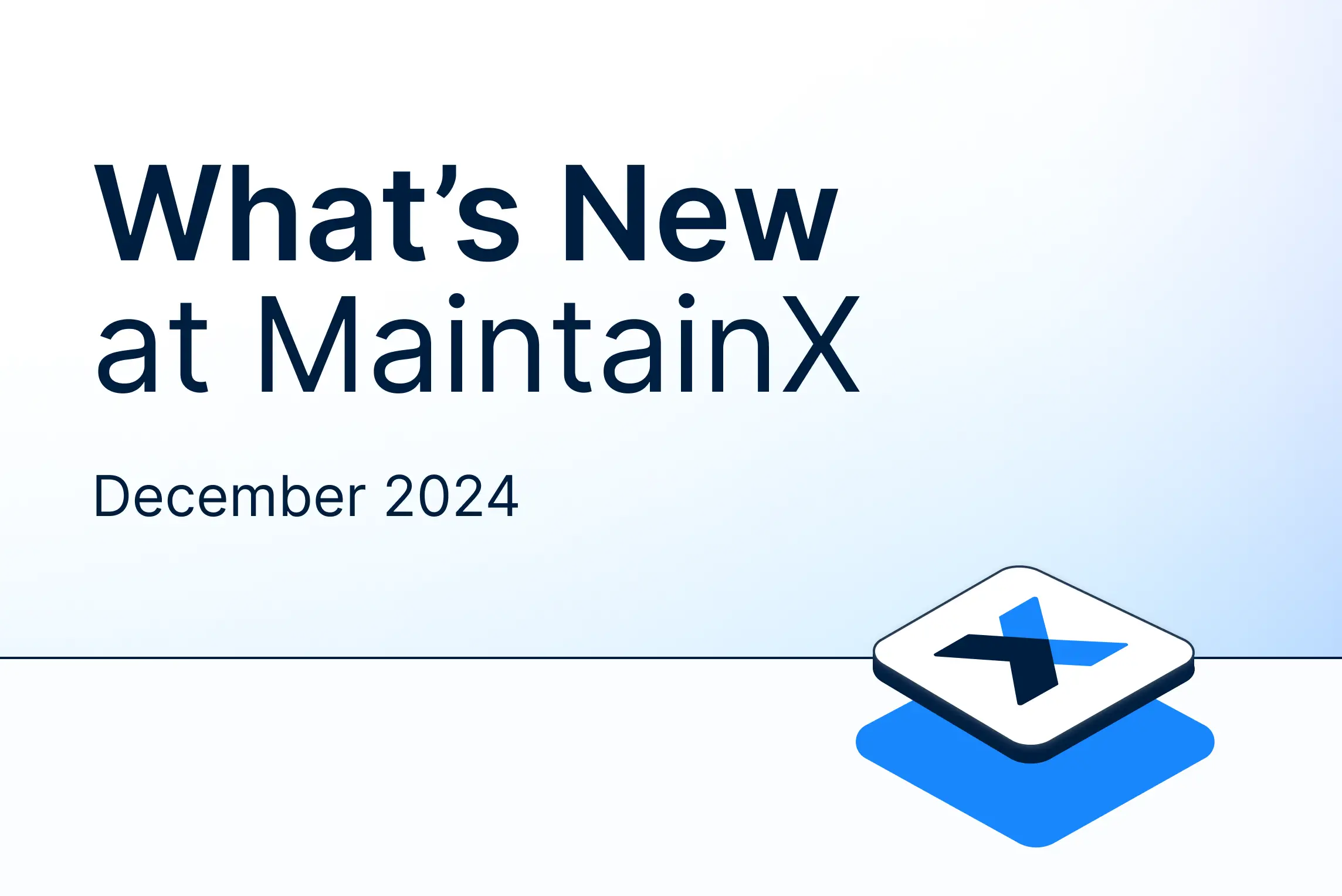
The Thanksgiving season left us feeling extra grateful for the strong partnerships we’ve built with our customers.
And the past month demonstrated what these partnerships can achieve, as we rolled out several exciting updates powered by customer feedback.
Workflow Automations, along with some updates to our Meters module, transformed the way MaintainX collects and acts on equipment data to help customers adopt smarter and more cost-effective maintenance strategies.
