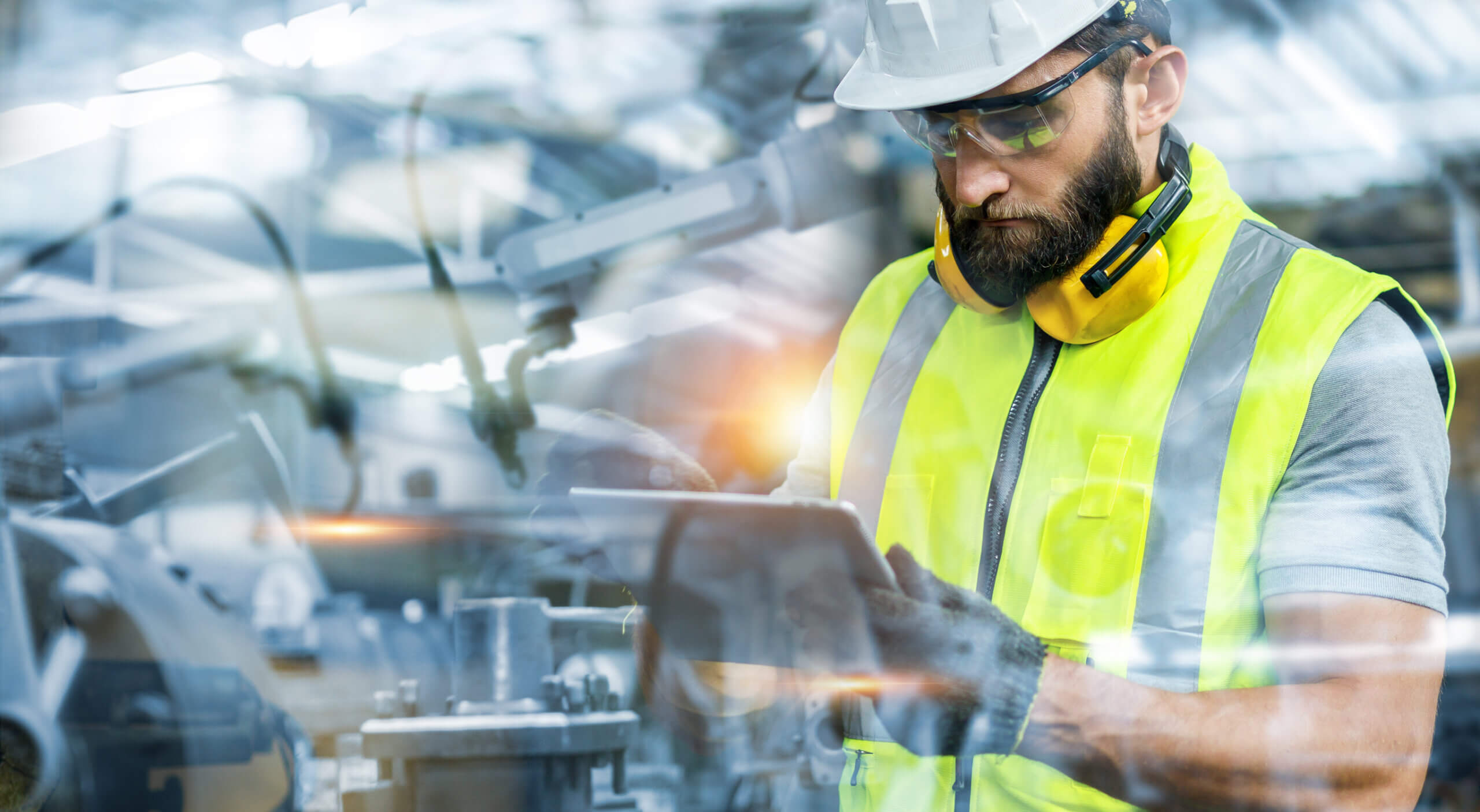
Creating a line of lean manufacturing is an approach to manufacturing that involves eliminating waste from the production line. Initially developed by the Toyota Motor Company as part of its Toyota Production System, the idea was Muda, or waste, or anything that didn’t contribute to the finished product or the customer needed to be eliminated from the cycle.
