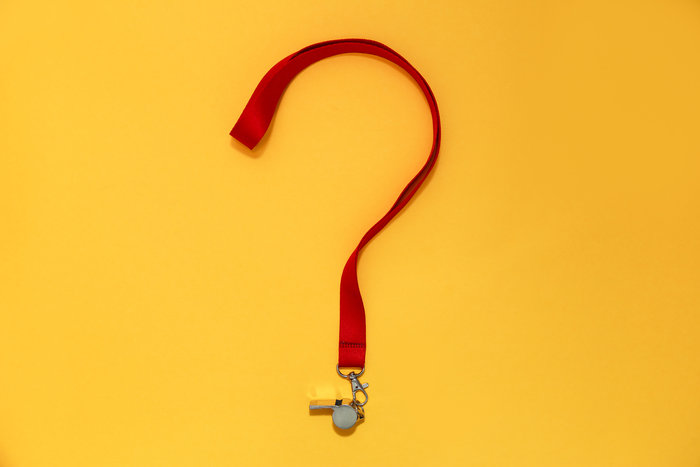
There’s a lot to gain from implementing reliability-centered maintenance (RCM).
Industrial organizations can potentially enjoy improved O&M optimization, reduced costs, and increased equipment longevity. But that doesn’t mean switching from standard preventive maintenance (PM) to RCM strategies that involve more advanced maintenance concepts and technologies is always the right move.
According to Reliability Web, RCM-practicing plants fail to follow through with 85 percent of the recommended program changes from their own analyses! Inevitably, these organizations found themselves struggling to implement strategic maintenance recommendations among other competing daily priorities.
The findings come from a survey of more than 250 facilities with functioning RCM programs. Studies like this often point toward a lack of upper-management support as the primary cause of program failures. However, that’s certainly not the only reason.
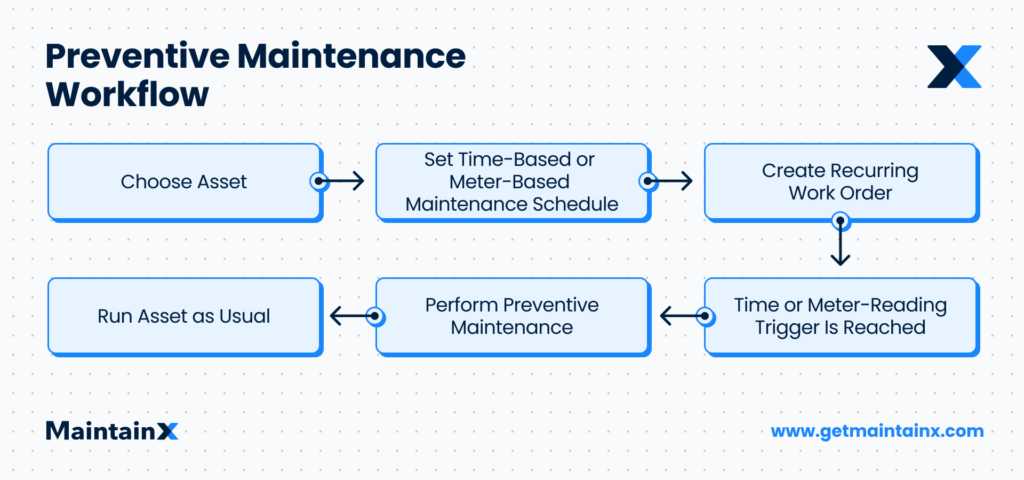
Is Your Organization Ready for RCM? 6 Questions to Ask Yourself
As mentioned in Implementation of Reliability Centered Maintenance in Process Industry-Issues and Difficulties, RCM-program collapses also result from the misunderstanding of RCM requirements, the mismanagement of regular maintenance tasks vs. RCM tasks, and “getting stuck in the weeds” with technicalities that don’t really matter.
In this article, we’ll dive into the overarching causes of RCM-launch failures. Below, you’ll find six essential questions to ask yourself before committing to an RCM program.
Conduct a careful assessment of your organization’s existing maintenance systems now, and you can proceed with confidence when the time is right (and potentially save thousands in unnecessary costs from a poorly executed RCM program)!
1. Do I Have an Employee to Implement the Work?
RCM is an advanced O&M framework used to extend equipment lifespans and decrease downtime cost efficiently. The framework encompasses several analytical processes to determine the proper balance of planned and corrective maintenance as part of a failure-management strategy.