We also updated Asset Hub to make it easy for customers to install OEM-approved maintenance plans for their existing assets in MaintainX.
Let’s get the festive season underway by walking through some of our most impactful recent updates.
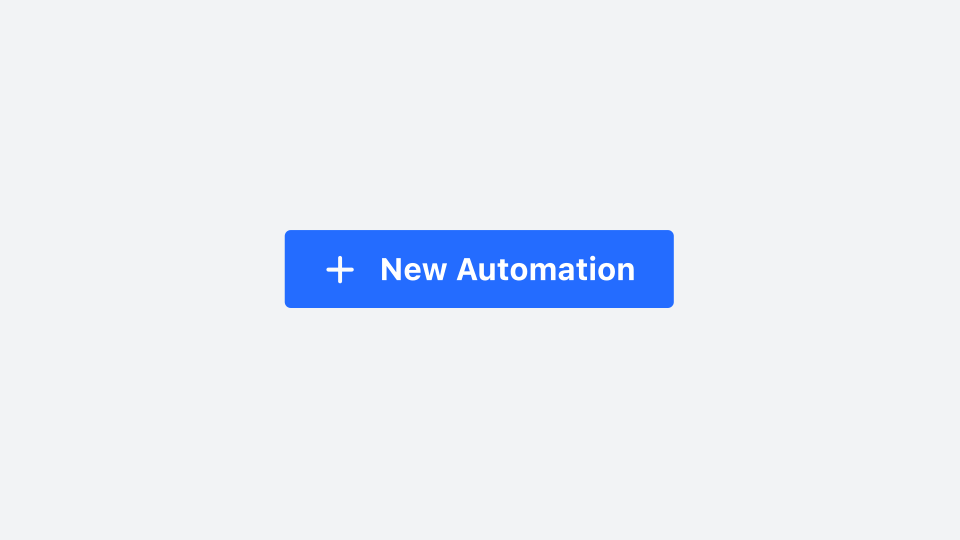
Automate tasks and reduce downtime with Workflow Automations
Catching faults early is the key to preventing breakdowns.
But doing this manually makes it harder to spot threats and act quickly enough to protect your assets from failing.
Last week’s release of Workflow Automations allows you to create more flexible usage-based and condition-based workflows using single or multiple meter readings.
In addition to triggering work orders, customers on our Enterprise plan can now automate alerts and asset status updates when meter thresholds are hit. This makes it easier to monitor equipment in real time and catch faults earlier.
The Enterprise plan also allows you to restrict automations to certain hours of the day, to align with operational hours and shift patterns.
Visit the Automations module to get started, or learn more about it in our Help Center.
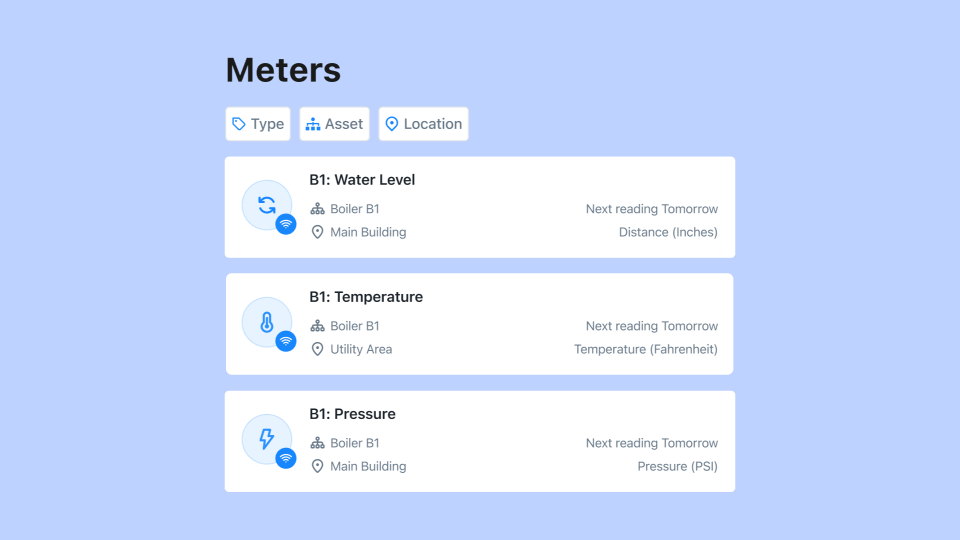
Connect and access your equipment data faster than ever
Since your automations are powered by equipment data, we also updated our Meters module to enable smarter and faster monitoring.