Have you ever reviewed your production process only to find that you were spending time on things that didn’t add to the quality or quantity of finished products? Or maybe you realized efforts were being duplicated. You decided to adjust your manufacturing process as a result. This continuous improvement and streamlining of processes is what lean manufacturing is all about.
Manufacturers can apply lean principles in various ways. One approach is the Six Sigma framework. According to the American Society for Quality, Six Sigma is “a method that provides organizations tools to improve the capability of their business processes.” Lean Six Sigma applies the Six Sigma framework to remove process waste and improve performance.
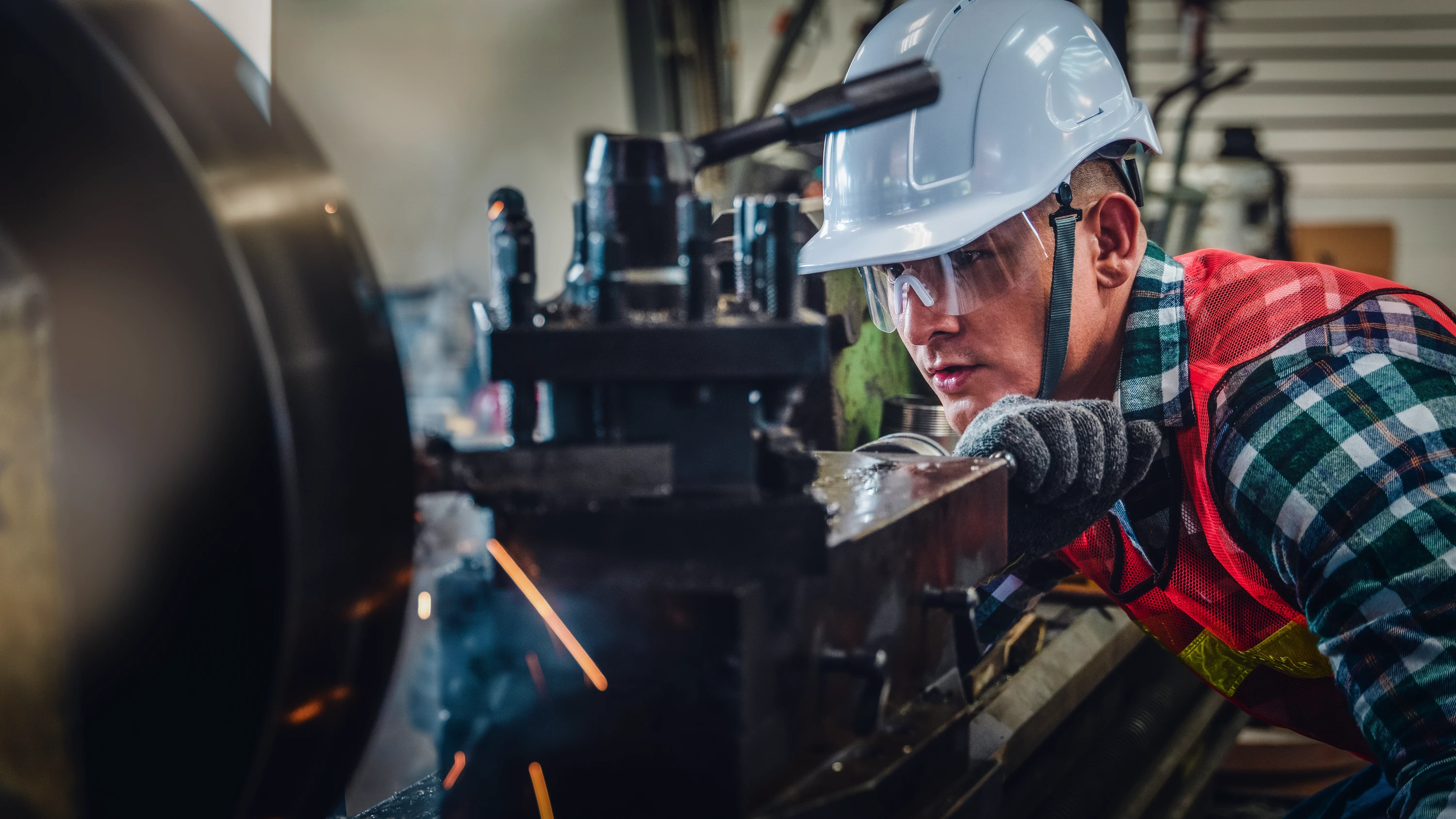
One pertinent principle is line balancing. Line Balancing refers to leveling the workload across all stages of a production cycle or value stream to remove buffers, bottlenecks, and excess effort. The goal is to match the production rate to takt time. Takt time is the rate at which products need to be completed to meet customer demand.
