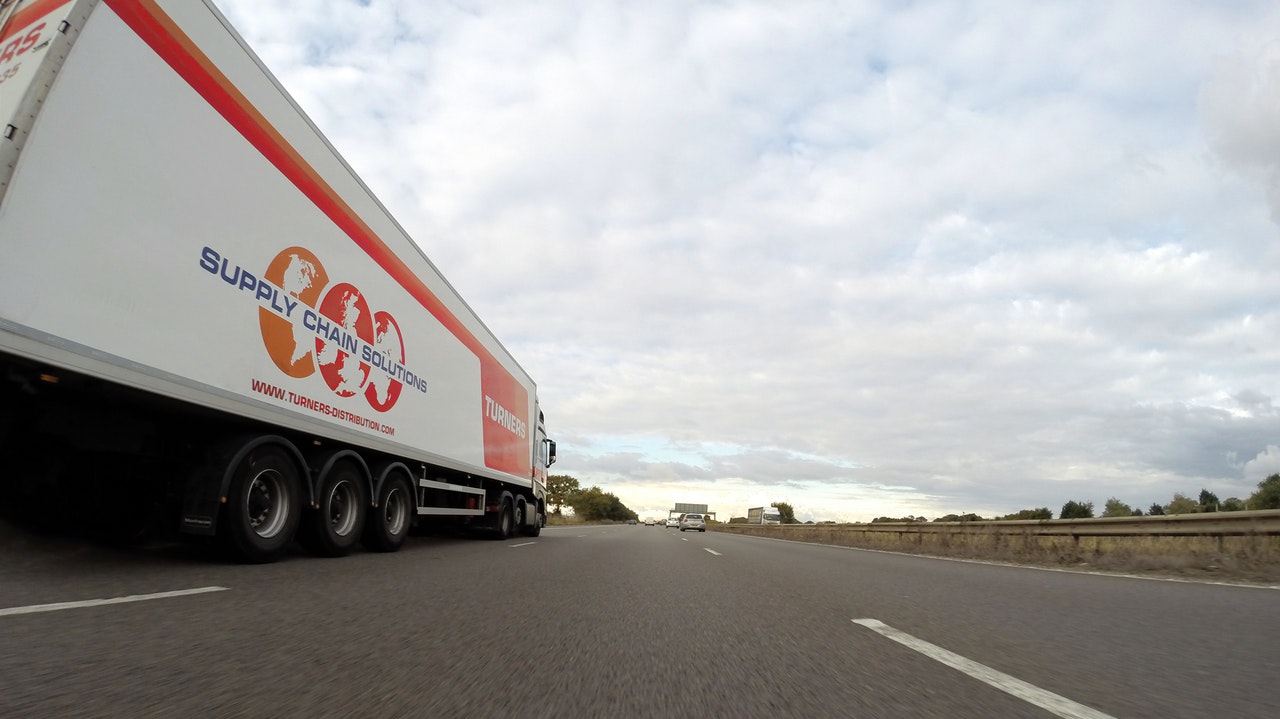
Field maintenance and field service businesses need to ensure that production delivery efficiency is optimized. Route planning plays a significant role in the production/service delivery business as it ensures that the right technician with the right products and tools reaches the destination in the minimum possible time.
Increasing production and service delivery efficiency can result in several benefits including timely project completion, employee productivity and timeliness, cost reduction, customer satisfaction, and more.
So what techniques can you use to increase production efficiency? How you can ensure timely and efficient service delivery to your departments and your customers? This article covers the best ways and approaches to increase production/service delivery efficiency across all departments and customers.
Increase Production Delivery Efficiency
1. Plan, Plan, and Plan
Plan production delivery. Create clear plans. Define goals.
Create a standardized plan or an outline for work orders that your team should follow for all the internal and external orders. Additionally, all the orders should be planned before you send your team out in the field.
Let’s assume you receive a work order request for building maintenance. The manager needs to evaluate the order, share it with the appropriate technician, check inventory, and assign it to the right department for further processing. It’s important that the building history is available to the technicians so they can identify what’s already been done, what needs to be done, and what they should expect.
In the absence of a plan, you might end up sending the wrong technician with the wrong products to the site to perform a task that had already been completed. A simple example might look like this:
- A light bulb is reported out
- The technician shows up with a new light bulb
- A technician replaces the light bulb, lazily doesn’t check that the new one works
- The cycle continues – until someone realizes the socket’s wiring is the issue several days and light bulbs later.
Planning is essential if you really want to increase production/service delivery efficiency.