A new boolean data type supports the tracking of machine status, leaks, open doors, and more, using energy and contact sensors.
And our new Automated meter type makes it easier to connect IoT devices to MaintainX.
We’re also now serving more useful insights on your Meter pages, including which automations are running and when the next reading will be taken.
And remember that you can monitor assets, check meter readings, and manage automations, all from the Assets module, which keeps all your equipment data in one place.
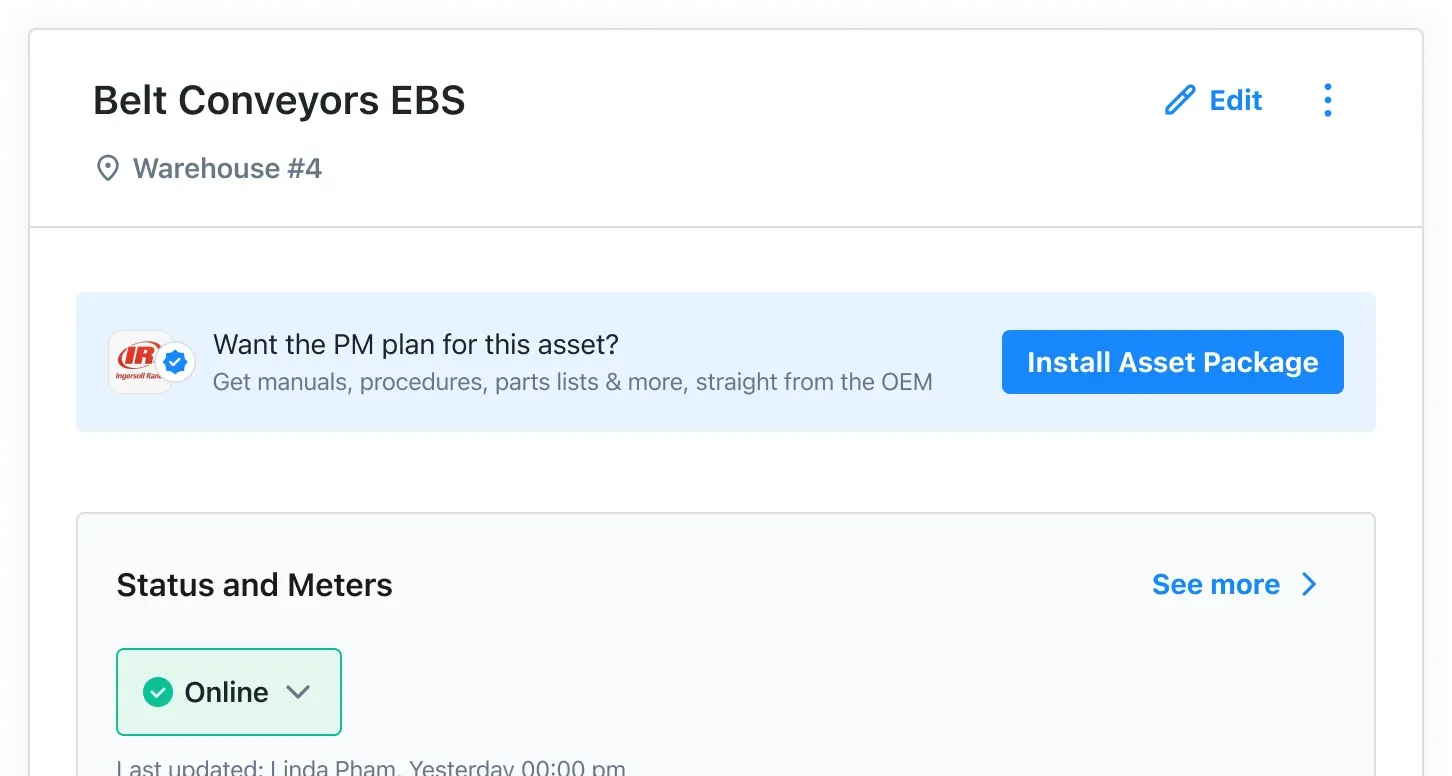
Install OEM-approved plans for your assets instantly
The foundation of any mature maintenance strategy is to have easy access to OEM-recommended maintenance plans and best practices.