The language and specific methodology may vary, but the general point is that businesses and manufacturing processes can benefit from focusing on what contributes to their finished product and eliminating anything that doesn’t.
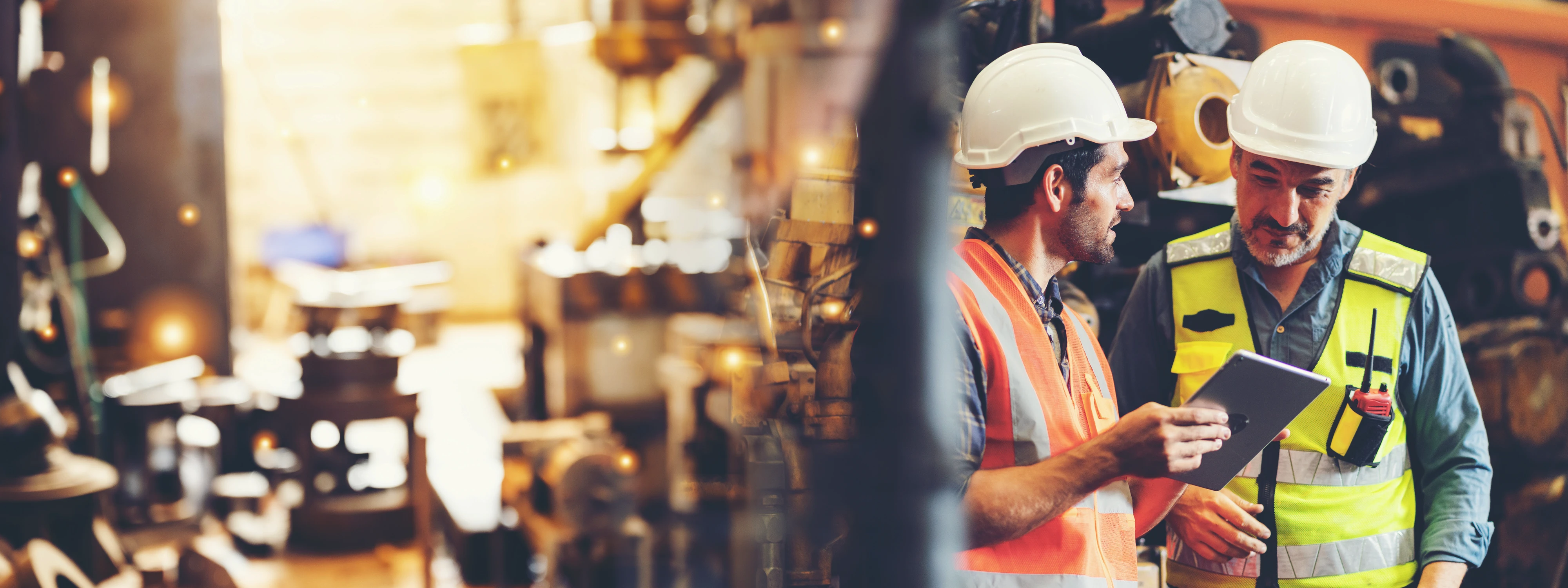
What Is Lean Maintenance?