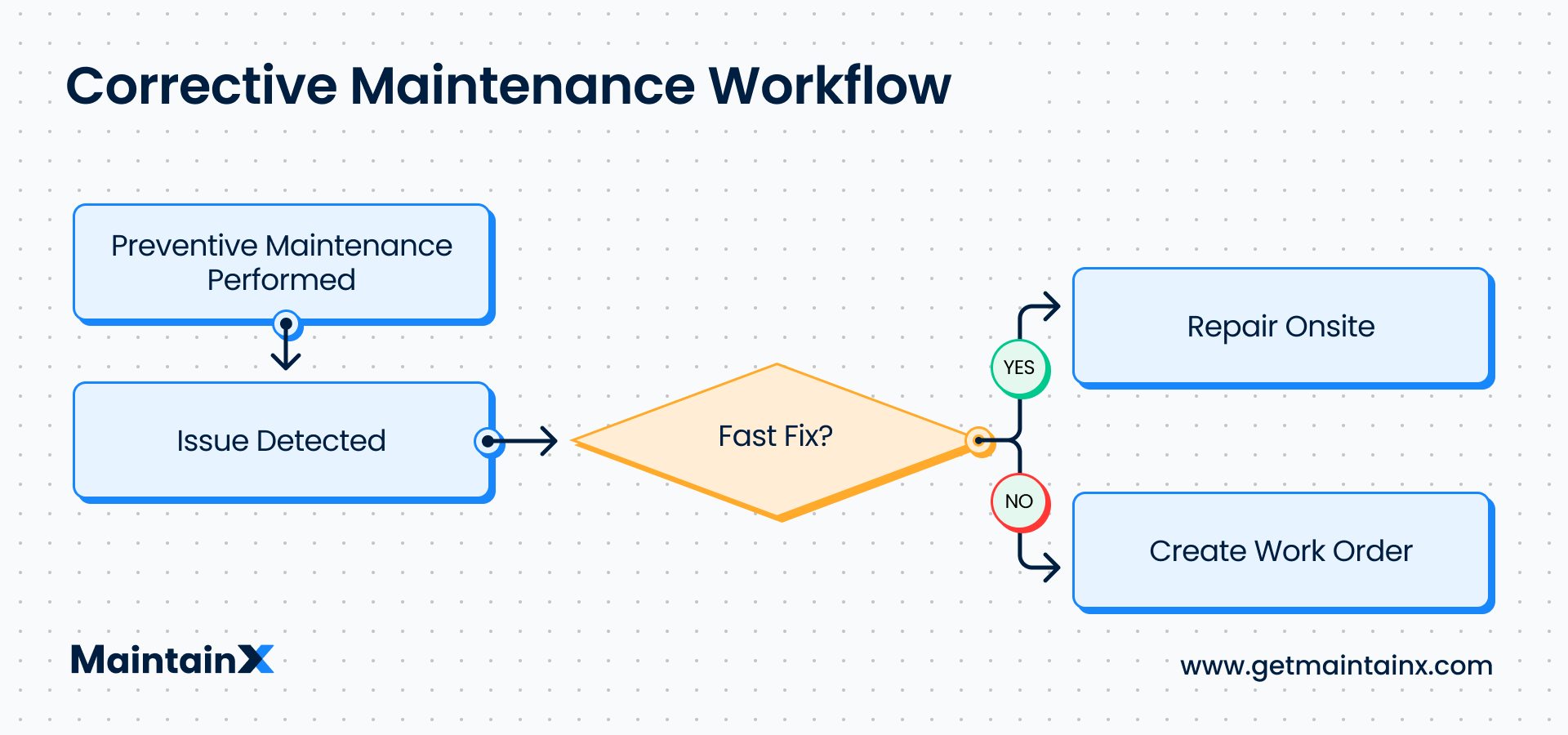
Thus, the most crucial factor for launching a successful RCM program is working with the right organizational manager to champion your efforts.
The manager’s responsibilities will include scheduling and monitoring equipment tests, evaluating incoming data, performing alignments, and making O&M decisions. For these reasons, your champion should understand general maintenance practices, possess strong mathematical skills, and bring consistent leadership qualities.