That’s why we recently launched Asset Hub, allowing customers to attach approved PM plans, procedures, and parts lists to new Assets in MaintainX.
Customers can now install this information for their existing MaintainX assets in just a few clicks from the Asset module.
For any of your assets that exist today in Asset Hub, Admin users will see an option to Install Asset Package directly from the asset page. Installing the package will add certified PM plans, procedures and parts information for that asset—ensuring you have the latest information and best practices to keep your equipment running.
Constantly evolving to help you work more efficiently
Like every month, we also made small improvements to MaintainX’s user experience and capabilities to help you manage your work and assets more efficiently.
Some recent updates include:
- The new Shared/Exported filter, allowing you to see only work orders that were exported to PDF
- The ability to see the number of Sub-Assets that belong to an Asset when searching or filtering
- A Vendor Type field and filter to improve your vendor management
If you’re not yet a customer of MaintainX, book a tour today.
Learn more about MaintainX
How do I train my team on new SOPs?
To effectively train your team on new procedures, arrange dedicated training sessions where team members can focus on learning the new SOPs without distractions. Depending on the complexity of the SOPs, you may need multiple sessions.
Also, allow team members to practice the new SOPs in a controlled environment. Doing so helps reinforce learning and allows them to apply the new procedures in real-world scenarios.
How does CMMS enhance asset lifecycle management?
CMMS software allows teams to track the lifecycle of complex machinery, pinpoint failures, and control costs. It also allows MRO professionals to access maintenance logs for each asset, schedule preventive maintenance to keep assets running smoothly, and prevent unplanned breakdowns by tracking asset health.
How often should maintenance KPIs be reviewed?
You should review KPIs regularly to confirm that operations are on track. For most companies, a monthly review provides a frequent enough snapshot to spot trends and address issues before they become major problems. You may need to monitor some KPIs weekly or even daily, such as equipment downtime or work order completion rates. Regular reviews ensure that your team can make adjustments quickly, optimize performance, and meet your organization's long-term goals.
How do you use maintenance KPIs to improve decision-making?
Maintenance KPIs provide valuable data to help make informed decisions. For example, by tracking technician productivity, asset utilization, and maintenance costs, you can see where your team excels and where they can improve. This data allows you to make strategic decisions, such as reallocating resources, adjusting maintenance schedules, or investing in preventive maintenance. Regularly analyzing KPIs backs your decisions up with data, helping to improve asset reliability and make the best use of your resources.
What are the best work order automation tools?
Every work order management system has its own strengths and challenges. The best tools for work order automation should offer real-time tracking, mobile accessibility, customizable workflows, and easy integration with existing systems. MaintainX provides all of these features, making it an ideal solution for businesses looking to achieve operational excellence.
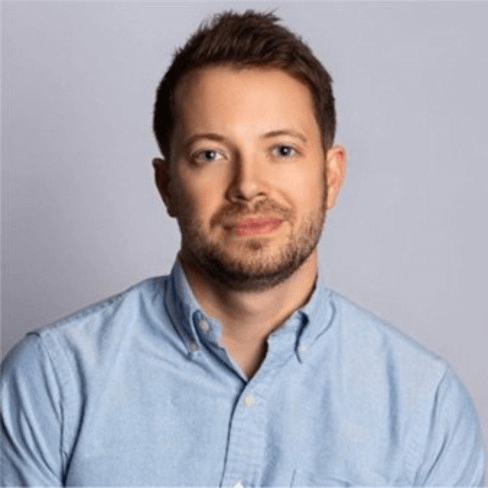
Colin Strachan is a Senior Product Marketing Manager at MaintainX, with a background in journalism and almost a decade of experience in SaaS marketing. In the past few years, he has worked with some of the world’s largest enterprises to adopt software that empowers their employees to work more effectively.