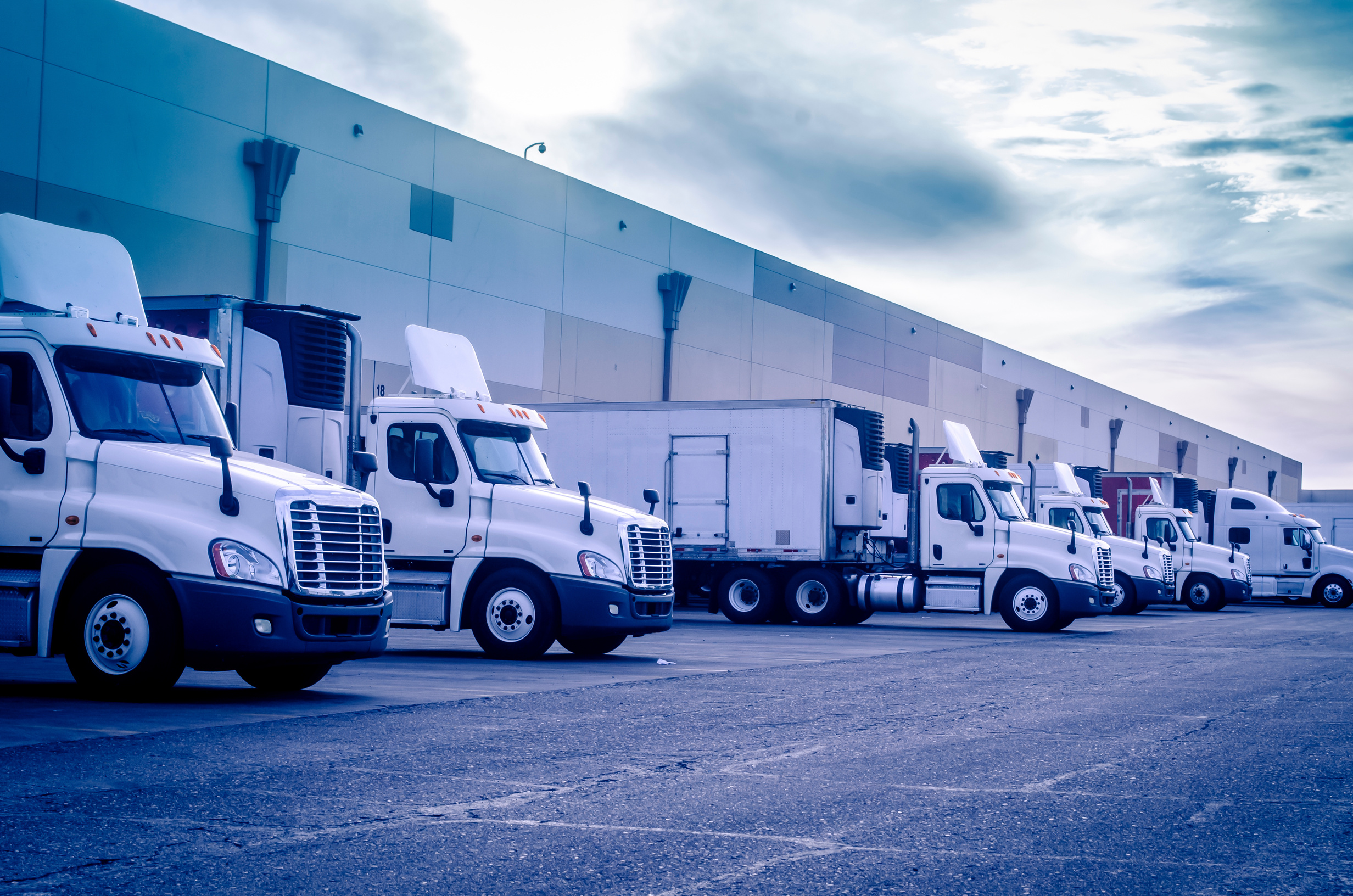
2. Prioritize
Prioritizing certain orders over others is a critical step toward enhancing efficiency. At the end of the day, not all work orders are equally important, and with limited resources, sometimes certain things need to be left for another day.
Setting priorities for orders based on site location, urgency, equipment available, servicing requirements, and delivery time can help you improve production delivery significantly.
An efficient work order management platform will enable you to re-route your team and re-prioritize work orders on the fly – while ensuring that the work orders that are being delayed aren’t lost in the shuffle.
In today’s fast-paced world, it is essential to prioritize work orders. You can’t do business efficiently without setting priorities and keeping in sync with your team. If all work orders are treated equally, it will cost your business lost opportunities and lost revenue.