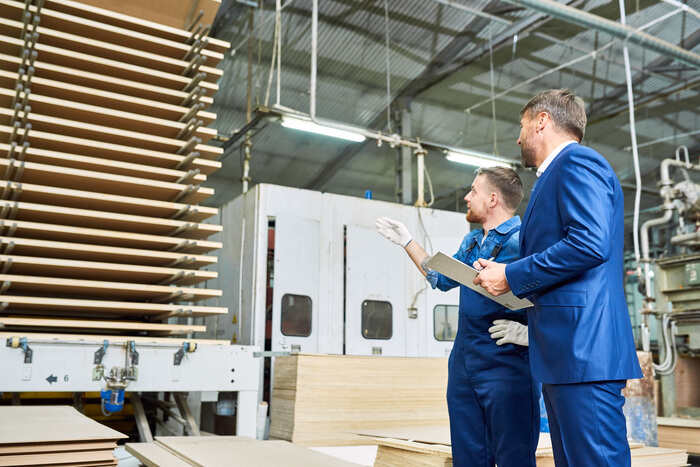
Ideally, the employee should also be well-versed in RCM concepts like root-cause analysis, fault-tree analysis, and equipment failure modes. Depending on your maintenance department’s size, you may already have a suitable candidate in mind. If hiring a new RCM supervisor isn’t in the budget right now, start with education.
A variety of online programs are available to take your team’s knowledge level from novice to expert. As your staff learns more about RCM and what it can offer in practical applications, someone may express interest in spearheading the challenge.
2. Have I Clearly Articulated Our Desired Outcomes?
Before embarking on any complex journey, define your goals clearly. After all, your organization will expend considerable time, effort, and capital on RCM initiatives.
Put simply, there’s no room for ambiguity in launching an RCM program. You’ll want to be as specific as possible, including defining objectives to measure both success and failure. What distinct rewards are you seeking in exchange for your investment?
Perhaps, you want to stop wasting money performing unplanned maintenance on a few critical pieces of machinery that consistently break down. OK, that’s an excellent start.
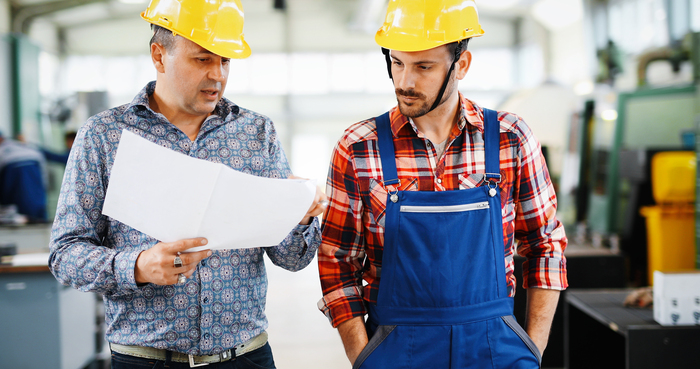
Now, take your O&M goal-setting further by asking yourself precisely where those savings could come from and how much they could amount to.
For example, say you want to improve equipment uptime by 50 percent on your facility’s five most critical assets. Calculate your average hourly production output and the amount of money spent on related emergency repairs to determine a dollar amount. How much would this save your organization each month, quarter, and year?
Decreased costs always sound attractive, but will their total value deliver the ROI you need? Or are there better strategies than RCM to achieve your goals? If the potential savings outweigh the initial costs of RCM implementation, you’re heading in the right direction.
3. Do I Have Executive Support and Understanding
Launching an effective RCM program is a multi-faceted initiative. As such, proper implementation involves collaborating with several departments, including maintenance, risk management, human resources, and purchasing.
For this reason, long-term success is dependent on obtaining executive support. RCM efforts without company-wide backing will wither over time.
Inevitably, unforeseen challenges related to RCM will arise. These speedbumps will cause team members to pivot and restrategize along the way. Time spent implementing new RCM calculations, configuring advanced equipment, and streamlining workflows is expected.
However, only when management is invested in the process and understands its prerequisites for success will your team see the initiative through to a positive endpoint. This sentiment brings us to our next question.
