%20(1).png)
Whether you’re a regional shop or a global corporation, operational efficiency and standardization is a must-have for multi-site leaders. But scaling best practices and SOPs, maintaining visibility across locations, and ensuring smooth collaboration between teams is easier said than done.
The reality for many multi-site businesses is that their locations often operate independently, using different systems and siloed processes. This disconnect makes it challenging to compare performance, standardize workflows, and manage inventory efficiently. Add in the broader challenges in manufacturing today—skilled labor shortages, supply chain volatility, and more—and it’s clear why multi-site leaders are looking to standardize and unify operations for improved efficiency.
That’s where MaintainX comes in. Our new multi-site capabilities help companies of all sizes drive standardization and efficiency across the management of parts, assets, procedures, and performance data. This helps companies of all sizes drive standardization and efficiency quickly, and where it matters most.
Here’s how you can use these multi-site features to build operational excellence:
Curious how multi-site customers use MaintainX? Read on for real-world examples for each feature below.
Standardize compliance and best practices with Global Procedures
Sharing and enforcing SOPs across sites is a critical piece to company-wide efficiency and standardization.
Take this scenario:
Corporate needed to roll out a new company-wide safety protocol for their conveyor inspections. They needed to update procedures across 12 facilities, but their method of emails and manual updates led to missed changes and inconsistencies. Without a reliable way to enforce the update, compliance and safety were at risk.
With MaintainX Global Procedures, the regional facilities manager can make the change once and instantly apply it across all facilities.
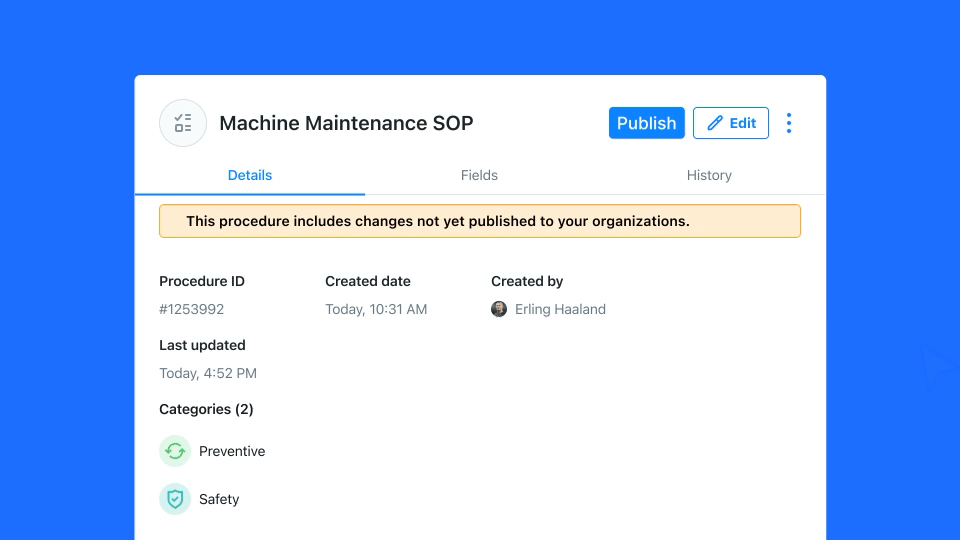
Every site now has the latest checklist, ensuring compliance without delays or confusion. Leaders can enforce best practices at scale, site managers can adapt quickly to operational changes, and technicians have access to the most up-to-date procedures—keeping teams aligned and operations running safely and efficiently.
Reduce carrying costs and last-minute purchases with Global Parts
Next, we’ll cover how multi-site customers use MaintainX for efficient parts inventory management.
Take this scenario:
A critical asset goes down and the maintenance manager needs a replacement part—fast. But their plant is out of stock, and ordering from a vendor means paying double for last-minute fees and shipping. Without a way to check inventory across locations, the only option is an expensive and time-consuming emergency order.
Global Parts gives teams real-time visibility into parts availability at their other sites, allowing them to request and transfer what they need without relying on costly vendor orders.
.gif)
With Global Parts, corporate leaders can run leaner inventory levels, improve forecasting, and minimize supply chain dependencies. Managers keep operations running smoothly by minimizing downtime and avoiding unnecessary spending. And technicians can more quickly access the parts they need—ensuring repairs happen faster, and at a lower cost.
Move and manage assets seamlessly with Global Assets
Multi-site leaders are also using MaintainX to drive efficiencies with better asset management and visibility.
