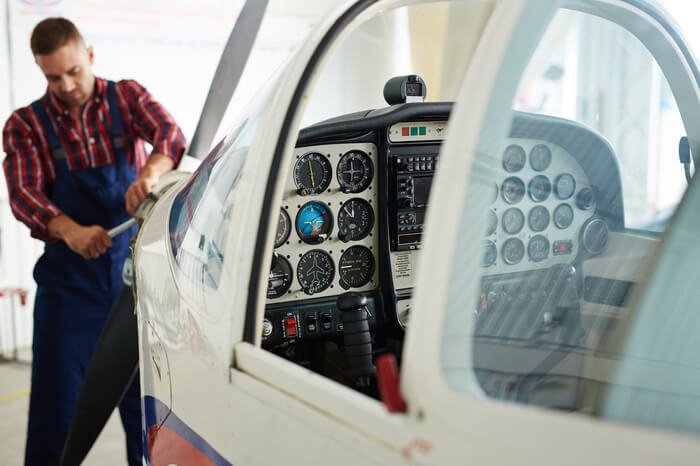
Preventive maintenance (PM) is a popular strategy used by maintenance departments of all sizes. According to the Plant Engineering Maintenance Report, up to 78 percent of facilities practice some form of planned maintenance on company assets.
This statistic isn’t too surprising considering that PM keeps critical assets in good working condition, reduces unplanned downtimes, and saves money. But will preventive maintenance eliminate all breakdowns?
In this article, we’ll answer that question. We’ll also discuss what steps industry leaders are taking to most effectively eliminate downtime.
Will Preventive Maintenance Eliminate All Breakdowns?
The short answer is—no, preventive maintenance will never eliminate all breakdowns. There are two primary reasons for PM’s lack of foolproof reliability:
1. Inventors don’t design machines to last forever: By nature, complex pieces of equipment are fallible. The older they become, the more likely they are to malfunction at unpredictable times.
2. PM only addresses identified failure modes: Manufacturer recommendations for conducting routine inspections, lubricating parts, and changing parts don’t consider an organization’s unique work environment. Factors like location, climate, and human behavior all influence breakdowns.
ARC Advisory Group reported that preventive maintenance (PM) typically can prevent unplanned downtime for only 18 percent of assets; the other 82 percent have random failure patterns.
For example, operator error accounts for up to 12 percent of unplanned downtimes in facilities. Asset failures also happen in between scheduled maintenance because aging equipment breaks down. For these reasons, most organizations don’t exclusively practice PM.
Even those with large maintenance budgets, and fine-tuned preventive maintenance programs, execute an 80:20 preventive-to-reactive maintenance ratio at best.
Preventive Maintenance at a Glance
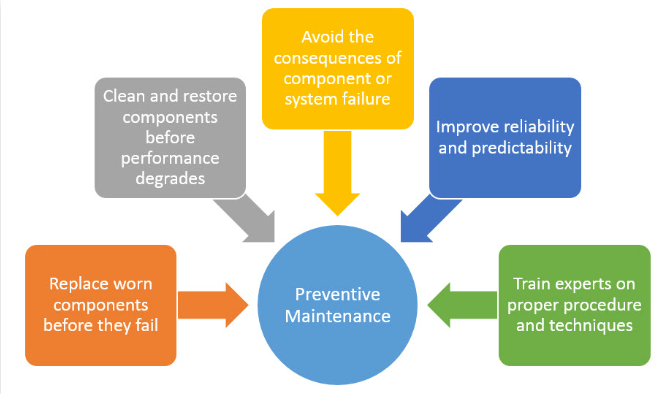
The best preventive maintenance can do is minimize unplanned breakdowns that cause downtime. Preventive maintenance activities usually are scheduled based on equipment usage or time period. For example, a fleet manager schedules their vehicles for maintenance every 1,000 miles.
Similarly, manufacturing facilities may schedule critical machines for lubrication every 100 hours of operation. Maintenance supervisors, planners, or schedulers create work orders that guide technicians on how and when to carry out tasks.
When developing a PM program, managers consider manufacturer recommendations, asset maintenance history, current equipment conditions, and production schedules (to minimize productivity disruptions).
Preventive Maintenance and Cost Savings
As previously mentioned, preventive maintenance can save organizations big money. However, performing preventive maintenance on all equipment is an unnecessary expense. Why?
Because preventive maintenance requires more manpower and more upfront hours than reactive maintenance. Thus, it’s not cost-effective for non-critical, quick-to-repair, and inexpensive assets.
Additionally, maintenance teams must be careful not to over-perform maintenance. Wasted O&M expenses associated with over-maintenance are counterproductive to PM cost savings. Tip: if the costs of performing PM outweigh the benefits, choose planned reactive maintenance instead.
