time entries entered via the Stopwatch are denoted with an icon to help distinguish them from manual time entries.
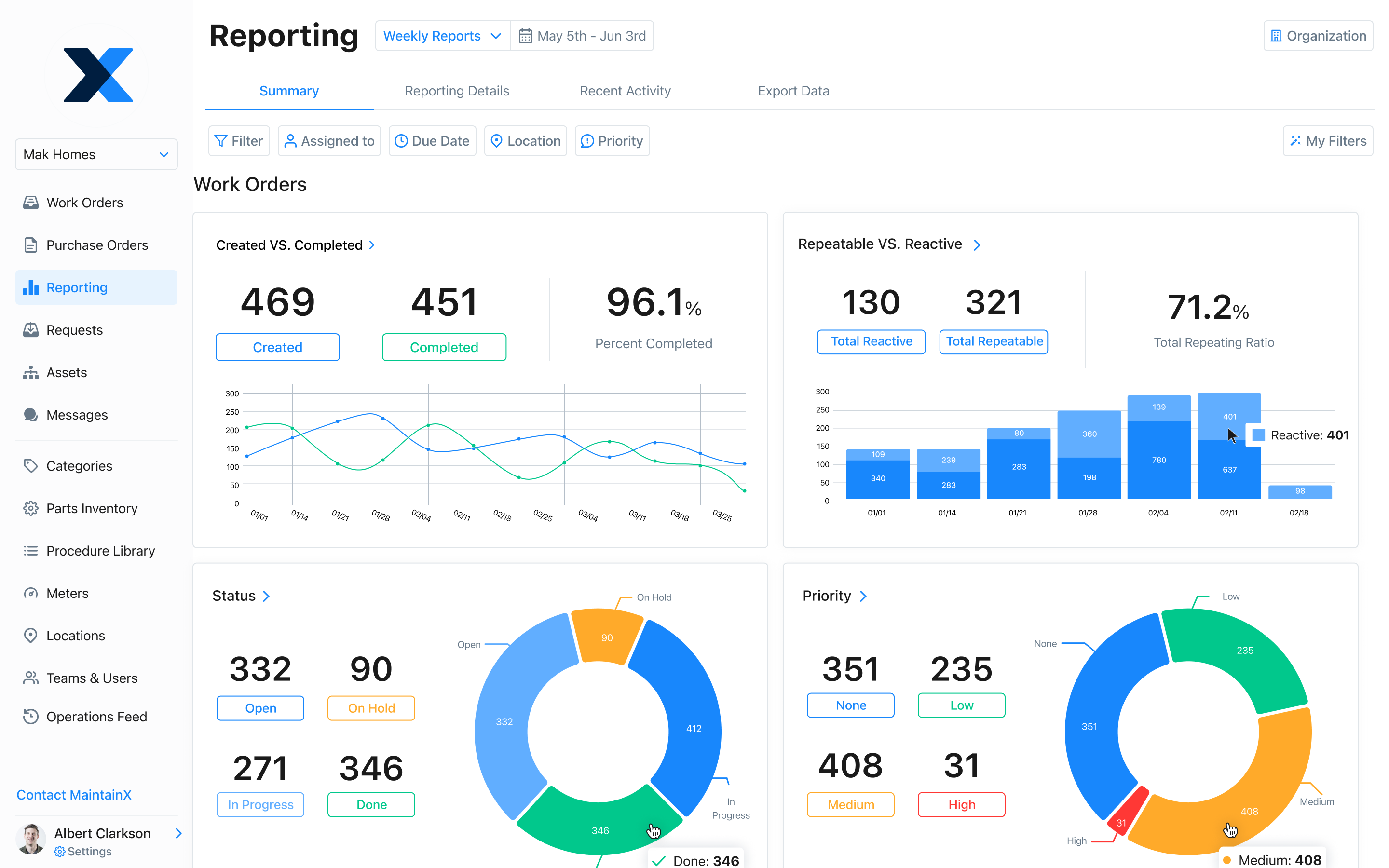
After task times were compared to clocked hours in Kronos, the organization’s time and attendance software, to arrive at a work-hour utilization percentage. This KPI allowed Jim to investigate any discrepancies and ensure workers had everything they needed to be productive while on the clock. Today, the organization averages a 97 percent utilization rate!