4. Can I Prove the Benefits Outweigh the Costs?
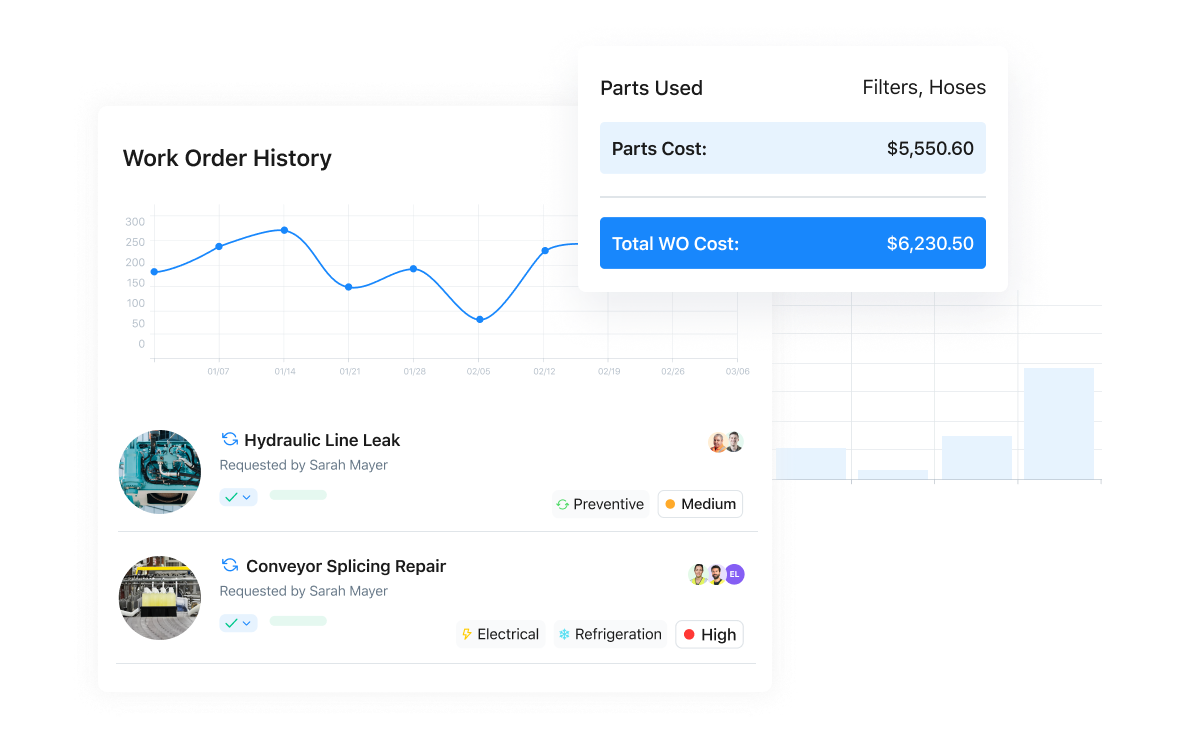
This question relates to a core concept of remaining profitable—ensuring an initiative’s benefits outweigh associated costs. If your company’s leadership has only expressed lukewarm sentiments about RCM, consider providing them with more educational material to increase enthusiasm.
Additionally, if your team isn’t already tracking PM program metrics, get started! Quality RCM decisions depend on accurate, consistent, and reliable data. Do you have the data available to make such informed decisions about which preventive maintenance system you should target first using RCM strategies?
A user-friendly computerized maintenance management system (CMMS) can help your department track KPIs that prove the correlation between equipment reliability, time and cost optimization, and maintenance management initiatives.
5. Are Team Members Available for This Project?
On the ground level, you need experienced and willing team members to succeed. Your maintenance technicians, engineers, and planners have the practical equipment knowledge necessary to execute an RCM program.
Commit to providing staff with the support they need to thrive from the beginning. Commit more experienced team members specifically to these projects or allocate a set number of hours each week for specific RCM projects.
Depending on competing organizational priorities, now may be the best time to introduce new standard operating procedures (SOPs). Carefully consider team members’ available hours and how many hours are needed to get up and running.
6. Do I Have a Plan to Document Results?
Finally, how will you record your RCM program efforts? If you launch without a reliable documentation plan in place, you may struggle to prove the effectiveness of new program measures.