Why Industry Leaders Are Switching to Predictive Maintenance
Preventive maintenance is the go-to strategy for most facilities looking to improve critical assets’ overall health and reliability. PM has been the golden standard since its parent strategy, reliability-centered maintenance (RCM), gained popularity in the 1960s.
However, as previously mentioned, breakdowns don’t always happen according to your schedule. That’s not to say PM isn’t an effective approach to maintenance.
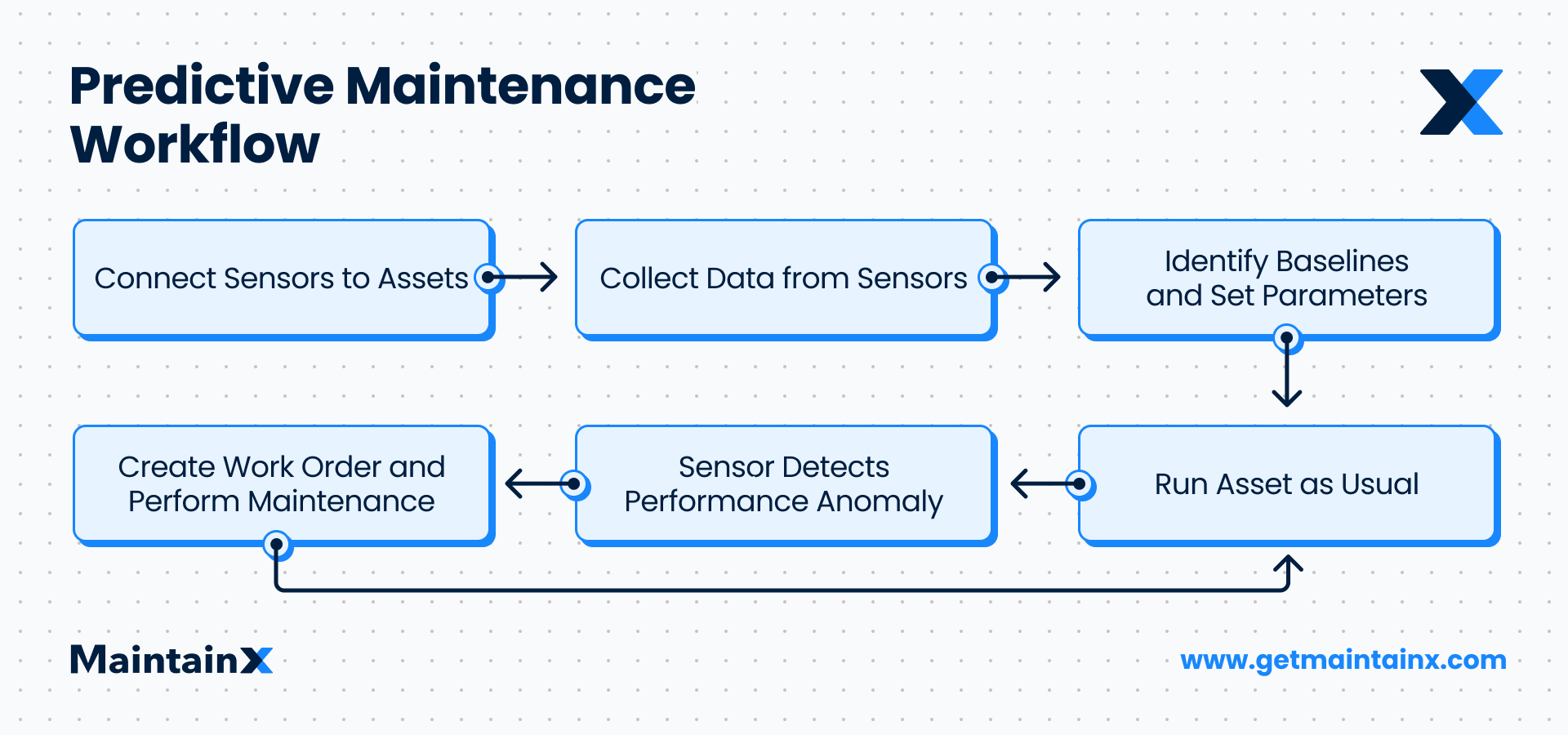
If PM programs didn’t deliver results, the average facility wouldn’t spend 20 hours per week on scheduled maintenance, as indicated in the 2019 Plant Engineering Maintenance Report.
However, increased consumer expectations and stricter regulatory requirements are motivating leading industrial organizations to pursue predictive maintenance (PdM) technologies. PdM enables organizations to leverage machine learning, prescriptive analytics, and the Internet of Things (IoT) to eliminate unplanned downtimes.