2. Gain Productivity Insights with “Categories”
Once the client knew workers were indeed being productive, another question arose: what are the tasks on which they are productive? MaintainX allows administrators to set mandatory category fields for creating work orders. In other words, an operational manager could not assign a work order without designating it within one of several predetermined categories. This level of organization, for example, allows users to determine how much time different levels of workers are spending completing different types of tasks.
For instance, our client employs level 1, 2, and 3 maintenance technicians. As expected, the differences in both salaries and skill levels between the three roles are substantial. For obvious reasons, organizational leadership doesn’t want a $ 75,000 salary worker doing what a $ 25,000 salary worker can accomplish. With MaintainX Advanced Reporting, Jim discovered his senior maintenance technicians were spending nearly 80 hours per month changing forklift batteries. The operational manager was able to see this data because he had already created categories for various types of work orders.
The reactive maintenance requests often required workers to travel from one end of the large warehouse to another for completion.
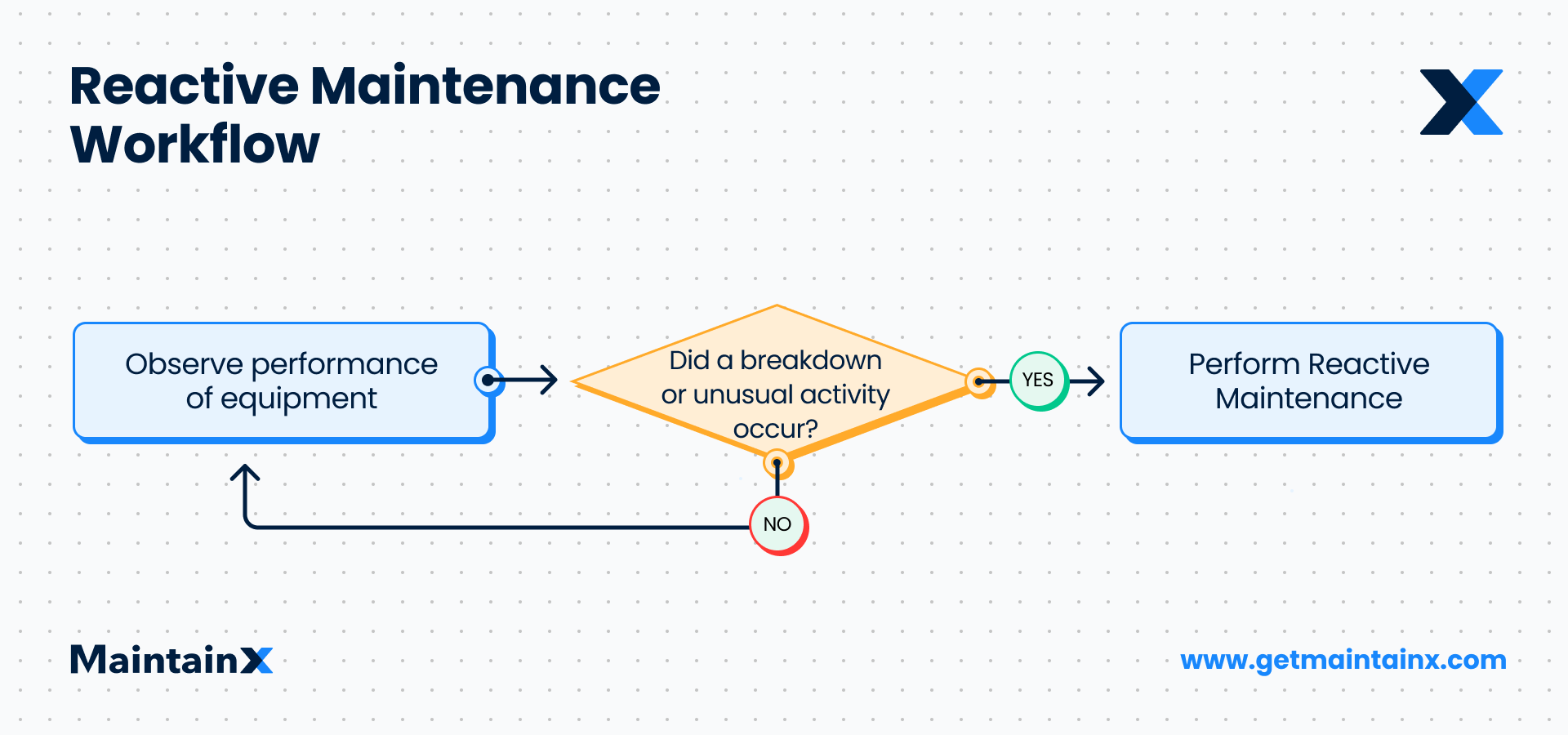
This one entry-level task was costing the company $1,735 per month. After analyzing his MaintainX dashboard, Jim told his general manager the organization should designate a $10/hour second-operator shift for such entry-level tasks. This is just one example of an overspending pattern Jim was able to notice by analyzing advanced reporting data.
3. Decrease Asset Lifecycle Costs with “Asset Types”
Finally, our manufacturing client is using mobile CMMS analytics to inform decisions about when to sell and replace assets. With the help of MaintainX, Jim can now determine the Total Cost of Maintenance (TCM) for each asset.
Once he realized the company had already spent thousands of dollars—not including parts—repairing one piece of equipment in a month, he knew the company would maximize savings by replacing the worn machine.
