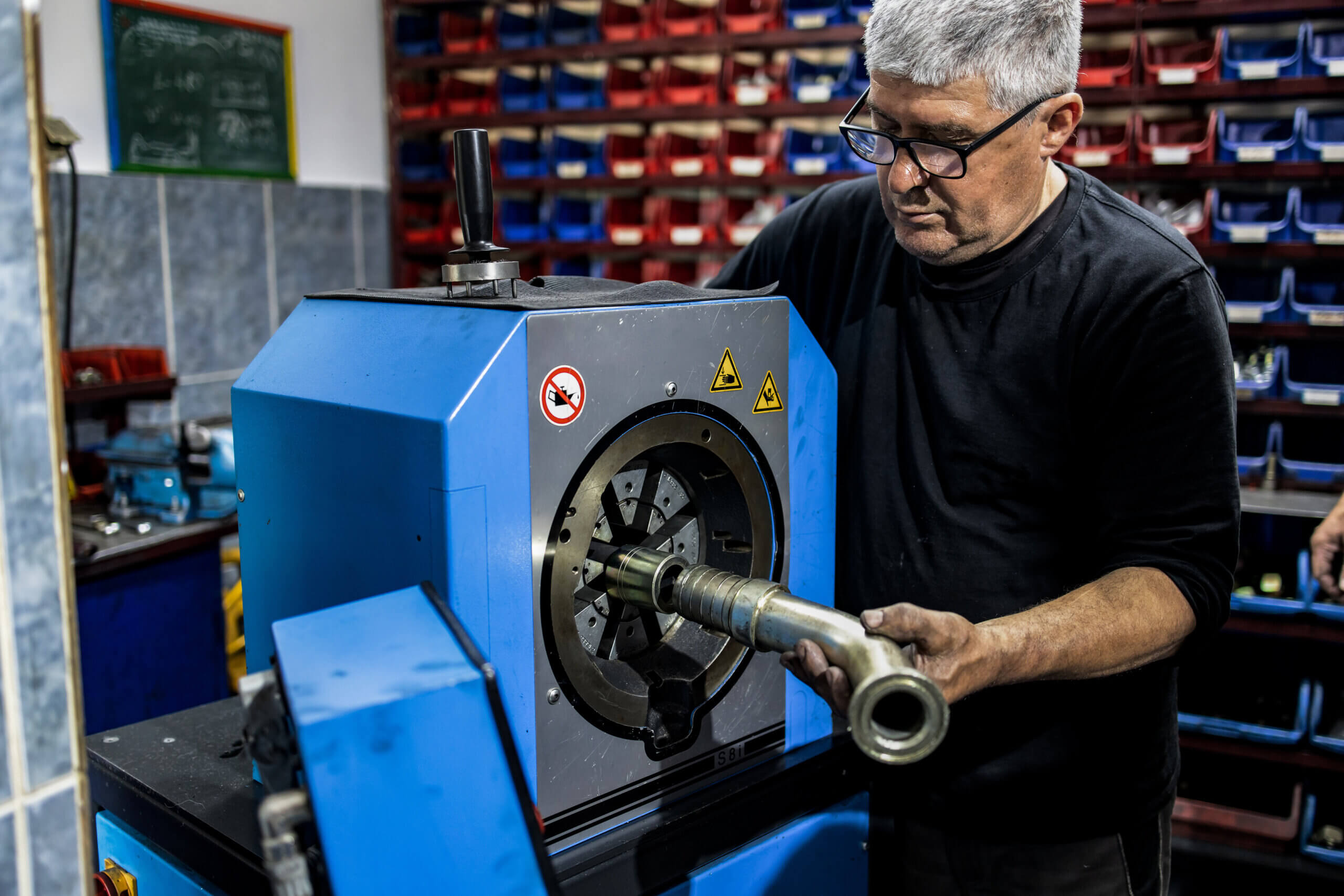
A job shop is a manufacturing system, usually small, that focuses on “job production.” Job production refers to unique, custom, or bespoke manufacturing processes, of customer orders in low volume.
In other words, job shop manufacturing is a process of catering to orders, making small batches of bespoke goods, with your company manufacturing each product according to specific customer requirements.
Job shop manufacturing is popular with small business ventures and is unique in multiple ways. For one, job shops only produce goods upon receiving orders. In this way, job shop manufacturing is similar to pull production systems.