According to the U.S. Department of Energy, an effective PdM program helps eliminate catastrophic equipment failures. Forty-seven percent of organizations list asset uptime as the primary reason for adopting PdM. Other reasons include safety risk management, maintenance cost reduction, higher customer satisfaction, new revenue streams, and extending asset lifespan.
Preventive vs. Predictive Maintenance: Which Is Right for You?
Both preventive and predictive maintenance aim to minimize unplanned downtime with planned upkeep. However, PM involves routine scheduling based on time or usage, while PdM schedules maintenance based on evolving asset conditions measured in real time.
Generally, PM is best suited for SMBs wanting to maintain an efficient level of service, extend asset longevity, and reduce emergency maintenance costs.
Alternatively, PdM is best suited to large organizations—manufacturers, warehouses, oil and gas companies—responsible for maintaining many expensive, critical pieces of equipment.
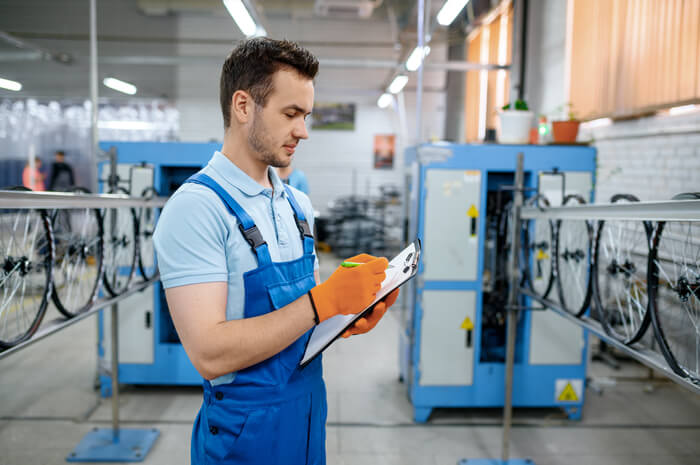
Also, the more significant the financial and safety impact of unplanned breakdowns, the more seriously an organization should consider adopting PdM. For example, one generator failing can create a domino effect of stalled production lines in a busy manufacturing facility.
According to the U.S. Department of Energy, predictive maintenance programs yield tenfold increases in ROI, 25 to 30 percent reductions in maintenance costs, 70 to 75 percent decreases in breakdowns, and 35 to 45 percent reductions in downtime.
World-class companies with large budgets incorporate both PM and PdM into their maintenance programs. Regardless of your choice, a cloud-based computerized maintenance management system (CMMS) can streamline recurring work orders, team communication, and more.
Ideal PM Candidates
PM is ideal for organizations looking to increase their assets’ lifespan without incurring any risks or high maintenance costs. Industries that rely on PM include:
- Hotels and restaurants
- Country clubs
- Fleet management
- Facility management
- Property Management
- Government institutions
- Learning institutions
Preventive maintenance only involves scheduling maintenance based on time and usage metrics and doesn’t require high upfront costs. So even small organizations with limited budgets looking for a proactive maintenance strategy can count on it.
Ideal PdM Candidates
PdM is ideal for organizations tracking significant amounts of data produced by machines. Essentially, PdM technologies help maintenance teams take tracking production, cost, and time metrics to another level! Industries that rely on PdM include:
- Consumer packaged goods (CPG)
- Manufacturing
- Automotive
- Electronics
- Textiles
- Aerospace
- Food and beverage
- Chemicals
- Oil and gas
- Pharmaceuticals
Again, it’s worth emphasizing that PdM requires significant upfront costs and specialized knowledge to implement successfully. At this time, the high barrier to entry limits Internet of Things (IoT) technology–like sensors and meters–to companies with large bank accounts.
Reduce Breakdowns with MaintainX
Are you still assigning your technicians paper work orders? If so, we invite you to join the digital revolution with MaintainX.
Anyone with a smartphone can download the app and get started within minutes. Our clients include everyone from small mom and pops to large franchises like McDonald’s. Pricing plans range from free unlimited work order creation for small businesses to monthly per-user plans for companies with complex needs.
FAQs
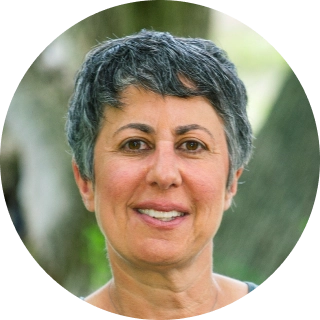
Caroline Eisner is a writer and editor with experience across the profit and nonprofit sectors, government, education, and financial organizations. She has held leadership positions in K16 institutions and has led large-scale digital projects, interactive websites, and a business writing consultancy.