If your organization is still using pen, paper, and spreadsheets to track maintenance work, choose a user-friendly CMMS to streamline documentation. Digitizing asset management and work order history will revolutionize your O&M workflows. The right CMMS can help automate RCM assignments, digitize audit trails, organize inventory, and much more. Here’s a quick glance at MaintaX’s mobile CMMS experience:
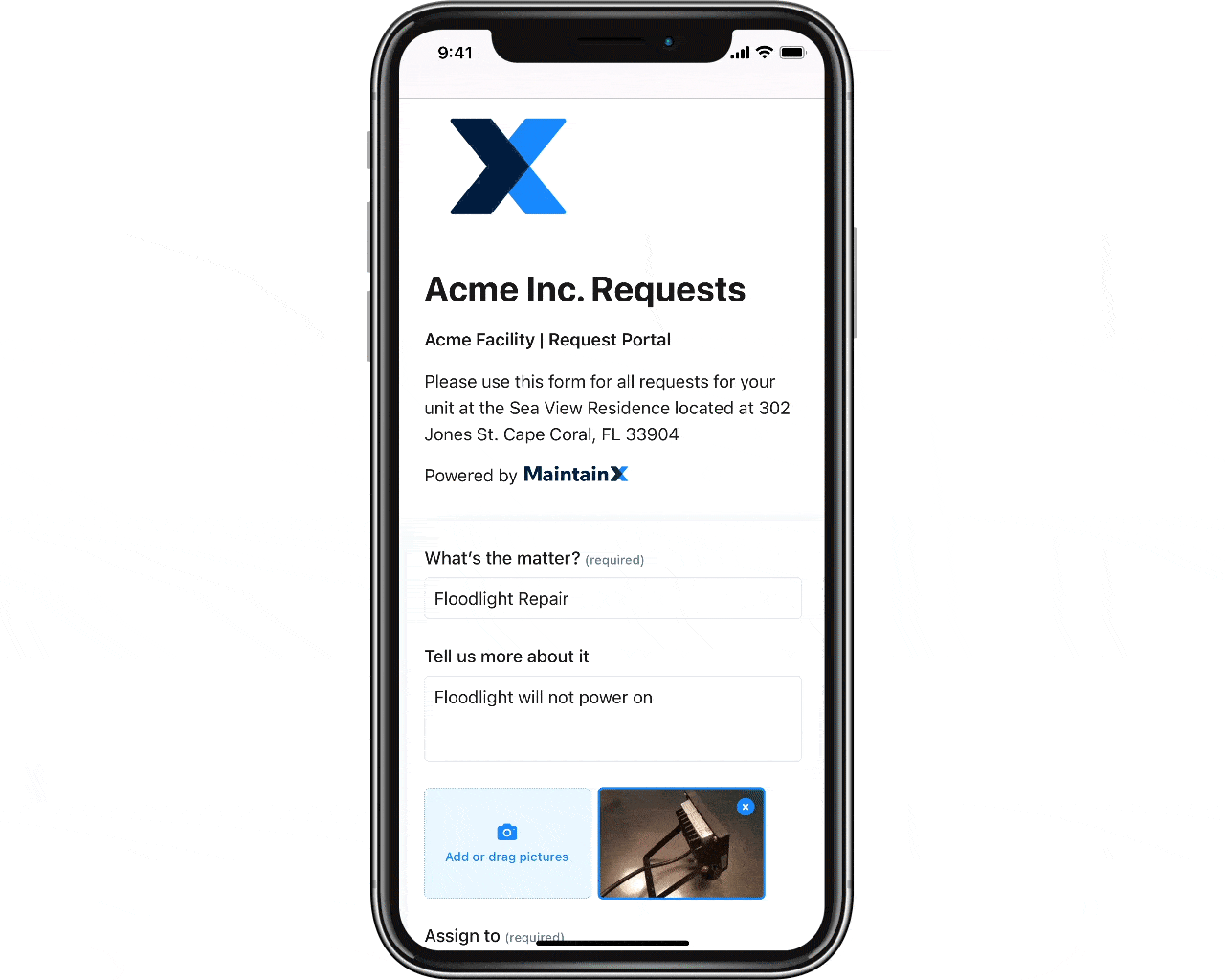
Recording and analyzing results of what you’re seeking to improve—O&M costs, production output, safety—will make for a more compelling case when approaching upper management for support.
For more information on launching an RCM program, consult the JA1012_201108: A Guide to the Reliability-Centered Maintenance (RCM) Standard
Simplify O&M Optimization with MaintainX
If you’re struggling to answer any of the questions mentioned above, conduct your due diligence as a team. Doing so could be the difference between feeling satisfied over groundbreaking improvements or feeling regretful over a trigger-happy launch.
However, you can reap the benefits of CMMS right now—no matter the experience level of your existing maintenance team. MaintainX is the world’s top-rated mobile CMMS with chat. Industrial facilities and mom-and-pops alike are already using MaintainX for RCM. With MaintainX, you can schedule recurring work orders, manage assets, and maintain a pulse on O&M spending.
FAQs
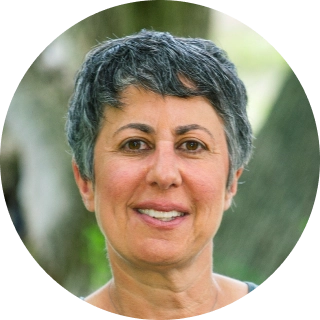
Caroline Eisner is a writer and editor with experience across the profit and nonprofit sectors, government, education, and financial organizations. She has held leadership positions in K16 institutions and has led large-scale digital projects, interactive websites, and a business writing consultancy.