Also, a shop can’t standardize products because it creates the products according to customer specifications. This means job shop manufacturing operations can’t really be standardized either. Instead, goods move along the production process in ways specific to customer demands, as opposed to standard production flow and batch or continuous manufacturing, for example.
“It is time to reform the job shop. This means embracing the new manufacturing principles that managers are now applying to high-volume operations—in particular, the commitment to total quality control (TQC) and just-in-time production (JIT). By implementing a philosophy of low-overhead, fast response manufacturing, job shops can simultaneously improve manufacturing performance and reduce costs.”
HBR
Maintenance Challenges in Job Shop Manufacturing
Let’s consider one example: clothes. Bespoke tailoring is a make-to-order process. Instead of clothes following a typical assembly line production, companies make them according to customer size and cloth specifications. Each item is made according to the customer’s measurements and tastes.
Let’s think about this clothes example even more specifically. Imagine your team needs coveralls for workers on the shop floor. Maybe you’ve had trouble with the clothes not fitting team members properly. Or maybe you want each set branded with the company logo. These specifications would impact at least some form of the job shop process. The alterations will happen later if the coveralls are made via typical automation. This is a common element of job shop manufacturing: products follow unique and sometimes irregular routings across the shop floor.
In a regular production line, products are progressively completed as they pass through each stage. However, with a job shop, products might return to different parts or stages they have previously passed through for additional customizing.
Job shop manufacturing follows a Just-in-Time workflow, a useful lean manufacturing and maintenance concept. The process has many benefits, such as reducing waste and unplanned equipment downtime. That said, maintenance teams face challenges.
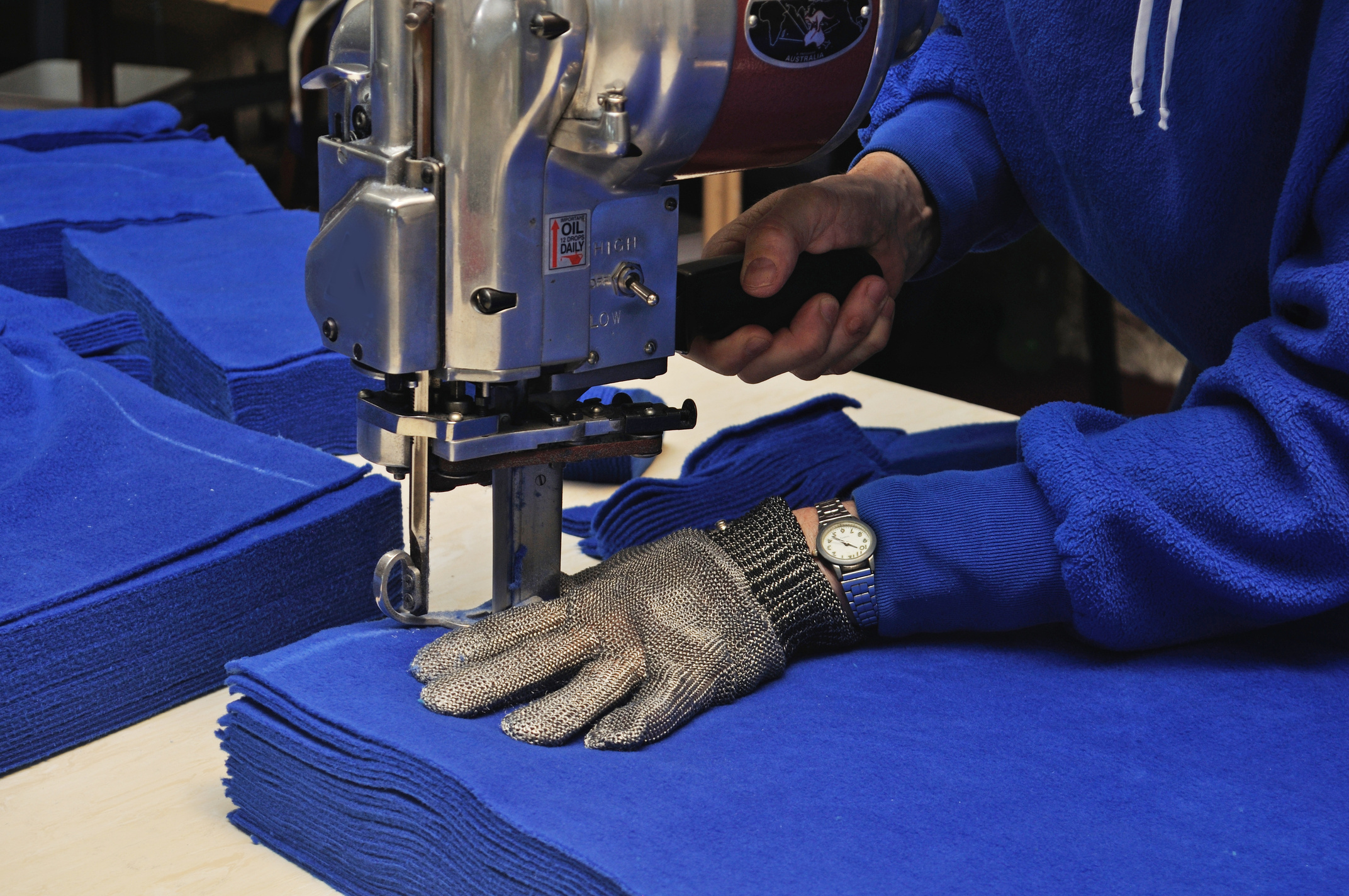
Workload Is Intensified
This may seem counterintuitive on the surface. After all, a common component of job shop manufacturing is making small batches of products. But this is precisely what can intensify the workload.