On the surface, lean maintenance might sound like something that flows from lean manufacturing. In reality, lean maintenance is far more integral. No lean manufacturing process can be complete without a strategy for lean maintenance.
Lean maintenance refers to reducing waste and inefficiency in your maintenance processes. It involves applying lean principles to the maintenance of your equipment and other physical assets, making the overall process faster, less expensive, and more efficient.
Consider, for example, a piece of equipment that gets checked weekly. (Think preventive maintenance here.) Week after week, technicians inspect the equipment and find it is in good shape. On the one hand, this is good. You don’t want to wait until your assets are about to fail before you spot any faults. (Think reactive maintenance here.)
On the other hand, the time spent carrying out these preventive inspections could be better utilized. A predictive maintenance strategy, for example, would eliminate unnecessary maintenance, streamlining efforts down to specific actions that actually make a difference.
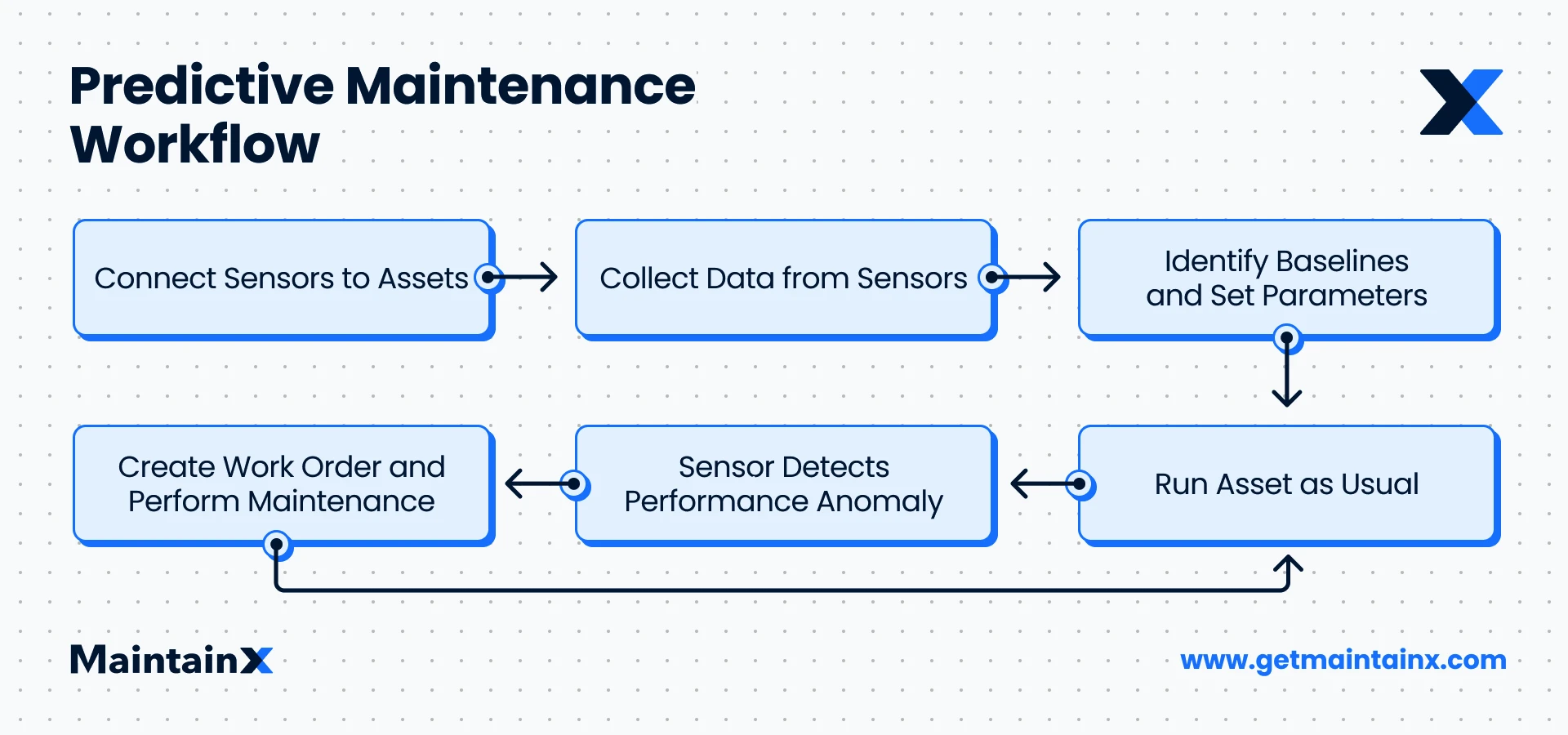
Lean maintenance principles involve eliminating excessive maintenance procedures and removing any unnecessary steps from the maintenance practices you carry out.