Take this scenario:
When opening a new facility, a regional operations manager faces a common challenge: ensuring a smooth transition for both equipment and teams. Moving assets between locations is straightforward enough, but critical maintenance data—like work history and asset health—often gets lost or siloed in other tools. Without this data and a centralized view, teams risk inefficiencies, unexpected downtime, and higher costs.
With MaintainX Global Assets, every asset arrives with its work history and asset health data intact.
.gif)
Leaders have visibility into cross-site inventory, allowing them to make informed decisions about asset deployment and replacement.
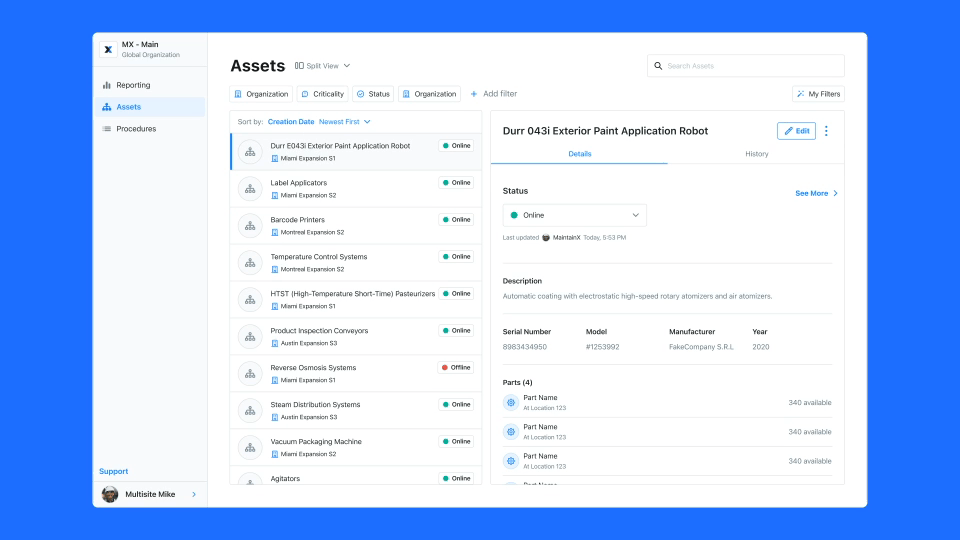
Site managers ensure their teams have the data they need to keep operations running smoothly. And technicians can start working immediately, with access to complete maintenance records that keep equipment performing at its best.
Gain full visibility into cross-site performance with Global Reporting
Getting a comprehensive view of performance by site and company-wide helps multi-site leaders quickly see where they need to focus their efforts for improvements or repeatable success.
Take this scenario:
Corporate leadership needs to invest in training to boost productivity and ensure on-time job completion. But with multiple regional sites operating independently, they face a critical question: Where should they allocate their training budget for maximum impact?
Finding the answer wasn’t easy—performance data was scattered, incomplete, and siloed across locations, making it nearly impossible to compare site performance, pinpoint inefficiencies, or scale best practices.
With MaintainX Global Reporting, leadership can see their most critical metrics, and drill into site-specific data, all in one view.
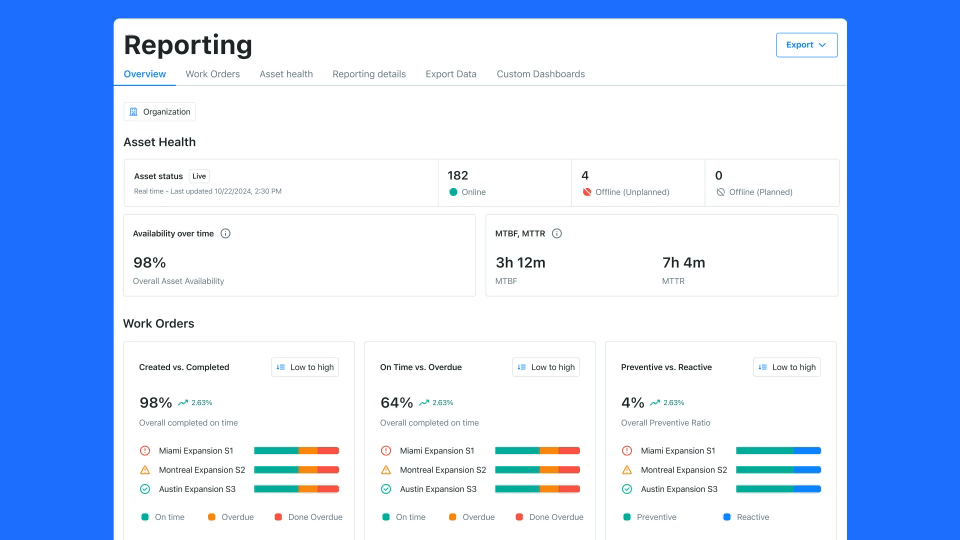
Now, they can quickly identify bottlenecks, recognize high-performing teams to replicate success, and allocate resources efficiently to improve performance.