Producing larger quantities of goods can lead to cost and energy savings through economies of scale. However, because a job shop doesn’t run a regular schedule, many orders can cause strain. For example, when production is high, the maintenance workload is intensive. That is, lots of equipment maintenance in the machine shop in a short period.
Resources Aren’t Maximized
While a large number of orders can be challenging, the opposite can also be challenging. Getting little to no orders means you aren’t getting maximum value from your assets. Job shop manufacturing production can thus have the unintended consequence of workforce, assets, and inventory lying idle for long periods.
Preventive Maintenance Is Hard to Schedule
Because the manufacturing process is irregular and dependent on customer orders, production scheduling can be challenging. And if production planning is complicated, maintenance also becomes difficult to schedule. In addition, it’s hard to schedule preventive maintenance if you have no idea if the equipment will be in use during that time.
It’s Hard to Know What Job Shop Maintenance to Perform
Apart from figuring out when to perform preventive maintenance, it’s hard to know what asset will need what maintenance activity. As such, It’s also challenging to develop standard operating procedures to guide your maintenance. Lack of planning also increases setup times and material handling for whatever maintenance tools are required.
“A job is characterized by its route, its processing requirements, and its priority. In a job shop the mix of products is a key issue in deciding how and when to schedule jobs. Jobs may not be completed based on their arrival pattern in order to minimize costly machine set-ups and change-overs. Work may also be scheduled based on processing time, from shortest to longest.”
Inc.
Overcoming Manufacturing Challenges
Aim for a Predictive Approach
Sure, a job shop may not know exactly what orders will come in and when. However, an attentive team will notice certain patterns over time. For example, specific goods may be ordered more frequently in the summer than in the winter, or specific customers will regularly repeat orders.
Predictive job shop scheduling will help you identify which assets are most critical. As a result, you can figure out how to approach your manufacturing and maintenance activities.
For example, Johnson’s Rule may be useful here. Its primary objective is to find the optimal sequence of jobs to reduce makespan (the total amount of time it takes to complete all jobs). It also reduces the amount of idle time.
Furthermore, given the irregular nature of production, consider implementing a predictive or condition-based maintenance approach.