This can mean anything from ensuring that spare parts are available (to prevent time spent ordering or going to buy them when they are needed) to knowing where tools are stored (to prevent time searching all over the shop floor) to digitizing your work orders (so people know who does what in the event of a breakdown).
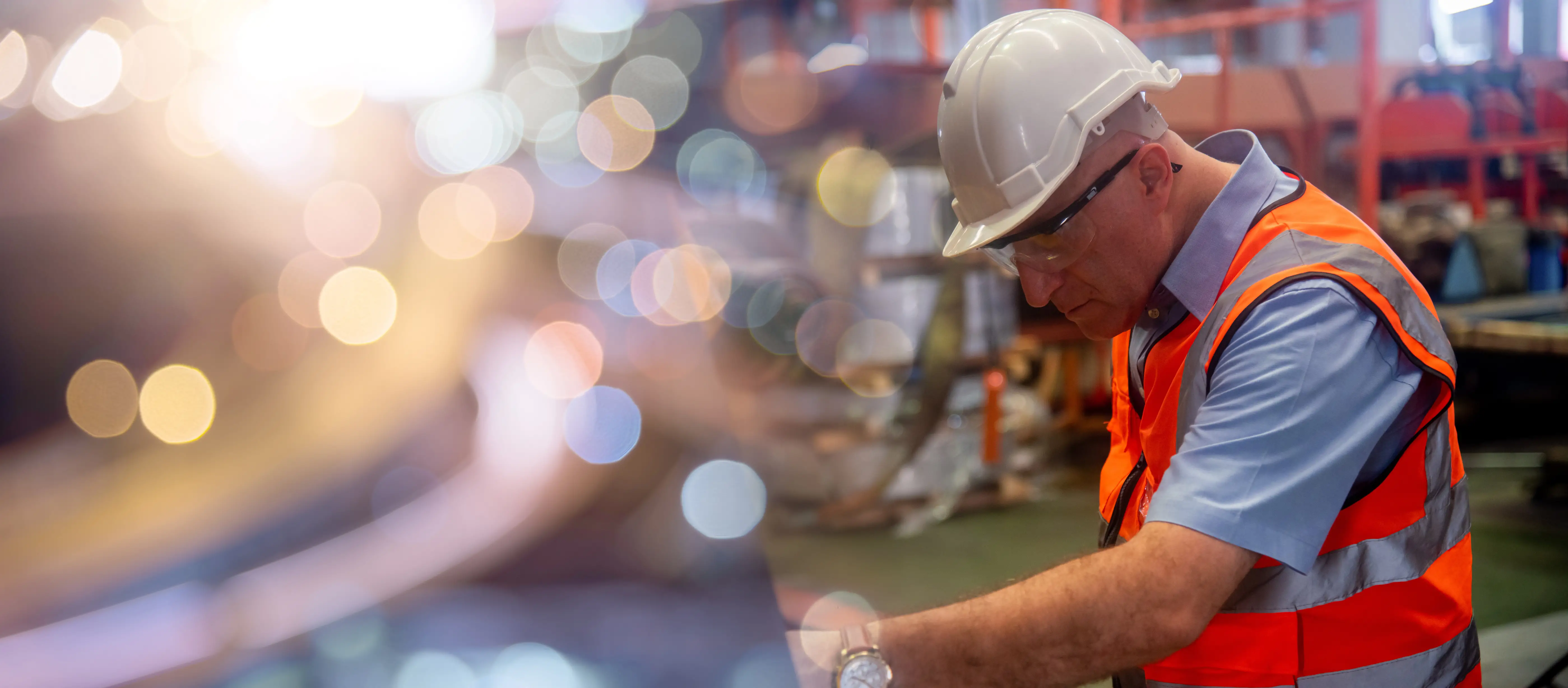
Benefits of Lean Maintenance
Not surprisingly, lean maintenance’s main benefit is the overall efficiency and an improved bottom line that results from streamlining maintenance processes. This can play out in different ways, such as:
Reducing Costs
This is a direct result of eliminating unnecessary elements, steps, or processes in maintenance. Every maintenance activity has a cost. It can be the cost of resources and equipment that could be used elsewhere or of staff who have to be pulled away from their workstations due to excessive maintenance.
“Throughput, in business, is the amount of a product or service that a company can produce and deliver to a client within a specified period of time. The term is often used in the context of a company’s rate of production or the speed at which something is processed.”
Investopedia
Lean maintenance helps you reduce both planned and unplanned downtimes. You save on resources, reduce production losses, and ensure throughput is at an optimal level. “Throughput” refers to the total time it takes to run a particular process from start to finish. In other words, reduced time = reduced spending.
Maximizing Output
Eliminating unnecessary maintenance practices allows your workforce to take on more productive tasks. Lean maintenance directly leads to a lean line of production overall. Workers are no longer carrying out unnecessary inspections or spending time looking for spare parts or tools when they need them. They can get to production and maintenance tasks that directly maximize output.
Use a CMMS to Build a Lean Maintenance Strategy