Unlock a New Level of Operational Efficiency
With MaintainX's multi-site functionality, you can standardize, optimize, and scale operations across one or hundreds of sites.
Ready to get started? Talk to a MaintainX specialist today.
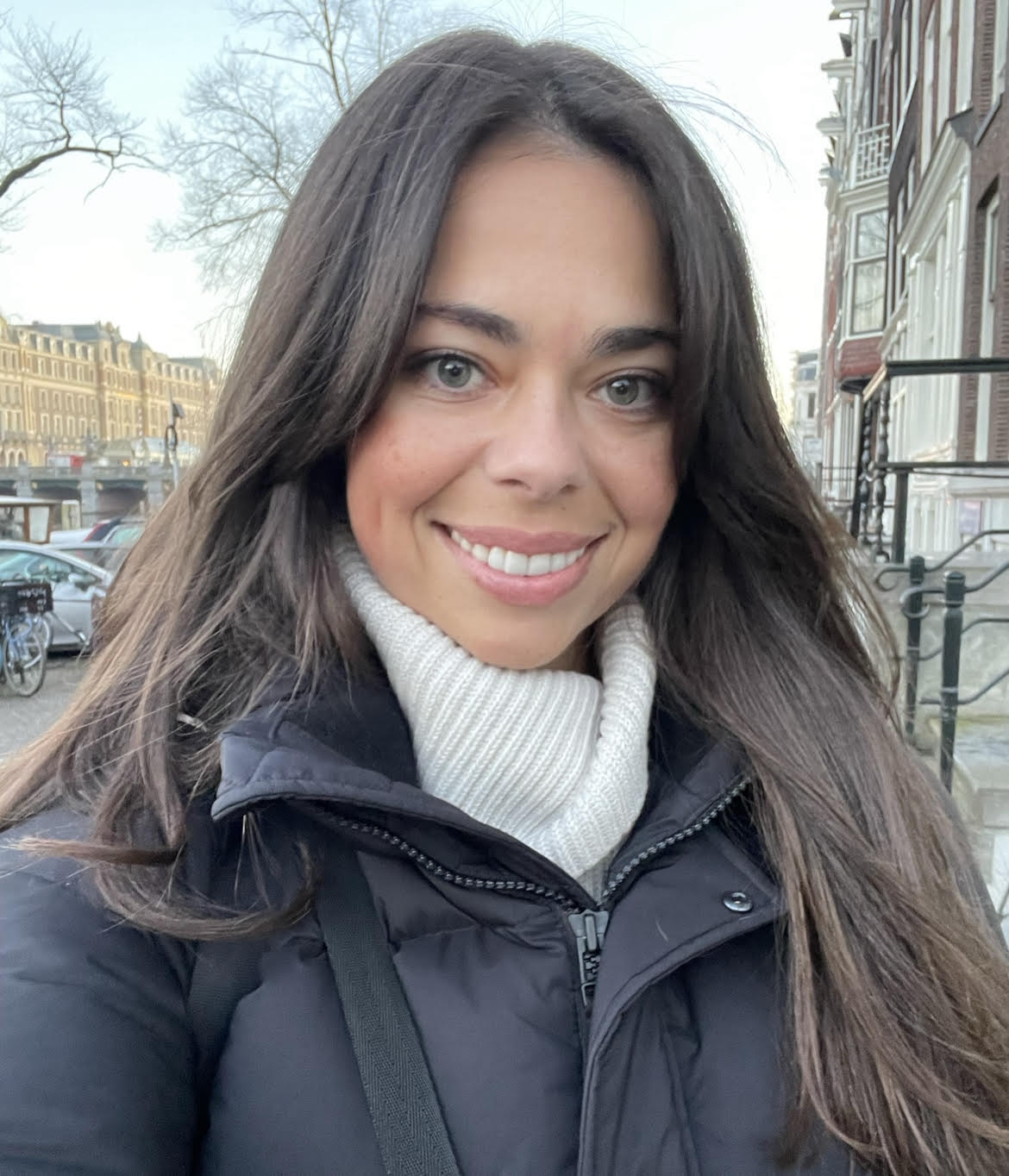
Simone Roscitt is a Product Marketing Manager at MaintainX, with a background in customer experience and data management and nearly 10 years of product-led SaaS experience. Simone has helped global enterprises maximize the use of their data to improve productivity, efficiency, and customer acquisition.