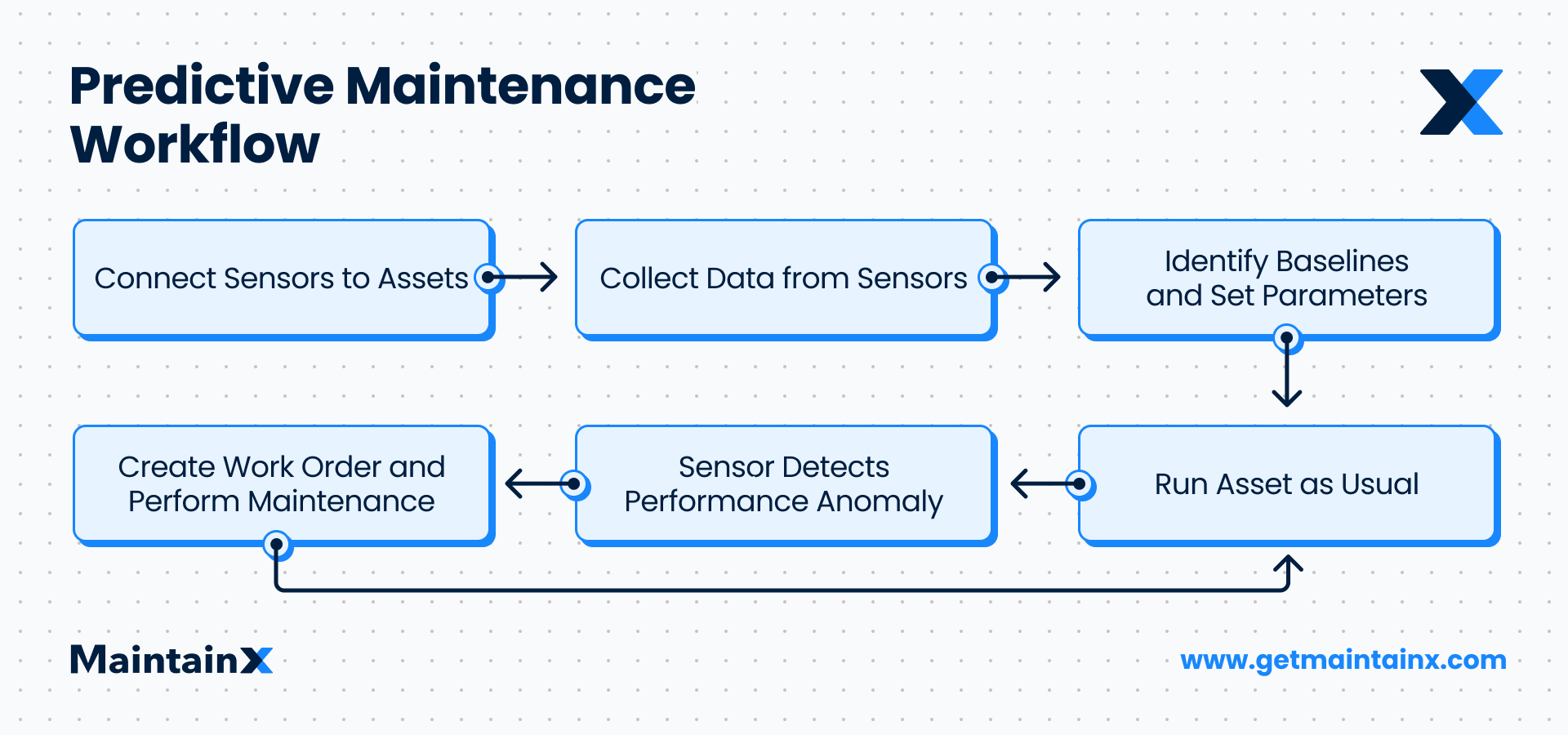
OR
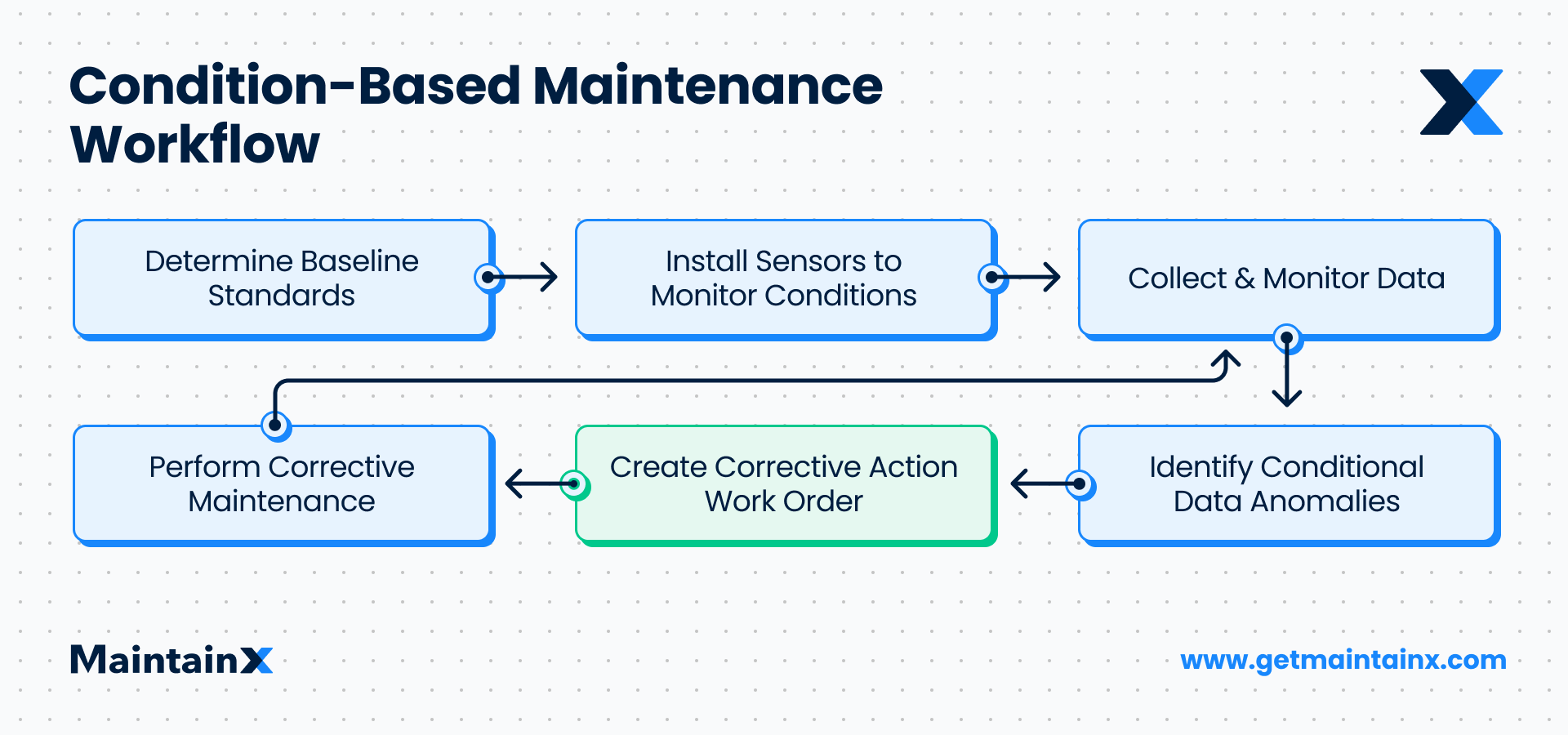
Know Your Lead Time
If you use a CMMS, tracking work orders, delivery time, and other KPIs is a no-brainer. With your data in the clouds and at your fingertips, you’ll be able to determine the lead and cycle time needed to manufacture and deliver goods. Knowing your lead time will help you manage your job shop production. In addition, you’ll be able to identify any lags in the supply chain and find ways to eliminate them beforehand.
Plan What You Can
First, despite bespoke orders, chances are you know your facility’s specialties. This means you know how much it takes to make a set of coveralls and how long it takes to brand them with a logo.
As such, when orders come in, you can process them more quickly by optimizing the use of assets. Planning also involves managing your inventory. Then, when you need to carry out maintenance, you can move quickly with the machine tools and parts you need on hand.
Optimize Your Job Shop with MaintainX
If you consider the best ways to optimize your job shop operations, the common thread is data. A Computerized Maintenance Management Software (CMMS) like MaintainX has the features you need to store, track, and analyze your maintenance and manufacturing data over time.
In addition, the app allows for straightforward ERP (Enterprise Resource Planning) system integration, giving you access to real-time data both on the floor and in the corporate office. What’s more, MaintainX has built-in instant messaging capabilities, meaning you can create and assign work orders on the go. And your teams can access these work orders from their mobile devices in real time.
Even if, as a job shop manufacturer, you can’t plan ahead as much as you’d like, you can always streamline workflows, track assets, and optimize maintenance and manufacturing schedules from the palm of your hand.
FAQs
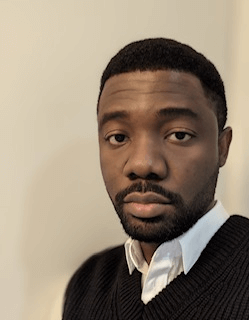
Lekan Olanrewaju is a content writer with years of experience in media and content creation. He has held positions at various media organizations, working with and leading teams at print magazines, digital publications, and television productions.