Knowing where your assets stand at any given time is essential. A CMMS ( computerized maintenance management software) like MaintainX has integrated functionalities designed just for this. So whether you’re looking to carry out root cause analysis, define your metrics and KPIs, or organize your standard operating procedures, MaintainX streamlines lines of lean manufacturing and maintenance directly from your mobile device.
.webp)
Communicating Values
To build and execute a lean maintenance strategy, first address the overall culture in your organization. Establishing a high-efficiency mindset to reduce waste is imperative. Stakeholders will understand why you’re adopting a lean approach and what it means for the business.
For example, Toyota pioneered the principle of Kaizen, referring to a continuous improvement mindset. You’ll likely have your organization-specific principles and goals, but the point is to communicate them to staff to ensure they keep them front of mind at all times. The best CMMS allows you to store this information and give staff access to it on the go.
Carrying Out Preventive Maintenance
A proactive approach to problem-solving is critical to creating a maintenance line of lean. A CMMS orchestrates how your department carries this out. MaintainX has multiple functionalities to help with preventive maintenance. Asset inventory and global procedures are crucial.
Managing Maintenance Workflows
MaintainX lets you manage workflows by creating, assigning, and overseeing work orders in real time. The instant messaging feature saves time otherwise spent walking from one department to another, or figuring out who is in charge of what. In addition, access to MaintainX’s Global Procedure Library ensures that maintenance workers are updated with the latest practices and methods to improve their overall efficiency and create that line of lean.
Ready to go lean?
FAQs
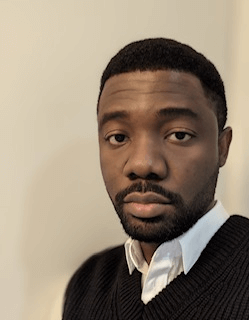
Lekan Olanrewaju is a content writer with years of experience in media and content creation. He has held positions at various media organizations, working with and leading teams at print magazines, digital publications, and television productions.