The industry rule of thumb is to place 25 percent of equipment value back into servicing before purchasing a new machine. Case in point: the company would have spent $40,000 on repair costs by the end of 2020, whereas a new machine would cost around $600,000.
“Because MaintainX is so easy to use, we have seen a dramatic increase in reported Corrective Maintenance and completed PMs resulting in an increase in our LEF and GLY KPIs by at least 15-20% on average, by increasing the effectiveness and ease of maintenance scheduling and execution. I also love the ability to integrate with our ERP when we are ready. We can easily calculate our Man-Hour Utilization, Maintenance Plan Attainment, and view future Maintenance Plans within a few clicks. I would recommend you take a 1st and 2nd look at MaintainX.”
—Akil Cox, Maintenance Planner, Barbados Dairy Industries Limited (Anheiser-Bush)
Decrease R&M Costs with Mobile CMMS Software
As we’ve shown, modern mobile CMMS makes it easier than ever for manufacturing companies to identify cost-saving opportunities, increase equipment reliability, and reduce lifecycle costs. Checkout MaintainX CMMS pricing. Our basic plan is free forever
MaintainX is the world’s first free digital maintenance and operations app designed with collaborative workflow functionality. The platform eliminates the problem of lost email threads, undocumented phone calls, and disorganized text messages with in-app messaging and work order commenting. Our clients also enjoy the convenience of work order commenting, supply inventory management, printable safety inspection completion reports, and more with our user-friendly app.
FAQs
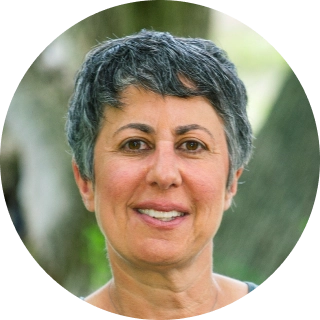
Caroline Eisner is a writer and editor with experience across the profit and nonprofit sectors, government, education, and financial organizations. She has held leadership positions in K16 institutions and has led large-scale digital projects, interactive websites, and a business writing consultancy.