3. Use a Tool
If you are operating like 39% of today’s manufacturing organizations, it’s highly likely that all of your day-to-day operations are still based 100% on paper. If you’re currently using a CMMS tool or another similar work order management tool, odds are that the strength of that system lives on desktop/web interfaces – not mobile devices. That likely works just fine for your office staff, but if most of your core operational staff are on their feet, it creates a log jam of information and communication.
The most common technology used by businesses to monitor maintenance is a CMMS. Statistics show that 53% of businesses now use a CMMS for maintenance. If you’re using a CMMS, then route planning and service delivery can be optimized, at least from the office staff’s side.
MaintainX, for instance, is a work order management tool that is optimized for mobile devices. Unlike traditional CMMS, MaintainX works intuitively for team members on the go. You can manage work orders, prioritize tasks, provide work instructions and standard operating procedures, and communicate with your employees both via direct/group messages and directly within work orders.
Perhaps the best thing about using a program like MaintainX is that all of your repeatable procedures can easily be automated. No need to remember your quarterly preventative maintenance tasks anymore!
4. Get Team Feedback
You can’t improve production delivery efficiency without the input of your entire team. Unfortunately, most organizations don’t bother taking feedback from their frontline staff – far too many prefer creating plans and schedules while only consulting their fellow office-based colleagues.
If you intend to improve service delivery efficiency, it seems obvious that you should seek feedback from the drivers. In fact, this should be the first thing you should do. Here are a few things that you need to get feedback for:
- Ask for candid organizational feedback. What drives them crazy about current procedures?
- Ask what they currently appreciate or like about current procedures.
- Ask what information they aren’t currently receiving that would be helpful to have.
You can get feedback on other things too but let’s start from the basics. Remember, there is always the right driver for the delivery, you need to find them.
5. Optimize Routes
Route optimization is yet another approach to increasing service delivery efficiency. Route optimization refers to managing drivers’ availability and vehicle space.
The management should have all the necessary information about vehicles such as weight, capacity, load limit, top speed, etc. This lets the manager avoid space wastage in the vehicles. Any misused space in a vehicle is wasted space.
If, for instance, a vehicle is setting out to a site and it has space available, you need to add a stop and use the vehicle’s capacity to its fullest.
Similarly, managing drivers’ availability and optimizing drivers is also a part of route optimization. When a driver will be available, how much time he will need to reach back to the office, when he will be available next, etc. are important factors that the manager needs to consider before assigning a task to a driver.
Once you optimize the routes, you are able to send the right vehicles and drivers at the right time to the right locations. It is a challenging task, and there should be someone in your team who should manage route optimization. This is one great way to boost production delivery efficiency without adding more vehicles and/or drivers.
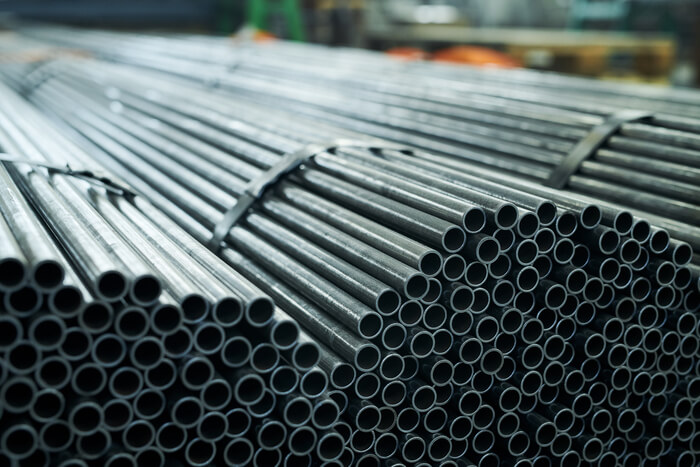
6. Update and Review
You have to make a lot of changes to the route, vehicles, driver schedule, etc. to improve production/service efficiency. Sometimes these changes work and sometimes they don’t.
How do you know if a change in your production/service delivery system worked? You have to review it. You should review and monitor every change and your full delivery system regularly.
What it will do?
It will help you see what works and what doesn’t work. Whenever you update or tweak something in your production delivery system, review the change and see how it worked.
Tweaking the production/service delivery system is essential if you want to improve efficiency and effectiveness. Keep doing it.
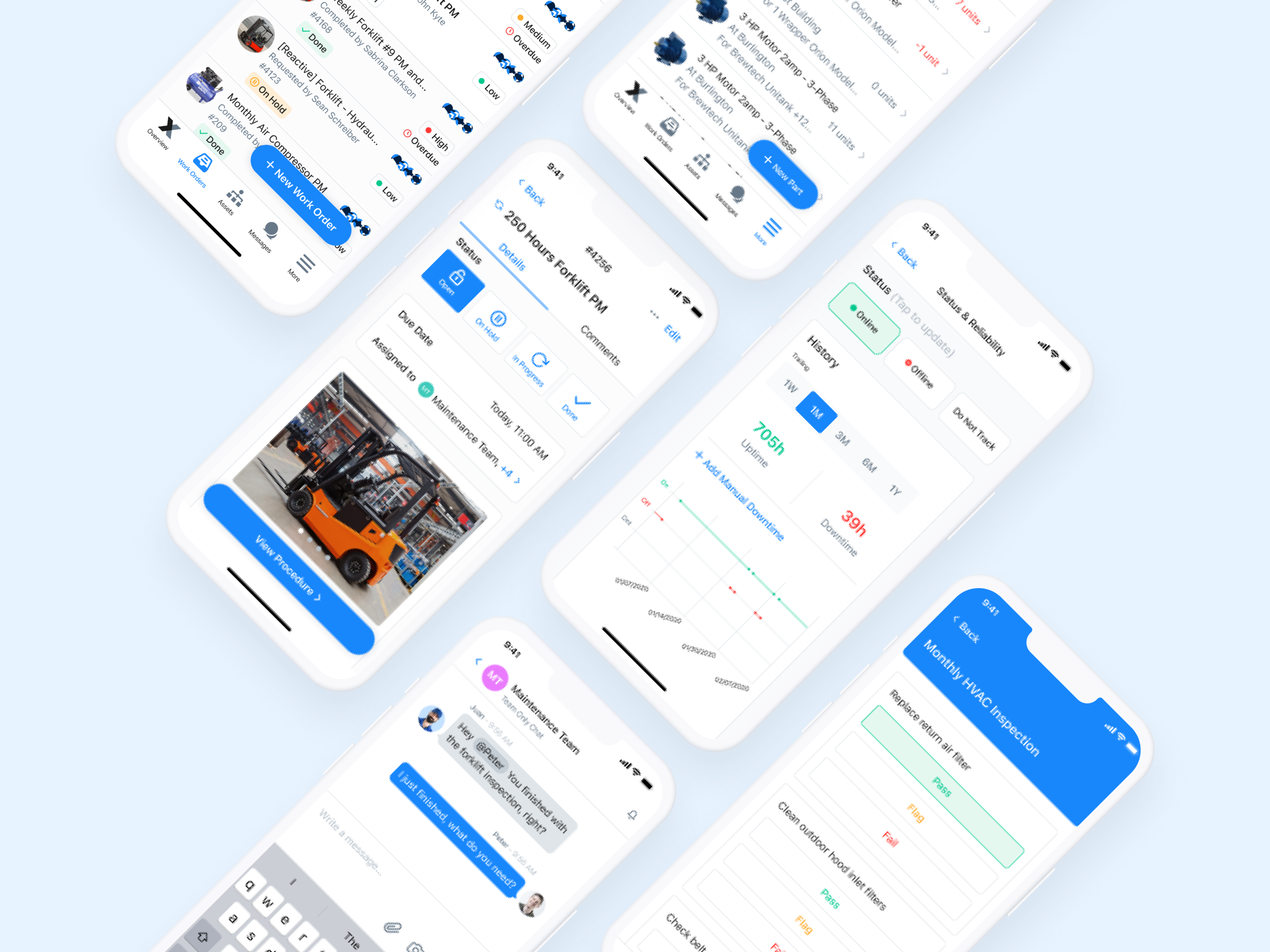
Increase Production Efficiency with a CMMS
These 6 ways to increase production/service delivery efficiency need one thing: Consistency. You might not be able to see the results immediately. For instance, if you collected feedback from your drivers and rescheduled their routes, don’t expect a miracle the next day.
Give it time.
Monitor the change for some time and see how it turns out. The case is the same with other techniques for improving production/service delivery efficiency.
Next, use appropriate software to manage production delivery. Most of the logjams that occur throughout the industry are related to team inefficiencies that happen before or after the actual delivery.
Your team should know what they have to do and how they have to do it. MaintainX will help you direct traffic.
FAQs
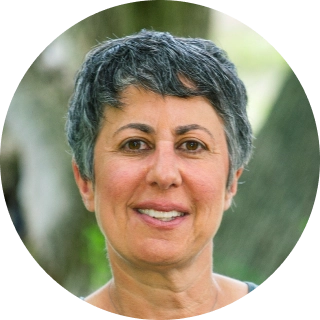
Caroline Eisner is a writer and editor with experience across the profit and nonprofit sectors, government, education, and financial organizations. She has held leadership positions in K16 institutions and has led large-scale digital projects, interactive websites, and a business writing consultancy.